O revestimento de um forno de indução é um componente crítico feito de materiais refractários, concebido para conter o metal fundido, isolá-lo da estrutura exterior do forno e proteger o corpo do forno durante o funcionamento.É essencial para manter a eficiência e a longevidade do forno, especialmente ao fundir metais como o alumínio, que requerem revestimentos especializados devido à sua alta frequência, vibração e penetrabilidade.A qualidade do revestimento tem um impacto direto no desempenho do forno e a sua vida útil é medida pelo número de ciclos de calor que pode suportar antes de necessitar de reparação ou substituição.
Pontos-chave explicados:
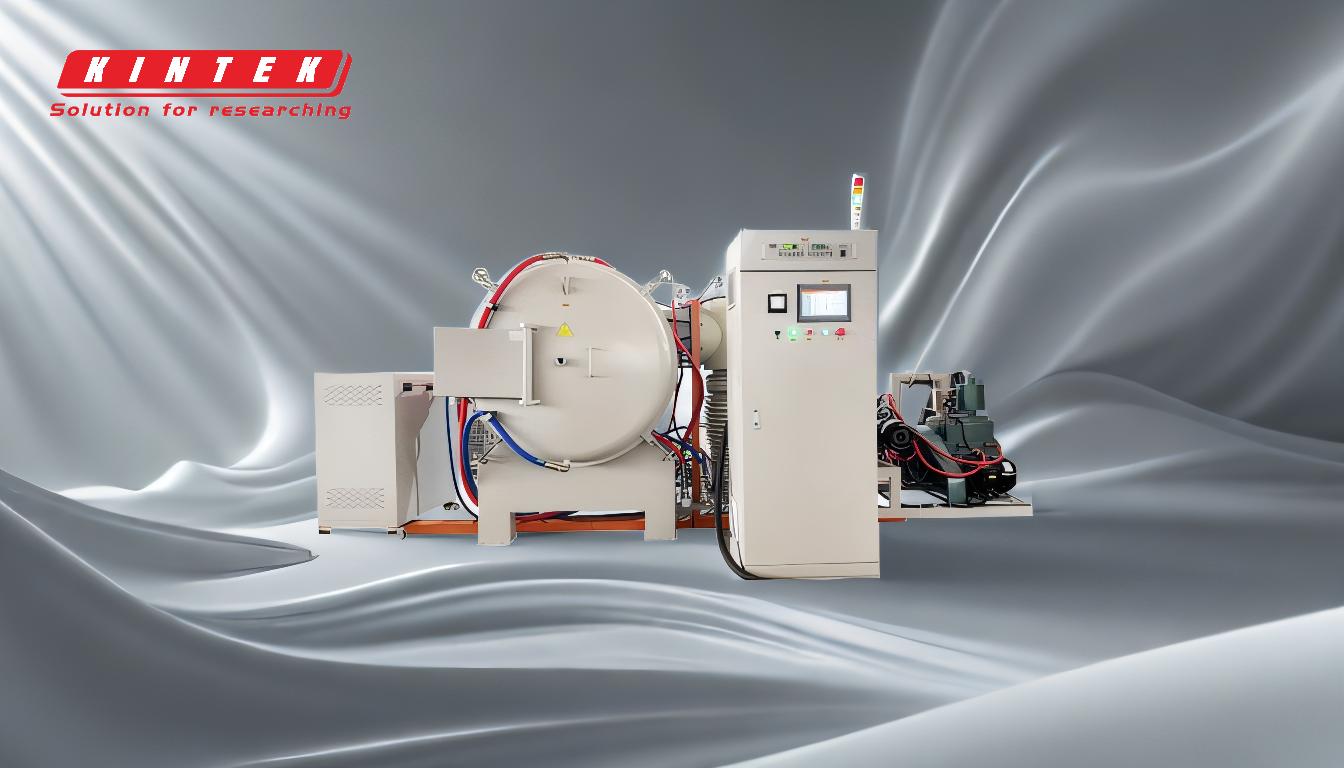
-
Objetivo do revestimento:
- Contenção de metal fundido:O principal papel do revestimento é manter o metal fundido firmemente dentro do cadinho, evitando fugas e garantindo um funcionamento seguro.
- Isolamento da estrutura exterior:O revestimento actua como uma barreira, impedindo o contacto direto entre o metal fundido e os componentes exteriores do forno, como a bobina de indução, que de outra forma poderiam ser danificados.
- Proteção do corpo do forno:Ao isolar o corpo do forno de temperaturas extremas e reacções químicas, o revestimento prolonga a vida operacional do forno.
-
Composição e materiais:
- Materiais refractários:O revestimento é normalmente feito de materiais refractários de alta qualidade que podem resistir a temperaturas extremas e à corrosão química.Estes materiais são escolhidos com base no tipo de metal que está a ser fundido.
- Revestimentos especializados para alumínio:Devido às propriedades únicas do alumínio (alta frequência, vibração e penetrabilidade), são necessários revestimentos especiais para os fornos de fusão de alumínio.Estes revestimentos são concebidos para suportar mais de 300 ciclos de calor.
-
Importância nos fornos de indução:
- Componente crítico:O revestimento é considerado a parte mais importante do forno de indução, uma vez que a sua qualidade afecta diretamente a eficiência do forno e a qualidade do metal fundido.
- Vida útil:O tempo de vida do revestimento, conhecido como vida útil do revestimento, é uma métrica de desempenho fundamental.Indica o número de ciclos de calor que o revestimento pode suportar antes de se degradar e necessitar de reparação ou substituição.
-
Degradação e manutenção:
- Degradação ao longo do tempo:Os revestimentos refractários degradam-se devido a tensões térmicas, reacções químicas e desgaste mecânico.A monitorização e a manutenção regulares são essenciais para garantir um desempenho ótimo.
- Reparação e substituição:Quando o revestimento chega ao fim da sua vida útil, deve ser reparado ou substituído para manter a eficiência e a segurança do forno.
-
Impacto na eficiência da produção:
- Qualidade do revestimento:Um revestimento de alta qualidade garante um funcionamento suave, reduz o tempo de paragem e melhora a eficiência global do processo de produção.
- Considerações sobre os custos:Embora os revestimentos de alta qualidade possam ter um custo inicial mais elevado, oferecem um melhor desempenho e uma vida útil mais longa, o que conduz a uma poupança de custos a longo prazo.
Em resumo, o revestimento de um forno de indução é um componente vital que garante a fusão segura e eficiente de metais.A sua conceção, seleção de material e manutenção são cruciais para alcançar um desempenho ótimo do forno e prolongar a sua vida operacional.
Tabela de resumo:
Aspeto-chave | Detalhes |
---|---|
Objetivo | Contém o metal fundido, isola-o da estrutura exterior e protege o corpo do forno. |
Materiais | Materiais refractários de alta qualidade; revestimentos especializados para alumínio. |
Importância | Crítico para a eficiência do forno, qualidade do metal fundido e vida útil do revestimento. |
Degradação e manutenção | Degrada-se devido a stress térmico, reacções químicas; requer manutenção regular. |
Impacto na produção | Os revestimentos de alta qualidade reduzem o tempo de inatividade, melhoram a eficiência e poupam custos. |
Optimize o desempenho do seu forno com o revestimento certo. contacte os nossos especialistas hoje !