Introdução à importância das atmosferas dos fornos
As atmosferas dos fornos desempenham um papel crucial em vários processos de tratamento térmico, como a sinterização e o recozimento. São essenciais para evitar a oxidação, reduzir o risco de contaminação e melhorar as propriedades dos materiais que estão a ser tratados. Um forno de atmosfera inerte, por exemplo, foi concebido para manter um ambiente controlado, isento de oxigénio, humidade e outras impurezas. Este tipo de forno é utilizado em aplicações que requerem o processamento de materiais a alta temperatura, tais como cerâmicas, metais e compósitos. A utilização de fornos de atmosfera controlada pode resultar numa melhor qualidade do material, maior eficiência e custos reduzidos.
Índice
- Introdução à importância das atmosferas dos fornos
- O que é um forno de atmosfera inerte?
- Utilização de fornos de atmosfera inerte para sinterização e recozimento
- Vantagens dos fornos de atmosfera controlada
- Condições ambientais melhoradas
- Melhor controlo do forno e rendimento eficiente
- Duas categorias principais: Fornos de lote e contínuos
- Fornos de atmosfera da KINTEK
- Conclusão
O que é um forno de atmosfera inerte?
Um forno de atmosfera inerte é um tipo de equipamento de laboratório utilizado para processos de sinterização e recozimento. Proporciona um ambiente controlado e isento de oxigénio que é essencial para determinadas aplicações de alta temperatura. Inerte significa quimicamente inativo, razão pela qual as atmosferas inertes são necessárias para processos químicos que não requerem contaminação por gases reactivos.
Como funciona um forno de atmosfera inerte?
Os fornos de atmosfera inerte funcionam removendo o oxigénio e outros gases reactivos do ambiente. Isto é conseguido através da purga do forno com um gás inerte, como o azoto ou o árgon. O forno é então aquecido à temperatura desejada e o material a ser sinterizado ou recozido é colocado no interior. O forno é selado para manter a atmosfera inerte, o que permite que o material seja submetido ao processo de aquecimento e arrefecimento sem qualquer oxidação ou outras reacções químicas.
Porque é que um processo requer um forno de atmosfera inerte?
Muitos processos de tratamento térmico requerem uma atmosfera altamente controlada para alcançar o resultado desejado. Por exemplo, a sinterização, o recozimento brilhante e a carbonitretação são processos utilizados para fabricar peças para várias indústrias. Estes processos requerem atmosferas que são altamente controladas para garantir um resultado bem sucedido. As atmosferas inertes, como as criadas por um forno de atmosfera inerte, são necessárias para evitar reacções químicas como a descarbonetação ou a oxidação, que podem ter um impacto negativo na qualidade e no desempenho do produto acabado.
A importância dos gases de atmosfera inerte
Os gases de atmosfera inerte são essenciais para criar o ambiente controlado necessário para os processos de sinterização e recozimento. O azoto, o hélio e o árgon são normalmente utilizados para criar atmosferas inertes porque são quimicamente estáveis e têm uma baixa reatividade. Ao utilizar estes gases, os investigadores e fabricantes podem criar um ambiente estável e sem oxigénio que permite um controlo preciso do aquecimento e arrefecimento dos materiais.
Em conclusão, um forno de atmosfera inerte é uma peça crítica de equipamento para investigadores e fabricantes que trabalham com materiais a alta temperatura. Ao proporcionar um ambiente estável e isento de oxigénio para os processos de sinterização e recozimento, os fornos de atmosfera inerte podem ajudar a obter melhores resultados e resultados de produção mais consistentes.
Utilização de fornos de atmosfera inerte para sinterização e recozimento
Os fornos de atmosfera inerte são amplamente utilizados em processos de sinterização e recozimento para criar um ambiente livre de gases reactivos. A utilização de gás inerte, como o árgon ou o nitrogénio, cria uma atmosfera estável e consistente que reduz a probabilidade de reacções indesejadas durante o processo de sinterização ou recozimento.
Vantagens da utilização de fornos com atmosfera inerte
A utilização de fornos de atmosfera inerte oferece várias vantagens. Uma das vantagens mais significativas é a melhoria da qualidade do produto. Ao criar uma atmosfera estável e consistente, os fornos de atmosfera inerte podem ajudar a produzir produtos finais de alta qualidade com menos defeitos.
