Introdução à sinterização por plasma de faísca (SPS)
A sinterização por plasma de faísca (SPS) representa uma abordagem inovadora nas modernas tecnologias de processamento de materiais, revolucionando a forma como os materiais são sinterizados. Este método inovador destaca-se pela utilização de impulsos de corrente direta para obter um aquecimento e sinterização rápidos, diferindo significativamente das técnicas tradicionais. O processo único da SPS envolve a geração de um plasma de faíscas através de correntes pulsadas, facilitando a criação de materiais com propriedades superiores. À medida que nos aprofundamos neste guia abrangente, iremos explorar os meandros da SPS, as suas inúmeras aplicações em várias indústrias e as vantagens substanciais que oferece em relação aos métodos de sinterização convencionais. Junte-se a nós enquanto descobrimos o potencial transformador da SPS para moldar o futuro da ciência dos materiais.
Como funciona o forno de sinterização por plasma de faísca
A sinterização por plasma de faísca (SPS), também conhecida como sinterização por corrente eléctrica pulsada (PECS), sinterização activada por plasma (PAS) ou tecnologia de sinterização assistida por campo (FAST), é uma técnica de sinterização sofisticada que utiliza correntes contínuas pulsadas elevadas para aquecer um pó compacto numa configuração de matriz/perfuração. Este método permite a aplicação de forças de compressão até 250 kN, com saídas de transformador capazes de atingir 10 V e correntes até 10 kA. Os padrões de corrente DC pulsada podem ser ajustados com segmentos ON e OFF que variam de 0 a 255 ms, permitindo um controlo preciso do processo de sinterização.
O processo SPS é caracterizado pelas suas rápidas taxas de aquecimento e arrefecimento, que podem exceder 1000°C/min e 400°C/min, respetivamente, dependendo do tamanho e do design da ferramenta. Este ciclo térmico rápido minimiza os processos de engrossamento a baixas temperaturas e preserva as nanoestruturas intrínsecas mesmo após a densificação total. A temperatura dentro do forno SPS é monitorizada através de um pirómetro central que incide no fundo de um furo no punção superior, assegurando uma medição precisa da temperatura, independentemente das propriedades ou tamanho da amostra. A monitorização adicional da temperatura pode ser conseguida utilizando um pirómetro externo e termopares flexíveis colocados em vários locais.
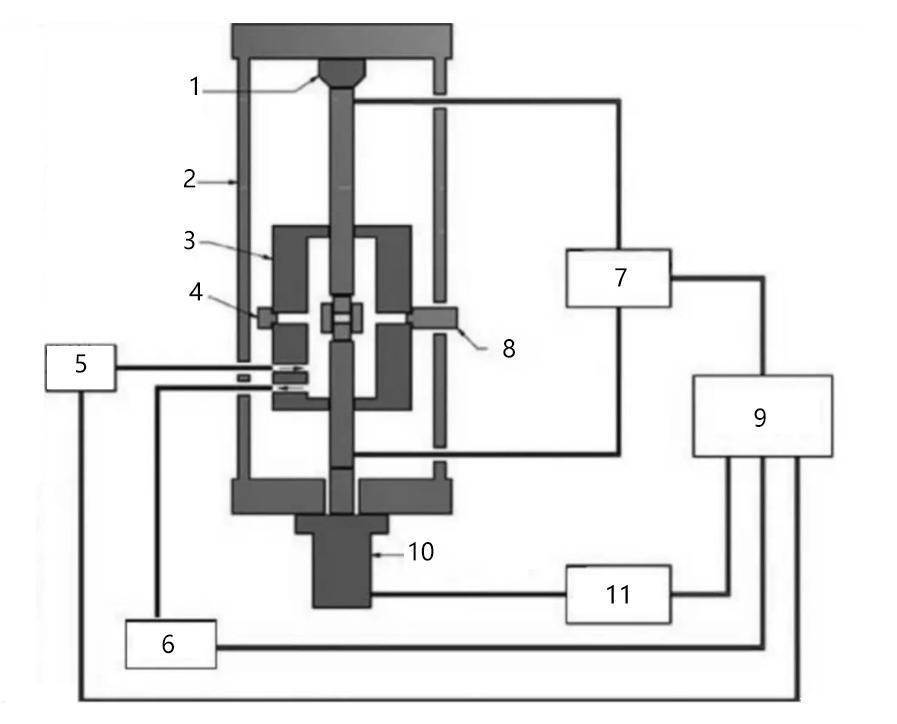
1. Unidade de carregamento 2. Estrutura de carga 3. Câmara de vácuo 4. Janela de observação 5. Canal de gás inerte 6. Bomba de vácuo 7. Interruptor de impulsos 8. Medidor de temperatura 9. Sistema de controlo 10. Cilindro hidráulico 11. Sistema hidráulico
