As zonas de temperatura de um forno são fundamentais para compreender o seu funcionamento e funcionalidade, particularmente em processos como sinterização, cozedura de cerâmica ou outras aplicações de alta temperatura.Os fornos são concebidos com zonas de temperatura específicas para assegurar o controlo do aquecimento, sinterização e arrefecimento dos materiais.Estas zonas incluem normalmente uma zona de pré-aquecimento, uma zona de sinterização ou de cozedura a alta temperatura e uma zona de arrefecimento.Cada zona serve um objetivo distinto, como a remoção de materiais orgânicos, a ligação de partículas por difusão ou a prevenção da oxidação durante o arrefecimento.Os intervalos de temperatura e as zonas exactas dependem do tipo de forno (por exemplo, rotativo, de túnel ou de laboratório) e dos materiais a serem processados.Por exemplo, os fornos rotativos podem necessitar de temperaturas de chama até 2000 °C para atingir temperaturas de zona de sinterização de cerca de 1450 °C, enquanto os fornos de laboratório podem funcionar numa gama mais ampla, de 100 a 1700 °C.A compreensão destas zonas é essencial para otimizar o desempenho do forno e garantir os resultados desejados para os materiais a serem processados.
Pontos-chave explicados:
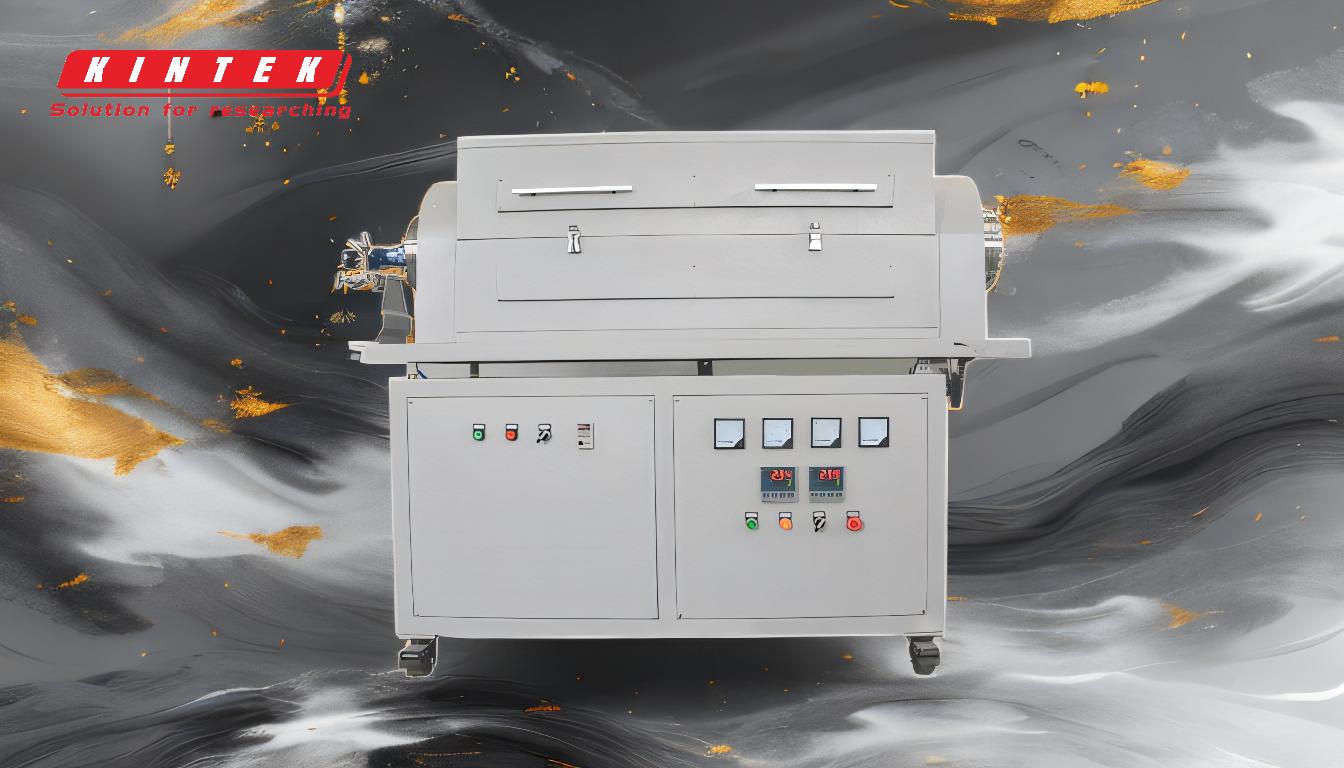
-
Estrutura geral das zonas de temperatura do forno:
- Os fornos estão normalmente divididos em três zonas principais de temperatura: pré-aquecimento, sinterização (ou aquecimento a alta temperatura) e arrefecimento.
