Os fornos de indução e de resistência são ambos utilizados para aquecer e fundir metais, mas funcionam com base em princípios fundamentalmente diferentes.Os fornos de indução utilizam a indução electromagnética para gerar calor diretamente na carga metálica, enquanto os fornos de resistência dependem de elementos refractários aquecidos eletricamente para transferir calor para o metal.Os fornos de indução são mais eficientes, reduzem a contaminação e são mais adequados para composições de ligas precisas, enquanto os fornos de resistência podem funcionar a temperaturas e densidades de potência mais elevadas, mas podem ter maiores perdas de calor e riscos de contaminação.
Pontos-chave explicados:
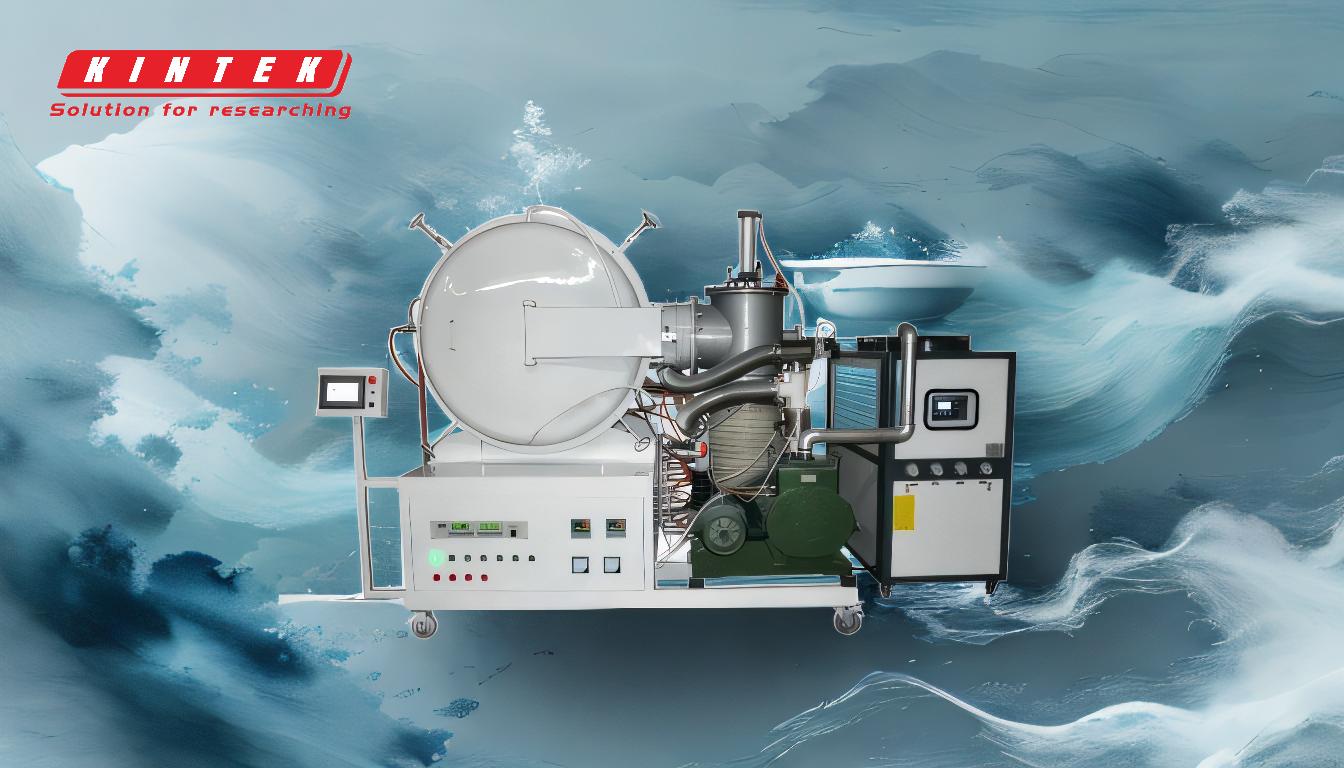
-
Mecanismo de aquecimento:
-
Forno de indução:
- O calor é gerado diretamente na carga metálica através da indução electromagnética.Uma corrente alternada na bobina do forno cria um campo magnético, induzindo correntes de Foucault no metal, que produzem calor.
- Este método assegura que o calor tem origem no próprio metal, reduzindo a contaminação e a perda de calor.
-
Forno de resistência:
- O calor é gerado por elementos refractários aquecidos eletricamente (tais como bobinas ou varetas) no interior do forno.Este calor é então transferido para a carga metálica através de condução e radiação.
