As peças metálicas sinterizadas são fabricadas através de uma série de etapas bem definidas que transformam metais em pó em componentes sólidos e duradouros.O processo envolve normalmente a preparação do pó, a compactação e a sinterização, seguidas de etapas opcionais de pós-tratamento para melhorar as propriedades do produto final.Selecionando cuidadosamente os pós metálicos, aplicando técnicas de compactação precisas e controlando o ambiente de sinterização, os fabricantes podem produzir peças com propriedades mecânicas, térmicas e químicas específicas.Este método é amplamente utilizado em indústrias como a automóvel, a aeroespacial e a eletrónica, devido à sua capacidade de criar formas complexas com elevada precisão e eficiência material.
Pontos-chave explicados:
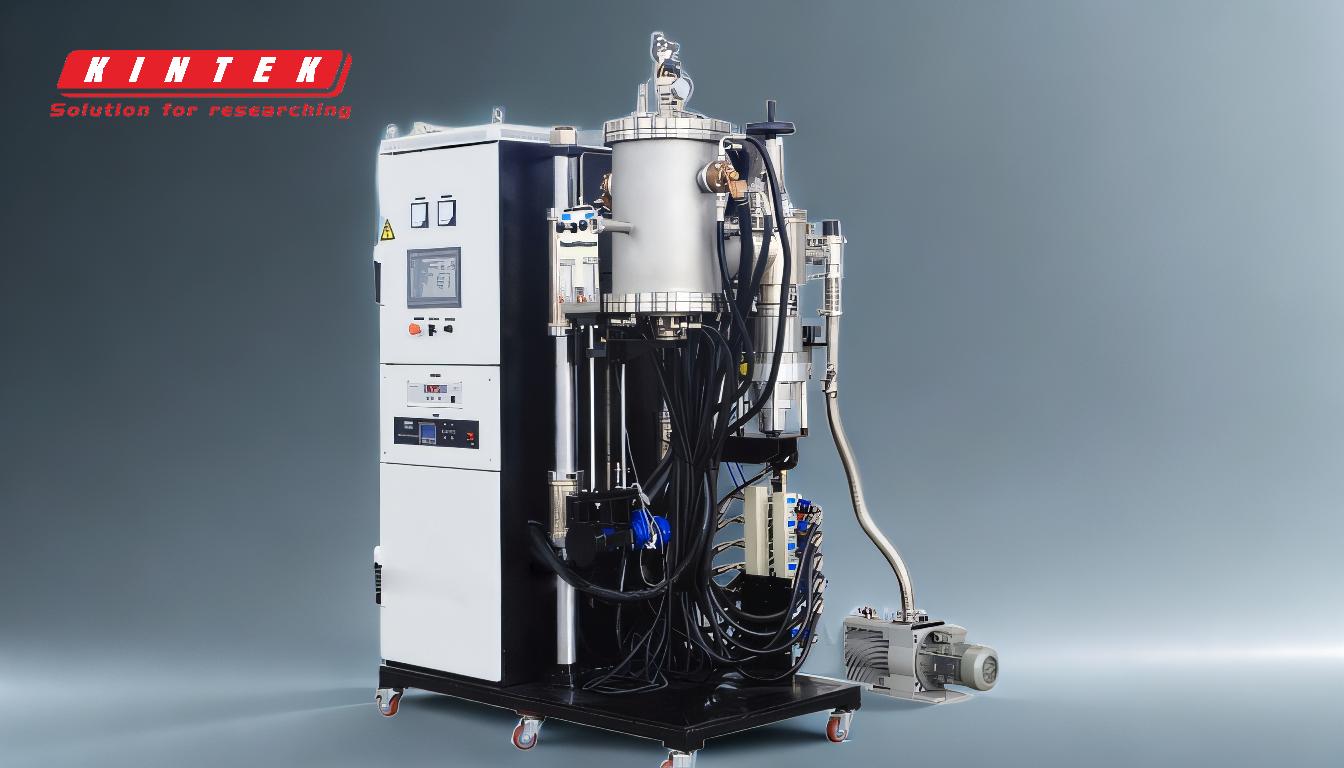
-
Preparação do pó
- Objetivo:A primeira etapa consiste em criar ou selecionar a composição adequada do pó metálico, que determina as propriedades finais da peça sinterizada.
