Considerações gerais sobre a pulverização catódica de magnetrões
Manutenção do ambiente de vácuo
A pulverização catódica por magnetrão necessita de um ambiente de vácuo impecavelmente mantido para evitar os efeitos prejudiciais das impurezas transportadas pelo ar na qualidade da película. O ambiente de vácuo não é apenas um pano de fundo, mas um componente crítico que garante a integridade e a precisão do processo de pulverização catódica.
Nos fornos de vácuo, os componentes mecânicos, tais como os vedantes e as juntas de soldadura, são submetidos a uma manutenção rigorosa para manter o vácuo sem fugas. Esta manutenção meticulosa é essencial porque mesmo pequenas fugas podem comprometer os níveis de vácuo, afectando assim a qualidade do produto final. O processo de identificação e correção destas fugas é moroso e trabalhoso, o que sublinha a importância da manutenção preventiva.
Além disso, a contaminação dos componentes internos do forno pode ter várias origens, incluindo gases residuais e partículas, que podem infiltrar-se no sistema durante as actividades de manutenção. Esta contaminação pode levar a propriedades de película inconsistentes, necessitando de protocolos de limpeza e validação minuciosos para garantir que o ambiente de vácuo permanece imaculado.
Aspeto da manutenção | Importância |
---|---|
Integridade do selo | Garante um vácuo sem fugas; fundamental para manter os níveis de vácuo operacionais. |
Juntas de brasagem | Requerem inspeção e manutenção regulares para evitar fugas. |
Componentes internos do forno | Devem ser mantidos livres de contaminação para manter a qualidade do filme. |
Em resumo, a manutenção do ambiente de vácuo é uma pedra angular do processo de pulverização catódica por magnetrão, exigindo uma atenção meticulosa aos detalhes e medidas preventivas rigorosas para garantir a produção de películas de alta qualidade.
Controlo da taxa de deposição
A taxa de deposição é um parâmetro crítico no processo de pulverização catódica por magnetrão, influenciando significativamente a qualidade e a espessura da película. Esta taxa determina a rapidez com que o material do alvo é transferido para o substrato, afectando assim a uniformidade, a densidade e as propriedades finais da película depositada.
Para obter resultados óptimos, a taxa de deposição deve ser meticulosamente controlada e ajustada de acordo com condições específicas. Factores como o tipo de material alvo, a espessura de película desejada e as propriedades específicas necessárias para a aplicação desempenham um papel importante na determinação da taxa de deposição adequada. Por exemplo, uma taxa de deposição mais elevada pode ser adequada para aplicações que exijam películas mais espessas, mas também pode levar a problemas como uma fraca aderência ou não uniformidade se não for gerida corretamente.
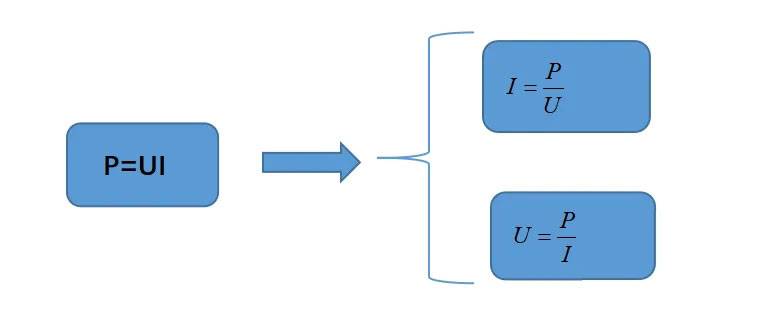
Fator | Impacto na taxa de deposição |
---|---|
Material alvo | Diferentes materiais têm rendimentos de pulverização diferentes, o que afecta a taxa de deposição. |
Temperatura do substrato | Temperaturas mais altas podem melhorar a adesão do filme, mas também podem alterar a taxa de deposição. |
Potência de pulverização | O aumento da potência normalmente resulta em uma taxa de deposição mais alta, mas deve ser equilibrado com outros parâmetros. |
Em resumo, o controlo preciso da taxa de deposição é essencial para produzir películas de PZT de alta qualidade. Este controlo garante que a película não só cumpre as especificações de espessura exigidas, mas também apresenta as propriedades desejadas, como a condutividade eléctrica e a resistência mecânica.
