Introdução
Índice
Quando se trata de produzir componentes cerâmicos de alta qualidade, um dos processos mais importantes é a prensagem isostática. Esta técnica garante a uniformidade e a precisão necessárias para o fabrico de cerâmica utilizada em várias indústrias. A prensagem isostática envolve a seleção cuidadosa dos pós de prensagem e o controlo das ferramentas para alcançar a uniformidade desejada. Outro fator chave neste processo é a otimização do processo de sinterização, que influencia grandemente as propriedades físicas da cerâmica. Ao compreender o processo de prensagem isostática, os fabricantes podem assegurar a produção de cerâmicas que cumprem as normas rigorosas de precisão dimensional e desempenho.
O Processo de Prensagem Semi-Isostática
Importância da uniformidade da prensagem
No processo deprensagem semi-isostática os produtos são colocados num recipiente fechado cheio de líquido e sujeitos a uma pressão igual em todas as superfícies. Este ambiente de alta pressão aumenta a densidade dos produtos e dá-lhes as formas pretendidas. As prensas semi-isostáticas são amplamente utilizadas na formação de refractários de alta temperatura, cerâmica, carboneto cimentado, ímanes permanentes de lantânio, materiais de carbono e pós de metais raros.
O papel da seleção cuidadosa dos pós de prensagem e dos controlos das ferramentas
A prensagem semi-isostática depende da seleção cuidadosa dos pós de prensagem e dos controlos das ferramentas para garantir o resultado desejado. Ao contrário de outros processos de metalurgia do pó, a prensagem semi-isostática oferece várias vantagens, incluindo a compactação igual em todas as direcções e uma densidade final do componente mais uniforme. No entanto, os fabricantes devem caraterizar cuidadosamente as propriedades do pó metálico utilizado no processo para obter as propriedades ideais do componente final. A caraterização do material é crucial para garantir a qualidade e o desempenho desejados do produto final.
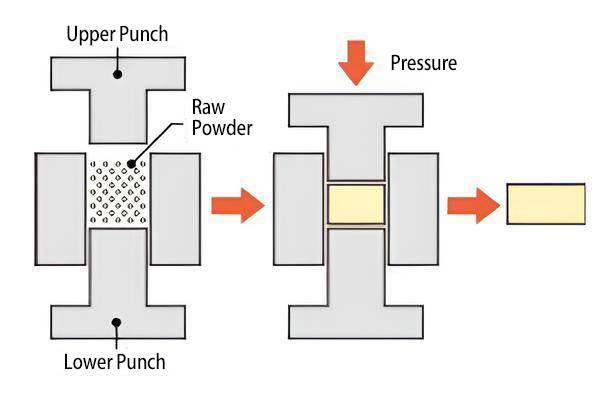
Influência do processo de sinterização optimizado nas propriedades físicas
O processo de sinterização optimizado desempenha um papel significativo na determinação das propriedades físicas dos componentes prensados semi-isostaticamente. A prensagem isostática permite a produção de vários tipos de materiais a partir de compactos de pó, reduzindo a porosidade da mistura de pó. A mistura de pós é compactada e encapsulada através da pressão isostática, que aplica uma pressão igual em todas as direcções. Este confinamento do pó metálico numa membrana flexível ou num recipiente hermético assegura uma compactação e densidade uniformes na peça compactada.
O processo de prensagem isostática tem evoluído ao longo dos anos e é atualmente amplamente utilizado em várias indústrias, incluindo cerâmica, metais, compósitos, plásticos e carbono. Oferece vantagens únicas para aplicações cerâmicas e refractárias, permitindo uma modelação precisa dos produtos e reduzindo a necessidade de maquinação dispendiosa. A pressão total exercida durante a prensagem isostática assegura uma compactação e densidade uniformes, respondendo às preocupações sobre a variação da densidade nos métodos de processamento convencionais. A prensagem isostática é particularmente adequada para a produção de peças de maiores dimensões, peças com elevadas relações espessura/diâmetro e peças que requerem propriedades materiais superiores.
Existem duas categorias principais de prensagem isostática: prensagem isostática a frio (CIP) e prensagem isostática a quente (HIP). A CIP envolve a aplicação de pressão isostática ao pó solto à temperatura ambiente, enquanto a HIP aplica pressão isostática ao pó quando este é aquecido numa embalagem. A HIP utiliza um gás inerte como meio de transferência de pressão. O processo de prensagem isostática a quente envolve a colocação do pó num recipiente de alta pressão, submetendo-o a uma temperatura elevada e a uma pressão equilibrada, e sinterizando-o em peças compactas. Em comparação com outros métodos, como a prensagem a quente, a prensagem isostática a quente oferece temperaturas de sinterização mais baixas e uma maior densidade do produto.
