Introdução: Fornos de grafite a vácuo para tratamento de materiais a alta temperatura
Os fornos de grafite a vácuo estão a revolucionar o tratamento de materiais a alta temperatura com o seu desempenho e versatilidade sem paralelo. Estes fornos avançados utilizam bolachas de grafite como elementos de aquecimento, proporcionando uma eficiência térmica excecional e um aquecimento uniforme. O seu ambiente de vácuo permite um controlo preciso de gases reactivos ou inertes, tornando-os ideais para várias aplicações nas indústrias aeroespacial, automóvel e médica. Ao adotar os fornos de grafite a vácuo, os investigadores e engenheiros podem desbloquear novas possibilidades no processamento de materiais, assegurando resultados óptimos e fazendo avançar as descobertas científicas.
Fornos à base de grafite: Desbloquear a eficiência térmica e o desempenho
As bolachas de grafite, conhecidas pelas suas propriedades excepcionais, servem como materiais ideais para a construção de fornos. A sua baixa densidade inerente e peso reduzido contribuem para a eficiência global do forno. No entanto, é a sua elevada emissividade que distingue a grafite, permitindo-lhe aproximar-se das condições ideais de corpo negro. Esta caraterística assegura um aquecimento uniforme, minimizando os gradientes de temperatura dentro da câmara do forno.
A condutividade térmica da grafite é outro fator crucial que contribui para a sua adequação a aplicações em fornos. A grafite apresenta uma elevada condutividade térmica, permitindo uma transferência de calor eficiente dos elementos de aquecimento para a câmara do forno. Esta transferência de calor eficiente assegura uma distribuição uniforme da temperatura, reduzindo o risco de gradientes térmicos e pontos quentes no interior do forno.
A resistência da grafite a altas temperaturas é outra vantagem que a torna uma escolha preferencial para materiais de forno. A grafite pode suportar temperaturas extremas, até 3000°C em gás inerte e 2200°C em vácuo, sem derreter ou perder a sua integridade estrutural. Esta excecional resistência à temperatura permite que os fornos de grafite funcionem a temperaturas mais elevadas, expandindo a sua aplicabilidade em processos térmicos exigentes.
A inércia química da grafite é outra vantagem significativa. A grafite apresenta resistência à oxidação, corrosão e reacções químicas com a maioria dos gases e líquidos. Esta inércia permite que os fornos de grafite sejam utilizados em vários processos químicos sem o risco de contaminação ou degradação dos materiais do forno.
Para além das suas propriedades térmicas e químicas, a grafite também oferece vantagens em termos de manutenção e reparação. As câmaras dos fornos de grafite são relativamente fáceis de reparar, permitindo uma manutenção rápida e económica. Além disso, a utilização de camadas de sacrifício feitas de CFC ou de laminado de grafite proporciona uma proteção adicional contra altas temperaturas e erosão gasosa, prolongando a vida útil da câmara do forno.
Em resumo, as propriedades excepcionais das pastilhas de grafite, incluindo a sua baixa densidade, alta emissividade, condutividade térmica, resistência à temperatura e inércia química, tornam-nas materiais ideais para a construção de fornos. Os fornos de grafite oferecem uma eficiência térmica superior, aquecimento uniforme, capacidades de alta temperatura e facilidade de manutenção, tornando-os um ativo valioso em várias aplicações térmicas.