Controlo da Potência e do Tempo de Sputtering
A potência e o tempo de pulverização são parâmetros críticos que influenciam significativamente a qualidade do filme. Estes factores devem ser meticulosamente ajustados para se alinharem com as caraterísticas e requisitos específicos do material a ser processado. O nível de potência durante a pulverização catódica afecta a energia transmitida ao material alvo, que por sua vez determina a velocidade a que os átomos são ejectados e depositados no substrato. Níveis de potência mais elevados resultam geralmente em taxas de deposição mais rápidas, mas também podem levar a um aumento do calor e da tensão no substrato, potencialmente causando defeitos ou alterando as propriedades desejadas da película.
Por outro lado, a duração do processo de pulverização catódica, ou tempo de pulverização catódica, tem um impacto direto na espessura e uniformidade da película depositada. Tempos prolongados de pulverização catódica podem produzir películas mais espessas, mas também aumentam o risco de contaminação e a probabilidade de obter uma espessura não uniforme em todo o substrato. Por conseguinte, é essencial equilibrar a potência e o tempo de pulverização catódica para obter uma qualidade óptima da película.
Para ilustrar a importância desses parâmetros, considere a tabela a seguir:
Potência de pulverização (W) | Tempo de pulverização (min) | Espessura da película (nm) | Qualidade da película (classificação 1-10) |
---|---|---|---|
100 | 30 | 200 | 8 |
150 | 20 | 250 | 7 |
200 | 15 | 300 | 6 |
Neste exemplo, embora uma potência mais elevada e tempos mais curtos resultem em películas mais espessas, a qualidade da película diminui devido ao aumento da tensão e a potenciais defeitos. Assim, a seleção da potência e do tempo de pulverização catódica adequados é um processo complexo que requer uma análise cuidadosa das propriedades do material e das caraterísticas da película pretendida.
Material alvo e preparação da superfície
Seleção do Material Alvo Adequado
A seleção do material alvo é um passo crítico no processo de pulverização catódica por magnetrão, influenciando significativamente a qualidade e o desempenho da película resultante. A escolha do material alvo afecta diretamente a composição química, a integridade estrutural e as propriedades funcionais da película depositada. Por conseguinte, é essencial selecionar um material alvo que se alinhe com os requisitos específicos e os resultados desejados da película.
Ao escolher um material alvo, devem ser considerados vários factores:
-
Composição química: O material alvo deve corresponder à composição química desejada da película. Por exemplo, na preparação de películas de titanato de zirconato de chumbo (PZT), o alvo deve idealmente consistir numa mistura homogénea de óxidos de chumbo, zircónio e titânio.
-
Pureza: A elevada pureza do material alvo é crucial para evitar a introdução de impurezas na película, o que pode degradar as suas propriedades. Quaisquer contaminantes podem dar origem a defeitos, reduzir a densidade da película e afetar o seu desempenho global.
-
Propriedades físicas: As propriedades físicas do alvo, tais como a sua densidade e condutividade térmica, podem influenciar o processo de pulverização catódica e as caraterísticas da película resultante. Por exemplo, um material alvo mais denso resultará numa taxa de deposição mais uniforme.
-
Condição da superfície: A superfície do material alvo deve ser lisa e livre de defeitos para garantir uma pulverização eficiente e uniforme. Podem ser necessários tratamentos de superfície para obter a planura e a limpeza necessárias.
A tabela abaixo resume as principais considerações para a seleção de um material alvo adequado:
Consideração | Importância |
---|---|
Composição química | Assegura as propriedades químicas desejadas da película. |
Pureza | Evita a contaminação e mantém a qualidade da película. |
Propriedades físicas | Influencia a eficiência da pulverização catódica e a uniformidade da película. |
Condição da superfície | Garante uma pulverização eficiente e uniforme, evitando defeitos na película. |
Em resumo, a seleção do material alvo é uma decisão multifacetada que requer uma consideração cuidadosa de vários factores para obter películas de alta qualidade e elevado desempenho.
Garantir a pureza e a planura da superfície do alvo
A pureza e a planura da superfície do alvo são factores críticos que influenciam significativamente o processo de pulverização catódica e a qualidade da película resultante. Quaisquer impurezas ou irregularidades na superfície do alvo podem levar a inconsistências na deposição da película de PZT, afectando o seu desempenho geral e uniformidade.
