Compreender o forno de fusão por indução de levitação a vácuo
Explore os componentes de um forno de fusão por indução de levitação a vácuo, incluindo o corpo do forno, a potência de média frequência, o sistema de vácuo, o sistema de arrefecimento e o sistema de controlo elétrico. Saiba como cada elemento contribui para a eficiência e precisão dos processos de fusão de metais.
Os fornos de fusão por indução em vácuo (VIM) evoluíram do processamento especializado de ligas exóticas para uma utilização mais comum em várias indústrias, incluindo a produção de aços inoxidáveis e outros metais. Estes fornos funcionam em condições de vácuo, oferecendo um controlo preciso do processo de fusão.
Como funciona um forno de indução a vácuo?
O material é carregado no forno de indução sob vácuo, onde é aplicada energia para iniciar a fusão. São adicionadas cargas adicionais para atingir a capacidade de fusão desejada. O metal fundido é refinado sob condições de vácuo, com ajustes efectuados para obter uma química de fusão precisa.
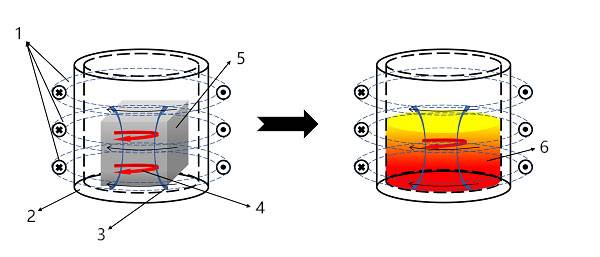
Principais componentes e funções
Para além do corpo do forno e do sistema de vácuo, um forno de fusão por indução a vácuo está equipado com componentes essenciais, tais como uma fonte de alimentação de média frequência, um sistema de controlo elétrico e um sistema de arrefecimento. Estes componentes trabalham em conjunto para fornecer a energia necessária à fusão, evitando o sobreaquecimento e assegurando a integridade estrutural.
Componentes auxiliares como carrinhos de transmissão, mecanismos de porta do forno e janelas de observação podem ser adicionados com base em requisitos específicos do processo. Para aplicações com elevados níveis de impureza, é essencial um sistema de filtragem de gás para manter a pureza do metal.
Vantagens dos fornos de fusão por indução de vácuo
A estrutura compacta dos fornos VIM, com apenas a parte de fusão encerrada na câmara de vácuo, permite um melhor controlo dos níveis de vácuo e tempos de evacuação mais rápidos. Características como a agitação electromagnética asseguram uma mistura uniforme dos elementos adicionados em toda a poça de fusão, mantendo uma temperatura consistente.
A inclusão de deflectores de filtro e outras medidas melhora a pureza do metal, atenuando o impacto das impurezas. A deteção e reparação de fugas de vácuo são simplificadas devido ao menor volume do forno, reduzindo o tempo de paragem para manutenção.
Precisão e controlo
Os fornos de fusão por indução de vácuo oferecem um controlo preciso da temperatura através de sistemas avançados de controlo elétrico. Os utilizadores podem monitorizar o processo de fusão em tempo real, garantindo precisão e consistência. O sistema de arrefecimento centralizado regula as temperaturas de fusão, melhorando o controlo do processo e a qualidade do produto.
Aplicações e flexibilidade
Os fornos VIM estão disponíveis numa gama de tamanhos, desde pequenas unidades adequadas para experiências à escala de gramas até modelos maiores para produção industrial. Esta versatilidade permite aos utilizadores ajustar os tamanhos dos lotes de acordo com as suas necessidades específicas.
Eliminação de gases e prevenção da oxidação
Uma das principais vantagens da fusão por indução a vácuo é a remoção de gases dos metais fundidos. Este processo evita a oxidação rápida, garantindo a pureza e a qualidade do produto final.
Em conclusão, os fornos de fusão por indução de vácuo desempenham um papel vital nos processos modernos de fundição de metais, oferecendo um controlo preciso, maior pureza e flexibilidade na produção.