Os principais componentes de um forno SPS incluem o dispositivo de pressão axial, o elétrodo de punção arrefecido a água e a câmara de vácuo. O dispositivo de pressão axial aplica a força de compressão necessária, enquanto os eléctrodos de punção arrefecidos a água ajudam a gerir o calor gerado durante o processo. A câmara de vácuo, associada a um sistema de controlo da atmosfera que pode alternar entre ambientes de vácuo e árgon, assegura condições óptimas de sinterização. A fonte de alimentação de impulsos DC, juntamente com um sistema de água de arrefecimento, medição de deslocamento, medição de temperatura e unidades de controlo de segurança, completam a configuração SPS, facilitando o controlo abrangente do processo e a programação do ciclo de sinterização através de uma interface de ecrã tátil de fácil utilização.
O forno SPS é amplamente utilizado para a sinterização de uma vasta gama de materiais, incluindo cerâmicas, cermets e metais. As suas principais vantagens técnicas residem nas suas elevadas taxas de aquecimento e arrefecimento, que reduzem significativamente os tempos de processamento. A elevada corrente pulsada não só aumenta a densificação em materiais condutores de eletricidade, como também ativa múltiplos mecanismos de sinterização, tais como a remoção de óxidos da superfície, a electromigração e a electroplasticidade. Esta combinação de pressão mecânica, campo elétrico e campo térmico melhora significativamente a ligação e a densificação entre partículas, tornando o SPS um método preferido para a preparação de materiais de elevado desempenho.
Em resumo, o processo Spark Plasma Sintering é um método altamente eficiente e controlado para a densificação de materiais, oferecendo tempos de processamento rápidos e a capacidade de manter microestruturas finas. As suas aplicações abrangem vários campos, desde cerâmicas avançadas a compósitos metálicos, destacando a sua versatilidade e importância na moderna ciência e engenharia de materiais.
Vantagens da utilização de SPS no processamento de materiais
A sinterização por plasma de faísca (SPS) revolucionou o campo do processamento de materiais ao oferecer vantagens significativas em relação às técnicas de sinterização tradicionais. A SPS é uma técnica de sinterização assistida por campo que utiliza tanto a temperatura como a pressão para conseguir uma rápida densificação dos materiais. Este método é particularmente eficaz para sinterizar uma vasta gama de materiais, incluindo cerâmicas, metais e compósitos, com uma eficiência e precisão notáveis.
Taxas de sinterização rápidas
Uma das vantagens mais notáveis do SPS é a sua capacidade de atingir taxas de sinterização rápidas. Os métodos tradicionais de sinterização, como a prensagem a quente e a sinterização sem pressão, podem levar várias horas para atingir a densificação desejada. Em contraste, a SPS pode densificar materiais em apenas alguns minutos. Esta sinterização rápida é possível graças às elevadas taxas de aquecimento, que podem exceder os 500°C por minuto. Por exemplo, atingir uma temperatura de 1200°C pode ser conseguido em apenas 4 minutos com a SPS, em comparação com 2 a 4 horas com os métodos convencionais. Esta velocidade não só aumenta a produtividade como também reduz o consumo de energia e os custos operacionais.
