Introdução aos fornos de vácuo de molibdénio
Os fornos de vácuo de molibdéniosão fundamentais em aplicações de alta temperatura, tirando partido das propriedades únicas do molibdénio para se destacarem em ambientes exigentes. Estes sistemas avançados não são apenas essenciais para a sinterização em atmosfera de alta temperatura, mas também para a sinterização por vácuo de vários materiais, demonstrando a sua versatilidade e o seu papel crítico nos processos industriais modernos. Este artigo analisa as caraterísticas complexas, a construção e as aplicações dos fornos de vácuo de molibdénio, fornecendo informações sobre os seus sistemas de controlo avançados e estratégias de manutenção, essenciais para garantir um desempenho e uma longevidade ideais.
Principais caraterísticas e objectivos dos fornos de vácuo de molibdénio
Os fornos de vácuo de molibdénio são peças especializadas de equipamento concebidas para o processamento a alta temperatura num ambiente de vácuo controlado. Estes fornos são particularmente conhecidos pela sua utilização na sinterização em atmosfera de alta temperatura e sinterização em vácuo de vários materiais, que incluem cerâmica, metais e compósitos. As propriedades únicas do molibdénio, tais como o seu elevado ponto de fusão, excelente condutividade térmica e resistência ao choque térmico, fazem dele um material ideal para elementos de aquecimento nestes fornos.
Estabilidade e eficiência a altas temperaturas
Uma das principais caraterísticas dos fornos de vácuo de molibdénio é a sua capacidade de manter a estabilidade a altas temperaturas. O molibdénio pode funcionar a temperaturas até 1700°C, o que é crucial para processos como a sinterização, em que o controlo preciso da temperatura é essencial. A elevada condutividade térmica do molibdénio assegura uma transferência de calor eficiente, permitindo um aquecimento rápido e uma distribuição uniforme da temperatura dentro da câmara do forno. Esta eficiência é particularmente importante em aplicações industriais em que o tempo e os custos de energia são factores significativos.
Desempenho do vácuo e controlo da contaminação
Os fornos de vácuo de molibdénio são concebidos para funcionar em vácuo ou numa atmosfera controlada, o que é essencial para evitar a contaminação dos materiais que estão a ser processados. O ambiente de vácuo elimina a presença de oxigénio e outros gases que poderiam reagir com os materiais a altas temperaturas, preservando assim a sua pureza e integridade. Esta caraterística é particularmente benéfica no processamento de materiais de elevada pureza e em aplicações em que os níveis de contaminação devem ser mantidos a um nível mínimo.
Versatilidade nas aplicações
A versatilidade dos fornos de vácuo de molibdénio estende-se a uma vasta gama de aplicações para além da sinterização. Estas incluem o tratamento térmico, a brasagem, o recozimento e o processamento de materiais avançados, tais como cerâmicas transparentes e compósitos de matriz metálica. Cada uma destas aplicações beneficia do controlo preciso da temperatura e do ambiente livre de contaminação proporcionado pelo forno.
Componentes estruturais e design
O design de um forno de vácuo de molibdénio incorpora vários componentes chave que asseguram a sua funcionalidade e eficiência. Estes incluem:
- Corpo e tampa do forno: Construídos em aço inoxidável de alta qualidade, o corpo e a tampa do forno são concebidos para manter um vácuo elevado e são frequentemente arrefecidos a água para suportar as altas temperaturas.
- Elementos de aquecimento: Fabricados em molibdénio de alta pureza, estes elementos são cruciais para atingir e manter as temperaturas necessárias.
- Telas de isolamento: São utilizadas para minimizar a perda de calor e garantir uma distribuição uniforme da temperatura dentro da câmara do forno.
- Sistema de vácuo: Composto por bombas, válvulas e manómetros, o sistema de vácuo é essencial para manter o ambiente de vácuo e controlar a atmosfera dentro do forno.
- Sistema de controlo: Os sistemas de controlo avançados, muitas vezes incluindo PLC e interfaces de computador, permitem um controlo preciso dos parâmetros do forno, garantindo a reprodutibilidade e a segurança no funcionamento.