Em conclusão, o processo de prensagem semi-isostática oferece vantagens únicas em termos de uniformidade de prensagem e densidade do componente final. A seleção cuidadosa dos pós de prensagem e dos controlos das ferramentas, bem como a otimização do processo de sinterização, são cruciais para alcançar as propriedades físicas desejadas. O processo de prensagem isostática tornou-se uma ferramenta valiosa em várias indústrias, permitindo a produção de componentes de alta qualidade com formas precisas e propriedades materiais superiores.
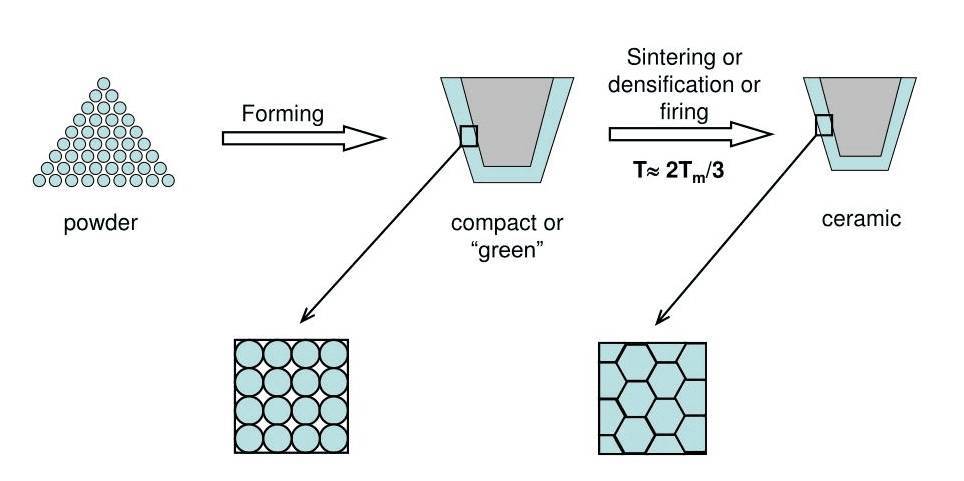
O papel das técnicas de sinterização personalizadas
Obtenção de linearidade e concentricidade
A sinterização é um processo crucial no fabrico de componentes cerâmicos. As técnicas de sinterização personalizadas desempenham um papel vital na obtenção da linearidade e da concentricidade destes componentes.
Uma vantagem da sinterização à temperatura ambiente é o facto de permitir a produção de alvos de grandes dimensões sem estar limitada pelo tamanho do equipamento. Este método também oferece baixo investimento em equipamento, baixo custo de produção, alta eficiência de produção, excelente desempenho do alvo e fácil produção industrial. É particularmente adequado para os requisitos de desempenho de alvos revestidos para ecrãs topo de gama.
No entanto, a sinterização à temperatura ambiente tem os seus pontos fracos. É considerado o método de sinterização mais difícil em comparação com outros. Para obter um corpo sinterizado denso, é frequentemente adicionado um auxiliar de sinterização. Mas remover o auxiliar de sinterização do corpo sinterizado pode ser um desafio, resultando numa menor pureza do produto. Além disso, devem ser cumpridos requisitos rigorosos relativamente à forma, tamanho das partículas e distribuição do tamanho das partículas do pó. As técnicas de processamento de pó, como a moagem de bolas, a moagem a jato e a classificação por sedimentação, são normalmente utilizadas para cumprir estes requisitos. Finalmente, os alvos produzidos através da sinterização à temperatura ambiente são geralmente finos.
