O processo de recozimento, embora amplamente utilizado na metalurgia e na ciência dos materiais para melhorar as propriedades dos metais e ligas, tem várias limitações.Estas incluem restrições relacionadas com o controlo da temperatura, requisitos de tempo, desafios específicos do material, consumo de energia e potencial de oxidação da superfície.Além disso, o processo pode nem sempre atingir as propriedades desejadas do material devido a complexidades microestruturais ou a uma seleção incorrecta dos parâmetros.Compreender estas limitações é crucial para otimizar o processo de recozimento e garantir os resultados desejados para aplicações específicas.
Pontos-chave explicados:
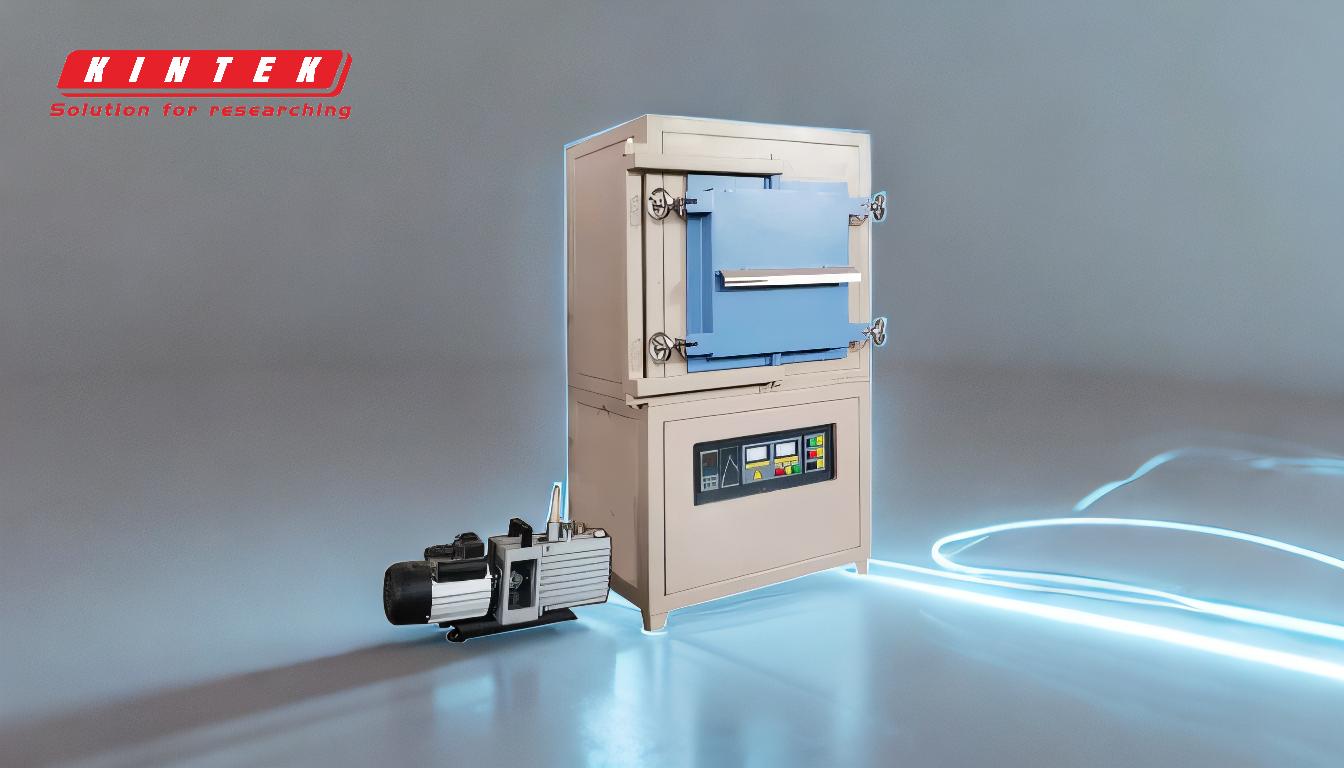
-
Desafios do controlo da temperatura:
- Requisitos de precisão:O recozimento requer um controlo preciso da temperatura para atingir as propriedades desejadas do material.Pequenos desvios podem levar a uma recristalização incompleta ou a problemas de crescimento de grãos.
- Limitações do equipamento:Nem todos os fornos conseguem manter temperaturas uniformes em peças de trabalho grandes ou complexas, o que leva a resultados inconsistentes.
- Sensibilidade do material:Alguns materiais, como os aços com elevado teor de carbono ou certas ligas, têm intervalos de temperatura estreitos para um recozimento eficaz, o que torna o processo mais difícil.
