O recozimento por indução é um processo de tratamento térmico que utiliza a indução electromagnética para aquecer materiais, normalmente metais, a uma temperatura específica para alterar as suas propriedades físicas e mecânicas.A temperatura para o recozimento por indução varia consoante o material a ser tratado, mas geralmente varia entre 500°C e 900°C para a maioria dos metais.O processo tem como objetivo aumentar a ductilidade e reduzir a dureza, reduzindo as deslocações na estrutura cristalina do material, tornando-o mais trabalhável e menos quebradiço.A temperatura exacta é crítica e deve ser cuidadosamente controlada para atingir as propriedades desejadas do material sem causar sobreaquecimento ou outros defeitos.
Pontos-chave explicados:
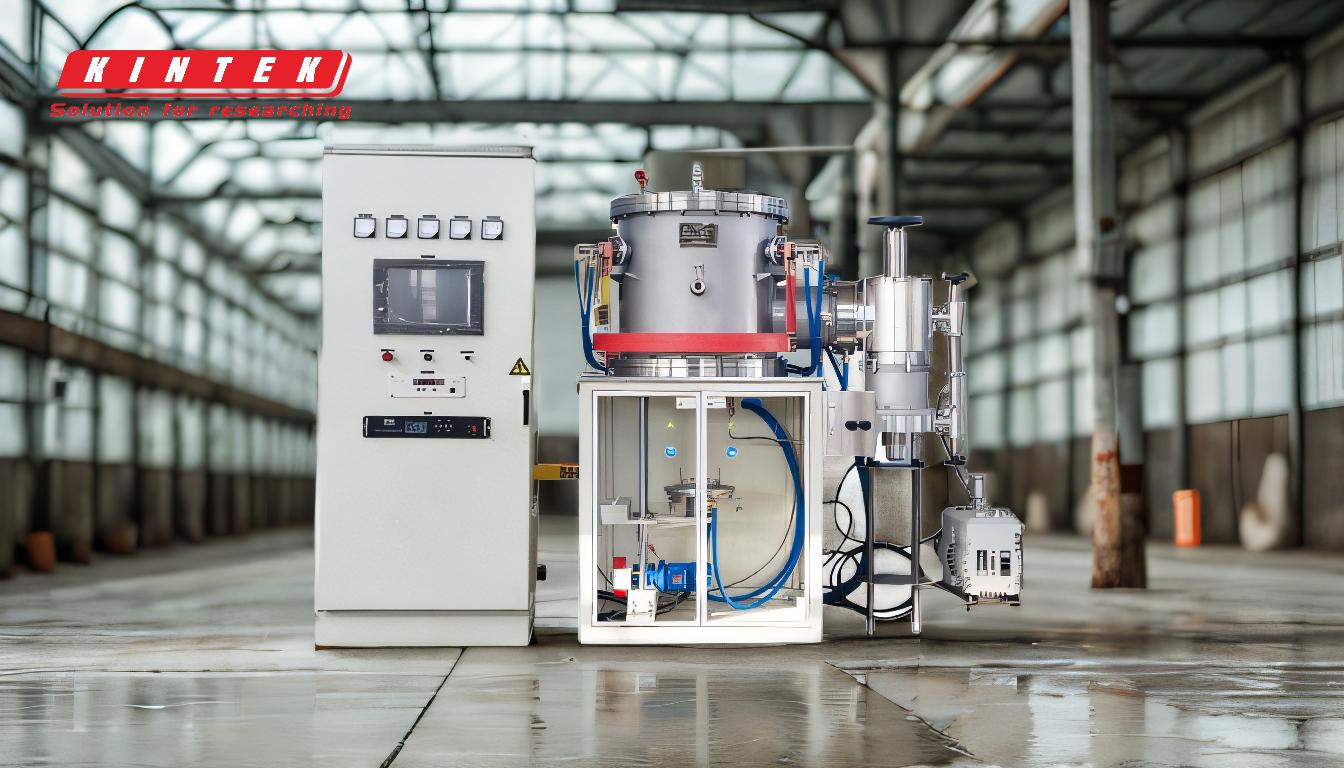
-
Definição de recozimento por indução:
- O recozimento por indução é um processo de tratamento térmico que utiliza a indução electromagnética para aquecer materiais, normalmente metais, a uma temperatura específica para alterar as suas propriedades físicas e mecânicas.
