O processo de sinterização é um método crítico na ciência e fabrico de materiais, utilizado para criar produtos sólidos e duradouros a partir de materiais em pó através de aquecimento e arrefecimento controlados. Envolve várias fases, incluindo a preparação das matérias-primas, a compactação, o aquecimento para facilitar a ligação das partículas e o arrefecimento para solidificar o produto final. Este processo assegura a formação de uma estrutura coesa e de baixa porosidade com propriedades mecânicas melhoradas. Abaixo, os principais passos e fases da sinterização são explicados em pormenor, focando as reacções químicas e as transformações físicas que ocorrem durante cada etapa.
Pontos-chave explicados:
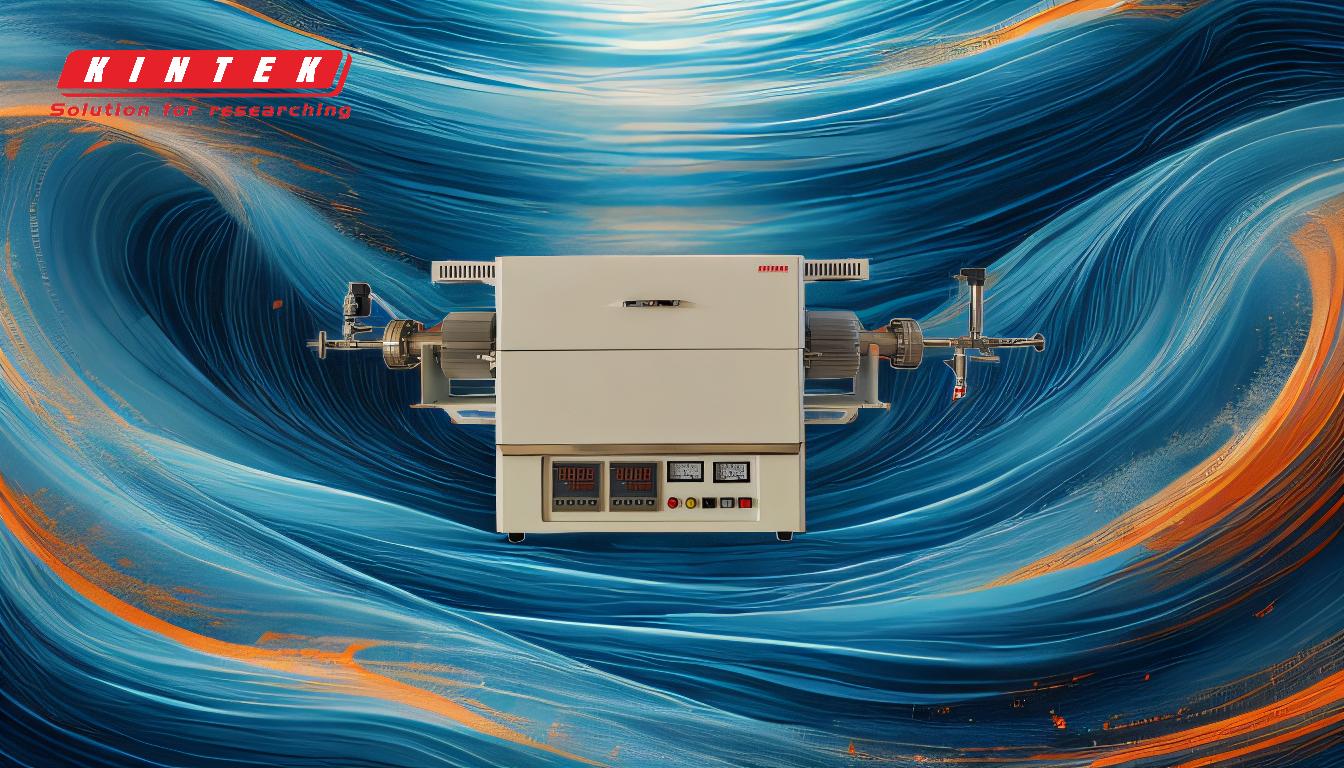
-
Preparação de matérias-primas
- O processo de sinterização começa com a preparação de matérias-primas, normalmente em forma de pó.
- Estes pós são misturados com aditivos, tais como agentes de acoplamento, aglutinantes ou defloculantes, para melhorar a uniformidade e facilitar a ligação.
- A mistura é frequentemente seca por pulverização para criar uma pasta, que é depois moldada na forma desejada.
