Os fornos rotativos são equipamentos industriais complexos utilizados principalmente para o processamento de materiais a alta temperatura.São constituídos por vários componentes críticos, cada um deles concebido para resistir a condições extremas e garantir um funcionamento eficiente.Os principais materiais e componentes incluem a carcaça do forno, o revestimento refratário, os pneus de apoio (anéis de suporte), os rolos, a engrenagem de transmissão e os permutadores de calor internos.O invólucro é normalmente feito de aço, enquanto o revestimento refratário é composto por materiais resistentes ao calor para proteger o invólucro de altas temperaturas.Os pneus e rolos de suporte são também feitos de materiais duráveis para suportar o peso e a rotação do forno.A engrenagem de acionamento e os permutadores de calor internos são personalizados com base na aplicação específica e no material a ser processado.
Pontos-chave explicados:
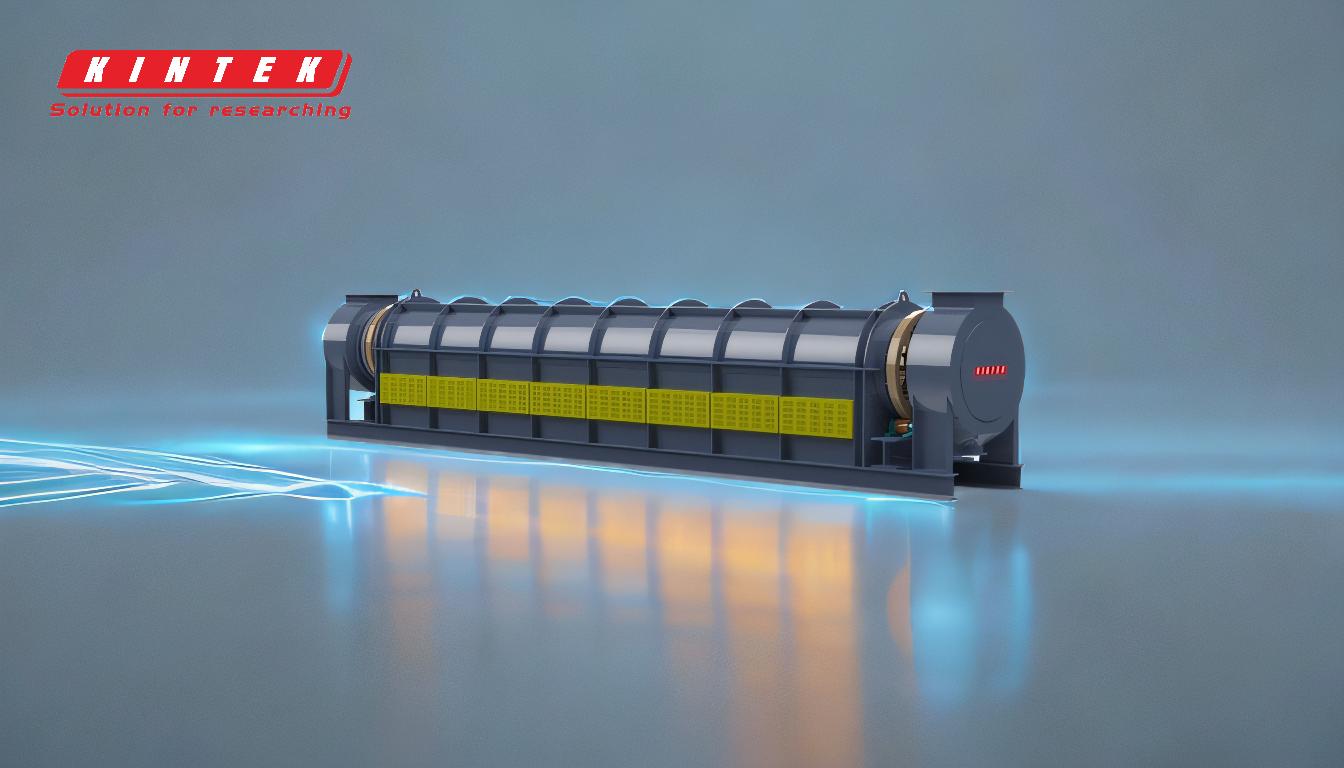
-
Forno:
- Material:O invólucro é geralmente construído em aço de alta qualidade, que proporciona a resistência e a durabilidade necessárias para suportar as tensões mecânicas de rotação e as altas temperaturas no interior do forno.
