O revestimento neutro de um forno de indução é um componente crítico concebido para proteger a estrutura do forno e melhorar o seu desempenho.É feito de materiais refractários capazes de suportar temperaturas extremas e de resistir a reacções químicas com metais fundidos.Este revestimento serve de barreira entre o metal fundido e a estrutura exterior do forno, como a bobina de indução, assegurando a longevidade e a eficiência do forno.Também isola o metal fundido, evitando a contaminação e mantendo a integridade do metal que está a ser fundido.O revestimento neutro é essencial para o funcionamento seguro e eficaz dos fornos de indução, o que o torna uma consideração fundamental para os compradores de equipamento e consumíveis.
Pontos-chave explicados:
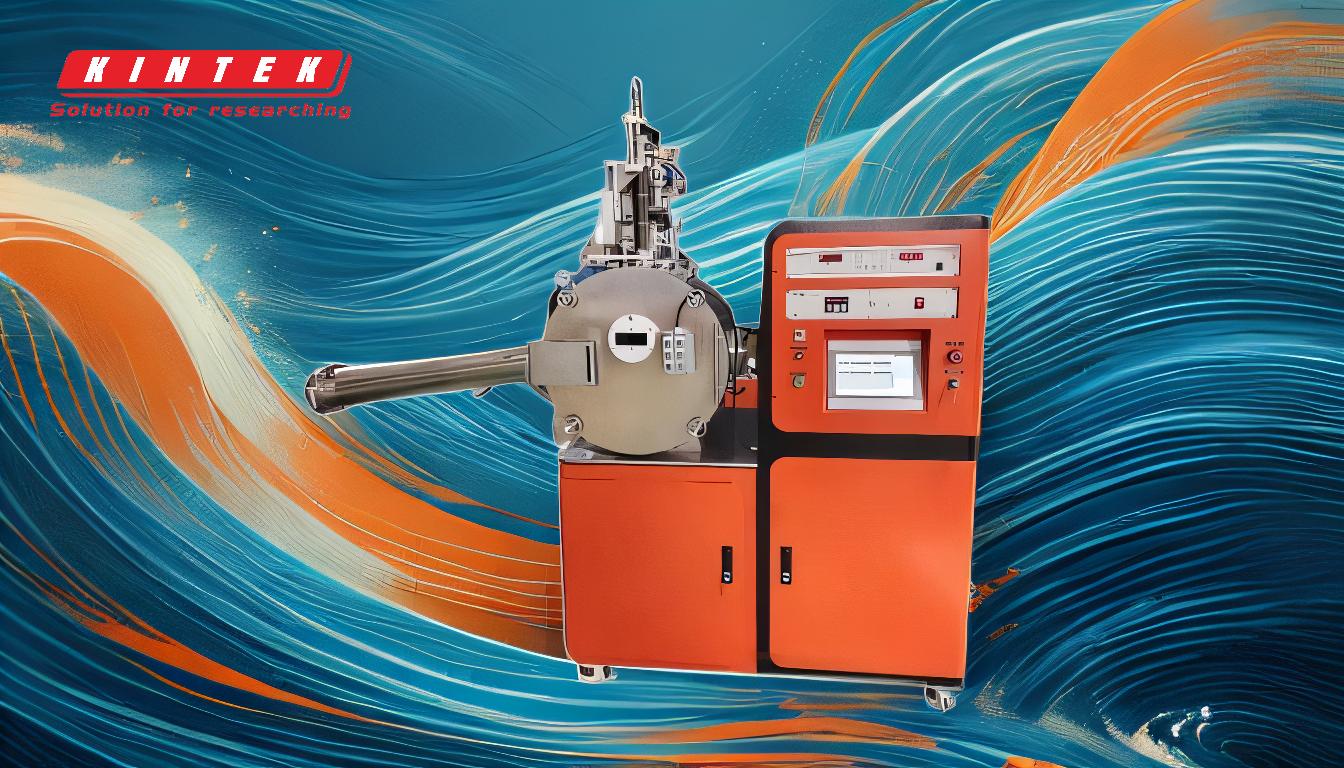
-
Definição e objetivo do revestimento neutro:
- O revestimento neutro é uma camada protetora no interior do forno de indução, feita de materiais refractários.
- O seu principal objetivo é conter o metal fundido, isolá-lo da estrutura exterior do forno e proteger o corpo do forno durante o funcionamento.
- Garante o funcionamento eficiente e seguro do forno, evitando reacções químicas e danos térmicos.
-
Materiais utilizados no revestimento neutro:
- Os materiais refractários são escolhidos pela sua capacidade de suportar temperaturas elevadas e resistir a reacções químicas com metais fundidos.
- Os materiais comuns incluem a alumina, a sílica e a magnésia, que são selecionados com base no tipo de metal a ser fundido e nas condições de funcionamento do forno.
-
Papel na proteção da estrutura do forno:
- O revestimento actua como uma barreira entre o metal fundido e a bobina de indução, evitando o contacto direto e potenciais danos.
- Também protege o corpo do forno do stress térmico e do desgaste mecânico, prolongando a vida útil do forno.
-
Importância na manutenção da integridade do metal:
- Ao isolar o metal fundido, o revestimento neutro evita a contaminação de elementos externos, garantindo a pureza e a qualidade do metal fundido.
- Isto é particularmente importante em aplicações que requerem composições de liga precisas, como nas indústrias aeroespacial e automóvel.
-
Impacto no desempenho do forno:
- Um revestimento neutro em bom estado de conservação assegura uma transferência de calor eficiente e uma fusão uniforme da carga metálica.
- Minimiza a perda de calor e reduz o consumo de energia, contribuindo para a rentabilidade global do funcionamento do forno.
-
Considerações para os compradores:
- Ao selecionar um revestimento neutro, os compradores devem considerar o tipo de metal a ser fundido, a temperatura de funcionamento e a frequência de utilização do forno.
- A escolha do material refratário deve estar de acordo com os requisitos específicos da aplicação para garantir um desempenho e uma durabilidade ideais.
-
Manutenção e substituição:
- A inspeção e manutenção regulares do revestimento neutro são essenciais para evitar fissuras, erosão e outras formas de desgaste.
- A substituição atempada do revestimento é necessária para evitar a paragem do forno e garantir um desempenho consistente.
Em resumo, o revestimento neutro de um forno de indução é um componente vital que garante o funcionamento seguro, eficiente e fiável do forno.Ele protege a estrutura do forno, mantém a integridade do metal fundido e contribui para o desempenho geral do forno.Para os compradores de equipamento e consumíveis, compreender o papel e a importância do revestimento neutro é crucial para tomar decisões informadas e otimizar as operações do forno.
Tabela de resumo:
Aspeto-chave | Detalhes |
---|---|
Objetivo | Protege a estrutura do forno, isola o metal fundido e garante um funcionamento seguro. |
Materiais | Alumina, sílica, magnésia - escolhidos para resistência a altas temperaturas. |
Papel na proteção | Actua como uma barreira, evita o stress térmico e o desgaste mecânico. |
Integridade do metal | Evita a contaminação, assegura a pureza e a qualidade do metal fundido. |
Impacto no desempenho | Melhora a transferência de calor, reduz o consumo de energia e melhora a eficiência. |
Considerações sobre a compra | Adequar os materiais refractários ao tipo de metal, temperatura e frequência de utilização. |
Manutenção | Inspeção regular e substituição atempada para evitar períodos de inatividade. |
Assegure-se de que o seu forno de indução funciona com o máximo desempenho- contacte os nossos especialistas hoje para saber mais sobre os revestimentos neutros!