Os elementos de aquecimento perdem potência ao longo do tempo devido a vários factores, incluindo a oxidação, o alongamento e as alterações na resistência.Estes factores são influenciados pelas condições de funcionamento, como a temperatura, a atmosfera, a densidade de watts e os padrões de utilização.Ao longo do tempo, a resistência do elemento de aquecimento aumenta, levando a uma redução da potência de saída e a uma eventual falha.Esta é uma parte natural do ciclo de vida do elemento, e os fabricantes têm em conta estas variáveis quando projectam e garantem os seus produtos.
Pontos-chave explicados:
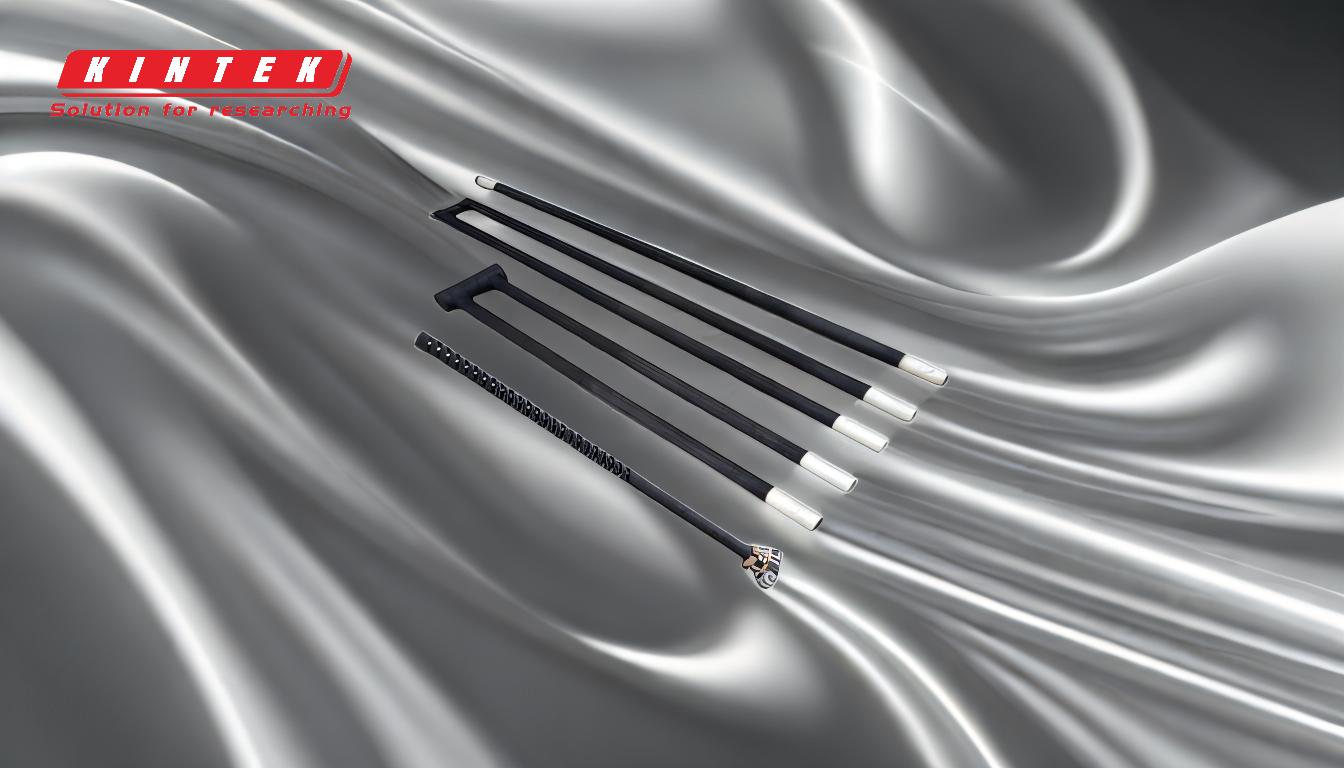
-
A resistência aumenta com o tempo:
- À medida que os elementos de aquecimento envelhecem, a sua resistência aumenta devido à oxidação, que reduz a área da secção transversal do elemento.Este processo de oxidação é inevitável e ocorre mais rapidamente em certos ambientes, tais como atmosferas de alta temperatura ou redutoras.
- Além disso, o alongamento dos laços do elemento de aquecimento contribui para o aumento da resistência.Este alongamento ocorre à medida que o material se expande e contrai durante os ciclos de aquecimento e arrefecimento.
