Os fornos de fusão por indução são ferramentas altamente versáteis e eficientes utilizadas nos processos de fusão de metais, capazes de atingir temperaturas extremamente elevadas. A faixa de temperatura desses fornos é um fator crítico para os usuários, pois determina os tipos de materiais que podem ser derretidos e a eficiência do processo. Com base nas referências fornecidas, os fornos de fusão por indução podem atingir temperaturas de até 2000 ℃, tornando-os adequados para a fusão de uma ampla gama de metais, incluindo aqueles com altos pontos de fusão, como aço e ferro. Além disso, a temperatura de drenagem do forno é normalmente controlada entre 100 ° F (37 ° C) e 150 ° F (65 ° C), com mecanismos de segurança em vigor para evitar o superaquecimento. Isto garante tanto a segurança operacional como a consistência do processo de fusão.
Pontos-chave explicados:
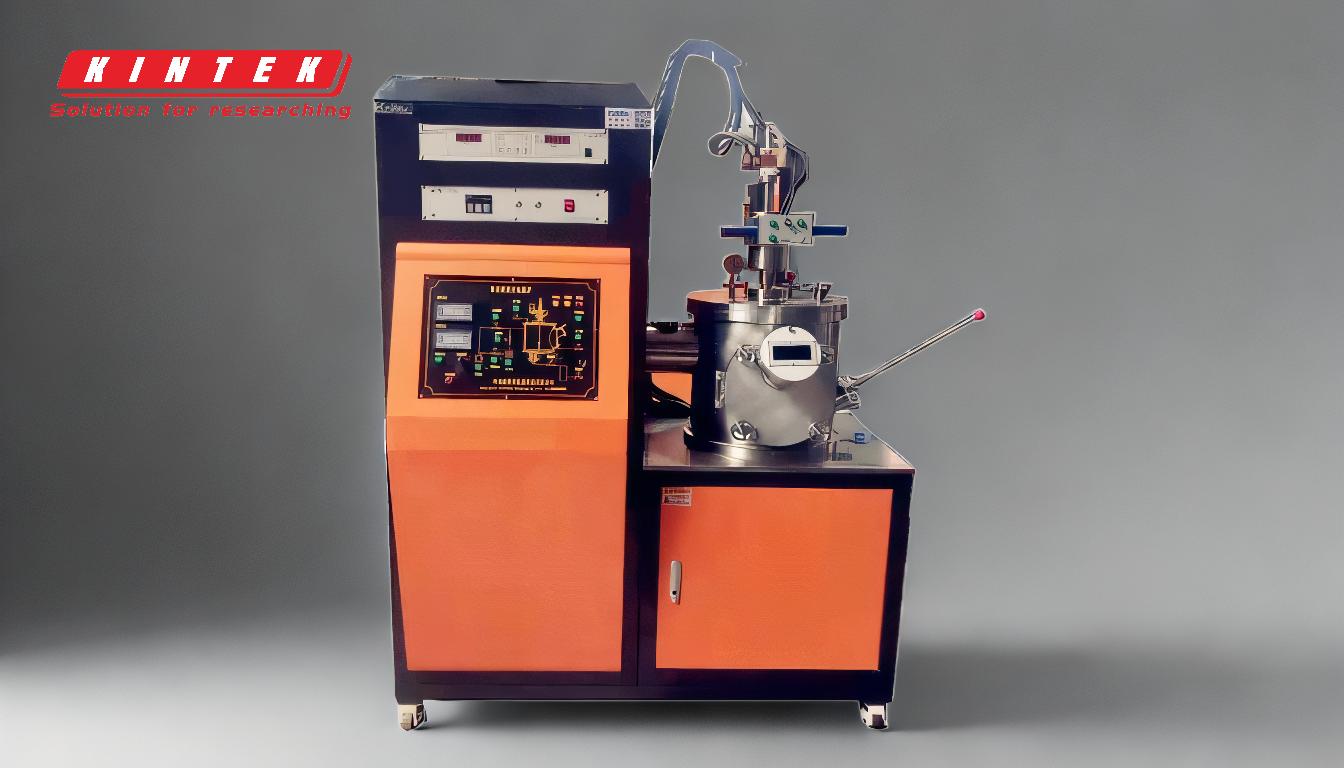
-
Capacidade de temperatura máxima:
- Os fornos de fusão por indução podem atingir temperaturas tão elevadas como 2000℃ como indicado nas referências. Este facto torna-os adequados para a fusão de metais a alta temperatura, como o aço, o ferro e outras ligas. A alta temperatura é alcançada através de um acoplamento indutivo eficiente entre a bobina e os materiais de carga, garantindo um aquecimento rápido e uniforme.