Sinterização de grão fino
A SPS facilita a sinterização de grão fino, que é crucial para melhorar as propriedades mecânicas e físicas dos materiais sinterizados. As taxas de aquecimento rápido inibem o crescimento do grão, permitindo a criação de materiais com microestruturas controladas. Isto é particularmente benéfico para a produção de materiais nanocristalinos, onde a manutenção de pequenos tamanhos de grão é essencial para alcançar propriedades superiores. A sinterização de grão fino também melhora a homogeneidade dos produtos sinterizados, conduzindo a um desempenho mais consistente e fiável.
Capacidade de controlar a densidade e os gradientes de temperatura
A SPS proporciona um excelente controlo sobre a densidade e os gradientes de temperatura nos materiais sinterizados. Este nível de controlo é conseguido através da aplicação simultânea de temperatura e pressão, o que permite ajustes precisos ao processo de sinterização. O controlo da densidade é particularmente importante para a criação de materiais com níveis de porosidade específicos ou para obter uma densificação total. Além disso, o SPS pode criar gradientes de temperatura dentro do molde, permitindo a sinterização simultânea de materiais com diferentes pontos de fusão. Esta capacidade é inestimável para a produção de materiais funcionalmente graduados (FGMs), onde a composição e as propriedades variam espacialmente.
Eficiência e compacidade dos fornos SPS
Os fornos SPS são concebidos para serem altamente eficientes e compactos, tornando-os ideais para aplicações industriais e de investigação. O design compacto dos fornos SPS reduz o espaço necessário e permite uma fácil integração nas linhas de produção existentes. Além disso, a eficiência dos fornos SPS é reforçada pela sua capacidade de atingir taxas de aquecimento e arrefecimento rápidas, o que contribui ainda mais para a poupança de energia e redução dos custos operacionais. O mecanismo de aquecimento interno, que envolve o aquecimento Joule do molde de grafite e do briquete de pó, assegura uma distribuição uniforme do calor e minimiza a perda de calor, optimizando assim o processo de sinterização.
Sinterização de purificação e ativação
O SPS também oferece vantagens únicas em termos de sinterização por purificação e ativação. O processo pode remover gases adsorvidos e películas de óxido das superfícies das partículas, conduzindo a interfaces mais limpas e a uma melhor ligação. Este efeito de purificação, combinado com a ativação das superfícies das partículas, permite a sinterização de materiais que, de outra forma, seriam difíceis de processar. Esta capacidade expande a gama de materiais que podem ser efetivamente sinterizados utilizando SPS, incluindo cerâmicas avançadas e compósitos.
Em conclusão, a sinterização por plasma de faísca (SPS) oferece uma multiplicidade de vantagens que a tornam uma escolha superior para o processamento de materiais. As suas taxas de sinterização rápidas, as capacidades de sinterização de grão fino, o controlo da densidade e do gradiente de temperatura, a eficiência e a compacidade fazem dela uma ferramenta inestimável para aplicações industriais e de investigação. Ao aproveitar estas vantagens, a SPS continua a alargar as fronteiras da ciência e engenharia de materiais, permitindo o desenvolvimento de materiais inovadores e de elevado desempenho.
Aplicações da SPS em vários sectores
A tecnologia Spark Plasma Sintering (SPS) revolucionou os processos de fabrico em várias indústrias, permitindo a criação de materiais avançados com propriedades únicas. A SPS é particularmente conhecida pela sua capacidade de produzir materiais de alta densidade e de grão fino rapidamente e a temperaturas relativamente baixas, tornando-a um método preferido para a síntese de nanomateriais, cerâmicas, compósitos e implantes médicos.
Nanomateriais
Uma das aplicações mais significativas da SPS é a preparação de nanomateriais. Os nanomateriais apresentam propriedades mecânicas e físicas excepcionais devido ao seu pequeno tamanho de grão, o que aumenta a sua resistência e plasticidade. A SPS facilita a síntese destes materiais ao inibir o crescimento do grão durante o processo de sinterização. O rápido aquecimento e os curtos tempos de sinterização inerentes à SPS ajudam a manter o tamanho do grão à escala nanométrica, o que é crucial para o desempenho dos nanomateriais. Esta técnica é particularmente eficaz para sinterizar pós obtidos através de métodos como a liga mecânica, que são frequentemente difíceis de consolidar utilizando métodos tradicionais.