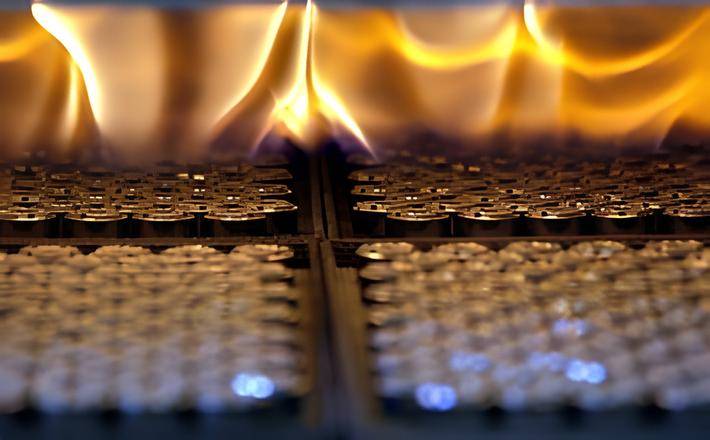
Adequação para o fabrico de vários componentes cerâmicos
A sinterização é um processo versátil que oferece várias vantagens no fabrico de componentes cerâmicos. Aqui estão alguns dos principais benefícios:
-
Formas complexas: A sinterização de metais permite a criação de formas complexas que seriam difíceis ou impossíveis de produzir utilizando outros métodos. Esta capacidade abre possibilidades para designs inovadores e componentes funcionais.
-
Elevada precisão dimensional: A sinterização oferece uma elevada precisão dimensional, garantindo que o produto acabado corresponde exatamente à forma desejada. Esta precisão é crucial em aplicações onde são necessárias tolerâncias apertadas.
-
Fiabilidade e repetibilidade da produção em grande escala: A sinterização é um processo fiável, que produz produtos acabados consistentes. Isto torna-o ideal para produções em grande escala, onde a consistência e a uniformidade são essenciais.
-
Auto-lubrificação: A sinterização pode criar peças com propriedades auto-lubrificantes. O pó compactado forma uma ligação densa entre as partículas, reduzindo a fricção e o desgaste. Esta propriedade é valiosa em aplicações onde a lubrificação é difícil ou indesejável.
-
Materiais únicos e isotrópicos: A sinterização é utilizada para criar materiais isotrópicos únicos, o que significa que possuem as mesmas propriedades em todas as direcções. Estes materiais são altamente duráveis e apresentam uma excelente resistência, tornando-os adequados para aplicações que exigem robustez.
-
Tecnologia verde: A sinterização é considerada uma tecnologia ecológica, uma vez que não produz emissões nocivas. Isto torna-a uma escolha amiga do ambiente para as empresas que pretendem reduzir o seu impacto ambiental.
-
Amortecimento das vibrações: A sinterização pode produzir peças com propriedades de amortecimento de vibrações. O pó compactado forma uma ligação densa, reduzindo as vibrações e o ruído. Este atributo é benéfico em aplicações onde o controlo das vibrações é crucial.
Diversas peças cerâmicas
A sinterização de metais encontra aplicação em várias indústrias, incluindo componentes eléctricos, semicondutores e fibras ópticas. Aumenta a resistência, a condutividade e a translucidez dos metais, tornando-os adequados para estas indústrias.
Na sinterização de cerâmica, o processo é utilizado para fabricar objectos de cerâmica, incluindo cerâmica. Envolve a consolidação do material, reduzindo a porosidade e aumentando a densidade. As matérias-primas cerâmicas requerem frequentemente aditivos orgânicos antes da sinterização para melhorar a plasticidade. O processo de sinterização é conduzido a altas temperaturas, pressão ou correntes eléctricas.
Foram desenvolvidos métodos modernos de moldagem de pós, como a prensagem isostática, o slipcasting, a extrusão, o tapecasting e a impressão 3D, para a produção de corpos verdes de cerâmica e metais. O corpo verde é então aquecido através de um processo de sinterização, reduzindo a porosidade e aumentando a densidade.
Os processos de sinterização são controlados por mecanismos de difusão no estado sólido activados termicamente. Estes mecanismos podem ser quantificados através do desenvolvimento de modelos de sinterização utilizando instrumentos como os dilatómetros de haste.
O equipamento de sinterização por micro-ondas é amplamente utilizado em aplicações industriais para sinterizar várias cerâmicas de alta qualidade, incluindo óxido de lítio-cobalto, nitreto de silício, carboneto de silício, óxido de alumínio, nitreto de alumínio, óxido de zircónio, hidróxido de magnésio, alumínio, zinco, caulino, sulfato de cobalto, oxalato de cobalto e óxido de vanádio. Também é utilizado na sinterização de dispositivos cerâmicos electrónicos, como cerâmicas piezoeléctricas PZT e varistores.
