A transferência de calor num forno de mufla é um aspeto crítico do seu funcionamento, uma vez que determina a eficiência com que o forno pode aquecer os materiais até às temperaturas desejadas.O forno baseia-se principalmente no aquecimento por resistência eléctrica, em que a energia eléctrica é convertida em calor e transferida para a peça de trabalho.A conceção da mufla, incluindo o seu isolamento, os elementos de aquecimento e a estrutura da câmara, desempenha um papel significativo na garantia de uma transferência de calor eficaz.Factores como o tamanho do forno, a disponibilidade de energia e a construção do material também influenciam o processo de transferência de calor.A compreensão destes elementos ajuda a otimizar o desempenho do forno para aplicações específicas, como o ensaio de materiais ou o tratamento térmico.
Pontos-chave explicados:
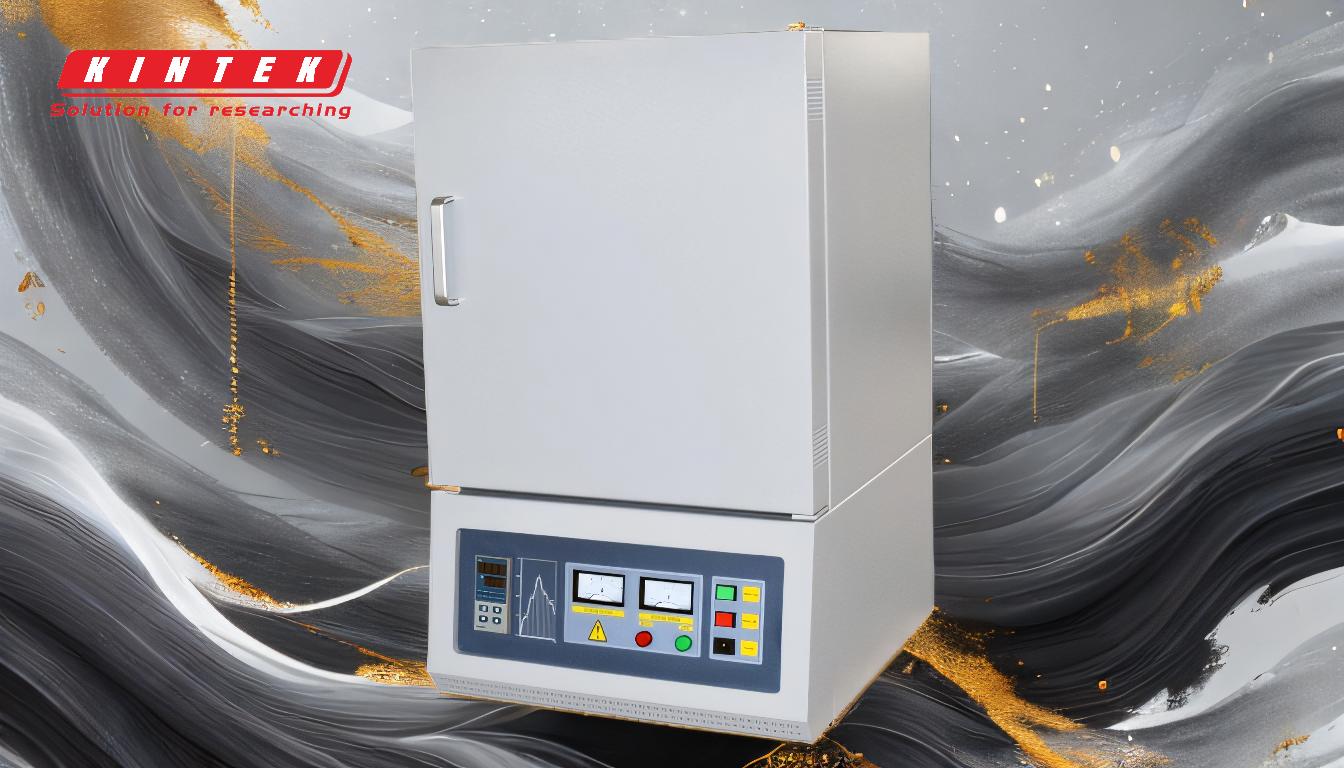
-
Princípio de funcionamento da transferência de calor:
- O forno de mufla funciona segundo o princípio do aquecimento por resistência eléctrica.A energia eléctrica é convertida em calor pelos elementos de aquecimento, que é depois transferido para a peça de trabalho.