Cerâmica e Cermets
A SPS é também amplamente utilizada na produção de cerâmicas e cermets de alta densidade e de grão fino. O mecanismo de aquecimento único da SPS, em que cada partícula de pó e os poros entre elas actuam como fontes de calor, permite uma rápida densificação e uma redução significativa dos tempos e temperaturas de sinterização. Este método é altamente vantajoso para a produção industrial, uma vez que poupa energia e melhora a eficiência da produção. A capacidade de produzir cerâmicas com elevada densidade e estrutura de grão fino aumenta a sua resistência mecânica e durabilidade, tornando-as adequadas para várias aplicações de engenharia.
Materiais funcionais gradientes
Os materiais funcionais de gradiente, que têm uma distribuição de gradiente em determinadas direcções, são outra área em que a SPS tem dado contributos significativos. Os métodos de sinterização tradicionais debatem-se com as diferentes temperaturas de sinterização necessárias para cada camada em materiais de gradiente. A SPS, no entanto, pode gerir eficazmente este gradiente, permitindo a produção à escala industrial destes materiais complexos. O processo de sinterização controlado na SPS assegura que cada camada atinge as propriedades desejadas sem comprometer a integridade da estrutura global.
Implantes médicos
No sector médico, a SPS é utilizada para fabricar implantes com propriedades mecânicas e biocompatibilidade adaptadas. A capacidade de controlar com precisão as condições de sinterização permite a criação de implantes com propriedades mecânicas específicas que correspondem ao osso humano, melhorando a sua funcionalidade e longevidade. Para além disso, a SPS pode ser utilizada para produzir estruturas porosas que facilitam o crescimento do osso, melhorando a integração dos implantes com o tecido circundante.
Compósitos e materiais nanoestruturados
A SPS é fundamental para o fabrico de compósitos e materiais nanoestruturados com propriedades melhoradas, tais como características magnéticas, piezoeléctricas, termoeléctricas e ópticas. O processo de sinterização rápida em SPS ajuda a manter a nanoestrutura dos materiais, o que é crucial para o seu desempenho. Por exemplo, o SPS é utilizado na sinterização de nanotubos de carbono para desenvolver eléctrodos de emissão de electrões de campo, demonstrando a sua versatilidade no manuseamento de diferentes tipos de materiais.
Em conclusão, a sinterização por plasma de faísca emergiu como uma técnica versátil e poderosa com aplicações que abrangem várias indústrias. A sua capacidade de produzir materiais avançados de alta qualidade e com propriedades únicas torna-a uma ferramenta indispensável no fabrico moderno. À medida que a investigação e o desenvolvimento neste domínio continuam a avançar, espera-se que as potenciais aplicações da SPS se expandam ainda mais, impulsionando a inovação na ciência e engenharia dos materiais.
Estudos de caso: Implementações bem-sucedidas de SPS
A tecnologia Spark Plasma Sintering (SPS) revolucionou o campo da ciência dos materiais, permitindo a rápida sinterização e densificação de uma vasta gama de materiais com propriedades melhoradas. Esta secção apresenta vários estudos de caso que destacam as aplicações bem-sucedidas da SPS em ambientes industriais e de investigação, demonstrando a sua versatilidade e eficácia.
Materiais de armazenamento de energia
Uma das aplicações mais significativas da SPS é o desenvolvimento de materiais avançados de armazenamento de energia. Por exemplo, a SPS tem sido utilizada para produzir baterias de iões de lítio de alta capacidade com um desempenho melhorado. Ao controlar com precisão os parâmetros de sinterização, os investigadores conseguiram criar materiais de bateria com densidades de energia mais elevadas e ciclos de vida melhorados. De acordo com estudos, as baterias de iões de lítio processadas por SPS mostraram um aumento de 20% na capacidade de armazenamento de energia em comparação com os métodos convencionais, tornando-as ideais para utilização em veículos eléctricos e eletrónica portátil.