-
Controlo da temperatura de drenagem:
- A temperatura de drenagem do forno é normalmente mantida entre 100°F (37°C) e 65°C (150°F) . Esta gama assegura que o metal fundido está a uma temperatura óptima para vazamento ou processamento posterior. Um interrutor fixo da temperatura de drenagem do forno é frequentemente definido em 79°C (175°F) que actua como um mecanismo de segurança. Se a temperatura exceder este limiar, a fonte de alimentação é automaticamente desligada, evitando o sobreaquecimento e potenciais danos no forno. O interrutor é reiniciado quando a temperatura arrefece abaixo de 165°F (73°C) .
-
Consistência e uniformidade da temperatura:
- Uma das principais vantagens dos fornos de fusão por indução é a sua capacidade de manter distribuição uniforme da temperatura em todo o metal fundido. Isto é conseguido através do campo magnético de média frequência, que proporciona agitação magnética. Esta ação de agitação não só assegura uma temperatura uniforme, como também melhora a composição química consistência do metal e ajuda na remoção de impurezas ou escórias.
-
Flexibilidade e segurança operacional:
- Os fornos de fusão por indução são concebidos com caraterísticas avançadas, tais como Conversão de frequência IGBT e regulação da potência que permitem um funcionamento flexível e suave. Estes fornos podem funcionar continuamente durante 24 horas tornando-os ideais para aplicações industriais. Além disso, estão equipados com funções de proteção abrangentes incluindo proteção contra sobreintensidade, falta de água, sobreaquecimento, sobretensão, curto-circuito e perda de fase. Estas caraterísticas garantem uma maior fiabilidade, durabilidade e segurança durante o funcionamento.
-
Eficiência energética e benefícios ambientais:
- Os fornos de fusão por indução são energeticamente eficiente e amigos do ambiente. Oferecem operações mais limpas com menor produção de resíduos , maior controlo das emissões e níveis de ruído reduzidos . A transmissão eficiente de calor e a distribuição uniforme da temperatura contribuem para perdas por oxidação reduzidas e custos operacionais mais baixos .
-
Conceção e portabilidade:
- Os modernos fornos de fusão por indução são concebidos para serem compacto , leve e portátil . Ocupam menos de um metro quadrado de espaço, tornando-os adequados para pequenas oficinas ou instalações com espaço limitado. Os corpos do forno são facilmente substituíveis, permitindo flexibilidade no manuseamento de diferentes materiais, pesos e métodos de arranque.
-
Tempo e eficiência da fundição:
- O tempo de fundição por forno é normalmente 20-30 minutos , o que é relativamente rápido em comparação com os métodos de fusão tradicionais. Esta eficiência, combinada com a capacidade de funcionar continuamente, torna os fornos de fusão por indução ferramentas altamente produtivas para aplicações industriais.
Em resumo, a gama de temperaturas de um forno de fusão por indução é um fator crítico que determina a sua adequação a várias aplicações de fusão de metais. Com uma capacidade de temperatura máxima de 2000℃ e um controlo preciso das temperaturas de drenagem, estes fornos oferecem uma combinação de elevado desempenho, segurança e eficiência. As suas caraterísticas avançadas, como a conversão de frequência IGBT, agitação magnética e mecanismos de proteção abrangentes, tornam-nos uma escolha fiável para as indústrias que requerem processos de fusão de metais consistentes e de alta qualidade.
Quadro de resumo:
Caraterística | Detalhes |
---|---|
Temperatura máxima | Até 2000℃ adequado para a fusão de aço, ferro e ligas de alta temperatura. |
Gama de temperaturas de drenagem | 100°F (37°C) para 65°C (150°F) com corte de segurança a 79°C (175°F) . |
Aquecimento uniforme | Obtido através de agitação magnética para uma distribuição consistente da temperatura. |
Segurança operacional | Inclui mecanismos de proteção contra sobreintensidades, sobreaquecimento e perda de fase. |
Eficiência energética | Reduz as perdas por oxidação, as emissões e os custos operacionais. |
Tempo de fundição | 20-30 minutos por forno, ideal para uma utilização industrial contínua. |
Pronto para otimizar o seu processo de fusão de metais? Contacte-nos hoje para encontrar o forno de fusão por indução perfeito para as suas necessidades!