Introdução aos fornos de sinterização por plasma de faísca (SPS)
Os fornos de sinterização por plasma de faísca (SPS) representam uma tecnologia de vanguarda no domínio da ciência dos materiais, oferecendo uma abordagem única à sinterização através da utilização de corrente de impulsos DC on-off para a geração de plasma. Este guia abrangente investiga os meandros da tecnologia SPS, explorando os seus componentes, tais como o dispositivo de pressão axial, o elétrodo de punção arrefecido a água e a câmara de vácuo. Ao compreender as principais caraterísticas e aplicações versáteis da SPS, podemos apreciar a forma como esta tecnologia revoluciona a sinterização rápida, eficiente e de alta qualidade de vários materiais, desde metais e cerâmicas a nanomateriais e compósitos.
Principais caraterísticas dos fornos de sinterização por plasma de faísca
Os fornos Spark Plasma Sintering (SPS) revolucionaram o campo da ciência dos materiais com as suas capacidades únicas e tempos de processamento rápidos. Estes fornos utilizam uma corrente contínua de alta pulsação para aquecer e sinterizar compactos de pó, oferecendo várias vantagens distintas em relação aos métodos de sinterização tradicionais. Aqui, aprofundamos as principais caraterísticas dos fornos SPS, incluindo a sinterização rápida, a sinterização por purificação e ativação, a sinterização de grão fino, a sinterização a uma temperatura de grande amplitude, a sinterização com controlo da densidade e a sinterização com gradiente de temperatura.
Sinterização rápida
Uma das vantagens mais significativas dos fornos SPS é a sua capacidade de obter uma sinterização rápida. A taxa de aquecimento pode exceder os 500°C/min, o que é significativamente mais rápido do que os métodos tradicionais, como a prensagem a quente, a prensagem isostática a quente (HIP) e a sinterização sem pressão. Esta taxa de aquecimento rápido permite tempos de sinterização muito mais curtos, reduzindo frequentemente o processo de horas para meros minutos. As taxas de aquecimento e arrefecimento rápidas também minimizam os processos de engrossamento e ajudam a manter as nanoestruturas intrínsecas do material após a densificação total.
Sinterização de purificação e ativação
Os fornos SPS oferecem um processo único de sinterização por purificação e ativação. A elevada corrente DC pulsada induz um efeito de purificação da superfície das partículas, que remove os gases adsorvidos e as películas de óxido. Este processo de purificação, combinado com o efeito de ativação da superfície das partículas, permite a sinterização de materiais que são tradicionalmente difíceis de sinterizar. Esta caraterística é particularmente benéfica para materiais com elevados requisitos de pureza ou sensíveis a contaminantes de superfície.
Sinterização de grão fino
O rápido aumento da temperatura nos fornos SPS inibe o crescimento do grão, permitindo a regulação da microestrutura e a preparação de corpos sinterizados de grão fino. Esta caraterística faz da SPS um excelente método para a preparação de materiais nanocristalinos. Ao controlar os parâmetros de sinterização, os investigadores podem obter o tamanho de grão e a microestrutura desejados, o que é crucial para otimizar as propriedades mecânicas, eléctricas e térmicas do material.
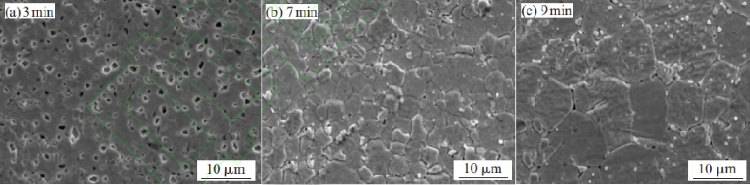
Sinterização a uma ampla gama de temperaturas
Os fornos SPS podem funcionar numa vasta gama de temperaturas, desde temperaturas baixas até 2300°C. Esta ampla gama de temperaturas torna os fornos SPS versáteis para a sinterização de uma variedade de materiais, incluindo cerâmicas, metais e compósitos. A capacidade de atingir altas temperaturas de forma rápida e eficiente é particularmente útil para materiais que requerem um processamento a alta temperatura para atingir uma densificação total e propriedades óptimas.
Sinterização com controlo de densidade
Outra caraterística notável dos fornos SPS é a sua capacidade de controlar a densidade do corpo sinterizado. Desde corpos porosos a corpos sinterizados totalmente densos, os fornos SPS oferecem um controlo flexível da densidade. Isto é conseguido através do ajuste dos parâmetros de sinterização, tais como a força aplicada, o curso do pistão e a corrente. O controlo preciso da densidade é essencial para adaptar as propriedades do material a aplicações específicas, como nas indústrias aeroespacial, automóvel e médica.