Outro benefício é o aumento da eficiência da produção. Os fornos de atmosfera inerte podem ajudar a reduzir o tempo de processamento e melhorar o rendimento da produção. Isto é conseguido minimizando a necessidade de retrabalho e aumentando o rendimento de produtos de alta qualidade.
Redução da contaminação e da oxidação
Os fornos de atmosfera inerte também podem minimizar a contaminação e a oxidação, que podem ter um impacto significativo nas propriedades finais do produto. A utilização de uma atmosfera controlada ajuda a reduzir a probabilidade de contaminação de fontes externas e também evita a oxidação do produto durante o processo de sinterização ou recozimento.
Versatilidade nos materiais
Os fornos de atmosfera inerte podem ser utilizados para uma vasta gama de materiais, incluindo metais, cerâmicas e compósitos, tornando-os numa ferramenta essencial para muitas indústrias. A capacidade de utilizar estes fornos para diferentes materiais proporciona aos fabricantes uma maior flexibilidade no que respeita à conceção e produção de produtos.
Vantagens dos fornos de atmosfera controlada
Os fornos de atmosfera controlada oferecem várias vantagens aos técnicos de laboratório, tornando-os uma ferramenta essencial nos processos de sinterização e recozimento.
Ambiente personalizado para aplicações específicas
Uma das vantagens mais significativas dos fornos de atmosfera controlada é a capacidade de criar um ambiente específico que pode ser adaptado a uma determinada aplicação. Ao controlar a composição do gás, a temperatura e a pressão no interior do forno, os técnicos de laboratório podem manipular as reacções químicas que ocorrem durante a sinterização e o recozimento, melhorando a qualidade e a consistência do produto final.
Prevenção da oxidação
Os fornos de atmosfera controlada podem ser utilizados para evitar a oxidação de materiais sensíveis, removendo o oxigénio do ambiente. Isto reduz o risco de contaminação e melhora a pureza do produto.
Processamento a alta temperatura
Outra vantagem dos fornos de atmosfera controlada é a sua capacidade de funcionar a altas temperaturas, proporcionando uma maior flexibilidade nos materiais que podem ser processados. Estes fornos são normalmente utilizados na produção de cerâmica, metais e semicondutores, onde são necessárias temperaturas elevadas para atingir as propriedades desejadas.
Controlo preciso para resultados exactos e reprodutíveis
O controlo preciso oferecido pelos fornos de atmosfera controlada significa que os técnicos de laboratório podem obter resultados mais precisos e reprodutíveis. Isto reduz o risco de erros e melhora a qualidade geral da sua investigação.
Superior aos fornos de caixa e de banho de sal
Os fornos de atmosfera controlada já substituíram largamente os fornos de caixa (carburação em pacote) e os fornos de banho de sal, com base no facto de apresentarem um melhor controlo do forno, um rendimento mais eficiente e serem menos exigentes em termos de mão de obra. Oferecem também condições ambientais de funcionamento muito melhores, sem os graves problemas de contaminação do solo com sais tóxicos (cianetos) e as dificuldades de eliminação dos resíduos de sais, dos gabaritos e acessórios contaminados e dos resíduos da cementação em caixa.
Em geral, os benefícios dos fornos de atmosfera controlada tornam-nos numa ferramenta indispensável para os laboratórios que trabalham em ciência dos materiais, química e engenharia.
Condições ambientais melhoradas
Os fornos de atmosfera controlada são concebidos para criar um ambiente onde os materiais podem ser aquecidos com precisão e sem qualquer contaminação indesejada. Uma das principais vantagens da utilização de um forno de atmosfera controlada é a melhoria das condições ambientais que proporciona. Ao controlar a atmosfera no interior do forno, é possível reduzir a quantidade de oxigénio e humidade presentes, o que pode ter um impacto significativo na qualidade do produto acabado.
Níveis reduzidos de oxigénio
Ao reduzir a quantidade de oxigénio presente durante o processo de sinterização ou recozimento, é possível evitar a oxidação, que pode conduzir a um produto final mais fraco e menos durável. Quando os níveis de oxigénio são elevados, pode reagir com muitos elementos químicos a temperaturas variáveis, provocando a oxidação. Com um forno de atmosfera controlada, os níveis de oxigénio podem ser reduzidos para evitar que isto aconteça. O azoto é considerado um gás de transporte quimicamente inerte do ar e é frequentemente utilizado como gás redutor para evitar a oxidação do material em fornos de alta temperatura. Este processo de cobertura é realizado utilizando entradas de gás, como medidores de fluxo de azoto, e uma porta de exaustão para expelir o gás gasto da câmara através de uma hotte ou de uma tubagem de coletor externo.
