Os fornos de indução, embora altamente eficientes e versáteis na fusão de metais, apresentam várias desvantagens notáveis.Uma das principais desvantagens é a sua falta de capacidade de refinação, o que significa que os materiais de carga já devem estar livres de óxidos e ter uma composição conhecida.Além disso, certos elementos de liga podem perder-se devido à oxidação durante o processo de fusão, sendo necessária a sua re-adição.Estas limitações podem aumentar a complexidade e os custos operacionais.Abaixo, exploramos estas e outras desvantagens em pormenor.
Pontos-chave explicados:
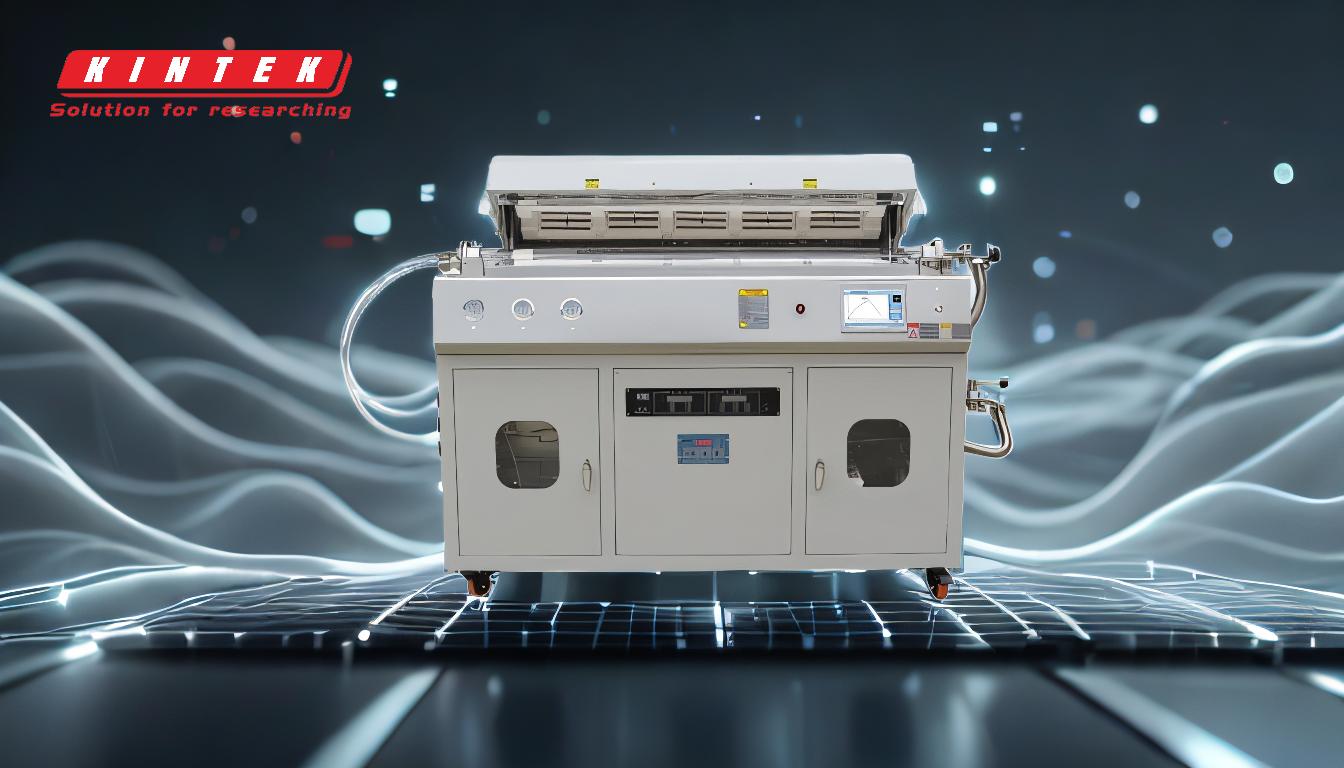
-
Falta de capacidade de refinação
- Os fornos de indução não têm a capacidade de refinar o metal durante o processo de fusão.Isto significa que os materiais de carga devem estar limpos, livres de óxidos e com uma composição conhecida antes de serem introduzidos no forno.
- Para as indústrias que requerem metais de elevada pureza, esta limitação pode ser uma desvantagem significativa, uma vez que necessita de passos adicionais de pré-processamento para garantir a qualidade dos materiais de carga.
-
Oxidação e perda de elementos de liga
- Durante o processo de fusão, certos elementos de liga, como o magnésio, o alumínio e o silício, podem oxidar e perder-se da fusão.