Explorando as opções e aplicações dos fornos de vácuo
Os fornos de vácuo oferecem uma versatilidade excecional no manuseamento de gases reactivos e inertes, permitindo um controlo preciso da atmosfera do forno durante os processos de tratamento térmico. Esta versatilidade torna-os adequados para uma vasta gama de aplicações em várias indústrias, incluindo:
Aeroespacial
Os fornos de vácuo desempenham um papel crucial na indústria aeroespacial, onde são utilizados para
- Brasagem de ligas de alta temperatura para motores e componentes de aeronaves
- Tratamento térmico de titânio e superligas utilizadas em estruturas de aeronaves
- Recozimento e alívio de tensões de peças críticas para satélites e naves espaciais
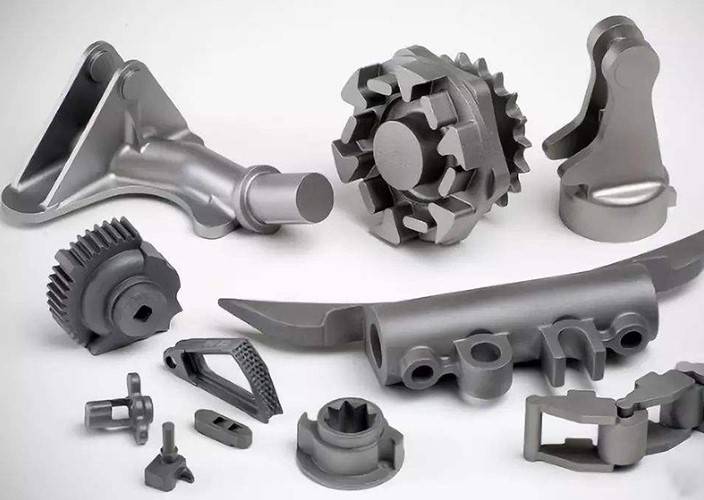
Indústria automóvel
Na indústria automóvel, os fornos de vácuo são utilizados para
- Carburação e nitruração de engrenagens e outros componentes de transmissão
- Sinterização e tratamento térmico de peças de metalurgia do pó
- Recozimento e envelhecimento de aços de alta resistência utilizados em estruturas de veículos e sistemas de segurança
Medicina
Os fornos de vácuo são essenciais na indústria de dispositivos médicos para:
- Brasagem de implantes e instrumentos cirúrgicos
- Esterilização e recozimento de ferramentas médicas
- Tratamento térmico de materiais biocompatíveis utilizados em próteses e implantes
A versatilidade dos fornos de vácuo estende-se para além destas indústrias principais. Também são utilizados nas seguintes aplicações:
- Desgaseificação e purificação por vácuo de metais e ligas
- Tratamento térmico de ferramentas de corte e moldes
- Sinterização e brasagem de componentes electrónicos
Os fornos de vácuo oferecem várias vantagens em relação aos métodos convencionais de tratamento térmico:
- Atmosfera controlada: Ao criar um ambiente de vácuo, a oxidação, descarbonetação e contaminação são minimizadas, garantindo a produção de componentes de alta qualidade com propriedades consistentes.
- Controlo preciso da temperatura: Os fornos de vácuo oferecem um controlo preciso da temperatura, permitindo ciclos de tratamento térmico personalizados que optimizam as propriedades mecânicas do material.
- Eficiência melhorada: O ambiente de vácuo reduz a perda de calor, levando a uma maior eficiência energética e a tempos de processamento mais rápidos.
- Ampla faixa de temperatura: Os fornos de vácuo podem funcionar numa vasta gama de temperaturas, desde o recozimento a baixa temperatura até à sinterização a alta temperatura.
A escolha do tipo de forno de vácuo (parede quente ou parede fria) e da atmosfera de gás (inerte ou reativo) depende dos requisitos específicos da aplicação. Os gases inertes, como o árgon ou o azoto, são normalmente utilizados para manter um ambiente não oxidante, enquanto os gases reactivos, como o hidrogénio ou o metano, podem ser utilizados para processos de cementação ou nitruração.
De um modo geral, os fornos de vácuo oferecem uma solução versátil e precisa para o tratamento térmico de uma vasta gama de materiais e componentes em várias indústrias. A sua capacidade de controlar a atmosfera, a temperatura e os parâmetros de processamento torna-os uma ferramenta indispensável para fabricantes e investigadores que procuram produzir produtos fiáveis e de alta qualidade.
Soluções personalizadas: Adaptação dos fornos a requisitos específicos
No exigente panorama industrial atual, o equipamento de laboratório padrão e os consumíveis muitas vezes não conseguem satisfazer as necessidades únicas e em evolução das equipas de investigação e desenvolvimento. As soluções personalizadas de fornos de vácuo surgiram como uma ferramenta poderosa para enfrentar estes desafios, permitindo que engenheiros e cientistas ultrapassem os limites da inovação.
Os fornos de vácuo oferecem um ambiente controlado para processos de tratamento térmico, permitindo um controlo preciso da temperatura e da atmosfera. No entanto, os fornos prontos a utilizar podem nem sempre estar alinhados com os requisitos específicos de uma determinada aplicação. É aqui que entra em ação a engenharia personalizada de fornos de vácuo.
