A calcinação é um processo de tratamento térmico utilizado para induzir a decomposição térmica, a transição de fase ou a remoção de fracções voláteis a altas temperaturas. Os fornos utilizados para a calcinação são especificamente concebidos para lidar com temperaturas elevadas e proporcionar um aquecimento uniforme, o que é fundamental para alcançar as alterações químicas ou físicas pretendidas. Com base nas referências fornecidas, os fornos mais comuns utilizados para a calcinação incluem fornos de mufla , fornos de reverberação , fornos de cuba e fornos . Estes fornos são escolhidos com base no material a ser processado, na escala de operação (laboratorial ou industrial) e nos requisitos específicos de temperatura. Segue-se uma explicação pormenorizada dos pontos-chave relacionados com os fornos de calcinação.
Pontos-chave explicados:
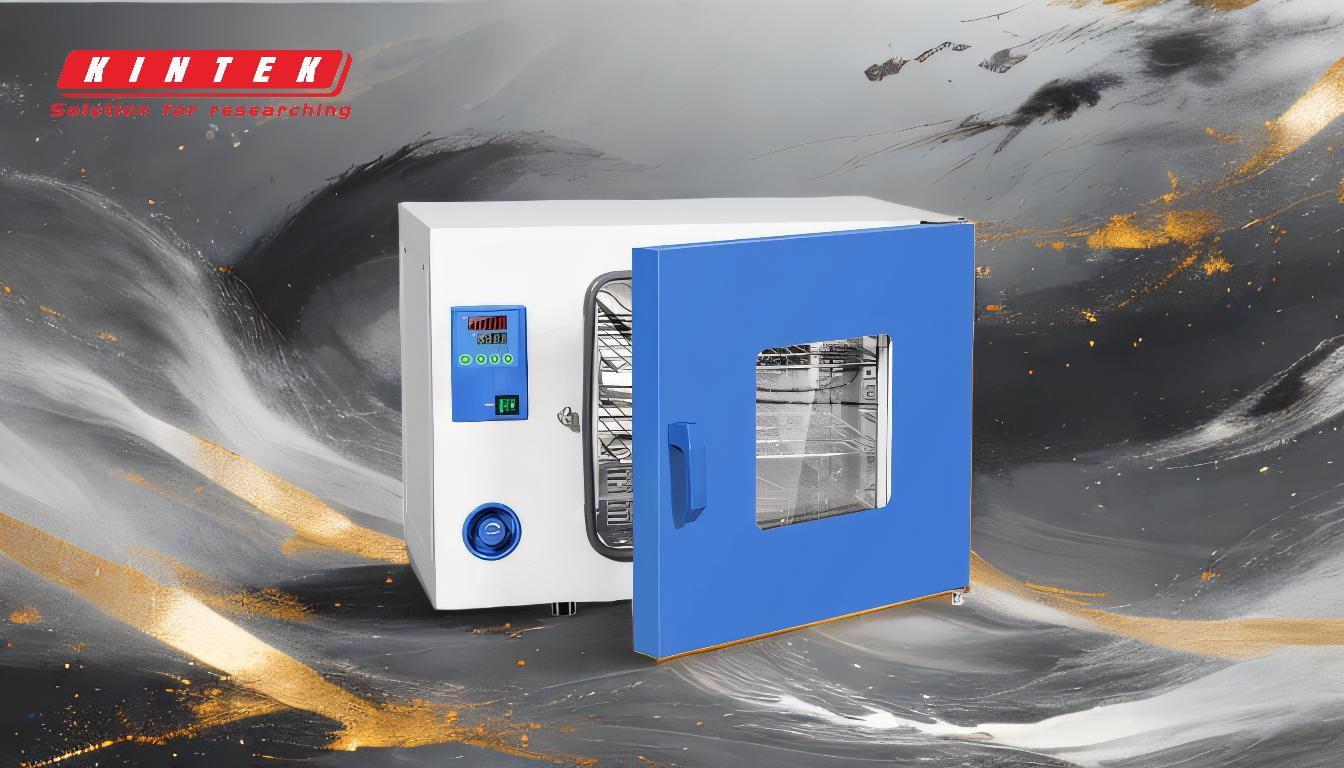
-
Tipos de fornos utilizados para a calcinação:
- Fornos de mufla: São muito utilizados em laboratórios e na indústria. São constituídos por uma câmara rodeada por elementos de aquecimento que asseguram uma distribuição uniforme da temperatura. Os fornos de mufla são ideais para a calcinação, uma vez que evitam a contaminação do material processado, isolando-o dos gases de combustão.
- Fornos Reverberatórios: Estes fornos são concebidos para aplicações industriais em grande escala. Utilizam uma chama para aquecer indiretamente o material, sendo o calor refletido nas paredes do forno. Esta conceção é adequada para a calcinação de materiais como minérios e minerais.
- Fornos de cuba: Normalmente utilizados para processos de calcinação contínua, os fornos de poço são estruturas verticais onde os materiais se movem para baixo enquanto são aquecidos. São eficientes para processar grandes quantidades de materiais, como calcário ou clínquer de cimento.