- Reacções Químicas: Durante esta fase, não ocorrem reacções químicas significativas, mas a uniformidade da mistura é fundamental para garantir uma sinterização consistente mais tarde.
-
Compactação (compactação do pó)
- O pó misturado é compactado utilizando pressão mecânica, como a prensagem a frio ou a quente, para formar uma "peça verde".
- A compactação elimina os espaços vazios e assegura que o material tem uma densidade uniforme, o que é essencial para obter um produto final forte.
- Reacções Químicas: Nesta fase, as partículas podem formar soldaduras frias, mas não ocorrem grandes alterações químicas.
-
Aquecimento (sinterização ou cozedura)
- A peça verde é aquecida num ambiente controlado, normalmente num forno de sinterização ou num forno, a uma temperatura ligeiramente inferior ao ponto de fusão do material.
-
Durante o aquecimento, as partículas sofrem difusão, o que leva à formação de pescoço e densificação. É aqui que ocorrem as reacções químicas primárias e as transformações físicas.
- Formação do pescoço: As partículas ligam-se nos seus pontos de contacto, formando pescoços que crescem à medida que os átomos se difundem através das superfícies das partículas.
- Densificação: Os espaços vazios entre as partículas diminuem e o material torna-se mais denso e resistente.
- Sinterização em fase líquida (LPS): Em alguns casos, pode formar-se uma fase líquida para acelerar a fusão e a densificação das partículas.
- Reacções Químicas: Dependendo do material, podem ocorrer oxidação, redução ou transformações de fase. Por exemplo, na sinterização de cerâmica, o aglutinante pode decompor-se e as partículas de cerâmica podem fundir-se.
-
Arrefecimento e solidificação
- Após a sinterização, o material é arrefecido gradualmente para permitir a sua solidificação numa estrutura rígida e coesa.
- O arrefecimento controlado evita tensões térmicas e assegura que o material mantém as propriedades desejadas.
- Reacções Químicas: Não ocorrem reacções químicas significativas durante o arrefecimento, mas a microestrutura do material estabiliza.
-
Tratamento pós-sinterização
- Em alguns casos, podem ser aplicados tratamentos adicionais, como maquinagem, polimento ou revestimento, para obter as especificações do produto final.
- Reacções Químicas: Os tratamentos pós-sinterização são essencialmente mecânicos ou de nível superficial e não envolvem alterações químicas significativas.
Importância dos parâmetros controlados:
- Temperatura: O controlo preciso da temperatura é crucial para garantir a ligação adequada das partículas sem provocar a sua fusão total.
- Atmosfera: O ambiente de sinterização (por exemplo, vácuo, gás inerte ou atmosfera redutora) pode influenciar as reacções químicas e as propriedades finais do material.
- Tempo: A duração do aquecimento e do arrefecimento afecta a extensão da densificação e o desenvolvimento da microestrutura.
Aplicações da Sinterização:
- Metais: Utilizados para produzir componentes com elevada força e resistência ao desgaste, tais como engrenagens e rolamentos.
- Cerâmica: Utilizada para criar produtos duráveis e resistentes ao calor, como azulejos e isoladores.
- Compósitos: A sinterização é utilizada para combinar diferentes materiais, como metais e cerâmicas, para obter propriedades únicas.
Ao compreender o processo de sinterização e as suas fases, os fabricantes podem otimizar a produção de materiais de alta qualidade com propriedades personalizadas para aplicações específicas.
Tabela de resumo:
Etapas | Acções-chave | Reacções Químicas |
---|---|---|
Preparação de matérias-primas | Mistura de pós com aditivos, secagem por pulverização para formar uma pasta, moldagem. | Não há reacções significativas; a uniformidade é fundamental. |
Compactação | Prensagem de moldes a frio ou a quente para formar uma "peça verde". | Podem formar-se soldaduras a frio; não há grandes alterações químicas. |
Aquecimento (Sinterização) | Aquecimento até um pouco abaixo do ponto de fusão; formação de pescoço, densificação, LPS. | Oxidação, redução ou transformações de fase (por exemplo, decomposição do ligante, fusão de partículas). |
Arrefecimento | Arrefecimento gradual para solidificar o material. | Sem reacções significativas; a microestrutura estabiliza. |
Tratamento pós-sinterização | Maquinação, polimento ou revestimento para especificações finais. | Principalmente mecânico ou ao nível da superfície; sem alterações químicas significativas. |
Optimize o seu processo de sinterização para obter materiais de alta qualidade. contacte os nossos especialistas hoje mesmo !