Em geral, as técnicas de sinterização por medida desempenham um papel crucial na obtenção de linearidade e concentricidade em componentes cerâmicos. Oferecem inúmeras vantagens, incluindo a capacidade de fabricar formas complexas, elevada precisão dimensional, fiabilidade na produção em grande escala, auto-lubrificação, materiais isotrópicos únicos, tecnologia ecológica e amortecimento de vibrações. A sinterização de metais encontra aplicações em várias indústrias, enquanto a sinterização de cerâmica é utilizada em cerâmica e noutros processos de fabrico de cerâmica. O equipamento de sinterização por micro-ondas é amplamente utilizado em aplicações industriais para sinterizar várias cerâmicas e dispositivos de cerâmica eletrónica.
Capacidades de dimensão e precisão
Gama padrão de capacidades de dimensão
As capacidades de dimensão de um sistema de deposição desempenham um papel crucial na determinação da sua adequação a várias aplicações. Em ambientes de I&D, a flexibilidade é um fator chave. O sistema deve ser capaz de lidar com diferentes materiais, tamanhos de substrato, gamas de temperatura, fluxo de iões, taxas de deposição, frequências, pontos finais e regimes de funcionamento de pressão. Isto permite a experimentação e a adaptação às prioridades em mudança. Além disso, as considerações orçamentais também entram em jogo, uma vez que o custo dos sistemas pode variar significativamente consoante as opções tecnológicas.
Precisão no estado de combustão
A precisão é um fator crítico quando se trata de sistemas de deposição. Por exemplo, no caso da micro-usinagem ou de aplicações de ultra-precisão, o diamante é frequentemente utilizado como material de ferramenta devido à sua extrema dureza e estabilidade dimensional. Quando se considera a precisão no estado de cozedura, é importante notar que o diâmetro interno pode ter uma tolerância de +/- 0,02 mm com uma repetibilidade de menos de 10 µm dentro do mesmo lote de produção.
Precisão depois da retificação com diamante
A retificação diamantada é um processo que pode aumentar significativamente a precisão nas aplicações de maquinagem. Após a retificação diamantada, o comprimento da peça de trabalho pode ter uma tolerância de +/- 0,03 mm, enquanto o diâmetro externo pode ter uma tolerância de +/- 0,01 mm. Além disso, a espessura mínima de parede que pode ser alcançada é de 0,3 µm. Estes níveis de precisão garantem resultados de peças de alta qualidade.
As ferramentas de corte de diamante podem ser criadas usando diamante maciço (monocristal, diamante CVD, PCD) ou revestimentos de diamante. As ferramentas abrasivas diamantadas padrão são feitas através da ligação de monocristais de diamante num corpo base. Em alternativa, existe uma nova tecnologia de camada de retificação que envolve camadas de diamante microcristalino depositadas por vapor químico com pontas de cristalito afiadas. Estas pontas afiadas contribuem para a eficácia do processo de retificação.
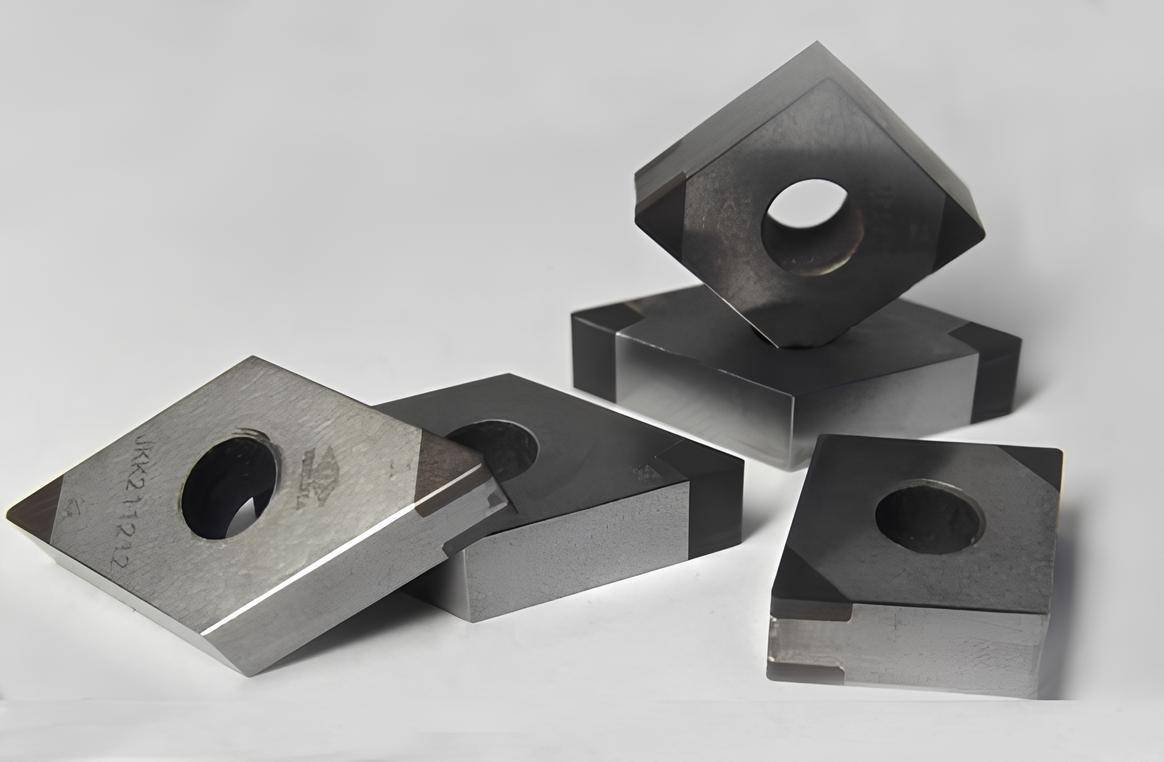