Manutenção e precauções
Embora os fornos de vácuo de molibdénio ofereçam numerosas vantagens, também exigem uma manutenção e um funcionamento cuidadosos para garantir a longevidade e o desempenho. O molibdénio é sensível à oxidação e à contaminação, pelo que os fornos devem ser operados em condições estritamente controladas. A manutenção regular, incluindo a inspeção e substituição de elementos de aquecimento e vedantes, é crucial para evitar falhas e garantir que o forno funciona com a máxima eficiência.
Em conclusão, os fornos de vácuo de molibdénio são ferramentas indispensáveis no processamento a alta temperatura, oferecendo estabilidade a alta temperatura, transferência de calor eficiente e um ambiente livre de contaminação. A sua versatilidade e precisão fazem deles um componente chave no avanço da ciência dos materiais e das tecnologias de processamento industrial.
Construção e composição dos fornos de vácuo de molibdénio
Os fornos de vácuo de molibdénio são peças sofisticadas de equipamento concebidas para aplicações de alta temperatura sob vácuo ou atmosferas controladas. Estes fornos são cruciais para processos como a sinterização, o tratamento térmico e a brasagem, em que é essencial manter um ambiente imaculado. A construção destes fornos envolve vários componentes chave, cada um concebido para funcionar sem problemas em condições extremas.
Componentes estruturais
Corpo e tampa do forno: O corpo do forno é normalmente construído em aço inoxidável, conhecido pela sua resistência à corrosão e à deformação a alta temperatura. Os invólucros interior e exterior são frequentemente fabricados em aço inoxidável 304, sendo a superfície exterior polida com espelho para aumentar a durabilidade e a estética. A tampa, que é amovível, inclui um mecanismo de arrefecimento a água na sua secção central para evitar o sobreaquecimento e garantir uma vedação estanque quando fechada.
Fundo e sistema de vácuo: A parte inferior do forno, semelhante à tampa, incorpora refrigeração por água e possui portas para eléctrodos, termopares e outros instrumentos de monitorização. O sistema de vácuo é parte integrante do funcionamento do forno, consistindo numa combinação de bombas de vácuo, válvulas e manómetros. Estes componentes trabalham em conjunto para atingir e manter os níveis de vácuo necessários, cruciais para evitar a oxidação e a contaminação dos materiais que estão a ser processados.
Elementos de aquecimento e ecrã de isolamento: O coração do forno reside nos seus elementos de aquecimento, frequentemente fabricados em molibdénio de elevada pureza. O molibdénio é escolhido pela sua excelente resistência a altas temperaturas e pela sua capacidade de manter a integridade estrutural até 1700°C. Os elementos de aquecimento são concebidos para funcionar a altas densidades de potência, garantindo um aquecimento rápido e uniforme. A tela de isolamento, normalmente feita de materiais como tungsténio e aço inoxidável, ajuda a manter a temperatura dentro do forno e a reduzir a perda de calor.
Considerações operacionais
Sistemas de manuseamento e controlo de materiais: Os fornos de vácuo de molibdénio estão equipados com sistemas de controlo avançados que permitem uma gestão precisa da temperatura e o controlo do processo. Estes sistemas podem ser automatizados, utilizando PLC e interfaces de ecrã tátil, permitindo aos operadores monitorizar e ajustar os parâmetros em tempo real. A inclusão de controlo computorizado não só aumenta a eficiência como também garante a repetibilidade e a segurança em processos de alta temperatura.
Caraterísticas de arrefecimento e segurança: Dadas as elevadas temperaturas de funcionamento, os sistemas de arrefecimento são cruciais para a longevidade dos componentes do forno. Camisas arrefecidas a água à volta do corpo, tampa e fundo do forno ajudam a dissipar o calor e a evitar danos estruturais. As caraterísticas de segurança, como as válvulas de alívio de pressão e as funções de paragem de emergência, também estão integradas para proteger tanto o equipamento como os operadores.
Aplicações e vantagens
Os fornos de vácuo de molibdénio são ferramentas versáteis, utilizadas numa variedade de indústrias, incluindo metalurgia, cerâmica e eletrónica. A sua capacidade de funcionar sob vácuo ou em atmosferas controladas torna-os ideais para processos que exigem elevada pureza e contaminação mínima. A utilização de elementos de aquecimento de molibdénio assegura um aquecimento eficiente e fiável, contribuindo para a qualidade geral e a consistência dos produtos finais.
