A pulverização catódica é uma técnica de deposição física de vapor (PVD) utilizada para depositar películas finas de materiais em substratos.Envolve a criação de um plasma através da aplicação de uma alta tensão a um material alvo numa câmara de vácuo cheia de um gás inerte, normalmente árgon.O plasma ioniza os átomos do gás, que depois colidem com o material alvo, ejectando átomos ou moléculas da sua superfície.Estas partículas ejectadas viajam através do vácuo e depositam-se num substrato, formando uma película fina.A pulverização catódica é amplamente utilizada em indústrias como a dos semicondutores, ótica e revestimentos, devido à sua capacidade de produzir películas uniformes e de alta qualidade a temperaturas relativamente baixas, o que a torna adequada para materiais sensíveis ao calor.
Pontos-chave explicados:
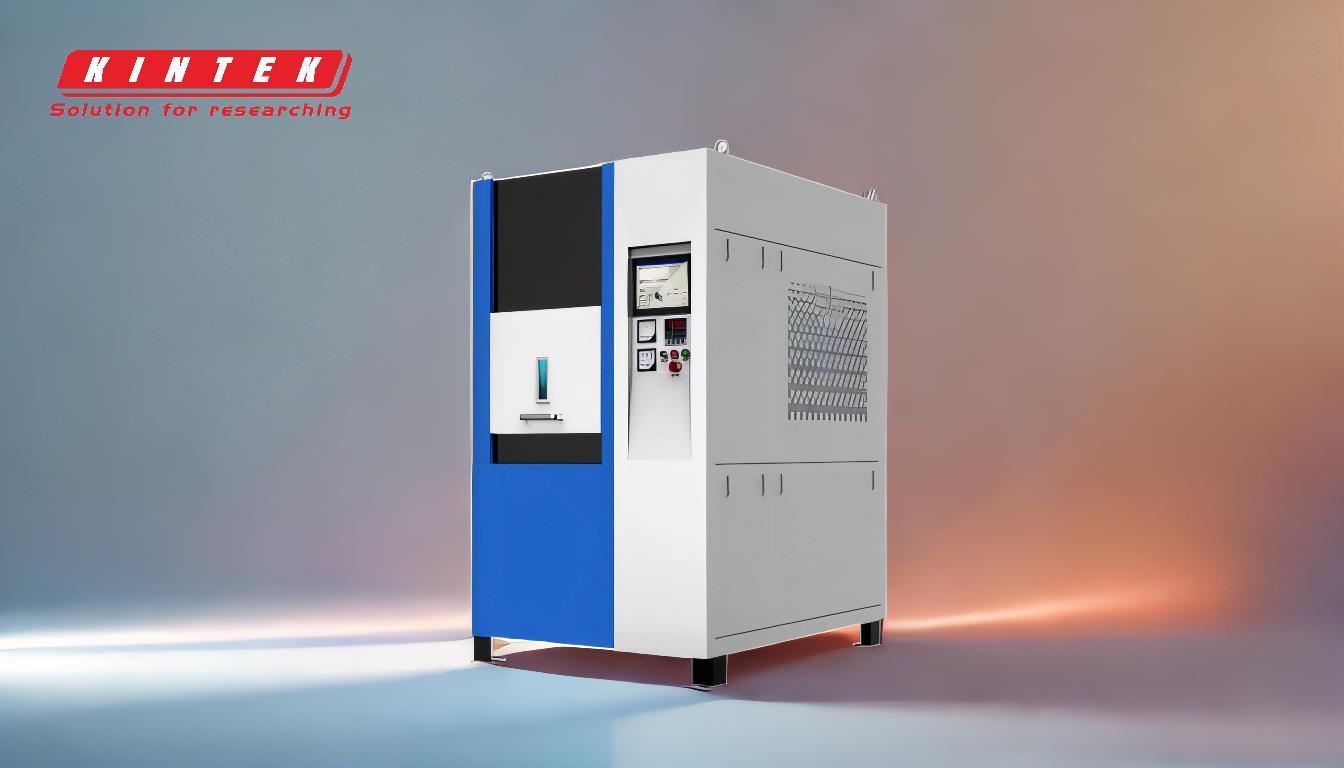
-
Princípio básico da pulverização catódica:
- A pulverização catódica é um processo em que os átomos são ejectados de um material alvo sólido devido ao bombardeamento por iões de alta energia.
- O material alvo é colocado numa câmara de vácuo e é introduzido um gás inerte (normalmente árgon).
- É aplicada uma alta tensão entre o alvo (cátodo) e a câmara, criando um plasma.
- O plasma ioniza os átomos do gás, que são então acelerados em direção ao alvo, provocando colisões que ejectam os átomos do alvo.