- Isto exige que os operadores monitorizem cuidadosamente a composição da fusão e voltem a adicionar estes elementos, o que pode aumentar os custos do material e o tempo de processamento.
-
Dependência da qualidade do material de carga
- Uma vez que os fornos de indução dependem da qualidade dos materiais de carga, quaisquer impurezas ou inconsistências na matéria-prima podem afetar diretamente o produto final.
- Isto torna difícil a utilização de sucata ou materiais reciclados sem uma seleção e preparação minuciosas, o que pode aumentar os custos operacionais.
-
Investimento inicial e custos operacionais elevados
- Os fornos de indução, particularmente os que utilizam tecnologias avançadas como fornos de indução IGBT requerem um investimento inicial significativo.
- Além disso, os custos operacionais, incluindo o consumo de eletricidade e a manutenção, podem ser mais elevados em comparação com outros tipos de fornos.
-
Capacidade limitada para produção em grande escala
- Os fornos de indução são normalmente mais adequados para operações em pequena escala ou produção em lotes.Para a produção contínua em grande escala, outros tipos de fornos, como os fornos de arco, podem ser mais eficientes.
- Esta limitação pode tornar os fornos de indução menos adequados para as indústrias que exigem uma produção de grande volume.
-
Complexidade no controlo da temperatura
- Embora os fornos de indução ofereçam um controlo preciso da temperatura, a manutenção de temperaturas consistentes ao longo da fusão pode ser um desafio, especialmente para fornos maiores.
- As variações de temperatura podem levar a inconsistências no produto final, exigindo uma monitorização e ajuste cuidadosos.
-
Suscetibilidade a problemas de alimentação eléctrica
- Os fornos de indução são altamente dependentes de uma fonte de alimentação estável e fiável.Quaisquer flutuações ou interrupções na energia podem perturbar o processo de fusão e danificar potencialmente o forno.
- Isto torna-os menos adequados para áreas com infra-estruturas de eletricidade pouco fiáveis.
-
Flexibilidade limitada para determinados metais
- Embora os fornos de indução sejam versáteis, podem não ser ideais para fundir certos metais ou ligas que requerem processos de refinação ou atmosferas específicas.
- Por exemplo, os metais que requerem vácuo ou ambientes de gás inerte podem não ser adequados para fornos de indução padrão.
-
Manutenção e desgaste dos componentes
- Os componentes de um forno de indução, como o cadinho e as bobinas, estão sujeitos a desgaste ao longo do tempo.
- É necessária uma manutenção regular para garantir um desempenho ótimo, e a substituição destes componentes pode ser dispendiosa.
-
Preocupações ambientais e de segurança
- Os fornos de indução geram campos electromagnéticos, que podem representar riscos de segurança para os operadores se não estiverem devidamente protegidos.
- Além disso, o processo de fusão pode produzir fumos e emissões, exigindo ventilação e controlos ambientais adequados.
Em resumo, embora os fornos de indução ofereçam muitas vantagens, como a eficiência energética e o controlo preciso da temperatura, as suas desvantagens - incluindo a falta de capacidade de refinação, a oxidação de elementos de liga e os elevados custos operacionais - devem ser cuidadosamente consideradas ao selecionar um forno para aplicações específicas.Para as indústrias que exigem metais de elevada pureza ou produção em grande escala, podem ser mais adequados tipos de fornos alternativos.
Tabela de resumo:
Desvantagem | Descrição |
---|---|
Falta de capacidade de refinação | Não é possível refinar metais; requer materiais de carga limpos e sem óxidos. |
Oxidação de elementos de liga | Perda de elementos como o magnésio, o alumínio e o silício durante a fusão. |
Dependência da qualidade da carga | As impurezas na matéria-prima afectam a qualidade do produto final. |
Custos iniciais e operacionais elevados | Investimento significativo e custos de eletricidade/manutenção mais elevados. |
Capacidade limitada em grande escala | Mais adequado para produção em pequena escala ou em lotes, não para produção contínua em grande escala. |
Controlo de temperatura complexo | Difícil de manter temperaturas consistentes em fornos maiores. |
Sensibilidade da fonte de alimentação | Requer energia estável; as interrupções podem afetar as operações. |
Flexibilidade limitada do metal | Não é ideal para metais que requerem refinação específica ou atmosferas controladas. |
Desgaste e manutenção dos componentes | É necessária uma manutenção regular e substituições dispendiosas de componentes. |
Riscos ambientais e de segurança | Os campos electromagnéticos e os fumos requerem uma proteção e ventilação adequadas. |
Precisa de ajuda para escolher o forno certo para as suas necessidades? Contacte os nossos especialistas hoje para um aconselhamento personalizado!