Redução dos níveis de humidade
Da mesma forma, ao controlar a quantidade de humidade presente, é possível evitar a formação de compostos químicos indesejados, que também podem afetar a qualidade do produto acabado. A humidade pode causar reacções químicas indesejadas durante o processo de recozimento, o que pode afetar a qualidade do produto final. Ao utilizar um forno de atmosfera controlada, os níveis de humidade podem ser reduzidos, garantindo que o produto final é de alta qualidade.
Aumento da eficiência e da produtividade
Para além destes benefícios ambientais, os fornos de atmosfera controlada também oferecem uma maior eficiência e produtividade, bem como uma maior flexibilidade e controlo sobre todo o processo de sinterização ou recozimento. Ao utilizar um forno de atmosfera controlada, é possível criar um ambiente mais propício ao processo de aquecimento, o que pode levar a um aquecimento mais rápido e mais eficiente. Isto, por sua vez, pode ajudar a aumentar a produtividade e a reduzir os custos.
Melhor controlo do forno e produção eficiente
Os fornos de atmosfera controlada (CAFs) oferecem várias vantagens em relação aos fornos tradicionais, incluindo um melhor controlo do ambiente do forno e um rendimento mais eficiente. Os fornos de atmosfera controlada são concebidos para funcionar em ambientes com níveis controlados de oxigénio, azoto ou outros gases, que podem ser ajustados com base nas necessidades específicas do processo.
Controlo preciso do ambiente do forno
Uma das maiores vantagens dos CAFs é a sua capacidade de oferecer um controlo preciso do ambiente do forno. Este nível de controlo pode levar a uma melhor qualidade do produto, uma vez que permite um controlo mais preciso do processo de sinterização ou recozimento. Os fornos CAF podem funcionar em ambientes com níveis controlados de oxigénio, azoto ou outros gases. Este nível de controlo pode levar a uma melhor qualidade do produto, uma vez que permite um controlo mais preciso do processo de sinterização ou recozimento.
Eficiência melhorada
Outra vantagem dos fornos CAF é a sua capacidade de processar materiais a temperaturas mais elevadas do que os fornos tradicionais, o que pode levar a tempos de processamento mais rápidos e a uma maior eficiência. As CAFs podem frequentemente processar materiais a temperaturas mais elevadas do que os fornos tradicionais, o que pode levar a tempos de processamento mais rápidos e a uma maior eficiência. Isto é particularmente importante para processos que requerem um processamento a alta temperatura, como a sinterização e o recozimento.
Oxidação reduzida
Os CAFs também têm a capacidade de reduzir a quantidade de oxidação que ocorre durante o processo de sinterização ou recozimento, o que pode ajudar a preservar a integridade do material que está a ser processado. Isto pode ser particularmente importante para materiais que são sensíveis à oxidação, como certos metais ou cerâmicas.
Qualidade consistente da produção
O controlo preciso do ambiente do forno nas CAFs conduz a uma qualidade consistente dos resultados, o que é vital para aplicações em investigação e desenvolvimento, bem como no fabrico industrial. A capacidade de controlar os níveis de oxigénio, azoto ou outros gases durante o processo de sinterização ou recozimento garante que o produto final cumpre os padrões de qualidade desejados.
Conclusão
Em conclusão, os fornos CAF oferecem uma série de vantagens em relação aos fornos tradicionais para os processos de sinterização e recozimento. Proporcionam um melhor controlo do ambiente do forno, uma maior eficiência, uma oxidação reduzida e uma qualidade consistente dos resultados. Estas vantagens fazem dos fornos CAF a escolha ideal para uma vasta gama de aplicações, desde a investigação e desenvolvimento até ao fabrico industrial.
Duas categorias principais: Fornos de lote e contínuos
Os fornos de atmosfera controlada são equipamento de laboratório essencial utilizado para processos de sinterização e recozimento em muitas indústrias. Existem duas categorias principais de fornos de atmosfera controlada: fornos de lote e fornos contínuos.