Engenharia biomédica
No domínio da engenharia biomédica, a SPS tem sido fundamental para a criação de cerâmicas porosas para a administração de medicamentos e andaimes para a engenharia de tecidos. Estes materiais requerem um controlo preciso da sua microestrutura para garantir a compatibilidade com os sistemas biológicos. A SPS permite o fabrico de estruturas altamente porosas com tamanhos de poros controlados, que são cruciais para a administração eficaz de medicamentos e o crescimento de tecidos. Por exemplo, as estruturas de hidroxiapatite processadas por SPS têm sido utilizadas na engenharia de tecidos ósseos, demonstrando uma biocompatibilidade e resistência mecânica superiores aos métodos tradicionais.
Cerâmica avançada
A SPS também tem sido amplamente utilizada na produção de cerâmicas avançadas, tais como supercondutores de alta temperatura e cerâmicas piezoeléctricas de alto desempenho. Estes materiais são essenciais para aplicações que vão desde a transmissão de energia a sensores e actuadores. A SPS permite a densificação destas cerâmicas a temperaturas mais baixas e em tempos mais curtos, preservando as suas propriedades únicas. Por exemplo, a SPS tem sido utilizada para produzir supercondutores de óxido de cobre e bário de ítrio (YBCO) com densidades quase teóricas, melhorando significativamente as suas temperaturas de transição supercondutoras.
Intermetálicos e Compósitos
A versatilidade da SPS é ainda demonstrada no processamento de intermetálicos e compósitos. A SPS tem sido utilizada para criar ligas avançadas com propriedades mecânicas, térmicas e eléctricas melhoradas. Por exemplo, a SPS tem sido utilizada para sintetizar ligas intermetálicas de alumineto de titânio (TiAl), que apresentam resistência superior a altas temperaturas e resistência à oxidação. Além disso, a SPS permitiu a produção de cerâmicas e metais reforçados com propriedades mecânicas melhoradas, tais como compósitos de matriz de titânio com partículas de cerâmica incorporadas, resultando em materiais com elevada resistência e resistência ao desgaste.
Aplicações industriais
Em ambientes industriais, a SPS foi adoptada para a produção de vários materiais, incluindo materiais magnéticos, materiais duros e materiais funcionais gradientes. Por exemplo, empresas japonesas como a Ohta Seiki implementaram com sucesso a SPS para a produção em massa de materiais superduros 100% WC, fornecendo a mais de 40 fabricantes no Japão e no estrangeiro. Estes materiais são utilizados numa vasta gama de aplicações, desde ferramentas de corte a componentes electrónicos, demonstrando a escalabilidade industrial da SPS.
Conclusão
Os estudos de caso aqui apresentados ilustram a ampla aplicabilidade das SPS em vários domínios, desde o armazenamento de energia à engenharia biomédica e aos materiais avançados. A capacidade da SPS para sinterizar e densificar rapidamente materiais a temperaturas mais baixas, juntamente com o seu controlo preciso do processo, torna-a uma ferramenta inestimável para cientistas e engenheiros de materiais. À medida que a investigação e o desenvolvimento continuam a avançar, espera-se que as potenciais aplicações da SPS se expandam ainda mais, solidificando a sua posição como uma tecnologia líder no processamento de materiais.
Desafios e considerações em SPS
A implementação da tecnologia Spark Plasma Sintering (SPS) apresenta vários desafios e considerações que as organizações têm de enfrentar para tirar o máximo partido das suas vantagens. Estes incluem custos elevados de equipamento, complexidades operacionais e a necessidade de formação especializada. Compreender estes desafios e desenvolver estratégias para os ultrapassar é crucial para uma integração e utilização bem sucedidas da tecnologia SPS.
Custos de equipamento
Uma das principais barreiras à adoção da tecnologia SPS é o elevado investimento inicial necessário para o equipamento. Os sistemas SPS são sofisticados e incluem características avançadas, como o controlo preciso da temperatura e da pressão, sistemas de vácuo e fontes de alimentação especializadas. Estes componentes não só aumentam o custo inicial, como também requerem manutenção e calibração regulares para garantir um desempenho ótimo.