- Processo:Os pós metálicos, como o ferro, o níquel, o molibdénio ou o cobre, são frequentemente misturados com elementos de liga, lubrificantes ou aditivos para obter as caraterísticas desejadas, como a força, a dureza ou a resistência à corrosão.
- Considerações:O tamanho, a forma e a distribuição das partículas do pó são fundamentais, uma vez que influenciam o comportamento de compactação e sinterização.
-
Mistura e combinação
- Objetivo:Garante a uniformidade da mistura de pós, o que é essencial para propriedades consistentes das peças.
- Processo:Os pós são misturados com aditivos como lubrificantes (por exemplo, cera ou ácido esteárico) para melhorar a fluidez e reduzir o atrito durante a compactação.
- Considerações:Uma mistura correta evita a segregação das partículas e assegura uma distribuição uniforme dos elementos de liga.
-
Compactação
- Objetivo:Converte o pó solto numa peça \"verde\" com uma forma específica e uma resistência inicial.
- Processo:O pó é pressionado numa matriz ou molde sob alta pressão (normalmente 20-50 toneladas por polegada quadrada) para formar uma forma coerente.
- Considerações:A força de compactação deve ser cuidadosamente controlada para evitar defeitos como fissuras ou densidade irregular.Os lubrificantes são frequentemente utilizados para facilitar a ejeção da matriz.
-
Sinterização
- Objetivo:Une as partículas para criar uma peça sólida e durável com propriedades mecânicas óptimas.
- Processo:A parte verde é aquecida numa atmosfera controlada (por exemplo, hidrogénio, azoto ou vácuo) a uma temperatura imediatamente inferior ao ponto de fusão do metal.Isto faz com que as partículas se liguem por difusão, reduzindo a porosidade e aumentando a resistência.
- Considerações:A temperatura, o tempo e a atmosfera de sinterização devem ser controlados com precisão para atingir a densidade, a dureza e a microestrutura desejadas.
-
Pós-tratamento
- Objetivo:Melhora as propriedades da peça sinterizada para satisfazer os requisitos específicos da aplicação.
-
Processo:As etapas comuns de pós-tratamento incluem:
- Maquinação:Maquinação de precisão com ferramentas de diamante ou ultra-sons para obter tolerâncias apertadas.
- Tratamento térmico:Processos como a têmpera e o revenido para melhorar a dureza e a resistência.
- Tratamento de superfície:Revestimentos ou chapeamento para aumentar a resistência ao desgaste ou à corrosão.
- Montagem:União de peças sinterizadas com outros componentes através de brasagem ou metalização.
- Considerações:As etapas de pós-tratamento são adaptadas à utilização prevista da peça, garantindo que esta cumpre as normas de desempenho.
-
Vantagens das peças metálicas sinterizadas
- Eficiência do material:Desperdício mínimo em comparação com a maquinagem tradicional.
- Formas complexas:Capacidade de produzir geometrias complexas que são difíceis ou impossíveis de obter com outros métodos.
- Custo-efetividade:Custos de produção mais baixos para o fabrico de grandes volumes.
- Personalização:Propriedades personalizadas do material através do controlo preciso da composição do pó e dos parâmetros de processamento.
Seguindo estes passos, os fabricantes podem produzir peças metálicas sinterizadas com uma precisão, durabilidade e desempenho excepcionais, tornando-as ideais para uma vasta gama de aplicações industriais.
Tabela de resumo:
Etapa | Objetivo | Considerações chave |
---|---|---|
Preparação do pó | Selecionar a composição do pó metálico para as propriedades desejadas | O tamanho, a forma e a distribuição das partículas influenciam a compactação e a sinterização. |
Mistura e combinação | Assegurar a uniformidade da mistura de pós para obter propriedades consistentes das peças | A mistura correta evita a segregação e assegura uma distribuição uniforme dos aditivos. |
Compactação | Converter o pó solto numa forma coerente com resistência inicial | Controlo da força de compactação para evitar defeitos como fissuras ou densidade irregular. |
Sinterização | Unir partículas para criar uma peça sólida e durável com propriedades óptimas | O controlo preciso da temperatura, do tempo e da atmosfera é fundamental. |
Pós-tratamento | Melhorar as propriedades para satisfazer os requisitos específicos da aplicação | Inclui maquinagem, tratamento térmico, tratamento de superfície e montagem. |
Precisa de peças metálicas sinterizadas personalizadas para a sua indústria? Contacte-nos hoje para obter soluções especializadas!