Ao colaborar estreitamente com os clientes, os engenheiros podem conceber fornos que são adaptados para satisfazer os seus objectivos e processos únicos. Esta abordagem colaborativa assegura que o design, a configuração e as características de desempenho do forno são optimizados para a aplicação pretendida.
Os fornos de vácuo personalizados oferecem uma vasta gama de vantagens, incluindo:
- Desempenho personalizado: Os fornos podem ser concebidos para atingir perfis de temperatura, taxas de aquecimento e taxas de arrefecimento específicos, assegurando condições de processo óptimas para os materiais a tratar.
- Aumento da eficiência: Os fornos podem ser concebidos para minimizar a perda de calor e otimizar o consumo de energia, resultando em custos operacionais reduzidos e maior produtividade.
- Segurança melhorada: Os fornos personalizados podem incorporar características de segurança que cumprem as normas e regulamentos específicos da indústria, minimizando os riscos e garantindo a segurança do operador.
- Integração com sistemas existentes: Os fornos podem ser concebidos para se integrarem perfeitamente com o equipamento de laboratório e os sistemas de automatização existentes, simplificando os fluxos de trabalho e melhorando a eficiência global.
O processo de personalização envolve normalmente os seguintes passos:
- Consulta: Os engenheiros discutem os requisitos do cliente, incluindo os parâmetros do processo, as propriedades do material e os resultados desejados.
- Projeto: Com base na consulta, os engenheiros desenvolvem um projeto detalhado para o forno, incluindo as suas dimensões, elementos de aquecimento, sistemas de controlo de temperatura e características de segurança.
- Fabrico: O forno é fabricado com materiais e componentes de alta qualidade, garantindo durabilidade e fiabilidade.
- Testes e validação: O forno acabado é submetido a testes rigorosos para garantir que cumpre as especificações do cliente e funciona como pretendido.
Ao tirar partido das soluções personalizadas de fornos de vácuo, os engenheiros e cientistas podem desbloquear novas possibilidades na investigação e desenvolvimento de materiais. Estes fornos permitem o controlo preciso dos processos de tratamento térmico, levando à criação de materiais inovadores com propriedades e desempenho melhorados.
Automação e controlo avançados: Melhorar a precisão e a eficiência
Os fornos de grafite a vácuo incorporam sistemas avançados de automação e controlo para garantir a regulação precisa da temperatura e a otimização do processo. Os controladores lógicos programáveis (PLCs) e os sistemas de aquisição de dados monitorizam e controlam os parâmetros do processo, ajustando a temperatura, a atmosfera e outras variáveis para alcançar os resultados desejados.
Estes sistemas fornecem monitorização em tempo real e registo de dados, permitindo aos operadores acompanhar o progresso do processo e tomar decisões informadas. Ajustam automaticamente as definições com base em parâmetros predefinidos, optimizando as condições para diferentes materiais e aplicações. Esta automatização reduz o risco de erro humano e assegura uma qualidade consistente do produto.
Os sistemas de controlo avançados também permitem a monitorização e o controlo remotos, permitindo aos operadores aceder e gerir os fornos a partir de qualquer local com uma ligação à Internet. Esta capacidade facilita a resolução remota de problemas, reduz o tempo de inatividade e melhora a eficiência global do processo.
Ao integrar sistemas avançados de automação e controlo, os fornos de grafite a vácuo proporcionam uma regulação precisa da temperatura, parâmetros de processo optimizados e uma maior eficiência, conduzindo a resultados consistentes e de alta qualidade e a custos operacionais reduzidos.
Eficiência energética e sustentabilidade: Adoção de práticas ecológicas
A indústria de fornos de vácuo está ativamente empenhada na sustentabilidade ambiental, reconhecendo a importância de minimizar o consumo de energia e reduzir as emissões de carbono. Os fornos de vácuo são dispositivos inerentemente eficientes em termos energéticos, mas os fabricantes estão continuamente a inovar para melhorar ainda mais as suas credenciais de sustentabilidade.
Um aspeto fundamental da eficiência energética nos fornos de vácuo é o controlo preciso dos ciclos de aquecimento e arrefecimento. Ao utilizar sistemas avançados de automação e controlo, os fornos de vácuo podem ser programados para fornecer a quantidade exacta de energia necessária para aquecer a carga de trabalho até à temperatura desejada. Isto elimina o consumo desnecessário de energia durante as fases sem aquecimento, tais como bombagem, carregamento, descarregamento e arrefecimento.
