Os fornos de resistência e de indução são ambos amplamente utilizados em processos industriais de aquecimento e fusão, mas diferem significativamente nos seus princípios de funcionamento, eficiência e aplicações.Os fornos de resistência dependem de elementos de aquecimento externos para gerar calor, que é depois transferido para o material, enquanto os fornos de indução geram calor diretamente dentro do material utilizando a indução electromagnética.Esta diferença fundamental leva a variações na eficiência energética, nos níveis de contaminação e nas capacidades operacionais.Abaixo, as principais diferenças são explicadas em pormenor.
Pontos-chave explicados:
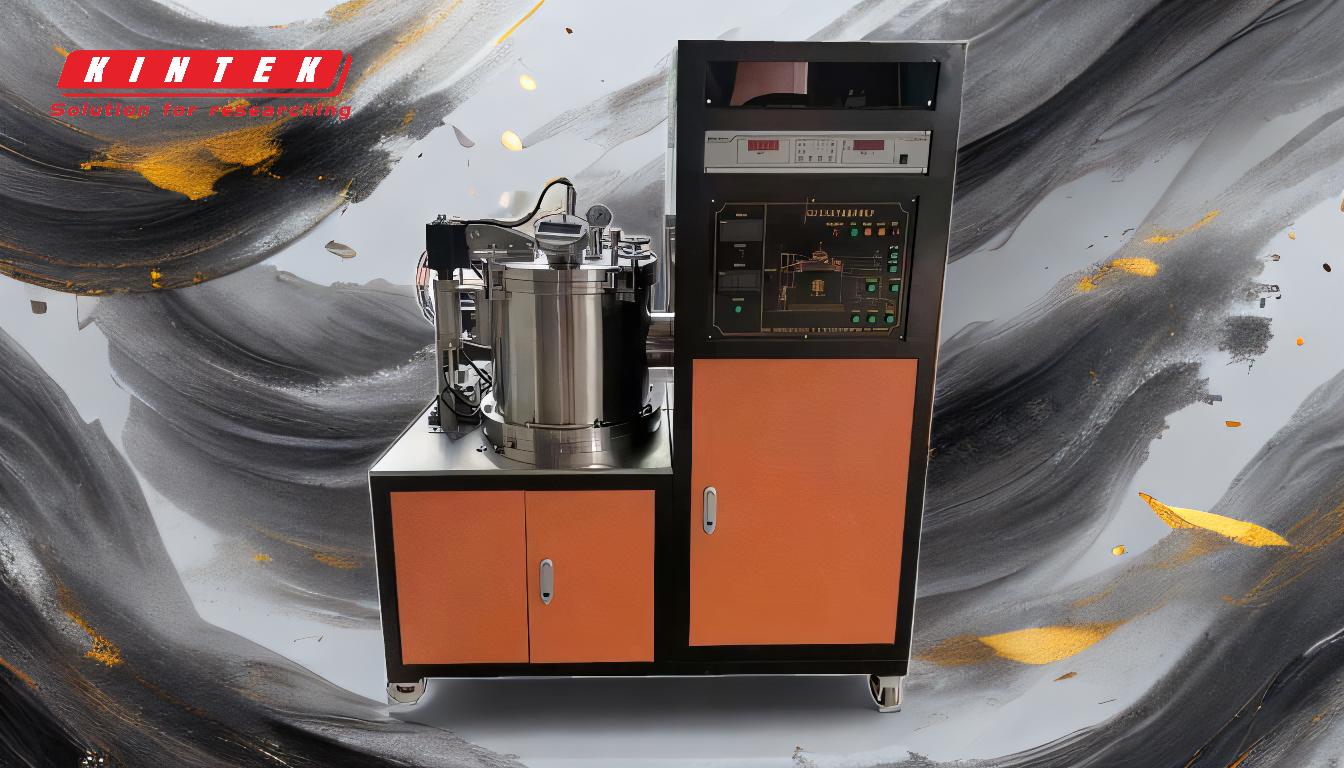
-
Mecanismo de aquecimento:
-
Forno de resistência:
- Utiliza elementos de aquecimento externos (por exemplo, elementos refractários ou bobinas) para gerar calor.
- O calor é transferido para o material através de condução, convecção ou radiação.
- Adequado para processos em que é necessário um aquecimento uniforme, mas a fonte de calor é externa ao material.
-
Forno de indução:
- Gera calor diretamente no material através da indução electromagnética.
- A corrente alternada cria um campo magnético alternado, induzindo correntes de Foucault no material, que produzem calor devido à resistência.
- Garante um aquecimento uniforme e minimiza a contaminação, uma vez que não está envolvida qualquer fonte de calor externa.
-
Forno de resistência:
-
Eficiência e consumo de energia:
-
Forno de resistência:
- Menos eficiente em termos energéticos devido à perda de calor durante a transferência da fonte externa para o material.
- Requer mais energia para manter temperaturas elevadas, especialmente em operações de grande escala.
-
Forno de indução:
- Mais eficiente em termos energéticos, uma vez que o calor é gerado diretamente no material, reduzindo a perda de calor.
- Atinge taxas de aquecimento mais rápidas e maior eficiência térmica, tornando-o ideal para aplicações de alta temperatura.