Eficiência e flexibilidade
Aprofunde-se na gama de fornos de vácuo disponíveis, desde unidades de pequena escala adequadas para lotes de nível grama até fornos maiores que acomodam diversos tamanhos de lotes. Compreenda como esta versatilidade permite aos utilizadores otimizar os processos de produção.
Automação e controlo avançados:
Os nossos fornos de vácuo estão equipados com sistemas avançados de automação e controlo, permitindo-lhe uma gestão precisa do processo e capacidades de monitorização. A nossa interface de fácil utilização permite-lhe programar e ajustar sem esforço vários parâmetros, garantindo um desempenho e uma eficiência óptimos. Com dados e diagnósticos em tempo real, pode tomar decisões informadas, detetar anomalias e otimizar os seus processos de produção para obter o máximo rendimento.
Eficiência energética e sustentabilidade:
Designs de vácuo
Os fornos de vácuo para processamento a baixa temperatura podem ser descontínuos ou contínuos, autónomos, integrados em sistemas de fornos de vácuo contínuos ou um "módulo" separado incorporado num sistema celular. Por exemplo, o funcionamento básico de um forno de vácuo descontínuo é o seguinte:
- Bombas de vácuo mecânicas, opcionalmente equipadas com ventiladores, produzem níveis de vácuo até 1,3 x 10-3 mbar (0,001 torr) com 6,7 x 10-3 mbar (0,005 torr) comum. Este valor é normalmente alcançado num período de 10 a 30 minutos após o início do ciclo, dependendo da dimensão dos sistemas de bombagem e da natureza de quaisquer contaminantes presentes na carga de trabalho.
- A unidade é então enchida na gama de 66,7 x 101 mbar (500 torr) de pressão negativa a 0,10 bar (1,5 psig) de pressão positiva com um gás inerte, como o azoto, o árgon ou uma mistura de azoto/hidrogénio (máximo de 3%), e inicia-se o aquecimento.
- Os ciclos duplos de bombagem são frequentemente considerados vantajosos para acelerar o tempo total do ciclo. Depois de atingir o ponto de referência e a temperatura de imersão, o ciclo de arrefecimento é iniciado.
Características do forno a vácuo
Os fornos a vácuo KinTek oferecem um controlo preciso da temperatura, uma excelente uniformidade de temperatura e uma vasta gama de aplicações para laboratórios, universidades e qualquer aplicação de produção em pequena escala utilizando modelos de fornos industriais.
Cada forno a vácuo padrão e personalizado oferece as seguintes características e benefícios:
- Excelente precisão e uniformidade de temperatura
- Isolamento de fibra cerâmica com eficiência energética
- Função de segurança de desligamento automático
Fornos de vácuo personalizados
Obtenha um forno a vácuo de alta temperatura construído especificamente para atender às suas necessidades de aplicação. Os representantes experientes e bem informados da KinTek podem ajudá-lo a projetar ou construir um forno personalizado para atender às suas especificações exatas ou necessidades de aplicação.
Esta gama abrangente de características e opções garante que os nossos fornos de vácuo fornecem a eficiência e a flexibilidade necessárias para uma grande variedade de aplicações de laboratório e de produção em pequena escala.
Controlo preciso da temperatura
Descubra como o sistema de controlo elétrico dos fornos de fusão por indução a vácuo assegura um controlo preciso da temperatura ao longo do processo de fusão. Explore o papel do sistema de arrefecimento na manutenção de temperaturas de fusão óptimas e na prevenção da oxidação.
O aquecimento indutivo é um processo em que as correntes de Foucault induzidas aquecem materiais condutores. Este aquecimento pode ser utilizado para fundir metais e produzir ligas. A fusão por indução no vácuo oferece uma combinação atraente de uma atmosfera controlada (vácuo ou gás inerte) e um controlo preciso do processo de fusão.
Descrição do forno de sinterização por vácuo
Um forno de sinterização por vácuo é um tipo de forno onde os artigos aquecidos são submetidos a sinterização num ambiente de vácuo. Este forno é crucial em vários processos industriais, particularmente na metalurgia do pó.
