A taxa de deposição na soldadura é influenciada por vários factores, incluindo o tipo de processo de soldadura, as definições do equipamento, as propriedades do material e os parâmetros operacionais.Por exemplo, no revestimento a laser, as taxas de deposição dependem da potência do laser, das taxas de alimentação e da velocidade transversal.Na pulverização catódica, factores como as propriedades do material alvo, a corrente e a energia do feixe desempenham um papel importante.Para a soldadura com elétrodo de arame, variáveis como o tamanho do arame, a amperagem e a posição de soldadura têm um impacto significativo na taxa de deposição.A compreensão destes factores ajuda a otimizar os processos de soldadura para obter eficiência e qualidade.
Pontos-chave explicados:
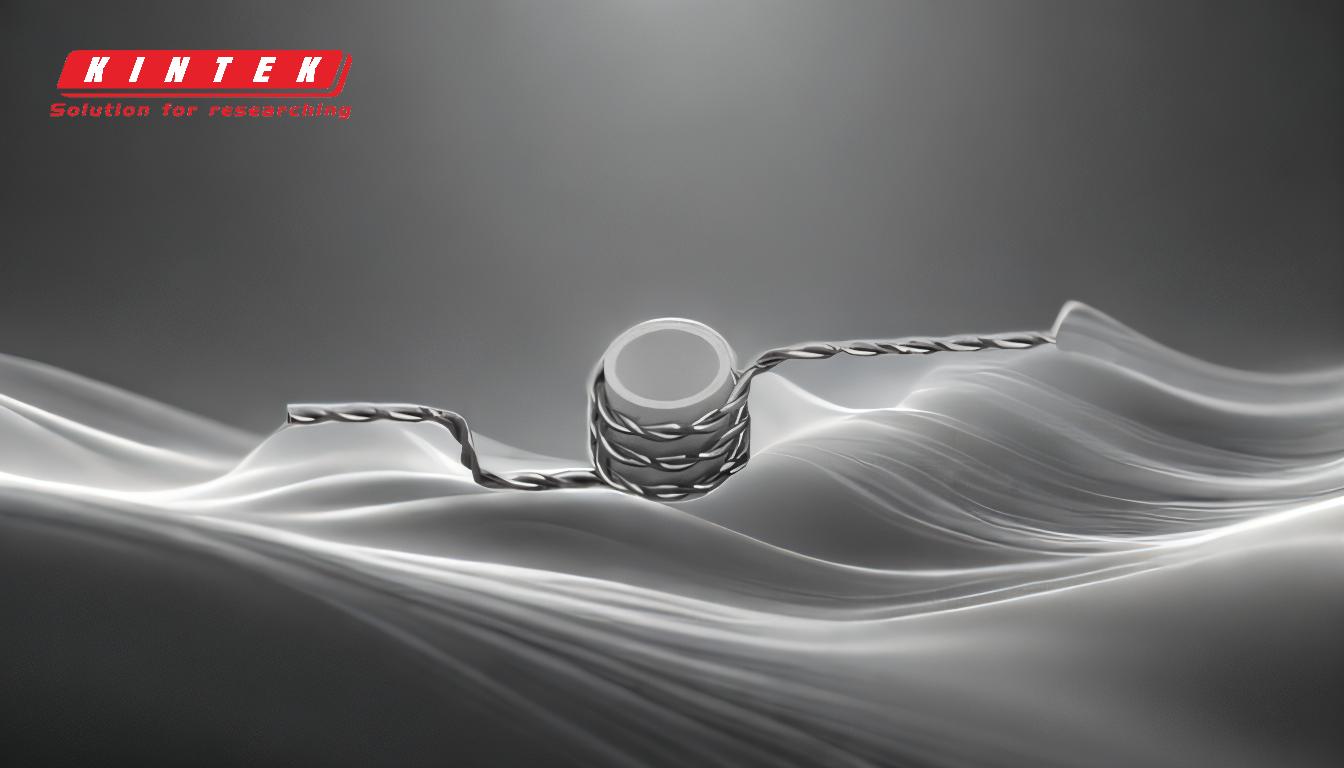
-
Potência laser no revestimento laser:
- A potência do laser afecta diretamente a entrada de energia no material, influenciando a taxa de fusão e a eficiência da deposição.
- Uma potência laser mais elevada aumenta geralmente a taxa de deposição, mas deve ser equilibrada para evitar defeitos como o sobreaquecimento ou a deformação.