Em conclusão, a construção e a composição dos fornos de vácuo de molibdénio são meticulosamente concebidas para satisfazer as exigências das aplicações de alta temperatura e alta pureza. Cada componente, desde o corpo do forno até aos elementos de aquecimento, desempenha um papel fundamental para garantir que o forno funcione de forma eficiente e segura, tornando-o uma ferramenta indispensável em ambientes avançados de fabrico e investigação.
Sistemas de controlo em fornos de vácuo de molibdénio
Os fornos de vácuo de molibdénio são parte integrante do processamento a alta temperatura e da síntese de materiais, empregando sistemas de controlo avançados para garantir precisão e eficiência. Estes sistemas de controlo, que incluem sistemas de controlo automático por computador e sistemas de controladores lógicos programáveis (PLC), são fundamentais na gestão de processos complexos e na manutenção de operações óptimas do forno.
Sistemas de controlo automático por computador
Os sistemas de controlo automático por computador em fornos de vácuo de molibdénio são concebidos para lidar com funções de controlo lógico complexas, monitorização contínua de parâmetros de processo e gestão de dados. Estes sistemas utilizam hardware e software informáticos dedicados para supervisionar operações como taxas de refusão, controlo de abertura de arco e aquisição de dados. Um PC de interface do operador (OIP) serve como interface principal entre o operador e o processo do forno, fornecendo visualização do processo em tempo real, ajustes de parâmetros e gestão de receitas. O OIP também pode ser equipado com uma interface de rede Ethernet para transferência de dados para outros computadores em rede, melhorando a integração do sistema e a acessibilidade dos dados.
Controladores lógicos programáveis (PLCs)
Os PLCs revolucionaram o controlo dos fornos de vácuo, substituindo os sistemas tradicionais baseados em relés por controlos digitais mais fiáveis e eficientes. Originalmente introduzidos para simplificar a gestão de múltiplos instrumentos de controlo, os PLCs são agora indispensáveis nos sistemas modernos de fornos de vácuo. Reduzem o envolvimento do operador, asseguram uma qualidade consistente do produto e minimizam o tempo de inatividade do forno. Nos fornos de vácuo de molibdénio contemporâneos, os PLCs são normalmente integrados com interfaces de painel tátil, permitindo aos operadores carregar e descarregar o forno, selecionar receitas de processo e iniciar operações com um simples toque num botão.
Caraterísticas e vantagens do sistema de controlo
A integração de sistemas de controlo avançados em fornos de vácuo de molibdénio oferece várias vantagens importantes:
-
Precisão e consistência: Os sistemas de controlo avançados permitem ajustes precisos dos parâmetros do forno, assegurando uma distribuição uniforme do calor e resultados de processamento consistentes. Esta precisão é crucial para aplicações de elevado valor, em que as propriedades do material têm de ser rigorosamente controladas.
-
Eficiência energética: Os sistemas de controlo modernos optimizam a utilização de energia, ajustando dinamicamente os ciclos de aquecimento e as taxas de arrefecimento com base em dados em tempo real. Isto não só reduz os custos operacionais como também minimiza o impacto ambiental.
-
Monitorização e controlo remotos: Com a capacidade de funcionar a partir de locais remotos, estes sistemas aumentam a flexibilidade e a segurança operacionais. O acesso remoto permite a monitorização e ajustes em tempo real, reduzindo a necessidade de pessoal no local durante as fases críticas da operação.
-
Gestão e análise de dados: Os sistemas de controlo avançados facilitam o registo e a análise de dados abrangentes, o que é essencial para a melhoria do processo e o cumprimento das normas de qualidade. Os dados históricos podem ser utilizados para aperfeiçoar os processos e resolver problemas de forma proactiva.
-
Segurança melhorada: Os sistemas de controlo automatizados incluem protocolos de segurança que evitam erros do operador e protegem contra avarias do equipamento. Isto é particularmente importante em ambientes de alta temperatura e vácuo, onde os riscos de segurança são elevados.
