A sinterização num forno de indução refere-se ao processo de compactação e ligação de partículas de pó numa massa sólida através da aplicação de calor, normalmente abaixo do ponto de fusão do material.Este processo é crucial para a formação do revestimento do forno, que deve suportar altas temperaturas e tensões mecânicas durante o funcionamento.O processo de sinterização num forno de indução envolve três fases fundamentais: cozedura, semi-sinterização e sinterização completa.Cada etapa é cuidadosamente controlada para garantir que o revestimento atinja uma microestrutura uniforme, durável e de alto desempenho.Os fornos de indução, com o seu controlo preciso da temperatura e capacidades de aquecimento uniforme, são adequados para processos de sinterização, garantindo a integridade e longevidade do revestimento.
Pontos-chave explicados:
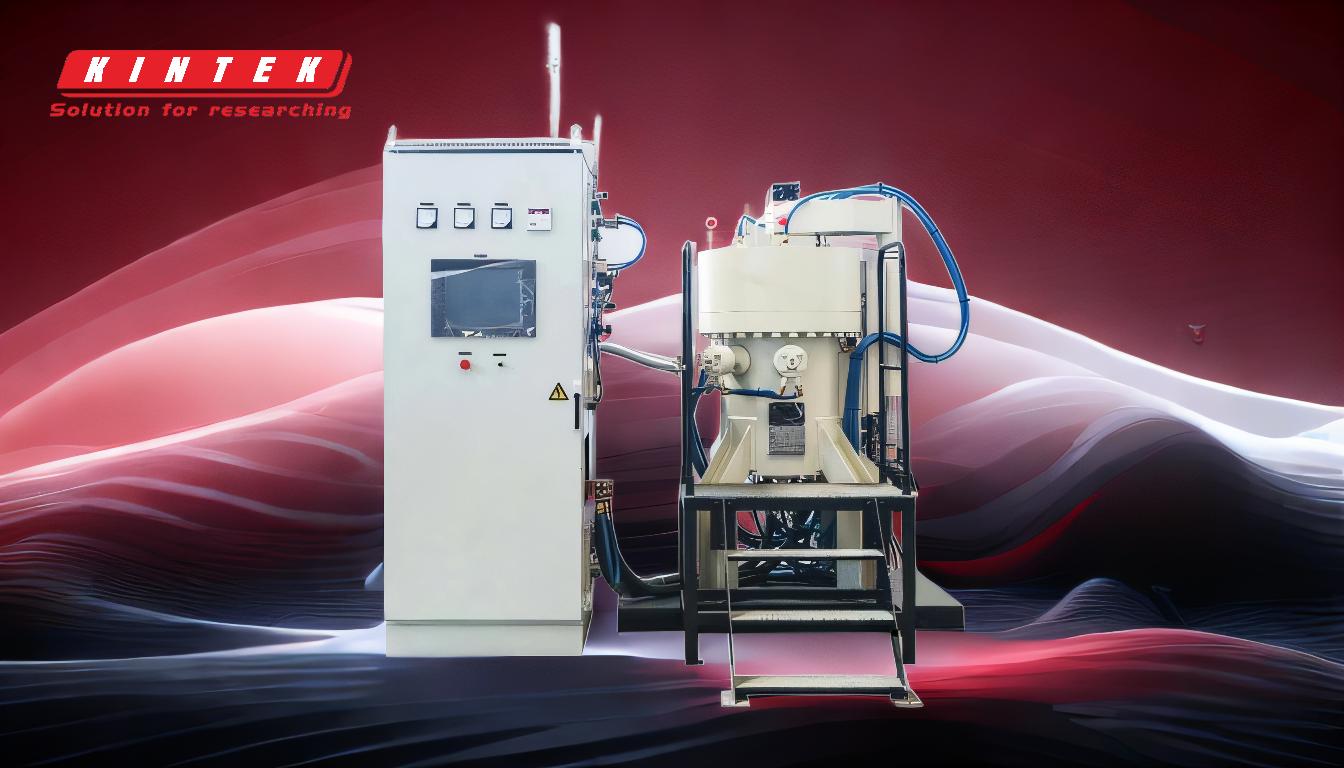
-
Definição de sinterização em fornos de indução:
- A sinterização é o processo de compactação e ligação de partículas de pó numa massa sólida utilizando calor, normalmente abaixo do ponto de fusão do material.
- Nos fornos de indução, a sinterização é utilizada principalmente para formar o revestimento refratário, que tem de suportar temperaturas elevadas e tensões mecânicas durante o funcionamento.
