A porosidade na metalurgia do pó é um fator crítico que afecta as propriedades mecânicas e o desempenho do produto final.A redução da porosidade pode ser conseguida através da otimização de vários parâmetros-chave durante o processo de fabrico.Estes incluem o aumento da pressão de compactação, da temperatura de sinterização e do tempo de sinterização, que, coletivamente, ajudam a diminuir a porosidade aparente e a aumentar a densidade aparente.Além disso, o controlo do tamanho das partículas é crucial, uma vez que as partículas maiores tendem a aumentar a porosidade.Ao gerir cuidadosamente estes factores, os fabricantes podem produzir componentes de alta densidade e baixa porosidade com propriedades mecânicas melhoradas.
Pontos-chave explicados:
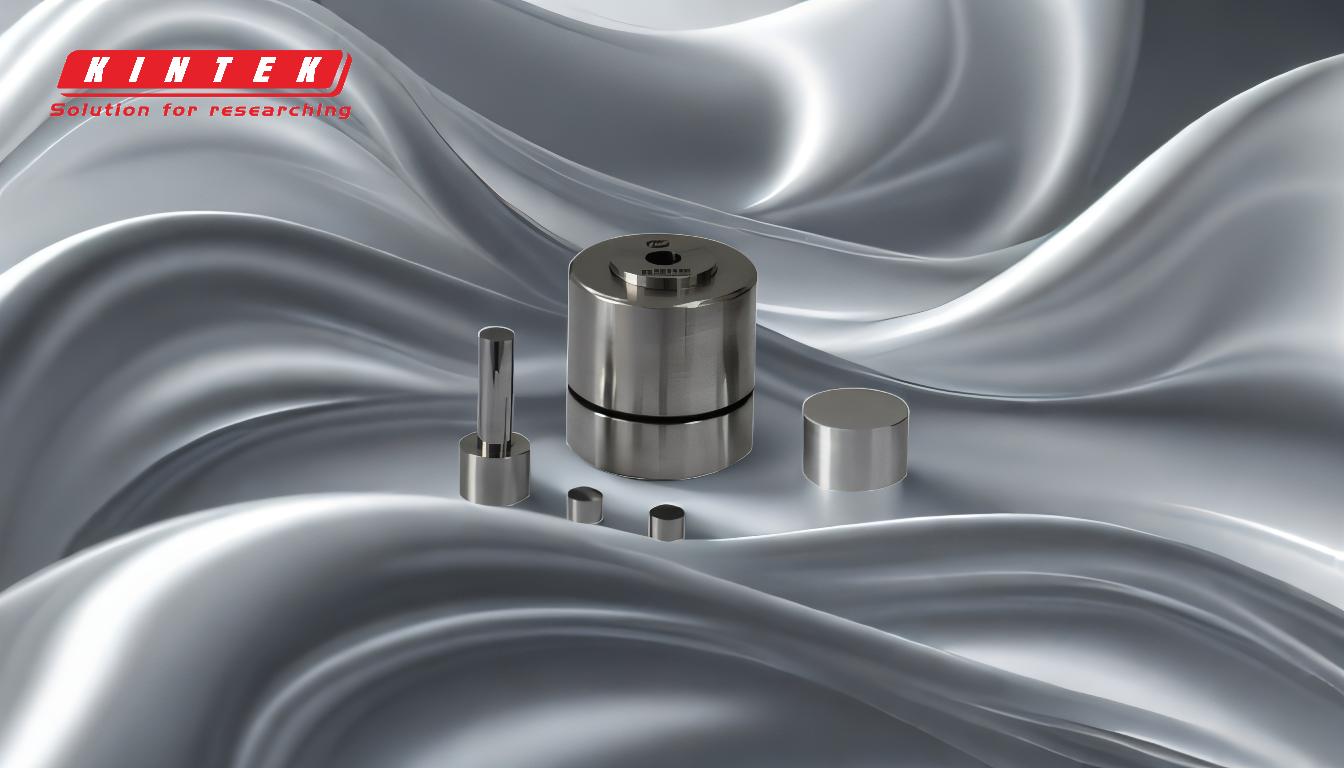
-
Aumentar a pressão de compactação:
- Impacto:Uma pressão de compactação mais elevada reduz os espaços entre as partículas de pó, conduzindo a um compacto mais denso e com menor porosidade.
- Mecanismo:Quando a pressão é aplicada durante a fase de compactação, as partículas são forçadas a aproximar-se umas das outras, minimizando os vazios e aumentando a densidade aparente do compacto verde.