O processo de sinterização é muito sensível às variações de temperatura. Um desvio de apenas alguns graus Celsius pode afetar significativamente a qualidade do produto final. Portanto, o controle estrito sobre a temperatura de sinterização é imperativo, com desvios normalmente não excedendo uma faixa especificada de ± 3 ℃ a ± 5 ℃.
Vantagens do equipamento de indução a vácuo
Em comparação com os métodos tradicionais de fundição, o equipamento de indução a vácuo oferece vantagens substanciais no controle do processo. Com os avanços da tecnologia informática, os modernos fornos de indução a vácuo integram sistemas de controlo inteligentes que agilizam as operações, reduzem os custos de mão de obra e aumentam a precisão.
Os futuros desenvolvimentos em sistemas de controlo inteligentes aumentarão ainda mais as capacidades do equipamento de indução de vácuo. Estes sistemas permitirão um controlo preciso das temperaturas de fusão, facilitarão a adição automática de ligas a intervalos pré-determinados e simplificarão todo o processo de fusão. Além disso, a integração da recolha de dados abrangentes e a análise em tempo real permitirão aos operadores tomar decisões informadas e otimizar os parâmetros do processo durante a fusão.
Componentes do forno de fusão por indução a vácuo
O forno de fusão por indução a vácuo é composto por vários componentes essenciais, incluindo
- Corpo do forno a vácuo: Fornece a câmara onde a fusão ocorre sob vácuo ou em condições de atmosfera controlada.
- Potência de média frequência: Fornece a energia necessária para o aquecimento por indução.
- Sistema de vácuo: Mantém o nível de vácuo desejado dentro da câmara do forno.
- Sistema de arrefecimento: Evita o sobreaquecimento e mantém as temperaturas de fusão ideais.
- Sistema de controlo elétrico: Permite um controlo preciso da temperatura e do funcionamento geral do forno.
Principais características e vantagens
- Controlo preciso da temperatura: O sistema de controlo elétrico assegura uma regulação precisa das temperaturas de fusão, melhorando a qualidade e a consistência do produto final.
- Remoção de gás: O ambiente de vácuo elimina os gases dos metais fundidos, evitando a oxidação rápida e preservando a integridade da liga.
- Tamanhos flexíveis de lotes: Os fornos de vácuo estão disponíveis em vários tamanhos, acomodando uma gama de tamanhos de lotes desde aplicações industriais de pequena escala até aplicações industriais maiores.
- Sistema de arrefecimento centralizado: O sistema de arrefecimento dissipa eficazmente o calor, mantendo temperaturas de funcionamento estáveis e prolongando a vida útil do equipamento.
Em conclusão, os fornos de fusão por indução a vácuo oferecem uma precisão e um controlo sem paralelo nos processos de fusão de metais. Ao tirar partido de tecnologias avançadas e sistemas de controlo inteligentes, estes fornos facilitam uma produção eficiente, garantem a qualidade do produto e abrem caminho a futuros avanços no processamento metalúrgico.
Princípio de funcionamento e significado histórico
Descubra as raízes históricas da tecnologia de fusão por indução em vácuo, traçando as suas origens nas indústrias aeroespacial e metalúrgica. Saiba como esta tecnologia evoluiu para se tornar uma pedra angular na produção de ligas de alto desempenho para várias aplicações.
Fusão por indução a vácuo: Um caminho para materiais avançados
A fusão por indução a vácuo (VIM) é uma tecnologia fundamental no domínio da metalurgia, particularmente na produção de ligas especializadas e exóticas. Inicialmente desenvolvida para o processamento de superligas, o seu espetro de aplicação expandiu-se para abranger aços inoxidáveis e vários outros metais. Esta expansão deve-se em grande parte à crescente procura de materiais avançados em diversas indústrias.
O processo de fusão por indução a vácuo
No centro do VIM está o princípio da fusão de metais sob condições de vácuo, com a indução electromagnética a servir de fonte de energia primária. O processo implica a geração de correntes eléctricas de Foucault no interior do metal, facilitada por uma bobina de indução que transporta corrente alternada. Estas correntes, por sua vez, induzem efeitos de aquecimento, conduzindo, em última análise, à fusão da carga metálica.