- Cada zona tem uma função específica e uma gama de temperaturas adaptada aos requisitos do material e do processo.
-
Zona de pré-aquecimento:
- Objetivo:Remove lubrificantes, materiais orgânicos e humidade do material antes do processamento a alta temperatura.
- Faixa de temperatura:Varia consoante o tipo de forno e o material, mas geralmente vai desde a temperatura ambiente até várias centenas de graus Celsius.
- Exemplo:Nos fornos de túnel, esta zona assegura a remoção de ligantes orgânicos ou lubrificantes antes da sinterização.
-
Zona de sinterização ou de alta temperatura:
- Objetivo:Facilita a ligação de partículas através de difusão, fusão ou reacções químicas para criar uma estrutura sólida.
-
Gama de temperaturas:Normalmente varia entre 1000 °C e 2000 °C, dependendo do material e do tipo de forno.
- Fornos rotativos:As temperaturas da zona de sinterização são de cerca de 1450 °C, exigindo temperaturas de chama de aproximadamente 2000 °C.
- Fornos de laboratório:Podem atingir temperaturas até 1700 °C.
- Exemplo:Nos fornos de sinterização, esta zona reduz os óxidos e une as partículas de pó por difusão.
-
Zona de arrefecimento:
- Objetivo: Permite que o material arrefeça gradualmente para evitar choques térmicos, fissuras ou oxidação.
- Intervalo de temperatura:Começa na temperatura de sinterização e diminui até à temperatura ambiente.
- Exemplo:Nos fornos de túnel, a zona de arrefecimento assegura um arrefecimento controlado, evitando a entrada de ar e a oxidação.
-
Variações por tipo de forno:
-
Fornos rotativos:
- São necessárias temperaturas de chama de cerca de 2000 °C para atingir temperaturas de zona de sinterização de 1450 °C.
- Inclui zonas de pré-aquecimento e de aquecimento a alta temperatura, cada uma com várias subzonas para um controlo preciso da temperatura.
-
Fornos de túnel:
- Três zonas distintas: pré-aquecimento, sinterização e arrefecimento.
- A zona de pré-aquecimento elimina os materiais orgânicos, a zona de sinterização funde as partículas e a zona de arrefecimento assegura um arrefecimento gradual.
-
Fornos de laboratório:
- Capaz de funcionar numa vasta gama de temperaturas (100-1700 °C).
- Frequentemente utilizado para processos experimentais ou de pequena escala com controlo preciso da temperatura.
-
Fornos rotativos:
-
Importância do controlo da temperatura:
- Os fornos permitem um excelente controlo da subida e descida do calor, o que é fundamental para obter resultados consistentes.
- A gestão precisa da temperatura evita defeitos, garante a integridade do material e optimiza a eficiência energética.
- Exemplo:Na cozedura de cerâmica, um arrefecimento incorreto pode levar a fissuras ou deformações, enquanto uma sinterização insuficiente pode resultar em estruturas fracas.
-
Considerações específicas sobre o material:
-
Diferentes materiais requerem perfis e zonas de temperatura específicos.
- Cerâmica:Requerem temperaturas elevadas para vitrificação e ligação.
- Metais:As temperaturas de sinterização dependem da liga e do tamanho das partículas.
- Materiais orgânicos:São necessárias temperaturas mais baixas para evitar a combustão ou a degradação.
- Exemplo:Nos fornos de sinterização, as zonas de temperatura são adaptadas ao ponto de fusão do material e aos mecanismos de ligação.
-
Diferentes materiais requerem perfis e zonas de temperatura específicos.
-
Materiais refractários em fornos:
- Os fornos são construídos com materiais refractários que podem suportar altas temperaturas sem derreter.
- Estes materiais garantem que o forno pode conter o calor e manter zonas de temperatura estáveis.
- Exemplo:Os tijolos refractários ou revestimentos são utilizados para isolar o forno e proteger a sua estrutura durante operações a altas temperaturas.
Ao compreender as zonas de temperatura de um forno, os utilizadores podem otimizar os processos, selecionar tipos de fornos adequados e obter as propriedades desejadas dos materiais.Quer se trate de aplicações industriais ou de experiências laboratoriais, o controlo preciso destas zonas é essencial para o sucesso dos resultados.
Tabela de resumo:
Zona | Objetivo | Gama de temperaturas |
---|---|---|
Zona de pré-aquecimento | Remove lubrificantes, materiais orgânicos e humidade. | Ambiente até várias centenas de °C |
Zona de sinterização | Liga as partículas por difusão, fusão ou reacções químicas. | 1000-2000 °C (varia consoante o tipo de forno e o material) |
Zona de arrefecimento | Evita o choque térmico, a fissuração ou a oxidação durante o arrefecimento gradual. | Temperatura de sinterização à temperatura ambiente |
Precisa de ajuda para otimizar as zonas de temperatura do seu forno? Contacte hoje mesmo os nossos especialistas para soluções à medida!