-
Forno de resistência:
-
Temperatura e densidade de potência:
-
Forno de resistência:
- Funciona com densidades de potência mais baixas em comparação com os fornos de indução.
- Adequado para aplicações que requerem temperaturas moderadas (por exemplo, recozimento, têmpera).
-
Forno de indução:
- Capaz de funcionar a temperaturas e densidades de potência mais elevadas.
- Pode atingir temperaturas de forjamento de até 1250°C e temperaturas de fusão de até 1650°C, tornando-o adequado para fusão e processamento a alta temperatura.
-
Forno de resistência:
-
Contaminação e pureza:
-
Forno de resistência:
- Maior risco de contaminação devido à utilização de elementos de aquecimento externos, que podem introduzir impurezas.
- Requer uma seleção cuidadosa dos elementos de aquecimento e dos revestimentos do forno para minimizar a contaminação.
-
Forno de indução:
- Contaminação mínima, uma vez que o calor é gerado dentro do próprio material.
- Ideal para aplicações que requerem materiais de elevada pureza, como nas indústrias de semicondutores ou aeroespacial.
-
Forno de resistência:
-
Controlo e automatização:
-
Forno de resistência:
- Depende normalmente de sistemas de controlo manuais ou semi-automatizados.
- Limitado pela complexidade de manter um aquecimento uniforme em grandes volumes.
-
Forno de indução:
- Equipado com sistemas de controlo avançados, incluindo varrimento automático de frequência, controlo de potência constante e mecanismos de proteção abrangentes.
- Oferece um controlo preciso da temperatura e um funcionamento suave, reduzindo a necessidade de intervenção manual.
-
Forno de resistência:
-
Aplicações:
-
Forno de resistência:
- Normalmente utilizado para processos de tratamento térmico como o recozimento, o endurecimento e a têmpera.
- Adequado para o processamento em lote de materiais que não requerem temperaturas extremamente elevadas.
-
Forno de indução:
- Amplamente utilizado em aplicações de fusão e forjamento, especialmente para metais como aço, alumínio e cobre.
- Preferido para processos contínuos e operações de alta temperatura onde a eficiência e a pureza são críticas.
-
Forno de resistência:
-
Conceção e manutenção:
-
Forno de resistência:
- Conceção mais simples com menos componentes, o que torna a manutenção relativamente fácil.
- No entanto, os elementos de aquecimento podem exigir uma substituição frequente devido ao desgaste.
-
Forno de indução:
- Conceção mais complexa com componentes como indutores, condensadores e sistemas de controlo.
- Requer considerações de design cuidadosas, tais como a disposição do jugo e o espaçamento do indutor, para garantir um desempenho ótimo.
- A manutenção é mais fácil nos modelos avançados com circuitos integrados e componentes modulares.
-
Forno de resistência:
-
Adequação do material:
-
Forno de resistência:
- Adequado para uma vasta gama de materiais, incluindo materiais não metálicos e magnéticos.
- Limitado pela capacidade do material de absorver calor de uma fonte externa.
-
Forno de Indução:
- Mais adequado para materiais condutores, especialmente metais.
- Surgem desafios com materiais não magnéticos como o alumínio, que requerem projectos de indutores especializados para garantir um aquecimento eficiente.
-
Forno de resistência:
Em resumo, os fornos de resistência e de indução servem diferentes objectivos com base nos seus mecanismos de aquecimento, eficiência e aplicações.Os fornos de resistência são mais adequados para processos de temperatura moderada e operações em lote, enquanto os fornos de indução se destacam em processos de alta temperatura, alta pureza e contínuos.A escolha entre os dois depende dos requisitos específicos da aplicação, incluindo temperatura, tipo de material e eficiência desejada.
Tabela de resumo:
Aspeto | Forno de resistência | Forno de indução |
---|---|---|
Mecanismo de aquecimento | Os elementos de aquecimento externos transferem calor por condução, convecção ou radiação. | Calor gerado diretamente no material através de indução electromagnética. |
Eficiência | Menos eficiente em termos energéticos devido à perda de calor durante a transferência. | Mais eficiente em termos energéticos com taxas de aquecimento mais rápidas e perda de calor reduzida. |
Gama de temperaturas | Adequado para temperaturas moderadas (por exemplo, recozimento, têmpera). | Capaz de altas temperaturas (até 1650°C) para fusão e forjamento. |
Risco de contaminação | Maior risco devido a elementos de aquecimento externos. | Contaminação mínima, ideal para aplicações de alta pureza. |
Sistemas de controlo | Sistemas de controlo manuais ou semi-automatizados. | Automação avançada com controlo preciso da temperatura e mecanismos de proteção. |
Aplicações | Processos de tratamento térmico (por exemplo, recozimento, endurecimento). | Operações de fusão, forjamento e alta temperatura para metais como o aço e o alumínio. |
Conceção e manutenção | Conceção mais simples, mas os elementos de aquecimento podem necessitar de substituição frequente. | Conceção complexa com manutenção mais fácil para modelos avançados. |
Adequação do material | Adequado para materiais não metálicos e magnéticos. | Melhor para materiais condutores, especialmente metais. |
Precisa de ajuda para escolher o forno certo para a sua aplicação? Contacte os nossos especialistas hoje para um aconselhamento personalizado!