Para garantir resultados óptimos, a superfície alvo deve ser submetida a rigorosos protocolos de tratamento e inspeção da superfície. Isto envolve:
-
Limpeza da superfície: Eliminação de quaisquer contaminantes, como poeiras, óleos ou óxidos, que possam comprometer a pureza do alvo. São normalmente utilizadas técnicas como a limpeza por ultra-sons, a gravação química e a limpeza por feixe de iões.
-
Inspeção da planicidade: Utilização de ferramentas de metrologia avançadas, como profilómetros e interferómetros, para medir a topografia da superfície. Quaisquer desvios da planicidade desejada devem ser corrigidos através de polimento ou outras medidas corretivas.
Tratamento da superfície | Objetivo | Técnicas comuns |
---|---|---|
Limpeza da superfície | Remoção de contaminantes | Limpeza por ultra-sons, gravura química, limpeza por feixe de iões |
Inspeção de planicidade | Verificar a uniformidade da superfície | Profilómetros, Interferómetros |
Ao seguir meticulosamente estes procedimentos, a pureza e a planicidade da superfície alvo podem ser asseguradas, melhorando assim a qualidade e a consistência da película de PZT produzida por pulverização catódica com magnetrões.
Controlo do substrato e do ambiente
Controlo da temperatura do substrato
A temperatura do substrato desempenha um papel fundamental na determinação das propriedades finais da película depositada, como a cristalinidade, a densidade e a rugosidade da superfície. Estas propriedades são críticas para o desempenho e funcionalidade da película, tornando o controlo preciso da temperatura um aspeto essencial do processo de pulverização catódica por magnetrão.
Quando a temperatura do substrato é demasiado baixa, a película pode apresentar uma fraca cristalinidade e uma baixa densidade, conduzindo a um aumento da rugosidade da superfície. Por outro lado, se a temperatura for demasiado elevada, pode causar alterações de fase indesejáveis ou mesmo danos térmicos no substrato. Por conseguinte, a temperatura deve ser meticulosamente ajustada com base nas caraterísticas e requisitos específicos do material que está a ser depositado.
Por exemplo, no caso de películas de titanato de zirconato de chumbo (PZT), a temperatura ideal do substrato pode variar significativamente, dependendo da estrutura de fase desejada e das propriedades ferroeléctricas. Normalmente, são utilizadas temperaturas entre 400°C e 600°C para obter a fase de perovskite desejada e a resposta piezoeléctrica ideal.
Para garantir um controlo preciso, os sistemas modernos de pulverização catódica incorporam frequentemente mecanismos avançados de monitorização e controlo da temperatura, tais como termómetros de infravermelhos e controladores PID. Estas ferramentas permitem ajustes em tempo real, assegurando que a temperatura do substrato se mantém dentro do intervalo ótimo durante todo o processo de deposição.
Intervalo de temperatura | Propriedades da película |
---|---|
< 400°C | Baixa cristalinidade, baixa densidade, alta rugosidade |
400°C - 600°C | Fase de perovskite desejada, resposta piezoeléctrica óptima |
> 600°C | Possíveis mudanças de fase, danos térmicos |
Em resumo, o controlo da temperatura do substrato é um parâmetro crítico no processo de pulverização catódica por magnetrão, influenciando diretamente a qualidade e o desempenho da película depositada. A gestão adequada da temperatura garante que a película cumpre as especificações exigidas e melhora a sua funcionalidade global.
Assegurar o controlo do vácuo e da atmosfera
O processo de pulverização catódica para a preparação de camadas de película de titanato de zirconato de chumbo (PZT) é altamente sensível às condições ambientais. Para obter resultados óptimos, tem de ser conduzido num ambiente de alto vácuo meticulosamente controlado. Este requisito rigoroso não é negociável, uma vez que tem um impacto direto na integridade e no desempenho da película de PZT.
Num ambiente de alto vácuo, a ausência de gases atmosféricos reduz significativamente o risco de contaminação. As partículas transportadas pelo ar, a humidade e outras impurezas podem introduzir defeitos na película, comprometendo as suas propriedades estruturais e eléctricas. Ao manter o vácuo, estes potenciais contaminantes são efetivamente eliminados, garantindo uma superfície de deposição imaculada.
Além disso, o controlo das condições atmosféricas vai para além da mera manutenção do vácuo. Também envolve a prevenção da oxidação, que pode alterar a composição química da película de PZT. A oxidação pode levar a variações na estequiometria da película, afectando as suas propriedades ferroeléctricas e piezoeléctricas. Por conseguinte, a manutenção de uma atmosfera controlada é crucial para preservar as caraterísticas químicas e físicas desejadas da película de PZT.