Aplicações e tendências futuras
Os fornos de vácuo de molibdénio equipados com sistemas de controlo avançados são utilizados numa variedade de aplicações de alta temperatura, incluindo sinterização, tratamento térmico e síntese de materiais. À medida que a tecnologia avança, é provável que as tendências futuras dos sistemas de controlo se concentrem numa maior integração com inteligência artificial e algoritmos de aprendizagem automática para prever e otimizar o desempenho do forno, melhorar a manutenção preditiva e melhorar a eficiência geral do processo.
Em conclusão, os sistemas de controlo avançados nos fornos de vácuo de molibdénio representam um salto significativo em termos de precisão, eficiência e segurança. Estes sistemas são essenciais para cumprir os requisitos rigorosos do processamento moderno a alta temperatura e da síntese de materiais, assegurando que os fornos de vácuo de molibdénio permanecem na vanguarda das tecnologias de fabrico avançadas.
Propriedades do material e desempenho dos elementos de aquecimento de molibdénio
O molibdénio, um metal refratário conhecido pela sua resistência a altas temperaturas e excelente condutividade eléctrica, é amplamente utilizado em vários elementos de aquecimento em ambientes industriais e laboratoriais. A sua capacidade de manter a integridade estrutural e o desempenho a temperaturas extremas torna-o uma escolha preferencial para aplicações que exigem durabilidade e fiabilidade.
Propriedades do material de molibdénio
O molibdénio apresenta várias propriedades chave que o tornam adequado para elementos de aquecimento:
- Alto ponto de fusão: O molibdénio tem um ponto de fusão de aproximadamente 2623°C (4753°F), que é significativamente mais elevado do que muitos outros metais. Este elevado ponto de fusão permite que os elementos de aquecimento de molibdénio funcionem a temperaturas até 1700°C (3100°F) sem falhas estruturais.
- Boa condutividade eléctrica: O molibdénio é um excelente condutor de eletricidade, o que é crucial para a geração eficiente de calor nos elementos de aquecimento.
- Resistência à fluência: A altas temperaturas, o molibdénio apresenta uma deformação mínima ao longo do tempo, conhecida como resistência à fluência. Esta propriedade garante que os elementos de aquecimento mantêm a sua forma e desempenho sob exposição prolongada a altas temperaturas.
- Baixa expansão térmica: O molibdénio tem um coeficiente de expansão térmica relativamente baixo, o que ajuda a reduzir o stress e a deformação durante ciclos rápidos de aquecimento e arrefecimento.
Desempenho em ambientes de alta temperatura
Em ambientes de alta temperatura, os elementos de aquecimento de molibdénio demonstram um desempenho excecional:
- Resistência à oxidação: O molibdénio forma uma camada protetora de trióxido de molibdénio (MoO3) quando exposto a temperaturas elevadas em atmosferas oxidantes. Esta camada ajuda a evitar mais oxidação e prolonga a vida útil dos elementos de aquecimento.
- Resistência e durabilidade: Apesar do seu funcionamento a alta temperatura, o molibdénio mantém a sua resistência e não se torna quebradiço, a menos que seja exposto a temperaturas superiores a 1700°C (3100°F). Isto assegura que os elementos de aquecimento podem suportar tensões mecânicas e choques térmicos.
- Distribuição eficiente do calor: A boa condutividade térmica do molibdénio assegura uma distribuição uniforme do calor, o que é essencial para um aquecimento consistente em fornos industriais e de laboratório.
Efeitos de liga no molibdénio
A liga de molibdénio com outros elementos melhora as suas propriedades e alarga a sua gama operacional:
- Liga TZM: A adição de titânio e zircónio ao molibdénio forma a liga TZM, que tem uma resistência melhorada, uma temperatura de recristalização mais elevada e uma melhor resistência à fluência. A TZM pode funcionar a temperaturas de elemento até 1400°C (2552°F).
- Molibdénio Lantanado (MoLa): A incorporação de trióxido de lantânio no molibdénio resulta numa estrutura de grão fina de "fibras empilhadas" que aumenta significativamente a resistência à recristalização e à deformação a alta temperatura. O MoLa pode ser utilizado a temperaturas de elementos até 2000°C (3632°F).
- Disilicida de molibdénio (MoSi2): Este composto oferece baixa resistividade, caraterísticas positivas de resistência-temperatura e excelente resistência à oxidação a alta temperatura. Os elementos de aquecimento MoSi2 podem funcionar com cargas de watt muito elevadas e manter um desempenho constante ao longo da sua vida útil.
