A escolha da temperatura de calcinação correta é um passo fundamental para garantir as propriedades e o desempenho desejados do material. A temperatura de calcinação influencia diretamente as transformações químicas e físicas do material, tais como a decomposição, as transições de fase e a cristalização. Para determinar a temperatura de calcinação adequada, é preciso considerar a estabilidade térmica do material, a fase ou estrutura desejada e as capacidades do equipamento. Segue-se uma explicação detalhada dos principais factores a considerar ao selecionar a temperatura de calcinação.
Pontos-chave explicados:
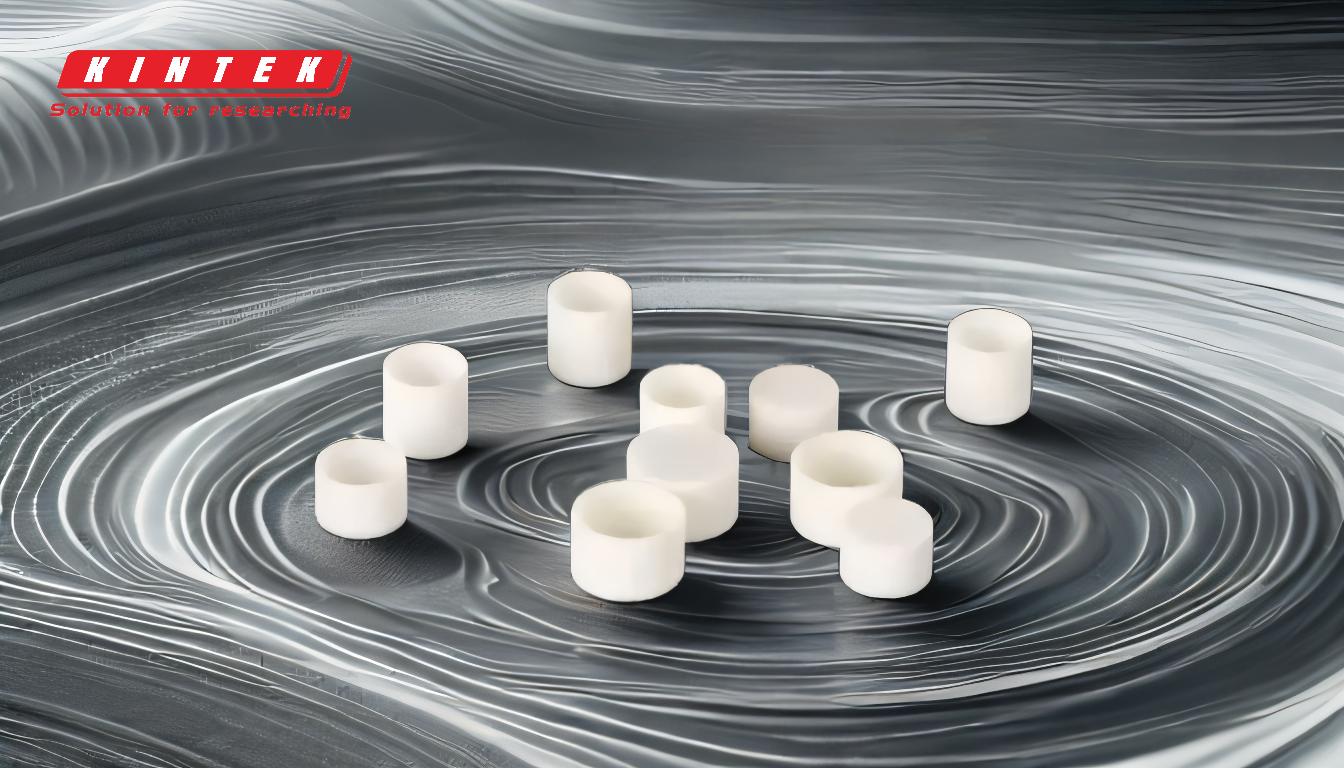
-
Compreender o comportamento térmico do material
- Temperatura de decomposição térmica: Determinar a temperatura a que o material sofre decomposição ou mudanças de fase. Isto pode ser identificado através de técnicas como a Análise Termogravimétrica (TGA) ou a Calorimetria Exploratória Diferencial (DSC).
