As cerâmicas são amplamente utilizadas em revestimentos de fornos devido às suas excepcionais propriedades de isolamento térmico, resistência ao calor e estabilidade química.São particularmente eficazes na manutenção de temperaturas estáveis e controladas, o que é fundamental para os processos industriais e laboratoriais.Os materiais cerâmicos, como a fibra cerâmica, oferecem uma baixa condutividade térmica, reduzindo a perda de calor e melhorando a eficiência energética.Além disso, a sua resistência à corrosão química torna-os ideais para ambientes onde é comum a exposição a temperaturas elevadas e a substâncias corrosivas.Estas propriedades garantem durabilidade, segurança e um desempenho ótimo nas operações do forno.
Pontos-chave explicados:
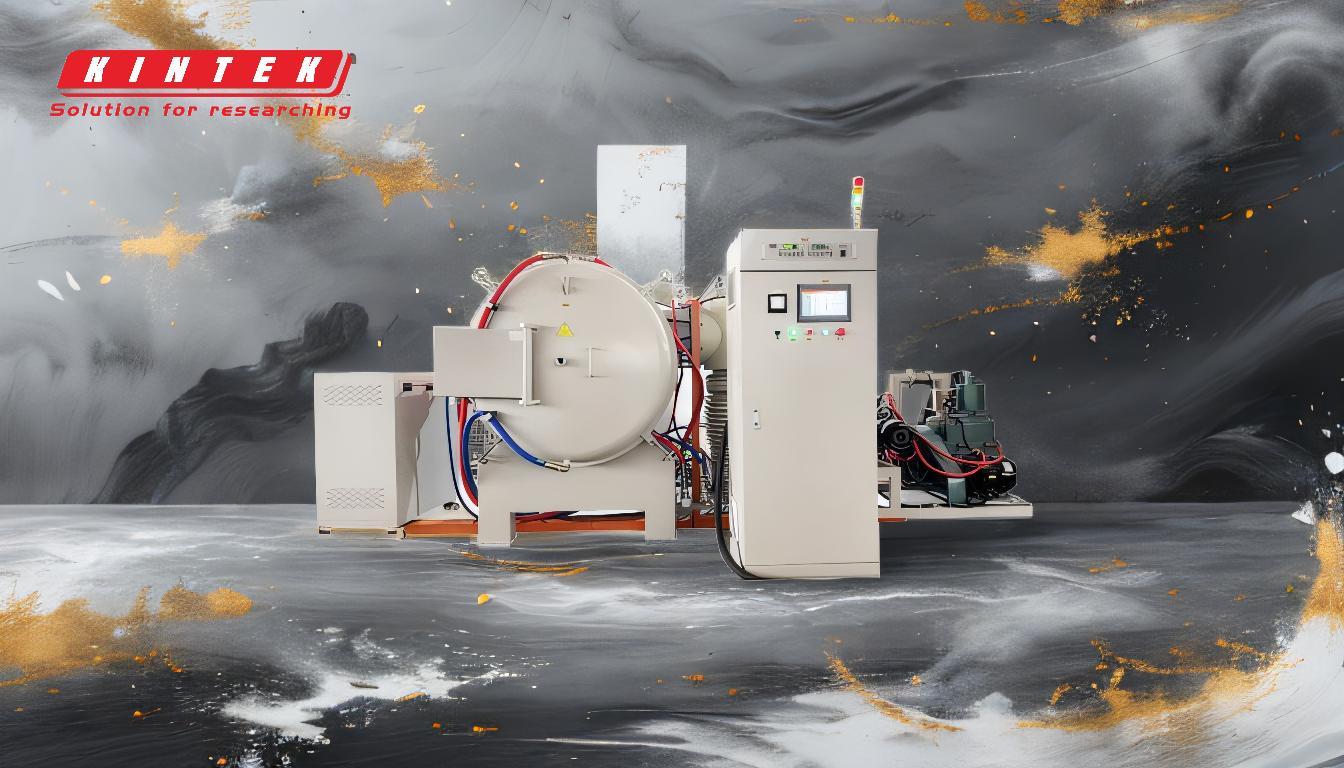
-
Propriedades de isolamento térmico
- As cerâmicas, especialmente a fibra cerâmica, são conhecidas pelas suas excelentes capacidades de isolamento térmico.
- Minimizam a transferência de calor, assegurando que o forno retém o calor de forma eficiente e funciona a temperaturas consistentes.
- Esta propriedade é crucial para processos que requerem um controlo preciso da temperatura, como o tratamento térmico de metais ou o fabrico de vidro.
-
Resistência ao calor
- As cerâmicas podem suportar temperaturas extremamente elevadas sem se degradarem, o que as torna adequadas para revestimentos de fornos.
- A sua capacidade de manter a integridade estrutural sob tensão térmica garante durabilidade e fiabilidade a longo prazo.
- Esta resistência ao calor é vital para aplicações como fornos, onde as temperaturas podem exceder os 1000°C.
-
Baixa condutividade térmica
- A baixa condutividade térmica da cerâmica reduz a perda de calor, melhorando a eficiência energética do forno.
- Esta propriedade ajuda a manter temperaturas uniformes em todo o forno, o que é essencial para resultados consistentes do processo.
-
Resistência à corrosão química
- As cerâmicas são altamente resistentes à corrosão química, mesmo em ambientes agressivos.
- Isto torna-as ideais para fornos que lidam com materiais ou gases corrosivos, como os utilizados no processamento químico ou na metalurgia.
- A sua resistência à degradação química garante uma vida útil mais longa para o revestimento do forno.
-
Durabilidade e segurança
- A combinação de resistência térmica e química faz da cerâmica uma escolha durável e segura para revestimentos de fornos.
- Reduzem o risco de falha do forno, que pode levar a paragens dispendiosas ou a riscos de segurança.
- A sua estabilidade em condições extremas garante um desempenho fiável durante períodos prolongados.
-
Aplicações em ambientes industriais e laboratoriais
- Os revestimentos cerâmicos são utilizados numa variedade de fornos, incluindo fornos de mufla, fornos e fornos industriais.
- A sua versatilidade torna-os adequados para diversas aplicações, desde a metalurgia até ao fabrico de vidro e ao processamento químico.
- A utilização de cerâmica garante que estes processos são efectuados de forma eficiente e segura.
Em resumo, a cerâmica é um material ideal para revestimentos de fornos devido ao seu isolamento térmico, resistência ao calor, baixa condutividade térmica e resistência à corrosão química.Estas propriedades tornam-nas indispensáveis tanto em ambientes industriais como laboratoriais, garantindo operações de forno eficientes, seguras e fiáveis.
Tabela de resumo:
Propriedade | Vantagens |
---|---|
Isolamento térmico | Minimiza a transferência de calor, assegura temperaturas consistentes e melhora a eficiência. |
Resistência ao calor | Resiste a temperaturas extremas, garantindo durabilidade e fiabilidade. |
Baixa condutividade térmica | Reduz a perda de calor, mantém temperaturas uniformes e aumenta a eficiência energética. |
Resistência à corrosão química | Resiste à degradação em ambientes agressivos, prolongando a vida útil do revestimento do forno. |
Durabilidade e segurança | Combina resistência térmica e química para um desempenho seguro e duradouro. |
Aplicações | Adequado para fornos de mufla, fornos e fornos industriais em vários sectores. |
Melhore o desempenho do seu forno com revestimentos cerâmicos- contacte os nossos especialistas hoje para saber mais!