A brasagem, embora seja uma técnica de união amplamente utilizada, apresenta diversas desvantagens que podem afetar a qualidade, a eficiência e o custo do processo. Essas desvantagens variam dependendo do tipo de método de brasagem utilizado, como brasagem a vácuo ou brasagem manual. Os principais problemas incluem a redução da dureza do material, altos requisitos técnicos e de processo, consumo de energia, longos tempos de processamento e desafios relacionados à oxidação e resíduos de fluxo. Compreender essas desvantagens é crucial para quem considera a brasagem como método de união, pois elas podem impactar o desempenho do produto final e o processo de produção geral.
Pontos-chave explicados:
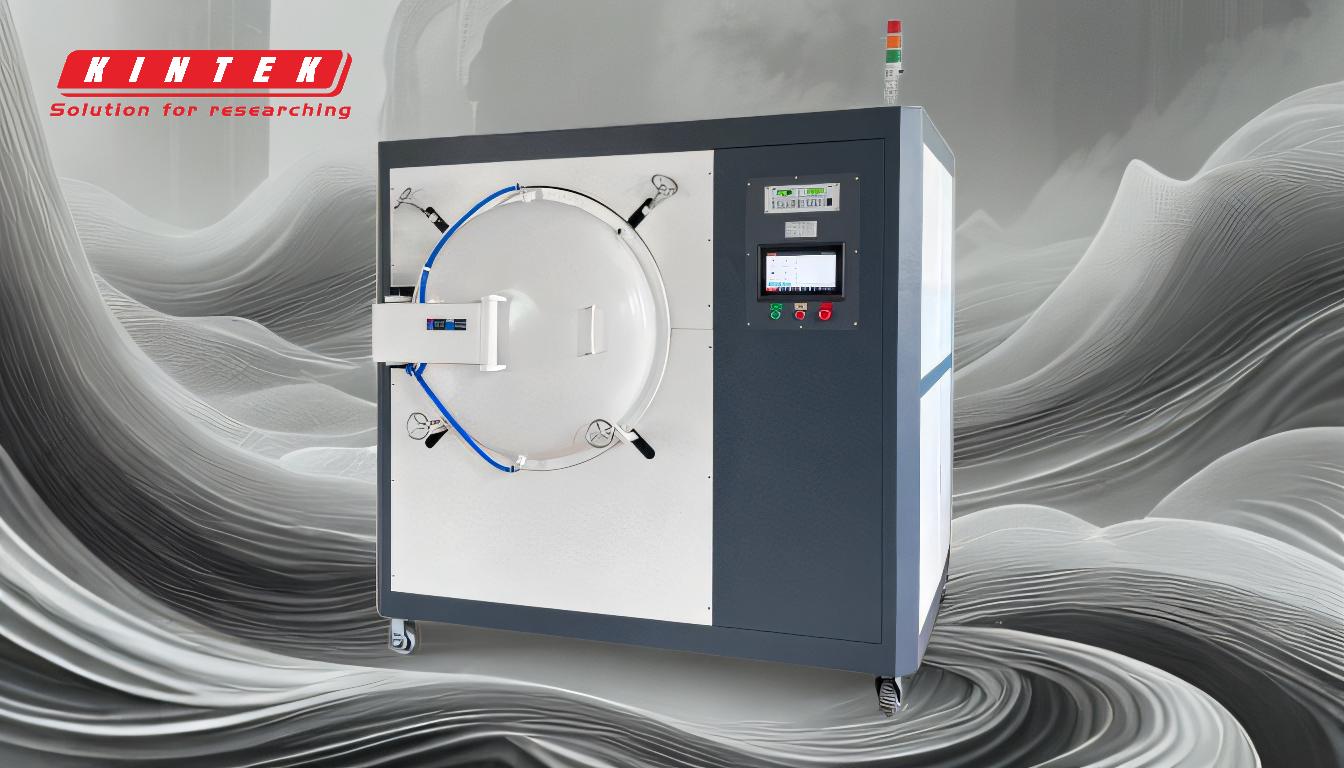
-
Dureza reduzida do material após soldagem em alta temperatura:
- Na brasagem a vácuo, as altas temperaturas necessárias para fundir o material de enchimento podem levar a uma redução na dureza do metal base. Isto é particularmente problemático para materiais que dependem da sua dureza para integridade estrutural ou resistência ao desgaste. O amolecimento do material pode comprometer a resistência e a durabilidade da junta, tornando-a menos adequada para aplicações de alto estresse.