As micro ferramentas de retificação, tais como lápis abrasivos e rebarbas, também podem ser produzidas utilizando a mesma tecnologia de revestimento. Mesmo ferramentas muito pequenas, com diâmetros de 50 mm, foram testadas com sucesso.
Em conclusão, as capacidades dimensionais e a precisão de um sistema de deposição são factores cruciais a ter em conta em ambientes de I&D. O sistema deve oferecer flexibilidade, permitindo a utilização de ferramentas de diâmetro muito reduzido. O sistema deve oferecer flexibilidade, permitindo a experimentação e a adaptação às prioridades em mudança. A retificação com diamante pode aumentar muito a precisão nas aplicações de maquinagem, garantindo resultados de alta qualidade. Quer se trate de uma gama padrão de capacidades de dimensão ou de precisão após a retificação de diamantes, estes factores contribuem para a eficácia e eficiência globais do sistema de deposição.
Conclusão
Em conclusão,prensagem isostática é um processo crucial no fabrico de cerâmica que assegura a uniformidade e a precisão dos componentes cerâmicos. Seleccionando cuidadosamente os pós de prensagem e controlando as ferramentas, os fabricantes podem alcançar a uniformidade desejada na cerâmica prensada. Além disso, a otimização do processo de sinterização melhora ainda mais as propriedades físicas da cerâmica. As técnicas de sinterização adaptadas desempenham um papel vital na obtenção de linearidade e concentricidade no produto final, tornando-o adequado para várias aplicações. Além disso, as capacidades dimensionais e a precisão das cerâmicas podem ser padronizadas, e quaisquer ajustes necessários podem ser efectuados através de retificação com diamante. Em geral, a prensagem isostática e as técnicas de sinterização à medida são essenciais para a produção de componentes cerâmicos de alta qualidade e precisão.
Se estiver interessado nos nossos produtos, visite o sítio Web da nossa empresa:https://kindle-tech.com/product-categories/isostatic-pressA nossa equipa de investigação e desenvolvimento é constituída por engenheiros experientes e profissionais de saúde. A nossa equipa de I&D é constituída por engenheiros e cientistas experientes que seguem de perto as tendências da indústria e estão constantemente a ultrapassar os limites do que é possível. O nosso equipamento de laboratório incorpora a tecnologia mais recente para garantir a obtenção de resultados exactos e repetíveis durante as suas experiências. Desde instrumentos de alta precisão a sistemas de controlo inteligentes, os nossos produtos oferecem-lhe possibilidades ilimitadas para o seu trabalho experimental.
CONTACTE-NOS PARA UMA CONSULTA GRATUITA
Os produtos e serviços da KINTEK LAB SOLUTION foram reconhecidos por clientes de todo o mundo. A nossa equipa terá todo o prazer em ajudar com qualquer questão que possa ter. Contacte-nos para uma consulta gratuita e fale com um especialista de produto para encontrar a solução mais adequada para as suas necessidades de aplicação!