Para alcançar e manter este ambiente de alto vácuo, são utilizados sistemas de vácuo avançados. Estes sistemas incluem bombas de alta eficiência, detectores de fugas e sensores de pressão que funcionam em conjunto para manter o nível de vácuo necessário. A monitorização e calibração regulares destes sistemas são essenciais para garantir um controlo de vácuo contínuo e fiável.
Em resumo, garantir o controlo do vácuo e da atmosfera é um aspeto crítico do processo de pulverização catódica com magnetrões para a preparação de películas de PZT. Não só protege contra a contaminação e a oxidação, como também assegura a consistência e a qualidade da película depositada. Este controlo meticuloso é a pedra angular de todo o processo, sustentando o fabrico bem sucedido de películas de PZT de elevado desempenho.
Controlo da uniformidade
A uniformidade é uma propriedade crítica das películas finas, particularmente no contexto da preparação de películas de Titanato de Zirconato de Chumbo (PZT) por pulverização catódica magnetrónica. Conseguir uma deposição uniforme da película é essencial para garantir um desempenho consistente e fiabilidade em todo o substrato. Esta uniformidade é gerida principalmente através de um controlo meticuloso do processo de pulverização catódica, que envolve vários parâmetros e técnicas fundamentais.
Em primeiro lugar, o posicionamento e a orientação da fonte de pulverização e do substrato desempenham um papel fundamental na obtenção de uma deposição uniforme da película. A fonte de pulverização catódica, normalmente um material alvo, deve ser colocada a uma distância óptima do substrato para assegurar que os átomos ou partículas ejectados do alvo são distribuídos uniformemente pela superfície. Além disso, o ângulo a que estas partículas se deslocam para o substrato deve ser cuidadosamente controlado para evitar qualquer desvio direcional no processo de deposição.
Em segundo lugar, a utilização de técnicas avançadas, como a rotação do substrato, pode aumentar significativamente a uniformidade. Ao rodar o substrato durante o processo de pulverização catódica, a deposição da película torna-se mais uniformemente distribuída, atenuando os efeitos de quaisquer variações localizadas na saída da fonte de pulverização catódica. Este método garante que cada parte do substrato receba uma quantidade consistente de material, levando a uma película final mais uniforme.
Parâmetro de controlo | Impacto na uniformidade |
---|---|
Posição da Fonte de Sputtering | Garante a distribuição uniforme das partículas |
Ângulo do substrato | Evita o desvio direcional na deposição |
Rotação do substrato | Melhora a distribuição uniforme do material |
Em resumo, a obtenção de uniformidade na deposição de películas finas requer uma combinação de controlo preciso sobre a fonte de pulverização e o substrato, bem como a utilização estratégica de técnicas como a rotação do substrato. Estas medidas contribuem coletivamente para a produção de películas de PZT uniformes e de alta qualidade, que são essenciais para as aplicações pretendidas.
Monitorização do processo e pós-tratamento
Monitoramento e Ajuste da Potência de Sputtering
A potência de pulverização é um parâmetro crítico no processo de pulverização catódica por magnetrão, influenciando significativamente a espessura e a composição da película depositada. O nível de potência afecta diretamente a energia dos iões que bombardeiam o material alvo, o que, por sua vez, determina a taxa a que o material é ejectado e depositado no substrato. Por exemplo, uma maior potência de pulverização catódica resulta normalmente em taxas de deposição mais rápidas, mas também pode levar a um aumento da rugosidade e da não uniformidade da película se não for corretamente gerida.
Para garantir uma qualidade óptima da película, é essencial monitorizar e ajustar dinamicamente a potência de pulverização catódica. Isto implica a utilização de sistemas de monitorização avançados que podem fornecer dados em tempo real sobre os níveis de potência, taxas de deposição e propriedades da película. Ao correlacionar essas métricas, os operadores podem ajustar a potência de pulverização para atingir as caraterísticas desejadas do filme. Por exemplo, se a espessura da película se desviar do objetivo, a potência de pulverização pode ser ajustada para compensar, garantindo uma espessura de camada consistente em todo o substrato.
