Os fornos de calcinação são concebidos para funcionar a altas temperaturas, normalmente entre 800°C e 1300°C, dependendo da aplicação específica.Estes fornos são utilizados para processos como a remoção de água, constituintes voláteis ou substâncias oxidantes.A gama de temperaturas é crítica para garantir que ocorrem as transformações químicas ou físicas desejadas.Além disso, factores como o tipo de material a ser processado, a conceção do forno e as condições operacionais (por exemplo, humidade, presença de gases corrosivos) influenciam as definições de temperatura.A manutenção adequada, como o funcionamento abaixo do limite máximo de temperatura, é essencial para prolongar a vida útil do forno e garantir um desempenho eficiente.
Pontos-chave explicados:
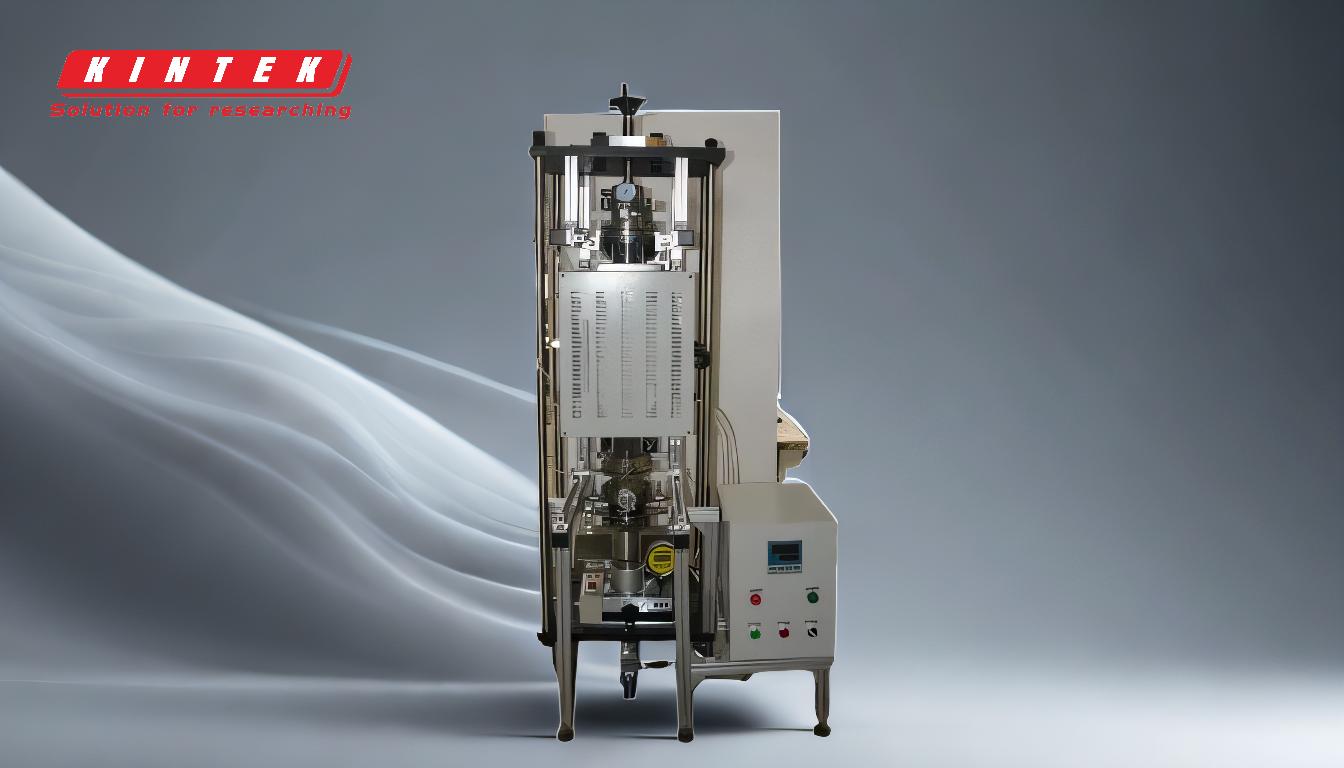
-
Gama de temperaturas dos fornos de calcinação:
- Os fornos de calcinação funcionam normalmente entre 800°C e 1300°C .
- Esta gama é necessária para alcançar as reacções químicas desejadas, tais como a decomposição, a oxidação ou a remoção de componentes voláteis como a água ou o dióxido de carbono.
-
Factores que influenciam a temperatura:
- Propriedades dos materiais:O tipo de material que está a ser processado determina a temperatura necessária.Por exemplo, os materiais com elevada estabilidade térmica podem exigir temperaturas mais elevadas.
- Requisitos do processo:As aplicações específicas, como a remoção de água ou de substâncias oxidantes, ditam as definições de temperatura.
- Conceção do forno:A conceção do forno, incluindo os elementos de aquecimento e o isolamento, afecta a gama de temperaturas alcançáveis.
-
Aplicações dos fornos de calcinação:
- Desidratação:Remoção de água de materiais como os hidratos.
- Descarbonatação:Eliminação do dióxido de carbono dos carbonatos.
- Oxidação:Oxidação de uma parte ou da totalidade de uma substância para alterar a sua composição química.
- Estas aplicações requerem um controlo preciso da temperatura para garantir os resultados desejados.
-
Considerações operacionais:
- Humidade e ambiente:Os fornos devem funcionar em ambientes com humidade relativa não superior a 85% e devem estar isentos de gases corrosivos ou explosivos.
- Elementos de aquecimento:Para prolongar a vida útil do forno, recomenda-se que este funcione a 50°C abaixo da sua temperatura máxima .
- Manuseamento de materiais:Ao processar materiais que libertam gases voláteis, devem ser utilizados recipientes selados ou ventilação adequada para evitar danos nos elementos de aquecimento.
-
Tipos de fornos e sua especialização:
- Fornos contínuos:São utilizados para processos consistentes como recozimento ou endurecimento, operando em condições de temperatura permanente.
- Fornos de mufla:Estes são ideais para o aquecimento controlado em ambientes onde a contaminação deve ser minimizada.
- Cada tipo de forno é optimizado para processos específicos, garantindo eficiência e precisão.
-
Importância do controlo da temperatura:
- O controlo exato da temperatura é crucial para obter resultados consistentes nos processos de calcinação.
- O sobreaquecimento pode danificar o forno ou o material, enquanto o aquecimento insuficiente pode não atingir a transformação química desejada.
Ao compreender estes pontos-chave, um comprador pode tomar decisões informadas sobre a seleção e funcionamento de um forno de calcinação adaptado às suas necessidades específicas.
Tabela de resumo:
Aspeto | Detalhes |
---|---|
Gama de temperaturas | 800°C a 1300°C, dependendo dos requisitos do material e do processo. |
Principais aplicações | Desidratação, descarbonatação, oxidação e transformações químicas. |
Factores operacionais | Propriedades do material, conceção do forno, humidade e condições ambientais. |
Conselhos de manutenção | Utilizar 50°C abaixo da temperatura máxima para prolongar a vida útil e garantir a eficiência. |
Tipos de fornos | Fornos contínuos, fornos de mufla, cada um optimizado para processos específicos. |
Controlo da temperatura | Crítico para resultados consistentes; o sobreaquecimento ou subaquecimento pode causar problemas. |
Precisa de um forno de calcinação adaptado às suas necessidades? Contacte-nos hoje para obter orientação especializada!