Fornos de lote
Os fornos de lote são adequados para pequenas quantidades de produtos e o material é carregado no forno num lote e aquecido à temperatura desejada durante um período específico. O forno de lote é um forno de câmara única que é carregado, aquecido e descarregado como um lote. A temperatura, a composição do gás e a pressão são definidas para todo o processo do lote. O forno de lote é ideal para a produção e investigação em pequena escala e também é adequado para materiais que requerem uma temperatura e atmosfera específicas durante um período específico.
Fornos contínuos
Por outro lado, os fornos contínuos são adequados para grandes quantidades de produtos que requerem um fluxo contínuo de material através do forno. Nos fornos contínuos, o material é carregado numa extremidade e transportado através do forno por um sistema de transporte. O sistema de transporte é concebido para proporcionar um fluxo contínuo de material através do forno. A temperatura, a composição do gás e a pressão são controladas ao longo de todo o processo. Os fornos contínuos são ideais para a produção de grandes volumes e são normalmente utilizados nas indústrias automóvel, aeroespacial e eletrónica.
Tanto os fornos descontínuos como os contínuos oferecem várias vantagens. Os fornos de atmosfera controlada podem melhorar significativamente a qualidade do produto final. As vantagens da utilização destes fornos incluem a redução da oxidação, a melhoria das propriedades dos materiais e o aumento do rendimento do produto. Os fornos de atmosfera controlada também podem melhorar a uniformidade do produto, reduzir o consumo de energia e minimizar a contaminação e os resíduos.
Em conclusão, os fornos de atmosfera controlada desempenham um papel fundamental em várias indústrias e oferecem uma série de benefícios para os processos de sinterização e recozimento. A escolha entre fornos descontínuos e contínuos depende das necessidades específicas da indústria ou do laboratório. O forno descontínuo é adequado para a produção e investigação em pequena escala, enquanto o forno contínuo é ideal para a produção de grandes volumes. Ambos os tipos de fornos são concebidos para proporcionar um ambiente controlado que melhora as propriedades do material e minimiza a oxidação.
Fornos de atmosfera da KINTEK
Os fornos atmosféricos são essenciais para os processos de sinterização e recozimento num ambiente laboratorial. A KINTEK, um dos principais fabricantes de equipamento de laboratório, oferece fornos atmosféricos que proporcionam um ambiente controlado com precisão para processos de sinterização e recozimento, de modo a garantir resultados da mais alta qualidade possível.
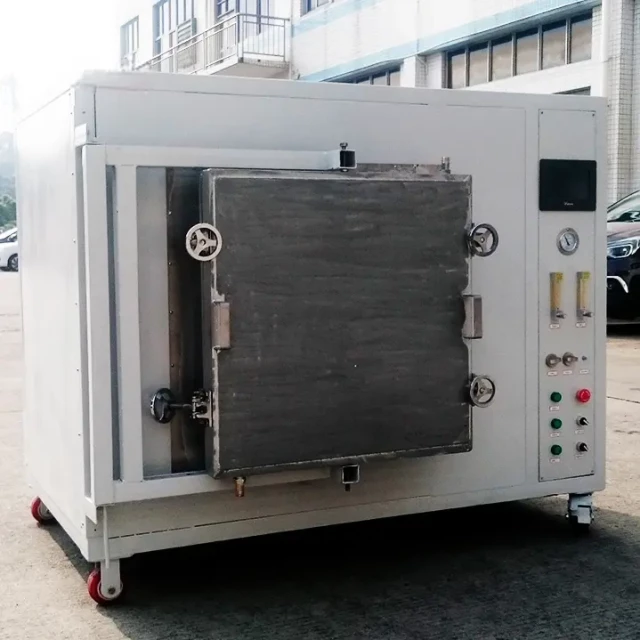
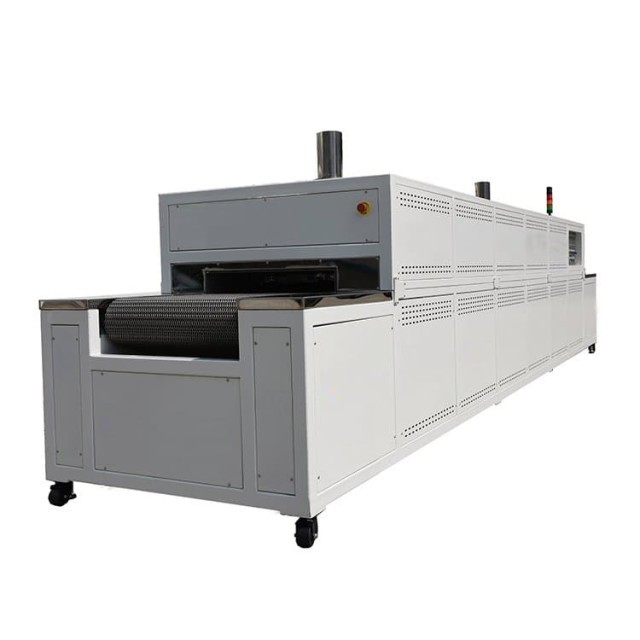
Características dos fornos atmosféricos KINTEK
Os fornos atmosféricos KINTEK são concebidos de acordo com as especificações exclusivas do cliente. Estes fornos têm uma gama de tamanhos de zonas de aquecimento e gamas de temperatura de trabalho (1100°C, 1300°C e 1600°C), o que os torna ideais para uma vasta gama de aplicações, desde a metalurgia e ciência dos materiais até ao processamento de semicondutores e fabrico de eletrónica.