Aplicações dos elementos de aquecimento de molibdénio
Os elementos de aquecimento de molibdénio são amplamente utilizados em várias aplicações, incluindo
- Fornos a vácuo: Devido à sua resistência à oxidação e ao seu elevado ponto de fusão, o molibdénio é ideal para fornos de vácuo utilizados em processos de tratamento térmico, como o endurecimento e a brasagem.
- Fornos industriais e de laboratório: A capacidade do molibdénio para suportar altas temperaturas e uma distribuição uniforme do calor torna-o adequado para uma vasta gama de fornos industriais e de laboratório.
- Ambientes de oxidação a alta temperatura: A formação de uma camada protetora de óxido nos elementos de aquecimento de molibdénio garante a sua longevidade e fiabilidade em atmosferas oxidantes de alta temperatura.
Em conclusão, o molibdénio e as suas ligas são materiais cruciais para os elementos de aquecimento devido ao seu excecional desempenho a altas temperaturas, resistência e durabilidade. Através de uma seleção e liga cuidadosas, estes materiais podem ser adaptados para satisfazer os requisitos específicos de várias aplicações industriais e laboratoriais, garantindo processos de aquecimento eficientes e fiáveis.
Manutenção e desempenho a longo prazo dos fornos de vácuo de molibdénio
A manutenção do desempenho a longo prazo dos fornos de vácuo de molibdénio é crucial para garantir um funcionamento consistente e fiável. Estes fornos foram concebidos para funcionar em condições extremas e uma manutenção adequada pode evitar problemas como o endurecimento, o colapso e a perda de resistência dos elementos de aquecimento a altas temperaturas. Aqui estão orientações detalhadas para ajudar a preservar a integridade e a eficiência do seu forno de vácuo de molibdénio.
Manutenção do elemento de aquecimento
Os elementos de aquecimento de molibdénio são componentes críticos dos fornos de vácuo. Devem ser mantidos cuidadosamente para evitar danos e garantir a longevidade. Após cada utilização, inspecionar os elementos de aquecimento para detetar quaisquer sinais de danos. Verifique se as ligações estão bem apertadas para evitar problemas eléctricos. Se um elemento de aquecimento estiver danificado, pode ser possível repará-lo. Normalmente, os elementos de molibdénio podem ser reparados até três vezes por banda de elemento, mas isto requer precauções especiais devido à fragilidade do molibdénio e à potencial libertação de vapores tóxicos de dióxido de molibdénio durante o processo de reparação.
Condicionamento de novos elementos de aquecimento
Os novos elementos de aquecimento de molibdénio devem ser condicionados para melhorar o seu desempenho e longevidade. Isto implica aquecer o forno vazio a 1550°C e mantê-lo a essa temperatura durante uma hora. Este processo ajuda a aplicar uma camada fina e protetora de vidro nos elementos, o que pode evitar a degradação prematura. Se o forno tiver de funcionar durante longos períodos a temperaturas inferiores a 800°C, recondicione as superfícies utilizando o procedimento de queima inicial para manter a sua integridade.
Controlo das taxas de aquecimento
A taxa de aquecimento é um fator crítico na manutenção da integridade estrutural dos elementos de aquecimento. Um aquecimento rápido pode levar à expansão térmica e à deformação do escudo térmico. Recomenda-se a utilização de uma taxa de aquecimento lenta, especialmente na fase de alta temperatura. Por exemplo, a redução da taxa de rampa para temperaturas 100-200°C abaixo da temperatura nominal máxima do forno para 60-100°C por hora pode evitar tensões indevidas nos elementos de aquecimento.
Verificações de vácuo e de fugas
Antes de iniciar o processo de aquecimento, é essencial verificar a taxa de fuga de vácuo e o grau de vácuo final. A garantia de um ambiente de vácuo correto é crucial para o funcionamento eficiente do forno. Quando o equipamento não estiver a ser utilizado, deve ser armazenado em vácuo. Se existirem substâncias voláteis no interior do forno, este deve ser seco para evitar a contaminação e potenciais danos nos elementos de aquecimento.