A rápida evolução da tecnologia VIM tem as suas raízes ligadas à procura de materiais de liga de alta temperatura por parte da indústria aeroespacial. Estes materiais, essenciais para o equipamento aeroespacial, de mísseis, foguetes e energia atómica, necessitavam de inovações nos processos de fundição. Os fornos VIM surgiram como uma solução, permitindo a fusão de ligas à base de níquel, ferro e cobalto em condições de vácuo. Este ambiente reduz eficazmente a presença de elementos de separação como O2, N2 e H2, assegurando a remoção de inclusões não metálicas e impurezas nocivas como Pb, Bi, Sb, Cu, Sn e Te.
Aplicações da fusão por indução a vácuo
A versatilidade do VIM se estende por várias aplicações no cenário metalúrgico:
- Refinação de metais e ligas de alta pureza.
- Produção de eléctrodos para processos de refusão.
- Fabrico de varas de ligas principais, vitais em procedimentos como a fundição por cera perdida.
- Fundição de componentes críticos para motores de aeronaves.
Evolução histórica
A génese da fusão por indução em vácuo remonta a 1920, quando surgiu o primeiro protótipo. Na sua essência, o VIM utiliza a indução electromagnética para induzir correntes de Foucault nos condutores, aquecendo e fundindo assim o metal. Ao longo das décadas, esta tecnologia encontrou uma utilidade indispensável nos sectores aeroespacial e nuclear, impulsionando os avanços na ciência e engenharia dos materiais.
Em resumo, a fusão por indução a vácuo é um testemunho do engenho humano, facilitando a produção de materiais que alimentam as maravilhas tecnológicas modernas. Desde as suas origens humildes até ao seu estatuto atual como pedra angular da inovação metalúrgica, o VIM continua a moldar o panorama do fabrico de materiais avançados.
Aplicações em todos os sectores
Explore as aplicações abrangentes da tecnologia de fusão por indução em vácuo na indústria aeroespacial, eletrónica, energia e muito mais. Compreenda como esta tecnologia melhora as propriedades e a qualidade dos materiais essenciais para a engenharia e fabrico avançados.
A tecnologia de fusão por indução a vácuo (VIM) evoluiu significativamente. Originalmente desenvolvida para o processamento de ligas especializadas e exóticas, tornou-se cada vez mais comum à medida que os materiais avançados encontram aplicações mais amplas. Inicialmente utilizada para materiais como as superligas, a VIM expandiu a sua utilidade para incluir aços inoxidáveis e vários outros metais.
O rápido desenvolvimento da tecnologia VIM está intimamente ligado à procura de materiais de liga de alta temperatura em indústrias como a aeroespacial, a de mísseis, a de foguetes e a de equipamento de energia atómica. As superligas, cruciais para estas aplicações, beneficiam grandemente das capacidades dos fornos VIM.
Como funcionam os fornos de indução a vácuo
Num forno de indução a vácuo, o material é carregado sob vácuo e é aplicada energia para fundir a carga. São efectuadas cargas adicionais para atingir a capacidade de fusão desejada, e o metal fundido é refinado sob condições de vácuo. Este processo permite um ajuste preciso da química da fusão até se obter a composição desejada.
Vantagens da fusão por indução a vácuo
-
Alta pureza e qualidade: O VIM é excelente na produção de materiais de alta pureza e qualidade. O ambiente de vácuo elimina o risco de contaminação por oxigénio, azoto e outros gases presentes na atmosfera. Isto resulta numa fusão mais limpa e homogénea, desprovida de inclusões e impurezas prejudiciais que podem comprometer as propriedades mecânicas.
-
Atmosfera controlada: Dentro da câmara de vácuo, a atmosfera é rigorosamente controlada, sendo apenas introduzidos gases específicos a pressões precisas. Este nível de controlo permite uma gestão precisa da composição química do material fundido e evita a oxidação ou reacções indesejadas com os gases ambiente.