- O processo é utilizado para aumentar a ductilidade e reduzir a dureza, tornando o material mais trabalhável e menos quebradiço.
-
Gama de temperaturas para o recozimento por indução:
- A temperatura para o recozimento por indução varia consoante o material a tratar.
- Para a maioria dos metais, a gama de temperaturas situa-se normalmente entre 500°C e 900°C.
- A temperatura exacta é crítica e deve ser cuidadosamente controlada para atingir as propriedades desejadas do material sem causar sobreaquecimento ou outros defeitos.
-
Importância do controlo da temperatura:
- O controlo da temperatura é crucial no recozimento por indução para garantir que o material atinge as propriedades desejadas.
- O superaquecimento pode levar a mudanças indesejáveis na microestrutura do material, como crescimento de grãos ou transformações de fase, que podem afetar negativamente o desempenho do material.
- O subaquecimento pode não atingir a redução desejada da dureza e o aumento da ductilidade.
-
Considerações específicas do material:
- Diferentes materiais têm diferentes requisitos de temperatura de recozimento.
- Por exemplo, o aço requer tipicamente temperaturas de recozimento entre 700°C e 900°C, enquanto as ligas de alumínio podem requerer temperaturas mais baixas, cerca de 300°C a 500°C.
- A temperatura específica para um determinado material é determinada pela sua composição, microestrutura e propriedades finais desejadas.
-
Parâmetros do processo:
- Para além da temperatura, outros parâmetros do processo, como a taxa de aquecimento, o tempo de espera e a taxa de arrefecimento, são importantes no recozimento por indução.
- A taxa de aquecimento deve ser controlada para garantir um aquecimento uniforme e evitar tensões térmicas.
- O tempo de permanência à temperatura de recozimento permite a ocorrência das alterações microestruturais necessárias.
- A taxa de resfriamento pode afetar as propriedades finais do material, sendo que taxas de resfriamento mais lentas geralmente resultam em materiais mais macios e dúcteis.
-
Benefícios do recozimento por indução:
- O recozimento por indução oferece várias vantagens em relação ao recozimento tradicional em forno, incluindo taxas de aquecimento mais rápidas, controlo preciso da temperatura e aquecimento localizado.
- O processo pode ser facilmente automatizado e integrado às linhas de produção, tornando-o adequado para a fabricação de grandes volumes.
- O recozimento por indução também reduz o consumo de energia e minimiza o risco de oxidação e contaminação em comparação com o recozimento em forno.
-
Aplicações do recozimento por indução:
- O recozimento por indução é amplamente utilizado em várias indústrias, incluindo a automóvel, a aeroespacial e a eletrónica.
- As aplicações comuns incluem o recozimento de fios, tubos e chapas, bem como o tratamento térmico de componentes como engrenagens, rolamentos e fixadores.
- O processo é também utilizado na produção de semicondutores e outros componentes electrónicos em que é essencial um controlo preciso da temperatura.
Em resumo, o recozimento por indução é um processo de tratamento térmico versátil e eficiente que requer um controlo preciso da temperatura para atingir as propriedades desejadas do material.A faixa de temperatura para o recozimento indutivo normalmente fica entre 500°C e 900°C, dependendo do material a ser tratado.O controlo adequado dos parâmetros do processo, incluindo a taxa de aquecimento, o tempo de espera e a taxa de arrefecimento, é essencial para garantir o sucesso do processo de recozimento.O recozimento por indução oferece várias vantagens sobre os métodos tradicionais, incluindo taxas de aquecimento mais rápidas, controlo preciso da temperatura e consumo reduzido de energia, tornando-o uma técnica valiosa em várias aplicações industriais.
Tabela de resumo:
Aspeto | Detalhes |
---|---|
Gama de temperaturas | 500°C-900°C (varia consoante o material) |
Principais vantagens | Aquecimento mais rápido, controlo preciso, utilização de energia reduzida, contaminação mínima |
Aplicações | Automóvel, aeroespacial, eletrónica, recozimento de fios/tubos |
Parâmetros do processo | Taxa de aquecimento, tempo de espera, taxa de arrefecimento |
Necessidades específicas do material | Aço: 700°C-900°C; Alumínio: 300°C-500°C |
Optimize o seu processo de tratamento térmico com recozimento por indução contacte os nossos especialistas hoje !