-
Papel do plasma na pulverização catódica:
- O plasma é um gás parcialmente ionizado que contém electrões livres, iões e átomos neutros.
- Na pulverização catódica, o plasma é gerado pela aplicação de uma alta tensão, que ioniza o gás inerte.
- Os iões de gás carregados positivamente são atraídos para o alvo carregado negativamente, onde colidem e transferem o momento para os átomos do alvo, ejectando-os.
-
Deposição de películas finas:
- Os átomos ejectados do alvo viajam através do vácuo e depositam-se num substrato colocado no lado oposto ao alvo.
- Os átomos depositados formam uma película fina sobre o substrato, camada a camada.
- Este processo é altamente controlável, permitindo uma espessura e uniformidade precisas da película.
-
Vantagens do Sputtering:
- Processo a baixa temperatura:A pulverização catódica pode ser efectuada a baixas temperaturas, o que a torna adequada para substratos sensíveis ao calor, como os plásticos.
- Filmes de alta qualidade:As películas produzidas são densas, uniformes e têm boa aderência ao substrato.
- Versatilidade:Uma vasta gama de materiais, incluindo metais, ligas e cerâmicas, pode ser depositada por pulverização catódica.
-
Tipos de pulverização catódica:
- Sputtering DC:Utiliza uma fonte de alimentação de corrente contínua (DC) para criar o plasma.Adequado para materiais condutores.
- Sputtering RF:Utiliza energia de radiofrequência (RF) para pulverizar materiais não condutores.
- Sputterização por magnetrão:Incorpora campos magnéticos para aumentar a densidade do plasma, aumentando a taxa de pulverização e a eficiência.
-
Aplicações da pulverização catódica:
- Indústria de semicondutores:Utilizados para depositar películas finas de metais, óxidos e nitretos no fabrico de circuitos integrados.
- Revestimentos ópticos:Utilizados para criar revestimentos antirreflexo, reflectores e protectores em lentes e espelhos.
- Revestimentos decorativos:Utilizado para aplicar películas finas de metais e ligas para fins decorativos em produtos como relógios e jóias.
- Revestimentos duros:Utilizado para depositar revestimentos resistentes ao desgaste em ferramentas e componentes.
-
Re-Sputtering:
- Nalguns casos, o material depositado pode ser novamente pulverizado, em que os átomos depositados são novamente bombardeados, levando a um maior refinamento ou modificação da película.
- Este processo pode melhorar a qualidade e as propriedades da película depositada.
-
Transferência de momento em Sputtering:
- O mecanismo chave na pulverização catódica é a transferência de momento dos iões de alta energia para os átomos alvo.
- Esta transferência de momento faz com que os átomos alvo sejam ejectados da superfície e se desloquem em direção ao substrato.
-
Ambiente de vácuo:
- A pulverização catódica é efectuada em alto vácuo para evitar a contaminação do ar ou de outros gases.
- O vácuo também assegura que as partículas pulverizadas viajam em linhas rectas até ao substrato, resultando numa deposição uniforme.
-
Compatibilidade com o substrato:
- A pulverização catódica é compatível com uma vasta gama de substratos, incluindo metais, vidro, cerâmica e polímeros.
- A natureza de baixa temperatura do processo permite o revestimento de materiais sensíveis ao calor sem danos.
Em resumo, a pulverização catódica é uma técnica de deposição de película fina versátil e amplamente utilizada que se baseia na ejeção de átomos alvo devido ao bombardeamento iónico.O processo é realizado num ambiente de vácuo, utiliza plasma para ionizar o gás inerte e deposita películas de alta qualidade em vários substratos.As suas aplicações abrangem várias indústrias, tornando-o uma tecnologia crítica no fabrico moderno e na ciência dos materiais.
Quadro de síntese:
Aspeto | Detalhes |
---|---|
Princípio básico | Átomos ejectados de um material alvo por bombardeamento iónico de alta energia. |
Papel do plasma | O plasma ioniza o gás inerte, acelerando os iões para colidirem com o alvo. |
Processo de deposição | Os átomos ejectados depositam-se nos substratos, formando películas finas e uniformes. |
Vantagens | Baixa temperatura, películas de alta qualidade, compatibilidade versátil de materiais. |
Tipos de pulverização | Pulverização catódica DC, RF e Magnetron para diferentes materiais e aplicações. |
Aplicações | Semicondutores, revestimentos ópticos, revestimentos decorativos e revestimentos duros. |
Vantagens principais | Adequado para materiais sensíveis ao calor e controlo preciso da espessura da película. |
Descubra como a pulverização catódica pode melhorar o seu processo de fabrico contacte os nossos especialistas hoje !