Os fornos de fusão por indução são fundamentais no campo da metalurgia de vácuo, desempenhando um papel significativo na produção de ligas e aços especiais cruciais para a indústria aeroespacial, de mísseis, foguetes, equipamento de energia atómica e indústria eletrónica. Uma parte considerável dos produtos destes sectores é fabricada com a tecnologia VIM.
Vários materiais, incluindo o aço inoxidável, o aço resistente ao calor, o aço de resistência ultra-alta, o aço para ferramentas, o aço para rolamentos, os materiais magnéticos, as ligas elásticas e as ligas de expansão, são fundidos utilizando fornos de fusão por indução em vácuo para garantir um desempenho e uma qualidade óptimos. Estes fornos melhoram a capacidade de trabalho a quente e as propriedades mecânicas das superligas à base de níquel, cobalto e ferro, tornando-as indispensáveis em processos avançados de engenharia e fabrico.
Vantagens em relação aos métodos tradicionais
A tecnologia de fusão por indução a vácuo destaca-se como um dos principais métodos de fusão de metais devido às suas inúmeras vantagens em relação às abordagens tradicionais. Ao comparar a sua eficiência, sustentabilidade e pureza do material com os métodos convencionais, torna-se evidente porque é que a fusão por indução a vácuo é cada vez mais favorecida em várias indústrias.
Eficiência energética e sustentabilidade ambiental
A tecnologia de fusão por indução a vácuo (VIM) representa um salto significativo na eficiência energética e na sustentabilidade ambiental em comparação com os métodos tradicionais de fundição. Ao contrário das abordagens convencionais, o VIM funciona num ambiente de vácuo, o que minimiza a perda de calor e reduz o consumo de energia. Esta utilização eficiente da energia não só reduz os custos de produção, como também contribui para um processo de fabrico mais ecológico, reduzindo as emissões de carbono e o desperdício de energia.
Pureza e qualidade do material
Uma das principais vantagens do VIM é a sua capacidade de produzir materiais de pureza e qualidade excepcionais. O ambiente de vácuo elimina a presença de oxigénio, azoto e outros gases que poderiam contaminar o metal fundido. Como resultado, o VIM produz fundidos mais limpos e homogéneos, desprovidos de impurezas e inclusões prejudiciais. Esta pureza melhora as propriedades mecânicas e o desempenho geral dos materiais resultantes, tornando-os altamente desejáveis para várias aplicações.
Atmosfera controlada
Na câmara de vácuo do equipamento VIM, a atmosfera é meticulosamente controlada, permitindo uma regulação precisa da composição e pressão do gás. Ao introduzir apenas gases especificados a pressões exactas, a VIM assegura um controlo rigoroso sobre a composição química do material fundido, minimizando o risco de oxidação indesejada ou de reacções com os gases ambientais. Este nível de controlo é crucial para produzir ligas com propriedades consistentes e minimizar o desperdício de material.
Eficiência e flexibilidade do processo
Para além dos seus benefícios ambientais e de qualidade, o VIM oferece uma eficiência e flexibilidade de processo inigualáveis. Os seus ciclos de aquecimento rápidos e o aquecimento uniforme das cargas metálicas aumentam significativamente as taxas de produção e reduzem as taxas de defeitos. Além disso, a versatilidade do VIM permite a fusão de vários metais e ligas com facilidade, facilitando trocas rápidas entre materiais e permitindo o desligamento imediato, se necessário. Esta agilidade na produção aumenta a eficiência operacional e a adaptabilidade às exigências de fabrico em constante mudança.
Aplicação e perspectivas futuras
A adoção generalizada da tecnologia de fundição por indução a vácuo em todas as indústrias sublinha o seu imenso potencial e versatilidade. Desde a investigação experimental em pequena escala até à produção industrial em grande escala, o VIM provou a sua eficácia e fiabilidade. O seu funcionamento simples e as suas rápidas temperaturas de fusão fazem dele a escolha preferida dos fabricantes que procuram precisão e consistência nos seus processos de produção. À medida que a tecnologia continua a avançar, espera-se que a aplicação do VIM se expanda ainda mais, impulsionando a inovação e a eficiência nos processos de fundição e refinação de metais.