Sinterização por gradiente de temperatura
Os fornos SPS podem criar um gradiente de temperatura dentro do molde, permitindo a sinterização simultânea de materiais com diferentes pontos de fusão. Esta caraterística é particularmente útil para a preparação de materiais funcionalmente graduados (FGMs), onde diferentes camadas ou regiões do material requerem diferentes condições de processamento. A capacidade de criar um gradiente de temperatura (centenas de °C/mm) no interior do molde permite a produção de materiais complexos, com várias camadas, com propriedades e funcionalidades adaptadas.
Em conclusão, os fornos SPS oferecem uma gama de caraterísticas avançadas que os tornam uma ferramenta poderosa no domínio da ciência dos materiais. A sua capacidade para obter sinterização rápida, sinterização por purificação e ativação, sinterização de grão fino, sinterização a uma temperatura de grande amplitude, sinterização com controlo da densidade e sinterização com gradiente de temperatura torna-os versáteis e eficientes para uma vasta gama de aplicações. À medida que a investigação e o desenvolvimento neste domínio continuam a avançar, os fornos SPS estão preparados para desempenhar um papel cada vez mais importante na produção de materiais de elevado desempenho.
Versatilidade no processamento de materiais com SPS
A sinterização por plasma de faísca (SPS) é uma técnica altamente eficiente e versátil utilizada na sinterização de uma vasta gama de materiais, incluindo metais, cerâmicas, nanomateriais e materiais compósitos. Este método utiliza impulsos de corrente direta para gerar um plasma de faíscas entre as partículas, facilitando o aquecimento rápido e os processos de densificação. A SPS é conhecida pela sua capacidade de obter uma preparação de materiais de alta qualidade com vantagens significativas em relação aos métodos de sinterização tradicionais.
Ampla aplicabilidade da SPS
Nanomateriais
A tecnologia SPS é particularmente eficaz na preparação de nanomateriais. Os métodos tradicionais de sinterização têm muitas vezes dificuldade em manter o tamanho do grão à escala nanométrica e em atingir uma densidade completa. A SPS, com o seu aquecimento rápido e tempos de síntese curtos, suprime eficazmente o engrossamento do grão. Este processo rápido também permite a retenção de defeitos e subestruturas no pó, o que pode ser benéfico para a síntese de materiais metaestáveis e nanomateriais.
Materiais funcionais de gradiente
Os Materiais Funcionais Gradientes (FGMs) são compósitos com uma distribuição gradiente numa determinada direção, exigindo frequentemente temperaturas de sinterização diferentes para cada camada. Os métodos tradicionais como a Deposição Química de Vapor (CVD) e a Deposição Física de Vapor (PVD) são dispendiosos e difíceis de utilizar na produção industrial. A SPS supera estes desafios ao permitir a sinterização de materiais com gradientes de resistência ao calor, resistência ao desgaste, dureza, condutividade e porosidade, com a capacidade de lidar com várias camadas.
Materiais electromagnéticos
A SPS é também utilizada na produção de vários materiais electromagnéticos, incluindo elementos de conversão termoeléctrica e materiais utilizados no campo da eletrónica, tais como materiais supercondutores, materiais magnéticos, materiais dieléctricos, entre outros. Estes materiais são cruciais para aplicações que vão desde o armazenamento de energia à engenharia biomédica.
Compostos intermetálicos
Os compostos intermetálicos, conhecidos pela sua fragilidade e elevados pontos de fusão, requerem processos especializados para a sua preparação. A SPS oferece um método eficiente para a preparação destes compostos, utilizando o auto-aquecimento e a ativação da superfície entre as partículas, permitindo uma sinterização rápida e a baixa temperatura.
Cerâmicas e cermets de alta densidade e granulação fina
O processo SPS encurta significativamente os tempos de sinterização e reduz as temperaturas, aproveitando o calor gerado dentro de cada partícula de pó e os espaços entre elas. Isto faz da SPS um excelente método para preparar cerâmicas e cermets de alta densidade e de grão fino, que são essenciais para várias aplicações industriais.