Manuseamento de produtos e controlo de impurezas
Ao manusear os produtos, ter o cuidado de evitar deixá-los cair sobre a superfície dos elementos de aquecimento de molibdénio, pois isso pode causar danos. Os produtos que contêm elementos de ferro com pontos de fusão mais baixos não devem volatilizar para a cinta de molibdénio no forno, uma vez que isso pode levar à fusão ao longo do tempo. Segurar firmemente os produtos com as duas mãos ou utilizar objectos mecânicos para evitar quedas acidentais. Além disso, controlar rigorosamente o teor de impurezas dos produtos para evitar a contaminação dos elementos de aquecimento.
Ligações eléctricas e sistemas de arrefecimento
A ligação eléctrica aos elementos de aquecimento é normalmente realizada através de uma passagem arrefecida a água. Esta ligação selada contém o condutor que transporta a corrente para o elemento de aquecimento. As passagens estão disponíveis em vários níveis de corrente, incluindo modelos de alta capacidade. O arrefecimento por água evita o sobreaquecimento e é essencial utilizar um sistema de arrefecimento de circuito fechado, ligado à terra, com líquidos de arrefecimento não condutores, como água desionizada ou etilenoglicol. As linhas de arrefecimento devem ser construídas com materiais não condutores, como tubos de polipropileno, para evitar que o líquido de arrefecimento se torne parte do circuito.
Conceção de elementos de aquecimento para resistência
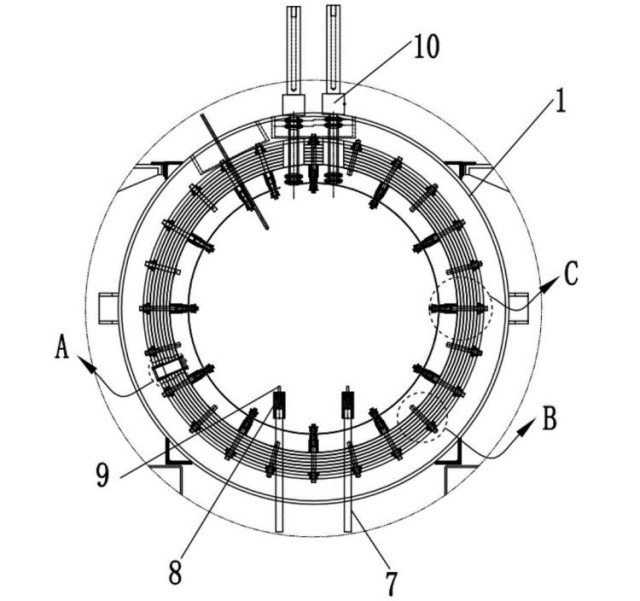
Para garantir que o fio de aquecimento do forno de vácuo mantém a resistência necessária a altas temperaturas e evita o endurecimento, o colapso ou a queda, o tamanho da construção do fio de aquecimento deve ser cuidadosamente projetado. Isto inclui a utilização de fio de resistência em espiral e a atenção ao diâmetro de dobragem, ao passo e ao diâmetro médio do elemento de aquecimento. O corpo de aquecimento deve ser fixado contra o revestimento de isolamento do forno de vácuo, com 95 peças de cerâmica colocadas no revestimento de isolamento para proporcionar um espaço de expansão adequado. Durante a utilização, posicionar os elementos de aquecimento de forma adequada, geralmente a intervalos de 100-200 mm, e prendê-los com segurança para evitar que o fio da resistência fique deitado. Além disso, evite o contacto direto entre os fios do forno para evitar curto-circuitos, normalmente utilizando placas de isolamento.
Seguindo estas diretrizes abrangentes de manutenção e conceção, pode assegurar o desempenho a longo prazo e a fiabilidade do seu forno de vácuo de molibdénio, prolongando a sua vida útil e mantendo uma eficiência operacional óptima.
Aplicações dos fornos de vácuo de molibdénio na indústria
Os fornos de vácuo de molibdénio desempenham um papel crucial em vários sectores industriais devido à sua capacidade de funcionar a altas temperaturas e em condições de vácuo, garantindo um controlo preciso do processo de aquecimento sem oxidação ou contaminação. Esta secção explora as diversas aplicações dos fornos de vácuo de molibdénio em indústrias como a cerâmica, metalurgia, eletrónica e tratamentos especiais de materiais.