Além disso, os fornos de vácuo são concebidos com elementos de aquecimento eficientes e isolamento térmico para minimizar a perda de calor. Isto assegura que a maior parte da energia utilizada é direccionada para o aquecimento da carga de trabalho em vez de se escapar para o ambiente circundante.
Para além de otimizar o processo de aquecimento, os fabricantes também se concentram em reduzir o consumo de energia dos sistemas auxiliares. Os sistemas de arrefecimento a água, os sistemas de arrefecimento a gás e as bombas de vácuo podem contribuir para a pegada energética global de um forno de vácuo. Ao utilizar componentes energeticamente eficientes e ao otimizar o funcionamento destes sistemas, os fabricantes podem reduzir significativamente o consumo de energia.
Ao adotar práticas energeticamente eficientes, os fabricantes de fornos de vácuo estão não só a contribuir para um futuro mais ecológico, mas também a ajudar os seus clientes a poupar dinheiro em custos de energia. Ao reduzir o consumo de energia, as empresas podem diminuir as suas despesas operacionais e melhorar a sua rentabilidade.
Como a procura de soluções sustentáveis continua a crescer, os fabricantes de fornos de vácuo estão bem posicionados para satisfazer as necessidades dos seus clientes. Ao investir na eficiência energética e na sustentabilidade, estão a demonstrar o seu compromisso com a gestão ambiental e a fornecer aos seus clientes as ferramentas de que necessitam para reduzir a sua pegada de carbono e atingir os seus objectivos de sustentabilidade.
Suporte técnico e serviço inigualáveis: Garantir um desempenho ótimo
O apoio técnico e a assistência técnica fiáveis são essenciais para garantir um desempenho ótimo dos fornos de grafite a vácuo. A assistência especializada pode ajudá-lo a resolver problemas rapidamente, minimizar o tempo de inatividade e maximizar a eficiência do seu forno.
A nossa equipa de técnicos experientes está disponível 24 horas por dia, 7 dias por semana, para prestar assistência por telefone, e-mail ou chat ao vivo. Também oferecemos serviço e formação no local para garantir que a sua fornalha está a funcionar com o máximo desempenho.
Vantagens da assistência técnica e do serviço incomparáveis:
- Redução do tempo de inatividade: A assistência especializada pode ajudá-lo a identificar e resolver rapidamente os problemas, minimizando o tempo de inatividade e mantendo a sua fornalha a funcionar sem problemas.
- Desempenho melhorado: A manutenção e a calibração regulares garantem que o seu forno está a funcionar com uma eficiência óptima, produzindo resultados de alta qualidade.
- Tempo de vida útil alargado: Uma manutenção e assistência adequadas podem prolongar a vida útil da sua fornalha, poupando-lhe dinheiro a longo prazo.
- Paz de espírito: O facto de saber que tem acesso a apoio especializado proporciona paz de espírito e permite-lhe concentrar-se na sua investigação ou produção.
O nosso compromisso com a satisfação do cliente:
Acreditamos que a satisfação do cliente vai para além da compra inicial. O nosso apoio e serviço técnico abrangente foi concebido para garantir que o seu forno de grafite de vácuo tem um desempenho ótimo durante toda a sua vida útil. Estamos empenhados em fornecer-lhe o mais alto nível de apoio e serviço para o ajudar a atingir os seus objectivos de investigação ou produção.
Experimente a diferença da Graphite Furnace Systems:
Quando escolheGraphite Furnace Systemsnão só obtém um forno de grafite a vácuo de alta qualidade, como também tem acesso ao nosso apoio técnico e serviço sem paralelo. A nossa equipa de especialistas dedica-se a ajudá-lo a tirar o máximo partido do seu forno e a obter um desempenho ótimo.
Contacte-nos hoje para saber mais sobre o nosso apoio técnico e ofertas de serviços, e experimente a diferença da Graphite Furnace Systems!
CONTACTE-NOS PARA UMA CONSULTA GRATUITA
Os produtos e serviços da KINTEK LAB SOLUTION foram reconhecidos por clientes de todo o mundo. A nossa equipa terá todo o prazer em ajudar com qualquer questão que possa ter. Contacte-nos para uma consulta gratuita e fale com um especialista de produto para encontrar a solução mais adequada para as suas necessidades de aplicação!