- A lei da conservação da energia garante que o calor gerado é efetivamente utilizado dentro da câmara do forno.
-
Conceção e construção:
- Os fornos de mufla são tipicamente em forma de barril e construídos com materiais resistentes a altas temperaturas.Esta conceção ajuda a manter temperaturas elevadas e a garantir uma transferência de calor eficiente.
- Os elementos de aquecimento são frequentemente colocados dentro de tijolos refractários ou dentro do isolamento, permitindo que o calor seja transferido para a câmara interior através das paredes.
-
Controlo e consistência da temperatura:
- Os fornos de mufla modernos utilizam elementos de aquecimento eléctricos, que proporcionam um maior controlo e consistência da temperatura em comparação com os modelos antigos baseados na combustão.
- As câmaras de combustão e aquecimento separadas nos modelos mais antigos eram seladas a gás para evitar a contaminação, mas os modelos eléctricos eliminam totalmente os subprodutos da combustão.
-
Factores que afectam a transferência de calor:
- Tensão de alimentação:É necessária uma tensão adequada para garantir que os elementos de aquecimento possam gerar calor suficiente.
- Condição do elemento de aquecimento:Os elementos de aquecimento gastos ou danificados podem reduzir a eficiência da transferência de calor.
- Tamanho e estrutura da câmara do forno:As câmaras maiores podem necessitar de mais energia para atingir a mesma temperatura, enquanto a estrutura afecta a distribuição do calor.
- Precisão do controlador de temperatura:O controlo preciso da temperatura assegura uma transferência de calor consistente.
- Vedação da câmara do forno:A vedação correta evita a perda de calor e mantém a consistência da temperatura.
- Qualidade do isolamento:O isolamento de alta qualidade minimiza a perda de calor e melhora a eficiência.
- Condições de carga:A quantidade e o tipo de material a ser aquecido podem afetar as taxas de transferência de calor.
- Precisão do termopar:A medição exacta da temperatura é crucial para uma gestão eficaz do calor.
- Vedação da porta do forno:Uma porta bem vedada evita a fuga de calor e a contaminação.
- Práticas operacionais:O funcionamento correto, incluindo evitar a abertura frequente da porta e minimizar a acumulação de pó, ajuda a manter uma transferência de calor eficiente.
-
Aplicações e importância da transferência de calor:
- Os fornos de mufla são utilizados em laboratórios para processos de alta temperatura, como o teste do teor de cinzas em materiais de borracha e polímeros.
- Uma transferência de calor eficaz garante que os materiais são aquecidos uniformemente e às temperaturas necessárias, o que é crucial para resultados experimentais exactos e para a análise das propriedades dos materiais.
-
Adaptações históricas e modernas:
- Historicamente, os fornos de mufla tinham câmaras de combustão e de aquecimento separadas para evitar a contaminação.Com o advento dos elementos de aquecimento eléctricos em meados da década de 1950, a maioria dos fornos foi convertida em eléctricos, melhorando a eficiência e o controlo da transferência de calor.
- As muflas eléctricas modernas oferecem maior flexibilidade e adaptabilidade, tornando-as adequadas para uma vasta gama de aplicações de alta temperatura.
A compreensão destes pontos-chave ajuda a selecionar e a operar eficazmente uma mufla, garantindo uma transferência de calor e um desempenho ideais para necessidades laboratoriais ou industriais específicas.
Tabela de resumo:
Aspeto-chave | Detalhes |
---|---|
Princípio de funcionamento | O aquecimento por resistência eléctrica converte a energia eléctrica em calor. |
Caraterísticas de conceção | Em forma de barril, materiais resistentes a altas temperaturas e paredes isoladas. |
Controlo da temperatura | Os elementos de aquecimento eléctricos asseguram um controlo preciso e consistente da temperatura. |
Factores que afectam a eficiência | Tensão de alimentação, estado do elemento de aquecimento, qualidade do isolamento, etc. |
Aplicações | Utilizado em laboratórios para testes de teor de cinzas, análise de materiais e tratamento térmico. |
Adaptações modernas | Os modelos eléctricos eliminam os subprodutos da combustão, aumentando a eficiência. |
Optimize a eficiência da transferência de calor do seu laboratório com um forno de mufla. contacte-nos hoje para obter aconselhamento especializado!