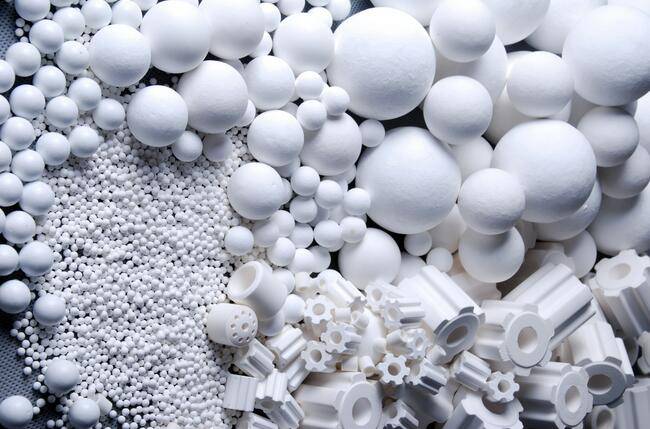
Vantagens da SPS
- Tempos de ciclo mais curtos: A SPS reduz significativamente os ciclos de sinterização de horas ou dias para apenas alguns minutos, aumentando a produtividade e as capacidades de desenvolvimento rápido de materiais.
- Temperaturas de sinterização mais baixas: Permite a sinterização a temperaturas mais baixas em comparação com os processos convencionais, o que é particularmente benéfico para materiais sensíveis ao calor.
- Controlo de processo de alta precisão: O SPS proporciona um controlo preciso dos parâmetros de sinterização, como a temperatura e a pressão, garantindo resultados óptimos e permitindo a criação de produtos químicos únicos que não são possíveis com os métodos convencionais.
- Versatilidade: Pode densificar uma vasta gama de materiais, desde metais de baixo ponto de fusão a cerâmicas de temperatura ultra-alta, e até mesmo unir materiais diferentes que requerem distribuições de temperatura não uniformes.
Aplicações da SPS
A tecnologia SPS encontra aplicações em vários domínios, incluindo:
- Armazenamento de energia: Baterias de iões de lítio de alta capacidade e outros materiais avançados de armazenamento de energia.
- Engenharia biomédica: Cerâmica porosa para administração de medicamentos e andaimes para engenharia de tecidos.
- Cerâmica avançada: Supercondutores de alta temperatura e cerâmicas piezoeléctricas de elevado desempenho.
- Intermetálicos: Ligas avançadas com propriedades mecânicas, térmicas e eléctricas melhoradas.
- Compósitos: Cerâmicas e metais reforçados com propriedades mecânicas melhoradas.
Em conclusão, a sinterização por plasma de faísca destaca-se como um método altamente versátil e eficiente para a sinterização de diversos materiais, oferecendo vantagens significativas em termos de controlo do processo, eficiência energética e capacidade de produzir materiais de alta qualidade para uma vasta gama de aplicações.
Facilidade operacional e caraterísticas de segurança dos fornos SPS
Os fornos Spark Plasma Sintering (SPS) são conhecidos pela sua facilidade operacional avançada e caraterísticas de segurança robustas, o que os torna uma escolha preferida em várias aplicações industriais. Estes fornos são concebidos com foco em interfaces fáceis de utilizar e mecanismos de segurança abrangentes para garantir operações eficientes e seguras.
Design e sistemas de controlo de fácil utilização
Os fornos SPS estão equipados com sistemas de controlo de última geração que aumentam a facilidade operacional. Uma caraterística notável é a integração de interfaces de ecrã tátil e Controladores Lógicos Programáveis (PLCs) para controlo central. Esta configuração permite aos operadores monitorizar e ajustar facilmente os parâmetros do forno, reduzindo a complexidade da operação e minimizando o potencial de erro humano. O sistema PLC Allen-Bradley, por exemplo, é conhecido pela sua facilidade de programação e modificação, o que simplifica ainda mais a gestão das operações do forno.
O armário de controlo destes fornos foi concebido para alojar todos os controlos eléctricos num armário standard NEMA 12, assegurando a conformidade com normas de segurança como a NFPA 70. Este controlo centralizado não só aumenta a segurança, como também torna a manutenção e a resolução de problemas mais simples. A inclusão de um interbloqueio do interrutor elétrico principal integrado acrescenta uma camada extra de segurança ao impedir operações não autorizadas ou acidentais.