Sinterização a vácuo: Melhorar a eficiência e a qualidade
Para além da fusão por indução a vácuo, a sinterização a vácuo surge como outro processo vital para melhorar a eficiência e a qualidade dos produtos no fabrico de metais. Ao sinterizar pós metálicos a temperaturas abaixo do ponto de fusão num ambiente de vácuo, a sinterização a vácuo oferece várias vantagens. Elimina as reacções entre metais e gases, aumenta a densificação e reduz as temperaturas de sinterização, conservando assim a energia e prolongando a vida útil dos fornos de sinterização. O resultado é a produção de produtos metálicos de alta qualidade com propriedades mecânicas melhoradas e consumo de energia reduzido.
Em conclusão, a fusão por indução a vácuo e a sinterização a vácuo representam tecnologias de ponta que oferecem inúmeras vantagens em relação aos métodos de fusão tradicionais. Desde a eficiência energética e pureza do material até à flexibilidade do processo e sustentabilidade ambiental, estas técnicas avançadas estão a impulsionar a inovação e a remodelar o panorama do fabrico de metais. À medida que as indústrias continuam a dar prioridade à sustentabilidade e à qualidade, a adoção de processos baseados no vácuo, como o VIM e a sinterização a vácuo, está pronta a acelerar, dando início a uma nova era de eficiência e excelência na produção de metais.
Principais características dos fornos de fusão por indução a vácuo
Os fornos de fusão por indução no vácuo são fundamentais nos processos metalúrgicos, oferecendo um espetro de características adaptadas para um controlo preciso e uma produtividade melhorada. Aqui está uma exploração abrangente dos seus principais componentes e avanços:
Componentes estruturais
O forno é composto por uma camisa de aço hermética arrefecida a água, concebida para manter as condições de vácuo necessárias durante o processamento. Dentro deste invólucro, o metal é fundido num cadinho aninhado numa bobina de indução arrefecida a água. Além disso, o interior do forno é normalmente revestido com refractários adequados para suportar temperaturas extremas.
Melhorias do processo
1. Controlo ambiental
- A fundição de metal fundido pode ser executada sob vácuo ou em ambientes de gás inerte, assegurando condições óptimas para a formação de ligas e manutenção da pureza.
2. Características adicionais
- Os fornos podem integrar mecanismos de inclinação e vazamento, câmaras de fundição e portas de amostragem para facilitar as diversas necessidades de produção.
- As instalações de manuseamento de moldes permitem um processamento automatizado ou semi-automatizado, incorporando por vezes sistemas de interbloqueio de vácuo para um funcionamento sem falhas.
Tendências de desenvolvimento futuro
A evolução do equipamento de fusão por indução em vácuo reflecte uma transição para estruturas multifuncionais capazes de acomodar diversos processos tecnológicos. Prevê-se que as configurações modulares sejam dominantes, permitindo combinações personalizadas de componentes para satisfazer eficazmente requisitos de processos específicos.
Controlo de precisão e automatização
A integração de tecnologias avançadas, como os sistemas informáticos e a aquisição inteligente de sinais, permite um controlo preciso dos processos. Interfaces homem-máquina amigáveis simplificam a operação, reduzindo os custos de mão de obra e aumentando a simplicidade operacional.
Sistemas auxiliares
Para além dos componentes principais, os sistemas auxiliares como as fontes de alimentação, as unidades de controlo e os sistemas de refrigeração desempenham papéis vitais. Estes sistemas asseguram a entrada de energia para a fusão e evitam o sobreaquecimento de componentes críticos.
Considerações estruturais
A atenção à conceção estrutural é fundamental para evitar a descarga de vácuo. O isolamento de todos os corpos carregados dentro do invólucro do forno e a eliminação de arestas vivas na conceção do indutor são cruciais para garantir um funcionamento ininterrupto.
Principais vantagens
- Fusão de determinadas ligas de titânio: As condições de vácuo permitem a fusão de ligas de titânio, expandindo a aplicabilidade do forno.
- Prevenção de reacções químicas: Os ambientes de vácuo protegem os metais e ligas fundidos de reacções químicas indesejáveis com inclusões não metálicas.