- Fornos: Os fornos são versáteis e podem ser utilizados para a calcinação em indústrias como a cerâmica e a produção de cimento. Funcionam a altas temperaturas e podem ser concebidos como unidades rotativas ou estacionárias, consoante a aplicação.
-
Principais caraterísticas dos fornos de calcinação:
- Capacidade para altas temperaturas: A calcinação requer normalmente temperaturas que variam entre 500°C e mais de 1000°C. Os fornos utilizados para este processo devem ser capazes de manter estas temperaturas de forma consistente.
- Aquecimento uniforme: A distribuição uniforme da temperatura é fundamental para garantir uma calcinação completa e consistente. Os fornos do tipo mufla e reverberatório são concebidos para o conseguir.
- Atmosfera controlada: Alguns processos de calcinação requerem uma atmosfera específica (por exemplo, inerte ou oxidante). Os fornos de mufla, por exemplo, podem ser selados para controlar o ambiente interno.
- Durabilidade e isolamento: Os fornos de calcinação têm de suportar uma exposição prolongada a temperaturas elevadas e a materiais corrosivos. Os materiais de isolamento de alta qualidade, como a fibra cerâmica, são frequentemente utilizados para melhorar a eficiência energética e a durabilidade.
-
Utilização industrial vs. utilização laboratorial:
- Fornos industriais: Os fornos de calcinação industriais, tais como os fornos reverberatórios e os fornos de cuba, são concebidos para uma produção em grande escala. São robustos, eficientes em termos energéticos e capazes de lidar com um elevado rendimento.
- Fornos de laboratório: Os fornos de mufla são normalmente utilizados em laboratórios para experiências de calcinação em pequena escala. Oferecem um controlo preciso da temperatura e são compactos, o que os torna adequados para investigação e desenvolvimento.
-
Aplicações dos fornos de calcinação:
- Produção de cimento: A calcinação do calcário para produzir cal é um passo fundamental no fabrico de cimento. Os fornos de eixo e os fornos rotativos são normalmente utilizados para este fim.
- Processamento de metais: A calcinação é utilizada para remover as impurezas dos minérios metálicos. Os fornos reverberatórios são frequentemente utilizados nesta indústria.
- Cerâmica e vidro: Os fornos são utilizados para calcinar matérias-primas como a argila e a sílica, que são essenciais para a produção de cerâmica e vidro.
- Indústria química: A calcinação é utilizada para produzir produtos químicos como a alumina e o dióxido de titânio. Os fornos de mufla são frequentemente utilizados em laboratórios para desenvolver e testar estes processos.
-
Vantagens dos diferentes tipos de fornos:
- Fornos de mufla: Ideal para processos de pequena escala e sensíveis à contaminação devido à sua conceção fechada.
- Fornos Reverberatórios: Adequado para operações em grande escala e materiais que requerem aquecimento indireto.
- Fornos de cuba: Eficiente para processamento contínuo e produção de grande volume.
- Fornos: Versátil e adaptável a vários materiais e indústrias.
-
Considerações sobre a seleção de um forno de calcinação:
- Propriedades do material: O tipo de material a calcinar (por exemplo, estabilidade térmica, tamanho das partículas) influencia a escolha do forno.
- Requisitos de temperatura: O forno deve ser capaz de atingir e manter a temperatura de calcinação requerida.
- Escala de operação: Os processos à escala industrial requerem fornos robustos e de elevada capacidade, enquanto os processos à escala laboratorial beneficiam de designs precisos e compactos.
- Eficiência energética: A conceção e o isolamento do forno devem minimizar o consumo de energia, especialmente para operações em grande escala.
- Impacto ambiental: Os fornos eléctricos são preferidos em ambientes onde a redução das emissões é uma prioridade.
Em resumo, a escolha do forno para calcinação depende da aplicação específica, das propriedades do material e da escala operacional. Fornos de mufla, reverberatórios, de eixo e fornos são os tipos mais utilizados, cada um oferecendo vantagens únicas para diferentes processos de calcinação. Compreender as principais caraterísticas e aplicações destes fornos é essencial para selecionar o equipamento certo para as suas necessidades.
Quadro de resumo:
Tipo de forno | Caraterísticas principais | Aplicações |
---|---|---|
Forno de mufla | Aquecimento uniforme, sem contaminação, controlo preciso da temperatura | Investigação laboratorial, calcinação em pequena escala, processamento químico |
Forno de reverberação | Aquecimento indireto, em grande escala, design robusto | Processamento de minério de metal, calcinação industrial |
Forno de cuba | Processamento contínuo, elevado rendimento, conceção vertical | Produção de cimento, calcinação de calcário |
Forno | Design versátil, de alta temperatura, rotativo ou estacionário | Cerâmica, produção de vidro, fabrico de cimento |
Precisa de ajuda para selecionar o forno de calcinação adequado para a sua aplicação? Contacte os nossos especialistas hoje mesmo para um aconselhamento personalizado!