Complexidades operacionais
As operações SPS envolvem várias fases, incluindo a criação de vácuo, aplicação de pressão, aquecimento por resistência e arrefecimento controlado. Cada fase requer uma monitorização e ajuste cuidadosos para evitar defeitos e garantir as propriedades desejadas do material. A complexidade dessas operações exige um alto nível de conhecimento técnico e atenção meticulosa aos detalhes, o que pode ser um desafio para organizações sem experiência prévia em técnicas avançadas de sinterização.
Formação especializada
Dada a natureza técnica do SPS, o pessoal envolvido na operação e manutenção do equipamento deve receber formação especializada. Esta formação deve abranger não só a operação básica do sistema SPS, mas também tópicos avançados como a otimização do processo, resolução de problemas e protocolos de segurança. O custo e o tempo necessários para esta formação podem ser significativos, atrasando potencialmente a implementação da tecnologia SPS.
Estratégias para superar os desafios
Para ultrapassar estes desafios, as organizações podem adotar várias estratégias:
-
Investimento em equipamentos de alta qualidade: Embora o custo inicial seja elevado, o investimento em equipamento SPS fiável e de alta qualidade pode reduzir os custos operacionais e de manutenção a longo prazo. A escolha de equipamento de fabricantes de renome com fortes redes de apoio e de serviços também pode ajudar a mitigar os problemas que surgem durante o funcionamento.
-
Colaboração e parcerias: A parceria com instituições de investigação ou outras empresas com experiência em SPS pode fornecer informações e apoio valiosos. Os projectos de colaboração podem ajudar a partilhar os custos e os conhecimentos necessários para uma implementação bem sucedida.
-
Formação e desenvolvimento contínuos: Investir na formação contínua do pessoal pode garantir que este se mantém atualizado com as mais recentes técnicas e melhores práticas em SPS. Isto pode ser conseguido através de workshops, cursos online e sessões de formação prática.
-
Otimização dos processos: O desenvolvimento de processos robustos, bem documentados e normalizados pode ajudar a reduzir a variabilidade e a melhorar a consistência dos resultados. Isto envolve uma experimentação e validação cuidadosas para identificar as condições ideais para cada material e aplicação.
-
Foco na Investigação e Desenvolvimento: O envolvimento em investigação e desenvolvimento contínuos pode ajudar as organizações a manterem-se na vanguarda da tecnologia SPS. Isto pode envolver a exploração de novos materiais, a otimização de processos existentes e o desenvolvimento de aplicações inovadoras para componentes produzidos por SPS.
Conclusão
Embora a implementação da tecnologia SPS apresente vários desafios, estes podem ser geridos de forma eficaz com as estratégias e investimentos correctos. Ao abordar os custos elevados, as complexidades operacionais e os requisitos de formação, as organizações podem desbloquear todo o potencial da SPS, levando a avanços significativos na ciência e fabrico de materiais.
Tendências futuras na sinterização por plasma de faísca
A tecnologia Spark Plasma Sintering (SPS), conhecida pelas suas capacidades de sinterização rápida a temperaturas relativamente baixas, continua a evoluir, oferecendo avanços significativos em termos de eficiência, escalabilidade e diversidade de aplicações. À medida que a procura de novos materiais e processos de fabrico eficientes cresce, a SPS está na vanguarda da inovação tecnológica na ciência dos materiais.
Melhorias na eficiência
Uma das principais áreas de foco da tecnologia SPS é o aumento da sua eficiência. Os métodos tradicionais de sinterização podem consumir muito tempo e energia, enquanto a SPS reduz significativamente o tempo de processamento e o consumo de energia. Os desenvolvimentos futuros visam otimizar ainda mais estes aspectos, aperfeiçoando as técnicas de corrente de impulso e melhorando os sistemas de controlo dos dispositivos SPS. Por exemplo, os avanços na fonte de alimentação e nos sistemas de controlo poderão permitir um controlo mais preciso da temperatura e da pressão, conduzindo a processos de sinterização mais eficientes.