Mecanismos de segurança avançados
A segurança é uma preocupação primordial no funcionamento dos fornos SPS, e estes sistemas estão equipados com várias camadas de proteção. As principais caraterísticas de segurança incluem alarmes de avaria por excesso de temperatura e de pressão, que alertam os operadores para potenciais perigos em tempo real. Além disso, existem sistemas mecânicos de proteção automática da pressão para salvaguardar contra problemas relacionados com a pressão, garantindo a integridade do forno e dos materiais processados.
Os fornos também possuem funções de interbloqueio que impedem operações em condições inseguras. Por exemplo, os encravamentos são utilizados para desativar o forno em caso de falta de eletricidade ou água, pressão insuficiente ou condições de temperatura excessiva. Estes encravamentos são cruciais para evitar acidentes e proteger tanto o equipamento como os operadores.
As capacidades de controlo remoto são outra caraterística de segurança significativa, permitindo o diagnóstico remoto de avarias e actualizações de programas. Isto não só aumenta a eficiência da manutenção, como também reduz o risco de exposição dos técnicos a condições perigosas.
Integração de termopares
O controlo preciso da temperatura é essencial nos processos de sinterização e os fornos SPS utilizam termopares de alta qualidade, como os do Tipo "S" e do Tipo "K", para uma monitorização e controlo precisos da temperatura. Estes termopares estão integrados em painéis de tomadas apropriados para monitorização e controlo do trabalho, assegurando que o processo de sinterização se mantém dentro de intervalos de temperatura seguros e ideais.
Conclusão
Em suma, a facilidade operacional e as caraterísticas de segurança dos fornos SPS foram concebidas para proporcionar uma experiência de sinterização perfeita e segura. Com sistemas de controlo fáceis de utilizar, mecanismos de segurança avançados e controlo preciso da temperatura, estes fornos são ideais para uma vasta gama de aplicações no processamento de metais, cerâmicas, nanomateriais e muito mais. A integração de tecnologia moderna e protocolos de segurança robustos garante que os operadores possam trabalhar de forma eficiente, minimizando os riscos.
Sistemas avançados de controlo e monitorização em SPS
Os sistemas avançados de controlo e monitorização são parte integrante do processo de sinterização por plasma de faísca (SPS), permitindo uma regulação precisa da temperatura, pressão e corrente, juntamente com uma aquisição de dados abrangente para acompanhar e analisar os parâmetros de sinterização. Estes sistemas são cruciais para garantir a qualidade e a reprodutibilidade dos materiais sinterizados.
Controlo automatizado do programa
O processo SPS começa com o carregamento de uma quantidade conhecida de amostra de pó seco e moído numa matriz cilíndrica revestida com uma folha de grafite, o que facilita a remoção do compacto sinterizado. O molde é então colocado no interior da câmara SPS e é definido o perfil específico de tempo-temperatura necessário para a experiência. A atmosfera no interior da câmara é mantida conforme necessário, seja vácuo, árgon ou outros ambientes controlados. A potência é definida para o máximo no modo Auto e a carga necessária é aplicada à matriz. A posição do eixo z é definida para zero e o temporizador é ativado antes de premir SINTER para iniciar o processo de sinterização.
Para a medição da temperatura, a SPS utiliza dois tipos de instrumentos: termopares para temperaturas de sinterização inferiores a 1000°C e pirómetros para temperaturas superiores a 1000°C. Entre os eléctrodos de grafite, passa um impulso DC elevado e, simultaneamente, é aplicada uma pressão axial desde o início do ciclo de sinterização. A amostra é aquecida por aquecimento Joule e por faíscas entre as partículas, levando a uma transferência instantânea mais rápida de calor e massa. Após a sinterização, a energia é desligada e a amostra é deixada arrefecer.
Sistemas de controlo computorizados
O sistema de controlo em SPS é tipicamente computorizado, apresentando um sistema automático de controlo por computador de ecrã plano PLC que permite a mudança manual para modos automáticos. O software do sistema de controlo é desenvolvido internamente, oferecendo uma interface de fácil utilização com monitorização em tempo real das condições do forno. O sistema é estável e fiável, com uma resposta rápida e fortes capacidades anti-interferência. O software apresenta um ecrã de simulação a cores, integrando a indicação da temperatura e o controlo da válvula de vácuo para uma operação intuitiva.
O dispositivo pode adotar várias curvas para análise, tais como curvas de temperatura, potência, vácuo, temperatura da água, pressão do ar e tempo de sinterização. Estas curvas proporcionam uma forma fácil de analisar o processo de sinterização com base em dados históricos. O sistema pode gerar automaticamente ficheiros Excel através da interface USB para análise posterior.