Indústria cerâmica
Na indústria da cerâmica, os fornos de vácuo de molibdénio são essenciais para a produção de cerâmica densa e de alta qualidade com propriedades uniformes. Estes fornos permitem a sinterização de cerâmicas avançadas a temperaturas até 2400°C, o que é crucial para obter as propriedades mecânicas, eléctricas e térmicas desejadas. O ambiente de vácuo evita a oxidação dos pós cerâmicos, levando a produtos com maior pureza e desempenho. As aplicações incluem a produção de cerâmicas técnicas utilizadas em dispositivos electrónicos, aeroespaciais e médicos.
Metalurgia
O sector da metalurgia utiliza extensivamente fornos de vácuo de molibdénio para fusão e tratamento térmico de metais. Estes fornos são ideais para o processamento de metais refractários como o tungsténio, o molibdénio e o tântalo, que requerem pontos de fusão elevados e resistem à oxidação. A fusão sob vácuo ajuda a remover impurezas e gases voláteis, resultando em metais com pureza e propriedades mecânicas superiores. Além disso, estes fornos são utilizados para o tratamento térmico de aços de alta resistência, aços inoxidáveis e aços para ferramentas, para obter a dureza, tenacidade e resistência ao desgaste desejadas.
Eletrónica
Na indústria eletrónica, os fornos de vácuo de molibdénio são utilizados para a produção de dispositivos semicondutores e circuitos integrados. Os fornos são utilizados para processos como a sinterização, o recozimento e a difusão, que exigem um controlo preciso da temperatura e um ambiente livre de contaminação. As capacidades de alta temperatura dos fornos de molibdénio permitem o processamento de materiais avançados como o carboneto de silício e o nitreto de gálio, que são essenciais para os dispositivos electrónicos da próxima geração.
Tratamentos especiais de materiais
Os fornos de vácuo de molibdénio são também utilizados para tratamentos de materiais especializados em várias indústrias. Estes incluem:
- Brasagem e soldadura: Os fornos de vácuo proporcionam um ambiente ideal para operações de brasagem e soldadura, garantindo juntas de alta qualidade com o mínimo de oxidação e porosidade. Isto é particularmente importante nas indústrias aeroespacial e automóvel, onde a fiabilidade e o desempenho são críticos.
- Processamento de combustível nuclear: Os fornos de molibdénio são utilizados para o fabrico de pastilhas de combustível nuclear, garantindo uma elevada pureza e densidade. O ambiente de vácuo ajuda a remover impurezas e gases voláteis, o que é essencial para a segurança e o desempenho nuclear.
- Fusão de vidro: Na indústria do vidro, os fornos de vácuo de molibdénio são utilizados para fundir vidros de alta pureza e criar cerâmicas técnicas. As altas temperaturas e a atmosfera controlada permitem a produção de vidros especiais com propriedades ópticas e mecânicas únicas.
Vantagens dos fornos de vácuo de molibdénio
A utilização de fornos de vácuo de molibdénio oferece várias vantagens, incluindo
- Capacidades de alta temperatura: Os elementos de aquecimento de molibdénio podem suportar temperaturas até 2400°C, tornando-os adequados para o processamento de materiais a alta temperatura.
- Atmosfera controlada: O ambiente de vácuo evita a oxidação e a contaminação, garantindo produtos de alta qualidade com propriedades consistentes.
- Eficiência energética: Os fornos de vácuo são concebidos para serem eficientes em termos energéticos, reduzindo os custos operacionais e o impacto ambiental.
- Versatilidade: Os fornos de vácuo de molibdénio podem ser configurados para várias aplicações, tornando-os uma ferramenta versátil em várias indústrias.
Em conclusão, os fornos de vácuo de molibdénio são indispensáveis na indústria moderna, permitindo a produção de materiais e componentes de alta qualidade com controlo preciso e contaminação mínima. As suas aplicações abrangem a cerâmica, a metalurgia, a eletrónica e os tratamentos especiais de materiais, destacando o seu papel fundamental no avanço dos processos tecnológicos e industriais.