Atmosfera controlada
Os fornos atmosféricos funcionam através do controlo do ambiente em que as amostras são aquecidas, criando uma atmosfera específica que pode afetar significativamente as propriedades finais do material a ser processado. Os fornos de atmosfera controlada da KINTEK vêm com várias características patenteadas que permitem uma melhor mistura, resultando numa melhor transferência de calor e de massa. A ausência de peças móveis no sistema de suporte do tubo proporciona um design simples, fiável e robusto que aumenta a escalabilidade. Adicionalmente, a ação de agitação do produto dentro do tubo resulta em elevados graus de uniformidade de temperatura e contacto gás-sólido, produzindo um produto mais homogéneo, reduzindo os tempos de processamento e aumentando as taxas de produção.
Atmosferas de processo
Os fornos atmosféricos da KINTEK podem acomodar uma variedade de atmosferas de processo. Os excelentes designs de vedação da empresa e o foco no controlo da atmosfera incluem a integração de sistemas de reciclagem de atmosfera, sistemas de redução de gases e mistura de atmosfera controlada para um controlo de processo personalizado. Estas atmosferas incluem gases inflamáveis e tóxicos, tais como hidrogénio, azoto, árgon, ar, oxigénio, etileno, metano, CO2, CO e cloro gasoso.
Personalização
A KINTEK aborda o projeto de um forno atmosférico como um sistema completo, com a capacidade de incorporar sistemas de controlo de processos, tratamento e manuseamento de gases, instalação chave-na-mão e comissionamento completo no terreno. A empresa também oferece fornos de laboratório de alta temperatura personalizados que proporcionam um excelente controlo e uniformidade da temperatura, bem como eficiência energética. Estes fornos podem ser modificados a partir de um modelo padrão ou construídos de acordo com as especificações exactas do cliente.
Em conclusão, os fornos de atmosfera da KINTEK são uma excelente escolha para qualquer laboratório que pretenda melhorar a qualidade e a consistência do seu trabalho. Estes fornos oferecem um ambiente controlado com precisão para processos de sinterização e recozimento, reduzindo a oxidação, controlando a formação de fases e melhorando a qualidade geral e a consistência do produto final.
Conclusão
Em conclusão, os fornos de atmosfera controlada tornaram-se parte integrante dos processos de sinterização e recozimento devido à sua capacidade de criar um ambiente inerte que evita a oxidação, reduz a contaminação e melhora a qualidade do produto final. Oferecem melhores condições ambientais, melhor controlo do forno, rendimento eficiente e um nível de segurança mais elevado em comparação com os fornos tradicionais. A KINTEK oferece uma vasta gama de fornos de atmosfera que são concebidos para satisfazer as necessidades de várias indústrias. Investir num forno de atmosfera controlada pode ajudar as empresas a poupar tempo, reduzir custos e produzir produtos de alta qualidade que cumprem as normas da indústria.
CONTACTE-NOS PARA UMA CONSULTA GRATUITA
Os produtos e serviços da KINTEK LAB SOLUTION foram reconhecidos por clientes de todo o mundo. A nossa equipa terá todo o prazer em ajudar com qualquer questão que possa ter. Contacte-nos para uma consulta gratuita e fale com um especialista de produto para encontrar a solução mais adequada para as suas necessidades de aplicação!