O método de controlo da temperatura utiliza um termopar para temperaturas até 1700°C, com instrumentos de infravermelhos para temperaturas superiores a 1700°C. O sistema suporta várias interfaces de comunicação como RS232, RS422, CAN, LAN e USB, facilitando a ligação em rede com outros equipamentos. A interface de controlo do software é visualizada, apresentando dinamicamente o fluxo de trabalho para maior comodidade e intuitividade. A atualização do software é gratuita para toda a vida.
Controladores e aquisição de dados
Tal como outras câmaras de teste, a SPS oferece várias opções de controladores, desde sistemas completamente manuais a sistemas totalmente automatizados. Os controladores automatizados permitem que os utilizadores definam os parâmetros do processo e, à medida que o procedimento se desenrola, o sistema faz ajustes na pressão, temperatura e outros factores programados. Estes sistemas de controlo são configuráveis com software personalizável e uma variedade de métodos de recolha de dados. A escolha do controlador é determinada pela criticidade da aplicação e pelo tamanho da câmara de vácuo. As câmaras mais pequenas podem necessitar apenas de um simples manómetro para monitorizar o bombeamento e a pressão, enquanto as câmaras maiores podem exigir um sistema mais agressivo e sofisticado.
Componentes da máquina de sinterização
A máquina SPS é assistida por vários componentes, incluindo uma prensa uniaxial, eléctrodos de punção, câmara de vácuo, atmosfera controlada, gerador de impulsos DC e unidades de medição de posição, temperatura e pressão. O controlo da temperatura de sinterização é conseguido através da definição de parâmetros como o tempo de espera, a taxa de rampa, a duração do impulso e a corrente e tensão do impulso. A descarga de impulsos DC gera plasma de faísca, pressão de impacto de faísca, aquecimento Joule e um efeito de difusão de campo elétrico. Na SPS, a sinterização é assistida pela tensão de impulsos de corrente contínua on-off, o que é diferente da prensagem a quente convencional. A aplicação de pressão ajuda o fluxo plástico do material, e o fluxo de corrente de impulsos DC através das partículas é ilustrado em diagramas detalhados.
Em conclusão, os sistemas avançados de controlo e monitorização em SPS são essenciais para alcançar resultados de sinterização precisos e reprodutíveis. Estes sistemas permitem ajustes em tempo real e a aquisição de dados abrangentes, garantindo a qualidade e a consistência dos materiais sinterizados. Com a integração de controlo computorizado, software personalizável e métodos avançados de recolha de dados, a tecnologia SPS continua a ultrapassar os limites da ciência e engenharia de materiais.
Aplicações da sinterização por plasma de faísca na ciência dos materiais
A Spark Plasma Sintering (SPS) é uma técnica de sinterização versátil e avançada que revolucionou o campo da ciência dos materiais. Ao combinar pressão uniaxial, corrente contínua pulsada e aquecimento rápido, a SPS permite a síntese de uma vasta gama de materiais com propriedades e estruturas únicas. Esta secção aprofunda as aplicações multifacetadas da SPS, incluindo sinterização, união, formação, modificação de superfícies e síntese de materiais como electrólitos sólidos e materiais térmicos eléctricos.
Sinterização de materiais avançados
A SPS é particularmente conhecida pela sua capacidade de sinterizar materiais de elevado ponto de fusão e nanomateriais de forma eficiente. As rápidas taxas de aquecimento (até 1000°C/min) e os curtos tempos de processamento inerentes à SPS ajudam a manter a nanoestrutura dos pós, evitando o crescimento de grãos e preservando as propriedades inerentes às partículas de tamanho nanométrico. Isto faz da SPS um método ideal para produzir cerâmicas e cermets de alta densidade e de grão fino. Por exemplo, o nitreto de titânio, um material conhecido pelas suas fracas propriedades de sinterização e fragilidade, pode ser densificado a níveis elevados utilizando a SPS, atingindo densidades próximas dos valores teóricos sob pressões de 1-5 GPa.
União e conformação
Para além da sinterização, a SPS é também utilizada para unir materiais diferentes e formar formas complexas. A corrente contínua aplicada durante o processo não só aquece o material como também melhora a ligação por difusão entre as partículas, facilitando a união de materiais que são tradicionalmente difíceis de unir, tais como cerâmicas e metais. Esta capacidade é particularmente útil nas indústrias aeroespacial e automóvel, onde a procura de compósitos leves e de alta resistência é elevada.