-
Impacto na potência de saída:
- O aumento da resistência afecta diretamente a potência de saída do elemento de aquecimento.De acordo com a Lei de Ohm (P = V²/R), à medida que a resistência (R) aumenta, a potência (P) fornecida ao forno diminui para uma determinada tensão (V).
- Esta redução da potência pode levar a um aquecimento ineficiente e a tempos de ciclo mais longos, afectando, em última análise, o desempenho do forno ou do sistema de aquecimento.
-
Factores que influenciam a vida útil dos elementos:
- Atmosfera do forno:Os elementos que funcionam em atmosferas redutoras ou em ambientes com elevados níveis de oxigénio ou outros gases reactivos tendem a oxidar-se mais rapidamente, encurtando a sua vida útil.
- Densidade em watts:Densidades de watts mais elevadas exercem mais pressão sobre o elemento de aquecimento, acelerando o seu desgaste.
- Temperatura de funcionamento:As temperaturas mais elevadas aumentam a taxa de oxidação e a degradação do material.
- Padrões de utilização:O serviço contínuo ou os ciclos frequentes de aquecimento e arrefecimento podem levar a uma degradação mais rápida em comparação com a utilização intermitente.
- Manutenção:A manutenção regular, como a limpeza e a inspeção dos elementos, pode ajudar a prolongar a sua vida útil, identificando e resolvendo os problemas numa fase precoce.
-
Considerações específicas sobre o material:
- Elementos de carboneto de silício:Estes elementos são particularmente sensíveis à atmosfera do forno e à densidade de watts.A sua esperança de vida é influenciada pelo ambiente de funcionamento e pela frequência dos ciclos térmicos.
- Elementos cerâmicos:As propriedades dos elementos de aquecimento cerâmicos são afectadas pela composição da liga, dimensões, carga de watts e arquitetura do dispositivo.Estes factores determinam a forma como o elemento responde às tensões térmicas e mecânicas ao longo do tempo.
-
Ciclo de vida normal e falha:
- O aumento gradual da resistência e a eventual falha dos elementos de aquecimento são considerados uma parte normal do seu ciclo de vida.Os fabricantes concebem os elementos tendo em conta estes factores e fornecem garantias que cobrem os defeitos de fabrico, mas não o desgaste devido às condições de funcionamento.
- Quando um elemento falha, é normalmente devido a uma combinação de factores, incluindo oxidação, alongamento e aumento da resistência, que coletivamente reduzem a sua potência de saída a um ponto em que já não pode funcionar eficazmente.
-
Estratégias de mitigação:
-
Para prolongar a vida útil dos elementos de aquecimento, os utilizadores podem:
- Utilizar o forno ou o sistema de aquecimento dentro dos limites recomendados de temperatura e densidade de watts.
- Minimizar os ciclos rápidos de aquecimento e arrefecimento.
- Utilizar atmosferas ou revestimentos protectores para reduzir a oxidação.
- Efetuar uma manutenção regular para identificar e resolver problemas antes que estes conduzam a falhas.
-
Para prolongar a vida útil dos elementos de aquecimento, os utilizadores podem:
Em resumo, os elementos de aquecimento perdem potência ao longo do tempo devido ao aumento da resistência causado pela oxidação, alongamento e outros factores operacionais.A compreensão destes factores e a implementação de estratégias para atenuar os seus efeitos podem ajudar a prolongar a vida útil dos elementos de aquecimento e a manter um funcionamento eficiente do forno.
Tabela de resumo:
Factores-chave | Impacto nos elementos de aquecimento |
---|---|
Aumento da resistência | A oxidação e o alongamento reduzem a área da secção transversal, aumentando a resistência e diminuindo a potência. |
Atmosfera do forno | O oxigénio elevado ou os gases reactivos aceleram a oxidação, encurtando a vida útil. |
Densidade de watts | Densidades de watts mais elevadas sobrecarregam os elementos, levando a um desgaste mais rápido. |
Temperatura de funcionamento | As temperaturas mais elevadas aumentam as taxas de oxidação e de degradação do material. |
Padrões de utilização | Os ciclos frequentes de aquecimento/arrefecimento degradam os elementos mais rapidamente do que a utilização intermitente. |
Manutenção | A limpeza e inspeção regulares podem identificar problemas atempadamente, prolongando a vida útil do elemento. |
Precisa de ajuda para manter ou substituir os seus elementos de aquecimento? Contacte os nossos especialistas hoje para soluções à medida!