Os tubos cerâmicos, dependendo da sua composição, apresentam uma excelente resistência à temperatura, tornando-os adequados para aplicações a altas temperaturas.Por exemplo, a cerâmica C30 (mulita) pode suportar temperaturas até 1600°C (2900°F) e é impermeável ao ar até 3000°F.Os tubos de cerâmica de alumina podem suportar temperaturas ainda mais elevadas, até 1800°C, especialmente em condições de redução, inertes e de alto vácuo.Estes materiais são escolhidos pela sua baixa expansão térmica, elevada resistência ao choque térmico e resistência a ambientes corrosivos, tornando-os ideais para aplicações industriais e científicas onde prevalecem condições extremas.
Pontos-chave explicados:
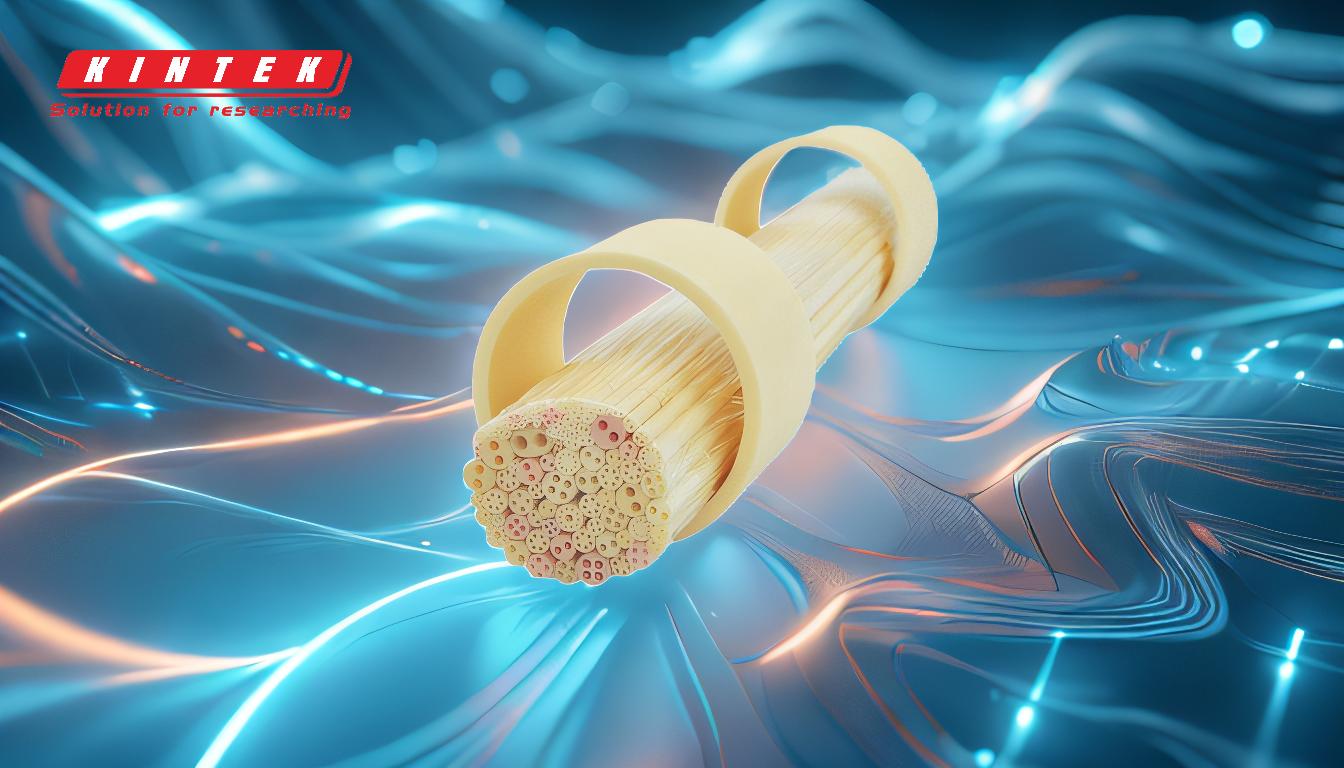
-
Resistência à temperatura da cerâmica C30 (Mullite):
- Temperatura máxima de funcionamento: A cerâmica C30 pode funcionar a temperaturas até 1600°C (2900°F).
- Impermeável ao ar: Mantém-se impermeável ao ar até 3000°F.
- Resistência aos gases: Também é resistente ao hidrogénio seco e ao monóxido de carbono até 2550°F.
- Expansão térmica: A baixa taxa de expansão térmica (2,8 x 10^-6/°F) aumenta a sua resistência ao choque térmico, tornando-o adequado para ambientes com mudanças rápidas de temperatura.
-
Resistência à temperatura dos tubos de cerâmica de alumina:
- Temperatura máxima de funcionamento: Os tubos de cerâmica de alumina podem suportar temperaturas até 1800°C.
- Condições ambientais: São particularmente eficazes em ambientes redutores, inertes e de alto vácuo, que são comuns em processos industriais avançados.
-
Propriedades gerais dos materiais cerâmicos:
- Estabilidade térmica: As cerâmicas tradicionais são conhecidas pela sua estabilidade térmica, que tem sido utilizada em várias aplicações, tais como recipientes para cozinhar e pratos de servir.
- Estabilidade química e mecânica: Estes materiais são também mecânica e quimicamente estáveis, o que é crucial para a sua utilização em ambientes agressivos.
- Cerâmica avançada: Os materiais cerâmicos avançados, compostos por ligações iónicas ou covalentes, oferecem propriedades como elevada resistência, dureza, resistência ao desgaste e resistência à corrosão, para além de resistência a altas temperaturas.
-
Aplicações e implicações:
- Uso industrial: A resistência a altas temperaturas dos tubos de cerâmica torna-os ideais para utilização em indústrias como a metalurgia, o processamento químico e o fabrico de semicondutores.
- Investigação científica: Na investigação científica, especialmente em experiências a altas temperaturas, a estabilidade e a resistência dos materiais cerâmicos são inestimáveis.
- Durabilidade e longevidade: A resistência ao desgaste e à corrosão destes materiais contribui para a sua durabilidade e longevidade, reduzindo a necessidade de substituições e manutenção frequentes.
Em resumo, os tubos cerâmicos, em particular os fabricados com cerâmica C30 e alumina, oferecem uma excecional resistência à temperatura e estabilidade em várias condições ambientais.Estas propriedades tornam-nos indispensáveis tanto em ambientes industriais como científicos, onde são comuns temperaturas elevadas e ambientes corrosivos.
Tabela de resumo:
Propriedade | Cerâmica C30 (Mullite) | Tubos de cerâmica de alumina |
---|---|---|
Temperatura máxima de funcionamento | 2900°F (1600°C) | 1800°C |
Impermeável ao ar | Até 3000°F | N/A |
Resistência a gases | Hidrogénio seco, CO até 2550°F | Redução, inerte, alto vácuo |
Expansão térmica | 2,8 x 10^-6/°F | N/A |
Aplicações | Investigação industrial e científica | Processos industriais avançados |
Precisa de tubos de cerâmica para aplicações a alta temperatura? Contacte-nos hoje para encontrar a solução perfeita!