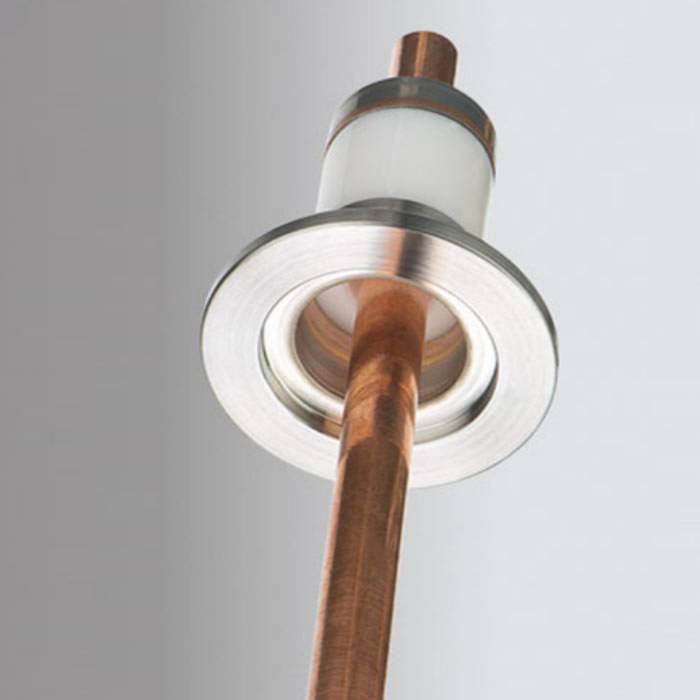
Modificação da superfície
A SPS também pode ser utilizada para modificação da superfície, melhorando as propriedades da superfície dos materiais sem afetar as suas caraterísticas gerais. Ao controlar a densidade da corrente e a pressão, podem ser adaptadas camadas superficiais específicas para obter as propriedades desejadas, como maior dureza, resistência ao desgaste ou resistência à corrosão. Esta aplicação é particularmente benéfica para materiais de ferramentas e componentes expostos a ambientes agressivos.
Síntese de materiais funcionais
Uma das aplicações mais significativas da SPS é a síntese de materiais funcionais, incluindo electrólitos sólidos e materiais térmicos eléctricos. Os electrólitos sólidos, cruciais para aplicações em baterias de estado sólido e células de combustível, requerem um elevado grau de densificação e pureza. A SPS facilita a síntese destes materiais com um mínimo de segregação nos limites do grão e uma excelente condutividade iónica. Do mesmo modo, os materiais térmicos eléctricos, utilizados em várias aplicações de aquecimento, podem ser sintetizados com condutividade térmica e resistividade eléctrica controladas através de parâmetros precisos de processamento SPS.
Importância industrial e perspectivas futuras
A importância industrial da SPS reside na sua capacidade de produzir materiais de elevado desempenho com um consumo de energia reduzido e tempos de processamento mais curtos. A tecnologia é particularmente adequada para a produção de nanomateriais, ligas amorfas a granel e materiais funcionais gradientes, que são difíceis de sintetizar utilizando métodos tradicionais. À medida que a investigação continua a descobrir novas aplicações e a otimizar os parâmetros de processamento, a SPS está preparada para desempenhar um papel crucial no futuro da ciência dos materiais, impulsionando os avanços em várias indústrias de alta tecnologia.
Em conclusão, a sinterização por plasma de faísca destaca-se como uma tecnologia transformadora na ciência dos materiais, oferecendo um vasto espetro de aplicações, desde a sinterização e união até à modificação da superfície e à síntese de materiais funcionais avançados. A sua capacidade de processar materiais com elevada eficiência e precisão torna-a uma ferramenta indispensável tanto para investigadores como para profissionais da indústria.
Desafios e considerações na utilização da tecnologia SPS
A tecnologia Spark Plasma Sintering (SPS) revolucionou o campo da ciência dos materiais ao permitir a síntese de materiais avançados com propriedades únicas. No entanto, a implementação da SPS tem o seu próprio conjunto de desafios e considerações que devem ser abordados para obter resultados de sinterização óptimos. Esta secção analisa os aspectos críticos da seleção e manutenção de moldes, bem como as considerações mais amplas para operações SPS eficazes.