Tendências futuras e inovações na tecnologia de fornos de vácuo de molibdénio
O campo da tecnologia de fornos de vácuo de molibdénio está preparado para avanços e inovações significativos que irão aumentar a eficiência e expandir as aplicações em várias indústrias. À medida que a procura de materiais de alta qualidade e de processos de tratamento térmico precisos aumenta, o desenvolvimento de fornos de vácuo de molibdénio avançados está a tornar-se crucial.
Melhorias na eficiência
Um dos principais focos na evolução da tecnologia de fornos de vácuo de molibdénio é a melhoria da eficiência operacional. Espera-se que as inovações nos elementos de aquecimento, materiais de isolamento e sistemas de controlo reduzam o consumo de energia e melhorem a uniformidade da temperatura. Por exemplo, a integração de materiais de isolamento avançados, como as fibras cerâmicas e o isolamento multicamadas, pode reduzir significativamente as perdas de calor, melhorando assim a eficiência energética global do forno.
Além disso, o desenvolvimento de sistemas de controlo inteligentes que utilizam inteligência artificial e algoritmos de aprendizagem automática pode otimizar os ciclos de aquecimento, prever as necessidades de manutenção e ajustar os parâmetros operacionais em tempo real. Estes sistemas podem analisar grandes quantidades de dados recolhidos a partir de sensores no interior do forno para garantir um desempenho ótimo e um tempo de inatividade mínimo.
Novas aplicações
A versatilidade dos fornos de vácuo de molibdénio está a abrir novos caminhos para aplicações em campos emergentes como o fabrico de aditivos, cerâmica avançada e processamento de semicondutores. A capacidade de controlar a atmosfera e a temperatura com elevada precisão torna estes fornos ideais para o processamento de materiais avançados que requerem condições ambientais específicas.
No domínio do fabrico de aditivos, os fornos de vácuo de molibdénio podem ser utilizados para o pós-processamento de peças metálicas, garantindo que estas estão isentas de impurezas e têm as propriedades mecânicas desejadas. Do mesmo modo, na produção de cerâmicas avançadas, estes fornos podem facilitar a sinterização de formas e composições complexas que não são possíveis com métodos convencionais.
Inovações em materiais
O desenvolvimento de novas ligas e compósitos de molibdénio é outra área de inovação. Ao incorporar elementos como o titânio, o zircónio e metais de terras raras, os investigadores estão a criar ligas de molibdénio com maior resistência a altas temperaturas, resistência à corrosão e condutividade térmica. Estes materiais avançados podem alargar a gama de temperaturas operacionais dos elementos de aquecimento de molibdénio e aumentar a sua durabilidade.
Além disso, a utilização da nanotecnologia na produção de elementos de aquecimento de molibdénio pode conduzir a melhorias significativas no seu desempenho. Os revestimentos nanoestruturados podem aumentar a emissividade dos elementos, permitindo uma transferência de calor mais eficiente e um menor consumo de energia.
Considerações ambientais
À medida que os regulamentos ambientais se tornam mais rigorosos, a conceção dos fornos de vácuo de molibdénio também está a evoluir para minimizar a sua pegada ecológica. Estão a ser exploradas inovações no design dos fornos que reduzem a produção de resíduos e melhoram as capacidades de reciclagem. Além disso, o desenvolvimento de fornos energeticamente eficientes que cumprem as normas internacionais de consumo de energia está a tornar-se uma prioridade para os fabricantes.
Conclusão
O futuro dosforno de vácuo de molibdénio é brilhante, com numerosas inovações no horizonte que irão impulsionar melhorias de eficiência e expandir as aplicações. Ao alavancar os avanços na ciência dos materiais, nos sistemas de controlo e na sustentabilidade ambiental, a indústria está preparada para satisfazer a crescente procura de materiais de alta qualidade e de engenharia de precisão. À medida que estas tecnologias continuam a evoluir, desempenharão um papel crucial na definição do futuro de várias indústrias, desde a aeroespacial e automóvel até à eletrónica e aos cuidados de saúde.
CONTACTE-NOS PARA UMA CONSULTA GRATUITA
Os produtos e serviços da KINTEK LAB SOLUTION foram reconhecidos por clientes de todo o mundo. A nossa equipa terá todo o prazer em ajudar com qualquer questão que possa ter. Contacte-nos para uma consulta gratuita e fale com um especialista de produto para encontrar a solução mais adequada para as suas necessidades de aplicação!