O método de pulverização catódica é uma técnica de deposição física de vapor (PVD) utilizada para depositar películas finas em substratos. Envolve o bombardeamento de um material alvo com iões de alta energia, fazendo com que os átomos sejam ejectados da superfície do alvo. Estes átomos ejectados viajam então através de uma câmara de vácuo e depositam-se num substrato, formando uma película fina. O processo é altamente preciso e é amplamente utilizado em indústrias como a dos semicondutores, da ótica e dos revestimentos. As etapas principais incluem a geração de iões, o bombardeamento do alvo, a ejeção de átomos, o transporte através de vácuo e a deposição no substrato. A pulverização catódica é favorecida pela sua capacidade de produzir películas uniformes e de alta qualidade, mesmo em materiais sensíveis ao calor.
Pontos-chave explicados:
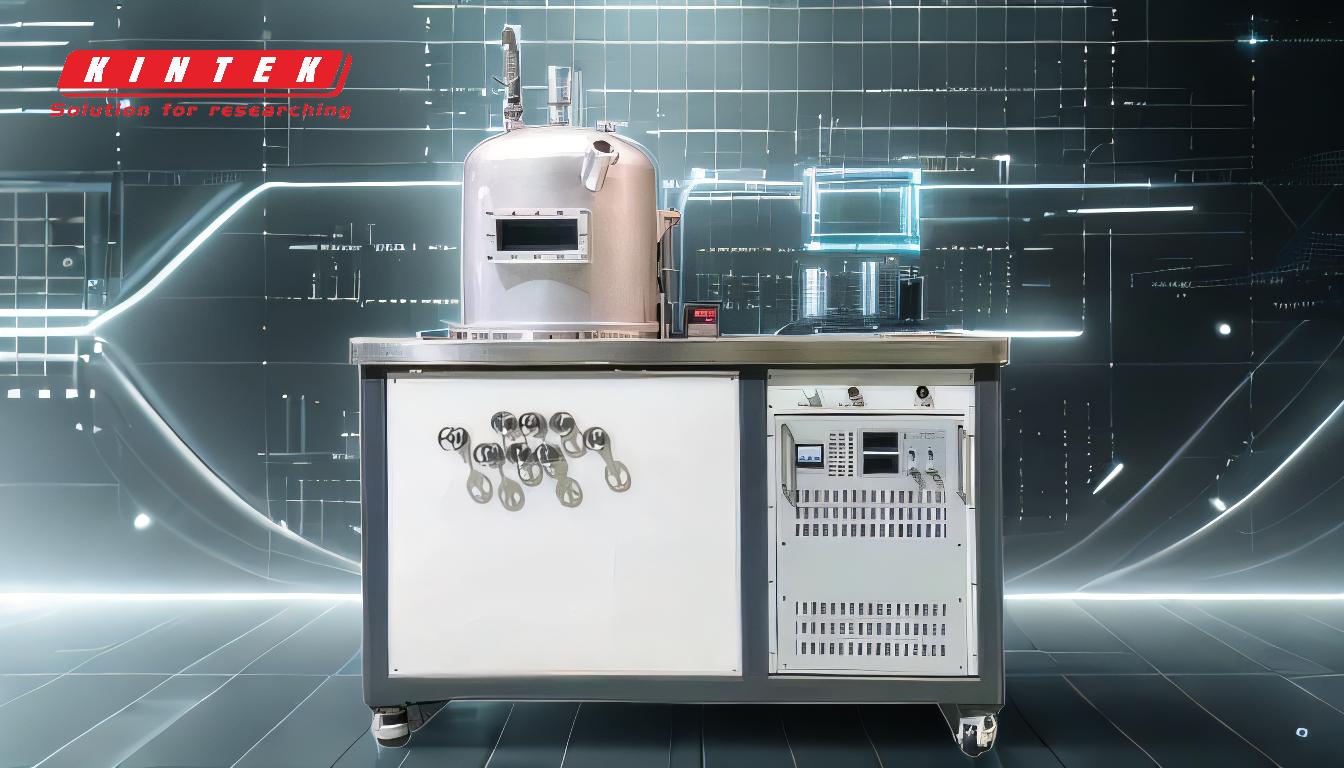
-
Geração e aceleração de iões:
- No processo de pulverização catódica, os iões são gerados através da ionização de um gás de pulverização catódica, normalmente um gás inerte como o árgon ou o xénon. Esta ionização ocorre num plasma criado dentro de uma câmara de vácuo.
- É aplicada uma tensão entre o alvo (cátodo) e o substrato (ânodo), acelerando os iões de carga positiva em direção ao material alvo.
-
Bombardeamento de alvos:
- Os iões acelerados atingem o material alvo com elevada energia cinética. Esta transferência de energia faz com que os átomos ou moléculas perto da superfície do alvo ganhem energia suficiente para escapar da superfície.
- O processo de ejeção de átomos do material alvo é conhecido como "pulverização catódica"
-
Ejeção e transporte de átomos:
- Os átomos ou moléculas ejectados do material alvo formam um fluxo de vapor. Estas partículas viajam através da câmara de vácuo em direção ao substrato.
- O ambiente de vácuo é crucial, pois evita interações com o ar ou outros gases indesejáveis, garantindo a pureza e a qualidade da película depositada.
-
Deposição no substrato:
- Os átomos pulverizados condensam-se no substrato, formando uma película fina. O substrato é normalmente montado em frente ao alvo dentro da câmara de vácuo.
- A baixa temperatura das partículas pulverizadas permite que mesmo os substratos sensíveis ao calor, como os plásticos, sejam revestidos sem danos.
-
Vantagens da pulverização catódica:
- Precisão e uniformidade: A pulverização catódica produz películas finas altamente uniformes e precisas, o que a torna ideal para aplicações que exigem elevada precisão, como o fabrico de semicondutores.
- Versatilidade: Pode depositar uma vasta gama de materiais, incluindo metais, ligas e cerâmicas, em vários substratos.
- Baixa temperatura: O processo pode ser efectuado a temperaturas relativamente baixas, permitindo o revestimento de materiais sensíveis ao calor.
-
Aplicações de Sputtering:
- Semicondutores: Utilizado para depositar películas finas em circuitos integrados e outros componentes electrónicos.
- Ótica: Aplicado na produção de revestimentos antirreflexo, espelhos e filtros ópticos.
- Revestimentos: Utilizado para revestimentos resistentes ao desgaste, resistentes à corrosão e decorativos em vários materiais.
Ao compreender estes pontos-chave, é possível apreciar a eficiência e a versatilidade do método de pulverização catódica na produção de películas finas de alta qualidade para uma vasta gama de aplicações.
Quadro de resumo:
Principais etapas | Descrição |
---|---|
Geração de iões | Os iões são gerados pela ionização de gases inertes, como o árgon, num plasma. |
Bombardeamento de alvos | Os iões de alta energia atingem o alvo, ejectando átomos da sua superfície. |
Ejeção de átomos | Os átomos ejectados formam um fluxo de vapor e viajam através de uma câmara de vácuo. |
Deposição | Os átomos condensam-se no substrato, formando uma película fina. |
Vantagens | Precisão, uniformidade, versatilidade e processamento a baixa temperatura. |
Aplicações | Semicondutores, ótica, revestimentos resistentes ao desgaste e muito mais. |
Descubra como a pulverização catódica pode melhorar os seus processos de película fina- contacte os nossos especialistas hoje mesmo !