Além disso, a composição da película pode ser influenciada pela potência de pulverização. Diferentes níveis de potência podem causar diferentes graus de pulverização de diferentes elementos num alvo multicomponente, levando a alterações na estequiometria da película. Por conseguinte, é necessário um controlo preciso da potência de pulverização para manter a composição química desejada da película. Isto é particularmente importante na preparação de películas de óxidos complexos, como o titanato de zirconato de chumbo (PZT), em que a manutenção da proporção correta de chumbo, zircónio e titânio é crucial para obter as propriedades eléctricas e mecânicas desejadas.
Em suma, a monitorização e o ajuste da potência de pulverização não se limitam ao controlo da taxa de deposição, mas também à obtenção do equilíbrio correto entre a espessura, a uniformidade e a composição da película. Este controlo dinâmico garante que o produto final cumpre os requisitos rigorosos para aplicações em eletrónica, ótica e outros campos de alta tecnologia.
Pós-tratamento de películas
Os processos de pós-tratamento são passos cruciais na preparação de películas de Titanato de Zirconato de Chumbo (PZT), com o objetivo de melhorar as suas propriedades e garantir a estabilidade a longo prazo. Estes tratamentos incluem frequentementerecozimento eoxidaçãoque são concebidos para refinar a microestrutura da película e melhorar as suas caraterísticas mecânicas e eléctricas.
Recozimento
O recozimento consiste em aquecer a película a uma temperatura específica e depois arrefecê-la lentamente. Este processo pode
- Aumentar a cristalinidade: Ao promover o crescimento de cristais maiores e mais uniformes, o recozimento pode melhorar significativamente a integridade estrutural da película.
- Reduzir o stress: As tensões internas dentro da película podem ser aliviadas, levando a um material mais estável e durável.
- Melhorar as propriedades eléctricas: A constante dieléctrica e as propriedades ferroeléctricas da película podem ser optimizadas através do recozimento controlado.
Oxidação
A oxidação da película envolve a sua exposição a um ambiente rico em oxigénio, o que pode:
- Estabilizar a camada de óxido: Assegurar que a camada de óxido da superfície da película é uniforme e estável pode evitar problemas como a delaminação e a degradação ao longo do tempo.
- Aumentar a resistência química: Uma superfície oxidada é menos suscetível a ataques químicos, tornando a película mais robusta em vários ambientes.
- Controlo da rugosidade da superfície: A oxidação pode ajudar a suavizar quaisquer irregularidades na superfície da película, melhorando a sua qualidade e desempenho globais.
Tanto o recozimento como a oxidação são fundamentais no pós-tratamento, uma vez que não só resolvem problemas imediatos de qualidade como também contribuem para o desempenho e a fiabilidade da película a longo prazo.
Controlo de qualidade e testes
As películas preparadas são submetidas a um rigoroso controlo de qualidade e a testes para garantir que cumprem os rigorosos requisitos necessários para as aplicações a que se destinam. Este processo envolve múltiplas facetas, cada uma meticulosamente avaliada para garantir a integridade e o desempenho das películas.
Parâmetros-chave para o controlo de qualidade
-
Morfologia da superfície: A superfície da película é examinada em microscópios de alta resolução para detetar quaisquer defeitos, tais como fissuras, buracos ou irregularidades. Este passo é crucial, uma vez que as imperfeições da superfície podem afetar significativamente a funcionalidade da película.
-
Medição da espessura: A espessura da película é medida utilizando instrumentos de precisão como elipsómetros ou profilómetros. A consistência da espessura é essencial para a uniformidade das propriedades eléctricas e mecânicas da película.
-
Análise da composição: A composição química da película é analisada utilizando técnicas como a difração de raios X (XRD) e a espetroscopia de raios X por dispersão de energia (EDS). Isto garante que a composição da película corresponde à estequiometria desejada, o que é fundamental para a utilização pretendida.
-
Propriedades eléctricas: São realizados testes eléctricos, incluindo medições de resistividade, capacitância e constante dieléctrica, para avaliar o desempenho da película em aplicações eléctricas. Estas propriedades são diretamente influenciadas pela estrutura e composição da película.
Métodos e instrumentos de ensaio
Parâmetro | Método de ensaio | Instrumento utilizado |
---|---|---|
Morfologia da superfície | Microscopia | Microscópio eletrónico de varrimento (SEM) |
Medição da espessura | Técnicas ópticas e mecânicas | Elipsómetro, Profilómetro |
Análise da composição | Técnicas espectroscópicas | Difração de raios X (XRD), EDS |
Propriedades eléctricas | Medições eléctricas | Medidor LCR, Analisador de impedância |
Ao avaliar sistematicamente estes parâmetros, o processo de controlo de qualidade assegura que cada película cumpre as normas predefinidas, garantindo assim a fiabilidade e o desempenho do produto final.