- Este método de aquecimento indireto pode levar a uma maior perda de calor e a uma potencial contaminação dos elementos de aquecimento.
-
Forno de indução:
-
Eficiência e contaminação:
-
Forno de indução:
- Mais eficiente devido ao aquecimento direto do metal, minimizando a perda de calor.
- Redução da contaminação, uma vez que o metal não entra em contacto direto com elementos de aquecimento externos.
-
Forno de resistência:
- Menos eficiente porque o calor tem de ser transferido dos elementos de aquecimento para o metal, levando a uma maior perda de calor.
- Maior risco de contaminação dos elementos de aquecimento, especialmente se estes se degradarem com o tempo.
-
Forno de indução:
-
Temperatura e densidade de potência:
-
Forno de indução:
- Funciona normalmente a temperaturas mais baixas em comparação com os fornos de resistência.
- Limitado pela capacidade de manter um campo magnético forte, especialmente com materiais não magnéticos como o alumínio.
-
Forno de resistência:
- Pode atingir temperaturas mais elevadas e funcionar com densidades de potência mais elevadas.
- Adequado para aplicações que requerem temperaturas muito elevadas, como os processos de sinterização.
-
Forno de indução:
-
Conceção e complexidade:
-
Forno de indução:
- Requer uma conceção cuidadosa da bobina e da bobina magnética para garantir uma indução eficiente, especialmente para materiais não magnéticos.
- Mais complexo devido à necessidade de um controlo preciso do campo eletromagnético.
-
Forno de resistência:
- Conceção mais simples com elementos aquecidos eletricamente, o que facilita a construção e a manutenção.
- Sistemas de controlo menos complexos em comparação com os fornos de indução.
-
Forno de indução:
-
Aplicações:
-
Forno de indução:
- Ideal para fundir e ligar metais com um controlo preciso da composição.
- Utilizado habitualmente em fundições para fundição e em investigação metalúrgica.
-
Forno de resistência:
- Adequado para processos de alta temperatura como sinterização, recozimento e tratamento térmico.
- Utilizado em indústrias que requerem temperaturas elevadas uniformes, como o fabrico de cerâmica e vidro.
-
Forno de indução:
-
Considerações sobre o material:
-
Forno de indução:
- Eficaz para materiais condutores, mas surgem desafios com materiais não magnéticos como o alumínio, onde pode ocorrer divergência do campo magnético.
- Requer uma conceção cuidadosa para gerir a fuga de fluxo magnético e garantir um aquecimento eficiente.
-
Forno de resistência:
- Pode tratar uma vasta gama de materiais, incluindo os não condutores, uma vez que o calor é gerado externamente.
- Menos sensível às propriedades magnéticas do material, o que o torna versátil para várias aplicações industriais.
-
Forno de indução:
Em resumo, a escolha entre um forno de indução e um forno de resistência depende dos requisitos específicos da aplicação, incluindo o tipo de material, a temperatura desejada, a eficiência e as preocupações com a contaminação.Os fornos de indução oferecem vantagens em termos de eficiência e controlo da contaminação, enquanto os fornos de resistência oferecem capacidades de temperatura mais elevadas e um design mais simples.
Tabela de resumo:
Caraterísticas | Forno de indução | Forno de resistência |
---|---|---|
Mecanismo de aquecimento | Aquecimento direto por indução electromagnética na carga metálica. | Aquecimento indireto através de elementos refractários aquecidos eletricamente. |
Eficiência | Maior eficiência devido ao aquecimento direto, reduzindo as perdas de calor. | Menor eficiência devido a perdas por transferência de calor. |
Risco de contaminação | Risco menor porque o metal não entra em contacto com os elementos de aquecimento externos. | Risco mais elevado devido à potencial contaminação dos elementos de aquecimento. |
Gama de temperaturas | Temperaturas mais baixas, limitadas pela força do campo magnético. | Temperaturas mais elevadas, adequadas para processos de sinterização e de alta temperatura. |
Complexidade do projeto | Mais complexo devido ao controlo preciso do campo eletromagnético. | Conceção mais simples com elementos aquecidos eletricamente. |
Aplicações | Ideal para fusão precisa de ligas, fundições e investigação metalúrgica. | Adequado para sinterização, recozimento e processos industriais de alta temperatura. |
Adequação do material | Melhor para materiais condutores; desafios com materiais não magnéticos como o alumínio. | Versátil, funciona com materiais condutores e não condutores. |
Ainda não tem a certeza de qual o forno mais adequado às suas necessidades? Contacte os nossos especialistas hoje para um aconselhamento personalizado!