Seleção e manutenção do molde
A escolha do material do molde é um fator essencial na tecnologia SPS. Tradicionalmente, a grafite tem sido o material preferido devido à sua resistência a altas temperaturas, excelente condutividade eléctrica e térmica e estabilidade química. No entanto, os moldes de grafite têm limitações, tais como baixa resistência mecânica, vida útil curta e potencial contaminação dos materiais sinterizados. Estas questões exigem a exploração de materiais de molde alternativos.
Avanços recentes levaram ao desenvolvimento de materiais de molde alternativos, como o carboneto cimentado, a cerâmica condutora e a fibra de carbono grafite. Cada um destes materiais oferece vantagens únicas, mas também apresenta desafios. Por exemplo, os moldes de carboneto cimentado oferecem maior resistência, mas podem ser propensos a deformações a altas temperaturas. As cerâmicas condutoras oferecem um equilíbrio de propriedades, mas são frequentemente caras. Os moldes de grafite com fibra de carbono combinam as vantagens da grafite com propriedades mecânicas melhoradas, mas requerem um manuseamento cuidadoso para evitar danos.
A manutenção da integridade do molde é crucial para resultados consistentes de sinterização. A inspeção regular e a substituição de moldes desgastados são essenciais para evitar inconsistências no processo de sinterização. Além disso, a limpeza e o condicionamento adequados dos moldes entre utilizações podem prolongar a sua vida útil e manter a qualidade dos materiais sinterizados.
Obtenção de resultados óptimos de sinterização
Para obter resultados óptimos de sinterização, devem ser tidas em conta várias considerações. Estas incluem a seleção de parâmetros de sinterização adequados, o controlo do ambiente de sinterização e a compreensão do mecanismo de sinterização.
Parâmetros de sinterização
Os parâmetros de sinterização, tais como a temperatura, a pressão e o tempo de permanência, desempenham um papel crítico na determinação das propriedades finais do material sinterizado. As taxas de aquecimento e arrefecimento rápidas que se podem obter com a SPS podem conduzir a microestruturas fora do equilíbrio, o que pode ser vantajoso para a obtenção de propriedades materiais únicas. No entanto, estas taxas devem ser cuidadosamente controladas para evitar o crescimento excessivo de grão ou outros defeitos.
Ambiente de sinterização
O ambiente de sinterização, incluindo a atmosfera e os gradientes de temperatura, pode influenciar significativamente o processo de sinterização. O controlo da atmosfera pode evitar a oxidação e outras reacções químicas que podem degradar o material. Os gradientes de temperatura dentro do molde podem levar a uma densificação não uniforme, o que exige uma conceção e otimização cuidadosas da configuração da sinterização.
Compreender o mecanismo de sinterização
O mecanismo de sinterização em SPS envolve a geração de um plasma de faísca entre as partículas, o que facilita o rápido aquecimento e a densificação. No entanto, os mecanismos exactos que regem este processo ainda não são totalmente compreendidos e são objeto de investigação contínua. As simulações de elementos finitos surgiram como uma ferramenta valiosa para estudar o processo de sinterização, fornecendo informações sobre as distribuições de temperatura e de campo elétrico no interior do material.
Direcções futuras
A melhoria contínua da tecnologia SPS requer investigação e desenvolvimento contínuos. As áreas-chave para exploração futura incluem o desenvolvimento de novos materiais de molde com propriedades melhoradas, a otimização dos parâmetros de sinterização através de técnicas de simulação avançadas e uma compreensão mais profunda do mecanismo de sinterização.
Em conclusão, embora a tecnologia SPS ofereça vantagens significativas para a síntese de materiais avançados, também apresenta vários desafios e considerações que devem ser abordados para alcançar resultados óptimos. Selecionando e mantendo cuidadosamente os moldes, controlando os parâmetros de sinterização e avançando na nossa compreensão do mecanismo de sinterização, podemos continuar a alargar os limites do que é possível com a tecnologia SPS.
Tendências futuras e inovações na tecnologia SPS
A tecnologia Spark Plasma Sintering (SPS), conhecida pelas suas capacidades de sinterização rápida, tem sido um ponto focal no campo da ciência dos materiais devido à sua capacidade de produzir materiais de alta qualidade com propriedades únicas. À medida que a investigação continua a evoluir, estão a surgir várias tendências e inovações que prometem aumentar a eficiência, alargar as aplicações e melhorar a segurança da tecnologia SPS.