Melhoria contínua e considerações ambientais
Melhoria contínua e otimização
A preparação de películas finas é um processo iterativo que exige uma análise e um aperfeiçoamento contínuos para se obterem resultados óptimos. O processo de preparação, desde a configuração inicial até ao produto final, requer uma análise meticulosa e uma melhoria para aumentar a qualidade e a eficiência da película. Este aperfeiçoamento contínuo envolve vários aspectos fundamentais:
-
Monitorização dos parâmetros do processo: A monitorização regular e o ajuste de parâmetros críticos como a potência de pulverização, a taxa de deposição e a temperatura do substrato são essenciais. Estes parâmetros influenciam significativamente as propriedades da película, incluindo a sua espessura, uniformidade e qualidade global.
-
Actualizações tecnológicas: A incorporação de tecnologias e metodologias avançadas pode levar a melhorias substanciais. Por exemplo, a utilização de sistemas automatizados para monitorização e controlo em tempo real pode reduzir o erro humano e aumentar a consistência do processo.
-
Controlo de qualidade: São indispensáveis medidas rigorosas de controlo de qualidade. Isto inclui testes exaustivos da morfologia da superfície, espessura, composição e propriedades eléctricas da película para garantir que cumpre as normas exigidas.
-
Circuitos de feedback: O estabelecimento de circuitos de feedback eficazes permite a rápida identificação e correção de quaisquer desvios em relação aos resultados desejados. Esta abordagem iterativa garante que cada ciclo de preparação da película seja melhor do que o anterior.
-
Considerações ambientais: Ao mesmo tempo que se melhora a qualidade da película, é também crucial ter em conta o impacto ambiental do processo de preparação. A adoção de métodos eficientes em termos energéticos e a minimização dos resíduos podem contribuir para um ciclo de produção mais sustentável.
Ao analisar e aperfeiçoar continuamente estes aspectos, o processo de preparação pode ser optimizado para produzir películas de alta qualidade com maior eficiência e menor impacto ambiental.
Proteção ambiental e consumo de energia
Na procura de práticas sustentáveis no processo de pulverização catódica por magnetrões, deve ser dada especial atenção à proteção ambiental e ao consumo de energia. Os métodos tradicionais de pulverização catódica, embora eficazes, apresentam muitas vezes desvantagens ambientais e energéticas significativas. Para os atenuar, a adoção de técnicas de preparação mais ecológicas e eficientes do ponto de vista energético não é apenas uma recomendação, mas uma necessidade.
Uma abordagem para o conseguir é através da otimização dos parâmetros de pulverização catódica. Através do ajuste fino de factores como a potência de pulverização, a taxa de deposição e a temperatura do substrato, é possível reduzir a pegada energética global do processo. Por exemplo, podem ser utilizadas potências de pulverização mais baixas sem comprometer a qualidade da película, conservando assim a energia. Além disso, a utilização de tecnologias de vácuo avançadas pode ajudar a manter um ambiente mais limpo, minimizando a libertação de gases e partículas nocivos para a atmosfera.
Além disso, a seleção de materiais desempenha um papel crucial na sustentabilidade ambiental. Optar por materiais-alvo que sejam menos tóxicos e tenham um menor impacto ambiental pode aumentar significativamente o carácter ecológico do processo. Isto não só protege o ambiente como também assegura a conformidade com regulamentos ambientais cada vez mais rigorosos.
Em resumo, embora o foco principal da pulverização catódica por magnetrão seja a qualidade e o desempenho da película de PZT, a integração de considerações ambientais e energéticas no processo de preparação é igualmente importante. Esta abordagem holística garante que os avanços na tecnologia da película estão alinhados com os objectivos mais amplos de gestão ambiental e sustentabilidade.
CONTACTE-NOS PARA UMA CONSULTA GRATUITA
Os produtos e serviços da KINTEK LAB SOLUTION foram reconhecidos por clientes de todo o mundo. A nossa equipa terá todo o prazer em ajudar com qualquer questão que possa ter. Contacte-nos para uma consulta gratuita e fale com um especialista de produto para encontrar a solução mais adequada para as suas necessidades de aplicação!