-
Restrições de tempo:
- Tempos de processamento longos:O recozimento requer frequentemente ciclos prolongados de aquecimento e arrefecimento, o que pode ser moroso e ineficaz para a produção de grandes volumes.
- Sensibilidade da taxa de arrefecimento:Para alguns materiais, são necessárias taxas de arrefecimento lentas para evitar tensões internas, mas isto pode prolongar ainda mais os tempos de processamento.
-
Limitações específicas do material:
- Microestruturas não uniformes:Os materiais com composições heterogéneas ou com antecedentes de processamento podem não responder uniformemente ao recozimento.
- Problemas de crescimento de grão:O recozimento excessivo pode levar a um crescimento excessivo do grão, reduzindo a resistência e a tenacidade do material.
- Aplicabilidade limitada:Alguns materiais, como os compósitos não metálicos ou as cerâmicas, não beneficiam significativamente do recozimento.
-
Consumo de energia:
- Elevadas necessidades energéticas:A manutenção de temperaturas elevadas durante períodos prolongados consome energia significativa, tornando o processo dispendioso e menos amigo do ambiente.
- Ineficiência no processamento em lote:O recozimento por lotes, embora comum, é menos eficiente em termos energéticos do que os processos de recozimento contínuos.
-
Oxidação da superfície e descarbonetação:
- Riscos de oxidação:A exposição a altas temperaturas na presença de oxigénio pode levar à oxidação da superfície, degradando a qualidade do material.
- Descarbonetação:Nos aços, o aquecimento prolongado pode provocar a perda de carbono da superfície, reduzindo a dureza e a resistência ao desgaste.
-
Complexidade do processo e requisitos de competências:
- Otimização de parâmetros:A seleção da temperatura, tempo e taxa de arrefecimento corretos para o recozimento requer conhecimento e experimentação.
- Tratamentos pós-recozimento:Podem ser necessários processos adicionais, como a têmpera ou o revenido, para obter as propriedades desejadas, o que aumenta a complexidade.
-
Restrições económicas e práticas:
- Custo do equipamento:A aquisição e manutenção de fornos de recozimento e sistemas de controlo de temperatura de alta qualidade podem ser dispendiosas.
- Requisitos de espaço:As operações de recozimento em grande escala requerem um espaço significativo, o que pode não ser viável para instalações mais pequenas.
-
Resultados inconsistentes:
- Variabilidade na resposta do material:Mesmo com parâmetros controlados, variações na composição do material ou no processamento anterior podem levar a resultados inconsistentes.
- Erro humano:O controlo manual dos processos de recozimento aumenta o risco de erros, tais como ajustes incorrectos da temperatura ou do tempo.
-
Melhoria limitada para determinadas propriedades:
- Compensações de dureza e resistência:O recozimento reduz frequentemente a dureza e a resistência para melhorar a ductilidade, o que pode não ser desejável para todas as aplicações.
- Impacto limitado nos defeitos:Embora o recozimento possa reduzir as tensões internas, pode não eliminar todos os defeitos, tais como vazios ou inclusões.
-
Preocupações ambientais e de segurança:
- Calor e emissões:Os processos a alta temperatura geram calor e emissões, exigindo uma ventilação adequada e medidas de segurança.
- Segurança dos trabalhadores:O manuseamento de materiais quentes e o funcionamento de equipamento a alta temperatura representam riscos de segurança.
Ao compreender estas limitações, os fabricantes e engenheiros podem conceber melhor os processos de recozimento, selecionar materiais adequados e implementar tratamentos complementares para obter resultados óptimos.
Tabela de resumo:
Categoria de limitação | Principais desafios |
---|---|
Controlo da temperatura | Requisitos de precisão, limitações do equipamento, sensibilidade do material |
Restrições de tempo | Tempos de processamento longos, sensibilidade à taxa de arrefecimento |
Questões específicas do material | Microestruturas não uniformes, crescimento de grão, aplicabilidade limitada |
Consumo de energia | Elevados requisitos de energia, ineficiência no processamento em lote |
Oxidação da superfície | Riscos de oxidação, descarbonetação em aços |
Complexidade do processo | Otimização de parâmetros, tratamentos pós-cozimento |
Restrições económicas | Custo do equipamento, requisitos de espaço |
Resultados inconsistentes | Variabilidade na resposta do material, erro humano |
Melhoria limitada das propriedades | Compensações entre dureza e resistência, eliminação limitada de defeitos |
Preocupações ambientais | Calor e emissões, riscos para a segurança dos trabalhadores |
Precisa de ajuda para otimizar o seu processo de recozimento? Contacte hoje mesmo os nossos especialistas para soluções à medida!