- Função:O invólucro actua como o principal componente estrutural, abrigando o revestimento refratário e suportando os componentes internos.É cónico nas extremidades para facilitar o movimento do material e reduzir as concentrações de tensão.
-
Revestimento refratário:
- Material:O revestimento é feito de materiais resistentes ao calor, como a alumina, a sílica ou a magnésia, dependendo da temperatura de funcionamento e do tipo de material a ser processado.
- Função:O revestimento refratário protege o invólucro de aço do calor extremo no interior do forno, evitando danos térmicos e prolongando a vida útil do forno.
-
Pneus de suporte (anéis de suporte) e rolos:
- Material:Estes componentes são normalmente fabricados em aço de alta resistência ou em ferro fundido para suportar o peso do forno e as forças de rotação.
- Função:Os pneus e rolos de suporte fornecem o apoio necessário à estrutura do forno, permitindo-lhe rodar suavemente.Também ajudam a distribuir uniformemente o peso do forno pela estrutura de suporte.
-
Engrenagem de acionamento:
- Material:A engrenagem de acionamento é normalmente fabricada em aço endurecido para garantir a durabilidade e uma transmissão de potência eficiente.
- Função:A engrenagem de acionamento, juntamente com o motor, induz o movimento de rotação do forno.Pode ser um conjunto de transmissão por corrente e roda dentada, por engrenagem, por fricção ou por transmissão direta, dependendo dos requisitos específicos da aplicação.
-
Permutadores de calor internos:
- Material:Os permutadores de calor são frequentemente fabricados com materiais que podem suportar temperaturas elevadas e ambientes corrosivos, como o aço inoxidável ou ligas especializadas.
- Função:Os permutadores de calor internos são utilizados para otimizar a transferência de calor dentro do forno, assegurando que o material é aquecido de forma uniforme e eficiente.Eles podem ser personalizados com base nos requisitos térmicos específicos do processo.
-
Componentes adicionais:
- Conjunto de rodas de tração:Este conjunto inclui engrenagens grandes e pequenas e rodas dentadas, essenciais para o mecanismo de rotação.
- Rolos de pressão:Estes rolos ajudam a manter a posição axial do forno e impedem o seu desalinhamento.
- Tubo de descarga:Este componente está localizado na extremidade de descarga do forno e é concebido para lidar com a descarga do material processado.
-
Personalização:
- Material e design:Os materiais e o design dos componentes do forno rotativo podem ser personalizados com base nas necessidades específicas da indústria e do material a ser processado.A personalização envolve frequentemente a seleção de materiais que podem suportar temperaturas mais elevadas ou ambientes mais corrosivos, mas isto tem normalmente um custo mais elevado.
-
Forno rotativo de laboratório:
- Corpo do forno:O corpo do forno em fornos rotativos à escala laboratorial utiliza frequentemente um forno de fibra de alumina para isolamento e um motor de 60W com uma caixa de redução para rotação.
- Controlo da inclinação:A inclinação do corpo do forno é controlada por um dispositivo hidráulico acionado por um volante, permitindo um controlo preciso das condições de processamento.
Em resumo, os fornos rotativos são fabricados a partir de uma combinação de aço de alta resistência, materiais refractários e componentes especializados concebidos para resistir a condições extremas.Cada componente desempenha um papel crucial para garantir o funcionamento eficiente e fiável do forno, e os materiais podem ser personalizados para satisfazer requisitos industriais específicos.
Tabela de resumo:
Componente | Material | Função |
---|---|---|
Carcaça do forno | Aço de alta qualidade | Principal componente estrutural, suporta as peças internas e resiste à rotação. |
Revestimento refratário | Alumina, sílica ou magnésia | Protege o invólucro do calor extremo, prolongando a vida útil do forno. |
Pneus e rolos de suporte | Aço de alta resistência ou ferro fundido | Suporta o corpo do forno, assegura uma rotação suave e distribui o peso. |
Engrenagem de acionamento | Aço temperado | Induz a rotação do forno, personalizado para aplicações específicas. |
Permutadores de calor internos | Aço inoxidável ou ligas especializadas | Optimiza a transferência de calor para um processamento uniforme e eficiente do material. |
Precisa de um forno rotativo adaptado às suas necessidades industriais? Contacte-nos hoje para discutir as opções de personalização!