O recozimento do aço é um processo crítico de tratamento térmico que envolve aquecer o aço a uma temperatura específica, mantê-lo nessa temperatura por um determinado período e depois resfriá-lo lentamente. A duração do recozimento depende de vários fatores, incluindo o tipo de aço, sua espessura e as propriedades desejadas. Geralmente, o processo de recozimento pode levar de algumas horas a várias horas, dependendo dessas variáveis. O objetivo é alcançar uma microestrutura uniforme, aliviar tensões internas e melhorar a usinabilidade ou ductilidade. Abaixo, detalharemos os principais fatores que influenciam o tempo de recozimento e forneceremos uma explicação detalhada do processo.
Pontos-chave explicados:
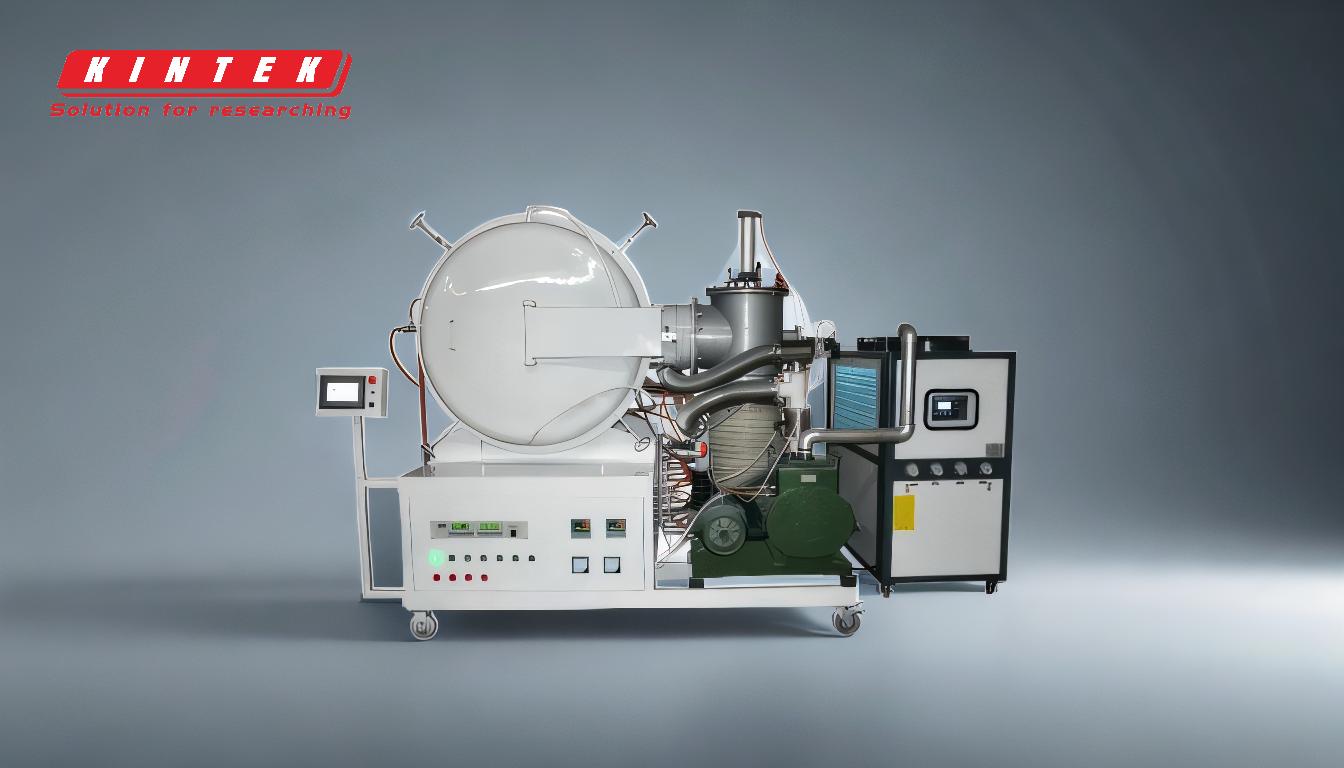
-
Tipo de Aço:
- Diferentes tipos de aço requerem diferentes temperaturas e tempos de recozimento. Por exemplo, os aços com baixo teor de carbono normalmente necessitam de temperaturas mais baixas e tempos de recozimento mais curtos em comparação com os aços com alto teor de carbono ou ligas. A composição específica do aço determina as condições ideais de recozimento.