Industrialização e produção em massa
Uma das tendências mais significativas na tecnologia SPS é a sua transição para a industrialização. Em comparação com os métodos de sinterização tradicionais, a SPS oferece vantagens substanciais em termos de poupança de energia e tempo, maior eficiência de produção e controlo superior do desempenho do produto. Países como o Japão já conseguiram aplicações industriais de SPS, principalmente na produção de materiais magnéticos, ligas duras e materiais funcionais gradientes. Por exemplo, a Ohta Seiki no Japão implementou com sucesso a produção em massa de materiais superduros 100% WC utilizando SPS, fornecendo a mais de 40 fabricantes a nível mundial. Em contrapartida, a tecnologia SPS noutras regiões, como a China, permanece em grande parte na fase de investigação laboratorial, centrando-se na preparação e investigação de processos de novos materiais.
Diversificação das formas sinterizadas
Atualmente, a SPS está limitada à produção de amostras cilíndricas simples devido às restrições do mecanismo de sinterização e dos moldes de grafite. No entanto, existe uma tendência crescente para desenvolver a tecnologia SPS para criar formas e estruturas mais complexas. Este avanço expandiria significativamente a aplicabilidade da SPS em vários sectores da engenharia, permitindo a produção de componentes intrincados que são atualmente inatingíveis.
Síntese e ligação de materiais
A tecnologia SPS não é apenas utilizada para sinterizar materiais a granel, mas também para a síntese de pós, particularmente aqueles que são difíceis de obter através de métodos convencionais. Por exemplo, a SPS tem sido utilizada para sintetizar pó de material ZrC de temperatura ultra-alta, alcançando alta pureza e um tamanho de grão fino de aproximadamente 100 nm. Além disso, a SPS está a ser explorada para a ligação de materiais (soldadura), incluindo juntas cerâmica-cerâmica e cerâmica-metal. A capacidade de ligar materiais sem uma camada intermédia, através da auto-difusão reforçada pelo campo elétrico da SPS, abre novas possibilidades para a criação de estruturas compostas robustas e duradouras.
Otimização do desempenho dos moldes de sinterização
A grafite, embora seja normalmente utilizada em SPS devido à sua resistência a altas temperaturas e excelente condutividade eléctrica e térmica, tem limitações como a baixa resistência e a potencial contaminação dos materiais sinterizados. Existe uma tendência para o desenvolvimento de novos materiais de molde que ofereçam maior resistência, reutilização e menor contaminação. Materiais como moldes de carboneto cimentado, moldes de cerâmica condutora e moldes de grafite com fibra de carbono estão a ser investigados, embora persistam desafios como a deformação a altas temperaturas e os custos elevados.
Avanços na Simulação e Modelação
Compreender o complexo processo de sinterização em SPS é crucial para otimizar os seus parâmetros e prever os resultados. A simulação de elementos finitos surgiu como uma ferramenta valiosa a este respeito, permitindo aos investigadores analisar as distribuições de temperatura e de campo elétrico durante a sinterização. Software como o ABAQUS, MATLAB e MSC.MARC está a ser utilizado para simular o processo de sinterização, fornecendo informações sobre o impacto de vários parâmetros e ajudando na orientação teórica da produção.
Caraterísticas de segurança melhoradas
À medida que a tecnologia SPS continua a evoluir, há um foco crescente na melhoria das suas caraterísticas de segurança. Isto inclui o desenvolvimento de protocolos de funcionamento mais seguros, a melhoria da fiabilidade do equipamento SPS e a garantia de que a tecnologia pode ser utilizada numa gama mais vasta de ambientes sem comprometer a segurança.
Em conclusão, o futuro datecnologia SPSparece promissor, com investigação e desenvolvimento contínuos destinados a melhorar a eficiência, alargar as aplicações de materiais e melhorar as caraterísticas de segurança. Estes avanços estão preparados para revolucionar o campo da ciência dos materiais, permitindo a produção de materiais e componentes de elevado desempenho que anteriormente eram inatingíveis. À medida que a tecnologia SPS continua a amadurecer, desempenhará, sem dúvida, um papel fundamental na definição do futuro do fabrico e da inovação de materiais.
CONTACTE-NOS PARA UMA CONSULTA GRATUITA
Os produtos e serviços da KINTEK LAB SOLUTION foram reconhecidos por clientes de todo o mundo. A nossa equipa terá todo o prazer em ajudar com qualquer questão que possa ter. Contacte-nos para uma consulta gratuita e fale com um especialista de produto para encontrar a solução mais adequada para as suas necessidades de aplicação!