- Considerações práticas:Embora uma pressão mais elevada seja benéfica, deve ser equilibrada com o risco de danificar a matriz ou causar uma distribuição desigual da densidade na peça.
-
Otimização da temperatura e do tempo de sinterização:
- Impacto:Temperaturas de sinterização mais elevadas e tempos de sinterização mais longos promovem uma melhor ligação e difusão das partículas, reduzindo a porosidade e aumentando a densidade.
- Mecanismo:A sinterização envolve o aquecimento do pó compactado abaixo do seu ponto de fusão, permitindo que os átomos se difundam através dos limites das partículas, o que fecha os poros e fortalece o material.
- Considerações práticas:Uma temperatura ou tempo excessivos podem levar ao crescimento ou distorção dos grãos, pelo que é necessária uma otimização cuidadosa.
-
Controlo do tamanho das partículas:
- Impacto:As partículas de menor dimensão resultam geralmente numa menor porosidade, uma vez que se compactam mais eficientemente, deixando menos espaços vazios.
- Mecanismo:As partículas finas têm um rácio área superficial/volume mais elevado, o que melhora a sinterização e a ligação.As partículas maiores, por outro lado, criam mais lacunas e aumentam a porosidade.
- Considerações práticas:Embora as partículas mais pequenas sejam preferíveis, podem também aumentar o risco de aglomeração, que deve ser gerido durante o processamento.
-
Métodos de produção de pó:
- Impacto:O método utilizado para produzir pós metálicos influencia o seu tamanho, forma e distribuição, o que, por sua vez, afecta a porosidade.
- Mecanismo:Técnicas como a atomização produzem pós com intervalos de tamanho controlados, que podem ser adaptados para minimizar a porosidade.A trituração e a moagem podem produzir partículas com formas irregulares que se compactam de forma menos eficiente.
- Considerações práticas:A seleção do método de produção de pó adequado é essencial para obter as caraterísticas desejadas das partículas e minimizar a porosidade.
-
Seleção do material:
- Impacto:A escolha do material de base (por exemplo, base de cobre ou base de ferro) pode influenciar a porosidade devido a diferenças na forma e tamanho das partículas e no comportamento de sinterização.
- Mecanismo:Alguns materiais sinterizam-se mais facilmente do que outros, conduzindo a uma melhor densificação e a uma menor porosidade.
- Considerações práticas:A seleção do material deve estar de acordo com a aplicação pretendida e as propriedades mecânicas desejadas.
Ao abordar estes factores-chave, os fabricantes podem reduzir eficazmente a porosidade na metalurgia do pó, resultando em componentes com maior resistência, durabilidade e desempenho.
Tabela de resumo:
Fator-chave | Impacto | Mecanismo | Considerações práticas |
---|---|---|---|
Aumento da pressão de compactação | Reduz os espaços entre as partículas, conduzindo a compactos mais densos com menor porosidade. | A pressão força as partículas a aproximarem-se, minimizando os espaços vazios e aumentando a densidade aparente. | Equilibrar a pressão para evitar danos na matriz ou uma distribuição desigual da densidade. |
Otimização da temperatura e do tempo de sinterização | Promove a ligação das partículas, reduz a porosidade e aumenta a densidade. | O aquecimento abaixo do ponto de fusão permite a difusão de átomos, fechando os poros e reforçando o material. | Evitar temperaturas ou tempos excessivos para prevenir o crescimento ou a distorção dos grãos. |
Controlo do tamanho das partículas | As partículas mais pequenas são compactadas de forma eficiente, reduzindo a porosidade. | As partículas finas têm uma maior relação área de superfície/volume, melhorando a sinterização e a ligação. | Gerir os riscos de aglomeração com partículas mais pequenas. |
Métodos de produção de pó | Influencia o tamanho, a forma e a distribuição das partículas, afectando a porosidade. | A atomização produz intervalos de tamanho controlados; a trituração/moagem pode criar partículas irregulares. | Selecionar o método correto para obter as caraterísticas desejadas das partículas. |
Seleção do material | O material de base afecta a porosidade devido a diferenças no comportamento de sinterização. | Alguns materiais sinterizam-se mais rapidamente, conduzindo a uma melhor densificação e a uma menor porosidade. | Alinhe a escolha do material com a aplicação e as propriedades mecânicas desejadas. |
Pronto para otimizar o seu processo de metalurgia do pó? Contacte hoje os nossos especialistas para soluções à medida!