- Temperatura de transição de fase: Identificar o intervalo de temperatura em que o material transita para a fase cristalina ou amorfa desejada.
- Estabilidade térmica: Assegurar que o material não se degrada nem perde as suas propriedades previstas à temperatura de calcinação escolhida.
-
Definir o resultado pretendido
- Pureza de fase: Se o objetivo é obter uma fase cristalina específica, a temperatura de calcinação deve estar alinhada com a temperatura de formação da fase.
- Tamanho e morfologia das partículas: Temperaturas mais elevadas podem levar ao crescimento do grão ou à sinterização, enquanto que temperaturas mais baixas podem resultar em reacções incompletas.
- Composição química: Assegurar que a temperatura de calcinação não provoca reacções indesejadas ou perda de componentes voláteis.
-
Considerar as limitações do equipamento
- Gama de temperaturas do forno: A temperatura máxima do forno deve exceder a temperatura de calcinação requerida em 100-200°C para garantir um desempenho consistente e evitar o funcionamento no limite superior do forno.
- Taxa de aquecimento e uniformidade: O forno deve proporcionar um aquecimento uniforme e um controlo preciso da temperatura para evitar gradientes térmicos que possam afetar as propriedades do material.
- Controlo da atmosfera: Se a calcinação exigir uma atmosfera específica (por exemplo, inerte, oxidante ou redutora), certifique-se de que o forno pode manter as condições exigidas.
-
Otimizar através de ensaios experimentais
- Experiências-piloto: Realizar experiências em pequena escala para testar diferentes temperaturas e durações de calcinação. Analisar as propriedades do material resultante para identificar a temperatura óptima.
- Refinamento iterativo: Ajustar a temperatura com base nos resultados experimentais, considerando factores como o rendimento, a pureza da fase e o tamanho das partículas.
- Caracterização: Utilizar técnicas como a difração de raios X (XRD), a microscopia eletrónica de varrimento (SEM) e a espetroscopia de infravermelhos com transformada de Fourier (FTIR) para avaliar o material após a calcinação.
-
Ter em conta as restrições práticas
- Eficiência energética: Temperaturas mais elevadas podem aumentar o consumo de energia e os custos operacionais. Equilibrar as propriedades desejadas do material com a eficiência energética.
- Considerações de segurança: Assegurar que a temperatura escolhida está dentro da gama de funcionamento seguro do equipamento e não apresenta riscos como sobreaquecimento ou degradação do material.
- Escalabilidade: Considerar se a temperatura escolhida pode ser atingida de forma consistente numa produção em grande escala.
-
Normas e literatura de referência do sector
- Investigação publicada: Rever estudos sobre materiais semelhantes para identificar as temperaturas de calcinação habitualmente utilizadas e os seus resultados.
- Recomendações do fabricante: Consultar os fabricantes de equipamentos para obter orientações sobre as temperaturas de funcionamento óptimas para materiais específicos.
- Dados históricos: Se for caso disso, utilizar dados de experiências anteriores ou de ciclos de produção para fundamentar a decisão.
Ao considerar cuidadosamente estes factores, é possível selecionar uma temperatura de calcinação que atinja as propriedades desejadas do material, assegurando simultaneamente um funcionamento eficiente e seguro. O processo envolve uma combinação de compreensão teórica, validação experimental e considerações práticas para otimizar as condições de calcinação.
Quadro de resumo:
Fator-chave | Descrição |
---|---|
Comportamento térmico do material | Identificar temperaturas de decomposição, de transição de fase e de estabilidade térmica. |
Resultado pretendido | Definir objectivos de pureza de fase, tamanho de partícula, morfologia e composição química. |
Limitações do equipamento | Considerar a gama de temperaturas do forno, a taxa de aquecimento, a uniformidade e a atmosfera. |
Ensaios experimentais | Realizar experiências-piloto e aperfeiçoar a temperatura de forma iterativa. |
Restrições práticas | Equilibrar a eficiência energética, a segurança e a escalabilidade. |
Normas do sector | Pesquisa de referência, recomendações do fabricante e dados históricos. |
Precisa de ajuda para selecionar a temperatura de calcinação perfeita? Contacte os nossos especialistas hoje mesmo para uma orientação personalizada!