-
Etapas do processo de sinterização:
-
Fase de cozedura:
- O revestimento do forno é aquecido a cerca de 600°C a uma velocidade controlada.
- Esta fase remove a humidade do material refratário, evitando fissuras e assegurando a integridade estrutural.
-
Fase de Semi-Sinterização:
- A temperatura é aumentada para 900°C e mantida durante um período de tempo.
- Subsequentemente, a temperatura é aumentada para 1200°C a um ritmo mais rápido e mantida novamente.
- Esta fase inicia a ligação das partículas, formando uma estrutura semi-sólida.
-
Fase de Sinterização Completa:
- A temperatura final é ajustada com base nas propriedades do material e nas caraterísticas desejadas do revestimento.
- Esta fase assegura que o revestimento atinge uma microestrutura totalmente ligada, densa e duradoura.
-
Fase de cozedura:
-
Importância da sinterização para revestimentos de fornos:
- Um revestimento bem sinterizado tem uma estrutura de três camadas, proporcionando propriedades térmicas e mecânicas óptimas.
- A sinterização adequada aumenta a resistência do revestimento ao choque térmico, à erosão e às reacções químicas com metais fundidos.
- O processo de sinterização tem um impacto direto na vida útil do revestimento e no desempenho geral do forno.
-
O papel dos fornos de indução na sinterização:
- Os fornos de indução permitem um controlo preciso da temperatura e um aquecimento uniforme, essenciais para resultados de sinterização consistentes.
- O campo eletromagnético nos fornos de indução gera correntes de Foucault, assegurando uma composição e distribuição de temperatura uniformes no material de revestimento.
- Os fornos de indução podem atingir temperaturas até 1650°C, adequadas para a sinterização de uma vasta gama de materiais refractários.
-
Vantagens dos fornos de indução para sinterização:
- Aquecimento uniforme:Assegura uma sinterização consistente em todo o revestimento, reduzindo o risco de pontos fracos.
- Eficiência energética:Os fornos de indução são altamente eficientes, com uma potência de saída efectiva superior a 95%.
- Automatização e controlo:Os sistemas de controlo avançados permitem uma regulação precisa das taxas de aquecimento, temperaturas e tempos de espera.
- Durabilidade:Os fornos de indução são concebidos para um funcionamento contínuo de 24 horas, o que os torna ideais para processos de sinterização industrial.
-
Parâmetros-chave do processo:
- Controlo da temperatura:A regulação exacta das taxas de aquecimento e dos tempos de espera é fundamental para obter as propriedades de revestimento desejadas.
- Composição do material:A composição química do material refratário, especialmente os elementos com elevada afinidade com o oxigénio, deve ser cuidadosamente gerida.
- Propriedades físicas:Factores como o ponto de fusão, a molhabilidade e a tensão superficial influenciam o processo de sinterização.
- Pureza e fluidez:Assegurar a pureza e a fluidez do material fundido durante a sinterização melhora o desempenho do revestimento.
-
Considerações práticas para a sinterização em fornos de indução:
- Conceção do forno:O forno deve estar equipado com um indutor, uma fonte de alimentação e um sistema de controlo de alta qualidade para apoiar o processo de sinterização.
- Materiais de revestimento:A escolha dos materiais refractários e a sua compatibilidade com o processo de sinterização é crucial.
- Manutenção:A inspeção e manutenção regulares do revestimento do forno são necessárias para garantir um desempenho a longo prazo.
Ao compreender estes pontos-chave, os compradores de equipamentos e consumíveis podem tomar decisões informadas sobre o processo de sinterização em fornos de indução, garantindo um desempenho ótimo e a longevidade do revestimento do forno.
Tabela de resumo:
Aspeto | Detalhes |
---|---|
Definição | Compactação e ligação de partículas de pó utilizando calor abaixo do ponto de fusão. |
Fases principais | Cozedura (600°C), Semi-Sinterização (900°C-1200°C), Sinterização completa. |
Importância | Aumenta a durabilidade do revestimento, a resistência ao choque térmico e o tempo de vida útil do forno. |
Vantagens | Aquecimento uniforme, eficiência energética, controlo preciso e durabilidade. |
Parâmetros-chave | Controlo da temperatura, composição do material, propriedades físicas, pureza. |
Considerações práticas | Conceção do forno, materiais de revestimento e manutenção regular. |
Pronto para otimizar o seu processo de sinterização? Contacte hoje os nossos especialistas para soluções à medida!