Melhorias na escalabilidade
A escalabilidade é outro aspeto crítico da tecnologia SPS. Atualmente, a SPS é predominantemente utilizada em laboratórios e na produção em pequena escala. No entanto, para satisfazer as exigências industriais, os futuros sistemas SPS terão de lidar com volumes maiores e formas mais complexas. Os investigadores estão a explorar novos materiais e designs de moldes que possam suportar pressões e temperaturas mais elevadas, garantindo a integridade e a reutilização dos moldes. Além disso, a integração de robótica e automação avançadas no equipamento de SPS poderá facilitar a produção de peças maiores e mais complexas, tornando a SPS uma opção viável para o fabrico de grandes volumes.
Expansão para novos tipos de materiais e indústrias
A tecnologia SPS tem sido tradicionalmente utilizada para a sinterização de metais e cerâmicas. No entanto, as suas capacidades únicas oferecem um potencial de expansão para novos tipos de materiais e indústrias. É provável que a investigação futura se concentre na aplicação da SPS a uma gama mais vasta de materiais, incluindo polímeros, compósitos e nanomateriais. Esta expansão poderá abrir novas aplicações em sectores como a eletrónica, a indústria aeroespacial e a engenharia biomédica, onde o controlo preciso das propriedades dos materiais é crucial.
Benefícios ambientais e económicos
Os benefícios ambientais e económicos da SPS estão também a impulsionar o seu desenvolvimento futuro. O processo de produção energeticamente eficiente e com poucos resíduos da SPS alinha-se com os objectivos globais de sustentabilidade. À medida que as indústrias procuram cada vez mais soluções de fabrico amigas do ambiente, a SPS pode tornar-se um método preferido para produzir materiais de alto desempenho. Além disso, os tempos de processamento reduzidos e os custos de energia mais baixos associados à SPS podem levar a poupanças económicas significativas, tornando-a uma opção atractiva para os fabricantes.
Integração e colaboração tecnológica
Finalmente, o futuro da tecnologia SPS envolverá provavelmente uma maior integração com outras tecnologias de fabrico avançadas e esforços de colaboração em diferentes áreas. Por exemplo, a combinação de SPS com técnicas de fabrico aditivo poderá levar à criação de processos de fabrico híbridos que potenciem os pontos fortes de ambas as tecnologias. Além disso, a investigação interdisciplinar envolvendo a ciência dos materiais, a engenharia eléctrica e a engenharia mecânica poderá conduzir a avanços na compreensão e otimização do processo SPS.
Concluindo, o futuro da sinterização por plasma de faísca é promissor, com potenciais avanços preparados para torná-la uma tecnologia mais eficiente, escalável e versátil. À medida que a investigação e o desenvolvimento continuam, a SPS poderá revolucionar a forma como produzimos materiais avançados, contribuindo para inovações em várias indústrias e promovendo práticas de fabrico sustentáveis.
Conclusão: O papel da SPS na formação da ciência dos materiais
Em conclusão, aSpark Plasma Sintering (SPS) destaca-se como uma tecnologia transformadora no domínio da ciência dos materiais. A sua capacidade de sinterizar rapidamente materiais a níveis de grão fino, juntamente com a sua eficiência e versatilidade, posiciona a SPS como uma pedra angular no processamento moderno de materiais. Ao olharmos para o futuro, a SPS está pronta para impulsionar inovações significativas, expandindo as suas aplicações em várias indústrias e abrindo caminho para o desenvolvimento de materiais avançados e de alto desempenho. A evolução e a adoção contínuas da tecnologia SPS irão, sem dúvida, moldar o futuro da ciência dos materiais, oferecendo novas possibilidades e soluções para desafios materiais complexos.
CONTACTE-NOS PARA UMA CONSULTA GRATUITA
Os produtos e serviços da KINTEK LAB SOLUTION foram reconhecidos por clientes de todo o mundo. A nossa equipa terá todo o prazer em ajudar com qualquer questão que possa ter. Contacte-nos para uma consulta gratuita e fale com um especialista de produto para encontrar a solução mais adequada para as suas necessidades de aplicação!