-
Espessura do Aço:
- A espessura do aço desempenha um papel significativo na determinação do tempo de recozimento. Seções mais espessas requerem tempos de recozimento mais longos para garantir que o calor penetre uniformemente em todo o material. Chapas ou fios finos, por outro lado, podem exigir tempos de recozimento mais curtos.
-
Temperatura de recozimento:
- A temperatura na qual o aço é recozido varia dependendo do tipo de aço. Para a maioria dos aços, a temperatura de recozimento está normalmente entre 700°C e 900°C. O aço deve ser mantido nesta temperatura por tempo suficiente para permitir que a microestrutura se transforme completamente.
-
Tempo de espera:
- O tempo de permanência na temperatura de recozimento é crucial. Ele garante que o aço atinja uma temperatura uniforme e que ocorram as mudanças microestruturais desejadas. Para muitos aços, o tempo de espera pode variar de 1 a 4 horas, mas pode variar com base nos fatores mencionados acima.
-
Taxa de resfriamento:
- Após o período de espera, o aço deve ser resfriado lentamente para evitar a formação de tensões internas ou endurecimento. A taxa de resfriamento é normalmente controlada permitindo que o aço esfrie no forno ou usando um meio de resfriamento controlado. O resfriamento lento garante que o aço permaneça macio e dúctil.
-
Objetivo do Recozimento:
- O resultado pretendido do processo de recozimento também influencia a duração. Por exemplo, se o objetivo é melhorar a usinabilidade, o tempo de recozimento pode ser menor em comparação com quando o objetivo é atingir a suavidade máxima ou o alívio de tensões.
-
Tipo e capacidade do forno:
- O tipo de forno utilizado para recozimento pode afetar a duração do processo. Fornos maiores com melhor controle de temperatura podem permitir um recozimento mais preciso, mas também podem exigir ciclos de aquecimento e resfriamento mais longos.
-
Considerações Práticas:
- Em ambientes industriais, considerações práticas como cronogramas de produção, custos de energia e disponibilidade de equipamentos também podem influenciar o tempo de recozimento. A otimização desses fatores é essencial para um recozimento eficiente e econômico.
Em resumo, o tempo de recozimento do aço não é um parâmetro que sirva para todos. Varia de acordo com o tipo de aço, sua espessura, a temperatura de recozimento e o resultado desejado. Compreender esses fatores e como eles interagem é crucial para alcançar as propriedades desejadas no aço recozido. O recozimento executado corretamente pode melhorar significativamente o desempenho e a trabalhabilidade do aço, tornando-o um processo vital na metalurgia e na fabricação.
Tabela Resumo:
Fator | Influência no tempo de recozimento |
---|---|
Tipo de Aço | Os aços de baixo carbono requerem tempos mais curtos; aços com alto teor de carbono/liga precisam de mais tempo. |
Espessura do Aço | Seções mais espessas requerem tempos de recozimento mais longos para penetração uniforme do calor. |
Temperatura de recozimento | Normalmente 700°C–900°C; o tempo de retenção varia (1–4 horas). |
Taxa de resfriamento | O resfriamento lento evita tensões internas; o resfriamento controlado é essencial. |
Objetivo do Recozimento | Mais curto para usinabilidade; mais tempo para máxima suavidade ou alívio do estresse. |
Tipo/capacidade do forno | Fornos maiores podem exigir ciclos mais longos, mas oferecem melhor controle de temperatura. |
Considerações Práticas | Cronogramas de produção, custos de energia e disponibilidade de equipamentos afetam o tempo de recozimento. |
Precisa de ajuda para otimizar seu processo de recozimento de aço? Contate nossos especialistas hoje para soluções personalizadas!