-
Taxas de alimentação no revestimento a laser:
- A taxa a que o material (por exemplo, pó ou fio) é alimentado na zona de soldadura tem impacto na taxa de deposição.
- As taxas de alimentação óptimas asseguram uma adição consistente de material sem sub-alimentação ou sobre-alimentação, o que pode levar a defeitos.
-
Velocidade de deslocação no revestimento a laser:
- A velocidade transversal determina a rapidez com que o laser se desloca através da peça de trabalho.
- As velocidades transversais mais rápidas podem reduzir as taxas de deposição, mas melhoram a produtividade, enquanto as velocidades mais lentas aumentam as taxas de deposição, mas podem conduzir a uma entrada excessiva de calor.
-
Caraterísticas do plasma na deposição por plasma:
- A temperatura, a composição e a densidade do plasma influenciam a taxa e a qualidade da deposição.
- O monitoramento desses parâmetros garante as propriedades desejadas do material e minimiza a contaminação.
-
Propriedades do material alvo em Sputtering:
- As propriedades físicas do material alvo, como a densidade e o ponto de fusão, afectam a facilidade com que pode ser pulverizado e depositado.
- Materiais com pontos de fusão mais baixos e rendimentos de pulverização mais altos geralmente têm taxas de deposição mais altas.
-
Corrente e energia do feixe na pulverização catódica:
- Uma corrente e uma energia de feixe mais elevadas aumentam a taxa de pulverização catódica, conduzindo a taxas de deposição mais elevadas.
- No entanto, uma energia excessiva pode danificar o alvo ou o substrato, pelo que a otimização é crucial.
-
Tamanho do fio elétrodo na soldadura:
- Os eléctrodos de fio maiores podem depositar mais material por unidade de tempo, aumentando a taxa de deposição.
- Por exemplo, um elétrodo de fio de 1,4 mm a 250 amperes tem uma taxa de deposição de 3,5 kg/hora em posições planas ou horizontais.
-
Amperagem na soldadura:
- Uma amperagem mais elevada aumenta a entrada de calor e a taxa de fusão, conduzindo a taxas de deposição mais elevadas.
- A seleção adequada da amperagem garante uma deposição eficiente sem comprometer a qualidade da soldadura.
-
Posição de soldadura:
- A posição (por exemplo, plana, horizontal, vertical, suspensa) afecta a influência da gravidade sobre a poça de fusão, influenciando as taxas de deposição.
- As posições planas e horizontais permitem normalmente taxas de deposição mais elevadas em comparação com as posições verticais ou suspensas.
-
Composição do material e contaminação:
- Garantir a composição elementar correta no processo de soldadura é fundamental para alcançar as propriedades desejadas do material.
- A contaminação pode reduzir as taxas de deposição e comprometer a integridade da soldadura, tornando a monitorização essencial.
Ao compreender e otimizar estes factores, os soldadores e engenheiros podem alcançar taxas de deposição mais elevadas, mantendo a qualidade e a eficiência da soldadura.
Tabela de resumo:
Fator | Impacto na taxa de deposição |
---|---|
Potência do laser (Laser Cladding) | Uma potência mais elevada aumenta a taxa de deposição, mas corre o risco de sobreaquecimento ou deformação. |
Taxas de alimentação (Laser Cladding) | As taxas óptimas garantem uma adição consistente de material sem defeitos. |
Velocidade de deslocação (Laser Cladding) | As velocidades mais rápidas reduzem as taxas de deposição mas melhoram a produtividade. |
Caraterísticas do plasma | A temperatura, a composição e a densidade influenciam a qualidade da deposição. |
Propriedades do material alvo | Pontos de fusão mais baixos e rendimentos de pulverização mais elevados aumentam as taxas de deposição. |
Corrente e energia do feixe | Uma energia mais elevada aumenta as taxas de pulverização catódica, mas deve ser optimizada para evitar danos. |
Tamanho do elétrodo de fio | Os fios maiores depositam mais material por unidade de tempo, aumentando as taxas de deposição. |
Amperagem | Uma amperagem mais elevada aumenta a entrada de calor e a taxa de fusão, aumentando as taxas de deposição. |
Posição de soldadura | As posições plana e horizontal permitem taxas de deposição mais elevadas do que as posições vertical ou suspensa. |
Composição do material | Uma composição correta assegura as propriedades desejadas; a contaminação reduz as taxas de deposição. |
Pronto para otimizar o seu processo de soldadura? Contacte hoje os nossos especialistas para soluções à medida!