-
Altos requisitos de processo e dificuldade técnica:
- A brasagem, especialmente a brasagem a vácuo, exige controle preciso sobre a temperatura, a atmosfera e a colocação do material de enchimento. Isto requer equipamentos especializados e operadores qualificados, aumentando a complexidade e o custo do processo. A necessidade de um ambiente controlado, como vácuo ou atmosfera de gás inerte, aumenta os desafios técnicos e limita a acessibilidade do processo para operações menores.
-
Alto consumo de energia:
- O processo de brasagem, principalmente a brasagem a vácuo, consome uma quantidade significativa de energia devido à necessidade de altas temperaturas e ambientes controlados. Isto não só aumenta os custos operacionais, mas também tem implicações ambientais, tornando-o menos sustentável em comparação com outros métodos de união.
-
Longo tempo de processamento:
- A brasagem muitas vezes requer ciclos prolongados de aquecimento e resfriamento para garantir a formação adequada das juntas e evitar estresse térmico. Isso pode levar a tempos de produção mais longos, reduzindo o rendimento e a eficiência. Em indústrias onde o tempo é um fator crítico, isto pode ser uma desvantagem significativa.
-
Altos custos de limpeza e proteção ambiental:
- Antes da brasagem, os materiais geralmente precisam ser cuidadosamente limpos para remover óxidos, óleos e outros contaminantes que possam prejudicar a qualidade da junta. Além disso, o uso de fluxos em alguns processos de brasagem pode deixar resíduos que necessitam de limpeza pós-brasagem. Estas etapas aumentam o custo geral e a complexidade do processo, e o descarte de agentes de limpeza e resíduos de fluxo pode ter implicações ambientais.
-
Superaquecimento e enfraquecimento do metal base na brasagem manual:
- Quando a brasagem é realizada manualmente com maçarico em ambiente aberto, existe o risco de superaquecimento do metal base. Isto pode levar ao enfraquecimento e oxidação localizados, resultando numa junta que é mecanicamente mais fraca e menos atraente visualmente. O aquecimento desigual também pode causar distorção ou empenamento dos componentes.
-
Resíduos de oxidação e fluxo:
- Na brasagem ao ar livre, a oxidação do metal base é um problema comum, que pode enfraquecer a junta e reduzir a sua qualidade estética. Para evitar a oxidação, são frequentemente utilizados fluxos, mas estes podem deixar resíduos difíceis de remover e podem causar vazios na junta. Esses vazios podem atuar como concentradores de tensão, reduzindo ainda mais a resistência da junta.
Em resumo, embora a brasagem ofereça diversas vantagens, como a capacidade de unir materiais diferentes e criar juntas fortes e estanques, ela também apresenta desvantagens significativas. Isso inclui amolecimento do material, altos requisitos técnicos e energéticos, longos tempos de processamento e problemas relacionados à oxidação e resíduos de fluxo. Compreender essas desvantagens é essencial para tomar decisões informadas sobre se a brasagem é o método de união correto para uma aplicação específica.
Tabela Resumo:
Desvantagem | Descrição |
---|---|
Dureza reduzida do material | As altas temperaturas na brasagem a vácuo amolecem o metal base, reduzindo a resistência. |
Altos requisitos de processo | Requer controle preciso de temperatura, equipamentos especializados e mão de obra qualificada. |
Alto consumo de energia | O uso significativo de energia aumenta os custos e o impacto ambiental. |
Longo tempo de processamento | Ciclos prolongados de aquecimento e resfriamento reduzem a eficiência da produção. |
Altos custos ambientais e de limpeza | A limpeza pré e pós-brasagem acrescenta complexidade e custo. |
Superaquecimento na brasagem manual | A brasagem manual com maçarico corre o risco de enfraquecer e deformar o metal base. |
Resíduos de oxidação e fluxo | A brasagem ao ar livre causa oxidação; resíduos de fluxo enfraquecem as juntas. |
Precisa de ajuda para decidir se a brasagem é adequada para sua aplicação? Contate nossos especialistas hoje para aconselhamento personalizado!