- Remoção de gases nocivos: O estado de vácuo facilita a eliminação de gases nocivos dissolvidos e poluentes do metal fundido líquido, garantindo a pureza do material.
Em conclusão, os fornos de fusão por indução a vácuo incorporam versatilidade e precisão, impulsionando avanços nos processos metalúrgicos através de um design inovador e integração tecnológica.
Benefícios ambientais e de desempenho
A fusão por indução a vácuo (VIM) oferece vantagens ambientais e de desempenho significativas, tornando-a um método preferido para a produção de materiais de alta pureza com propriedades superiores.
Alta Pureza e Qualidade
O VIM é excelente na produção de materiais de pureza e qualidade excepcionais. Ao funcionar num ambiente de vácuo, o VIM elimina o risco de contaminação por gases atmosféricos como o oxigénio e o azoto. Isto assegura uma fusão mais limpa e homogénea, desprovida de inclusões nocivas e impurezas que possam comprometer a integridade mecânica do material. Consequentemente, as ligas resultantes apresentam propriedades mecânicas e características de desempenho melhoradas.
Atmosfera controlada
Dentro da câmara de vácuo, a atmosfera é meticulosamente controlada, permitindo uma regulação precisa da composição e pressão do gás. Este nível de controlo é fundamental para alcançar a composição química desejada do material fundido, ao mesmo tempo que evita a oxidação indesejada ou reacções com gases ambiente. Como resultado, o VIM permite a produção de materiais com propriedades químicas consistentes e reatividade mínima, garantindo um desempenho superior em várias aplicações.
Resumo das vantagens
As vantagens da utilização de um forno de fusão por indução a vácuo são múltiplas:
-
Eliminação de gases: O VIM opera sob pressões extremamente baixas, normalmente em torno de 0,000001 atmosfera. Este ambiente facilita a remoção de gases indesejáveis e elementos voláteis das matérias-primas durante o processo de fusão, garantindo a produção de ligas de alta pureza.
-
Análise química precisa: A ausência de atmosfera na câmara de vácuo permite um controlo excecional e reprodutível da composição química dos materiais fundidos. Esta precisão permite a produção de ligas com composições personalizadas e propriedades desejadas, melhorando a eficiência geral do processo e a qualidade do produto.
-
Controlo superior do processo: O VIM oferece um controlo independente da pressão, temperatura e agitação indutiva, proporcionando um controlo de processo sem paralelo. Esta flexibilidade permite o desenvolvimento de práticas de fusão optimizadas específicas para cada composição de liga, melhorando ainda mais o desempenho e a consistência dos materiais produzidos.
Para além dos benefícios ambientais, as vantagens de um forno de indução a vácuo estendem-se ao processamento de vários metais e ligas:
- Aumento da pureza: A ausência de poluição do ar e de escórias nos fornos de indução a vácuo contribui para a produção de ligas relativamente puras com níveis de desempenho elevados.
- Remoção de gases: O funcionamento em condições de vácuo permite a redução do teor de gás no aço e ligas fundidos, resultando em materiais com concentrações de gás mais baixas e propriedades melhoradas.
- Prevenção da oxidação: O processamento de metais num ambiente de vácuo atenua o risco de oxidação, preservando a integridade do material processado.
- Evaporação de impurezas: As impurezas, como o chumbo (Pb) e o bismuto (Bi), podem evaporar-se mais rapidamente no vácuo, facilitando a purificação do material durante o processo de fundição.
Em conclusão,fornos de fusão por indução em vácuo oferecem uma solução abrangente para a produção de materiais de elevada pureza com características de desempenho superiores, ao mesmo tempo que reduzem a poluição ambiental e garantem a eficiência do processo.
CONTACTE-NOS PARA UMA CONSULTA GRATUITA
Os produtos e serviços da KINTEK LAB SOLUTION foram reconhecidos por clientes de todo o mundo. A nossa equipa terá todo o prazer em ajudar com qualquer questão que possa ter. Contacte-nos para uma consulta gratuita e fale com um especialista de produto para encontrar a solução mais adequada para as suas necessidades de aplicação!