Uma mufla é um equipamento crítico em laboratórios e ambientes industriais, usado principalmente para aplicações de alta temperatura, como incineração, tratamento térmico e testes de materiais. As configurações de um forno mufla, principalmente sua faixa de temperatura, são determinadas pela aplicação específica, pelos materiais que estão sendo processados e pelo projeto do forno. Os fornos mufla de alta temperatura normalmente operam entre 1.000°C e 2.000°C, enquanto os modelos de laboratório geralmente variam de 1.100°C a 1.200°C. Os principais fatores que influenciam o desempenho do forno incluem o tipo de material que está sendo aquecido, a fonte de combustível (eletricidade ou gás), as condições ambientais e recursos de segurança como controle de temperatura e sensores de desligamento automático. O posicionamento e a ventilação adequados também desempenham um papel significativo na garantia da eficiência ideal de aquecimento e da longevidade do forno.
Pontos-chave explicados:
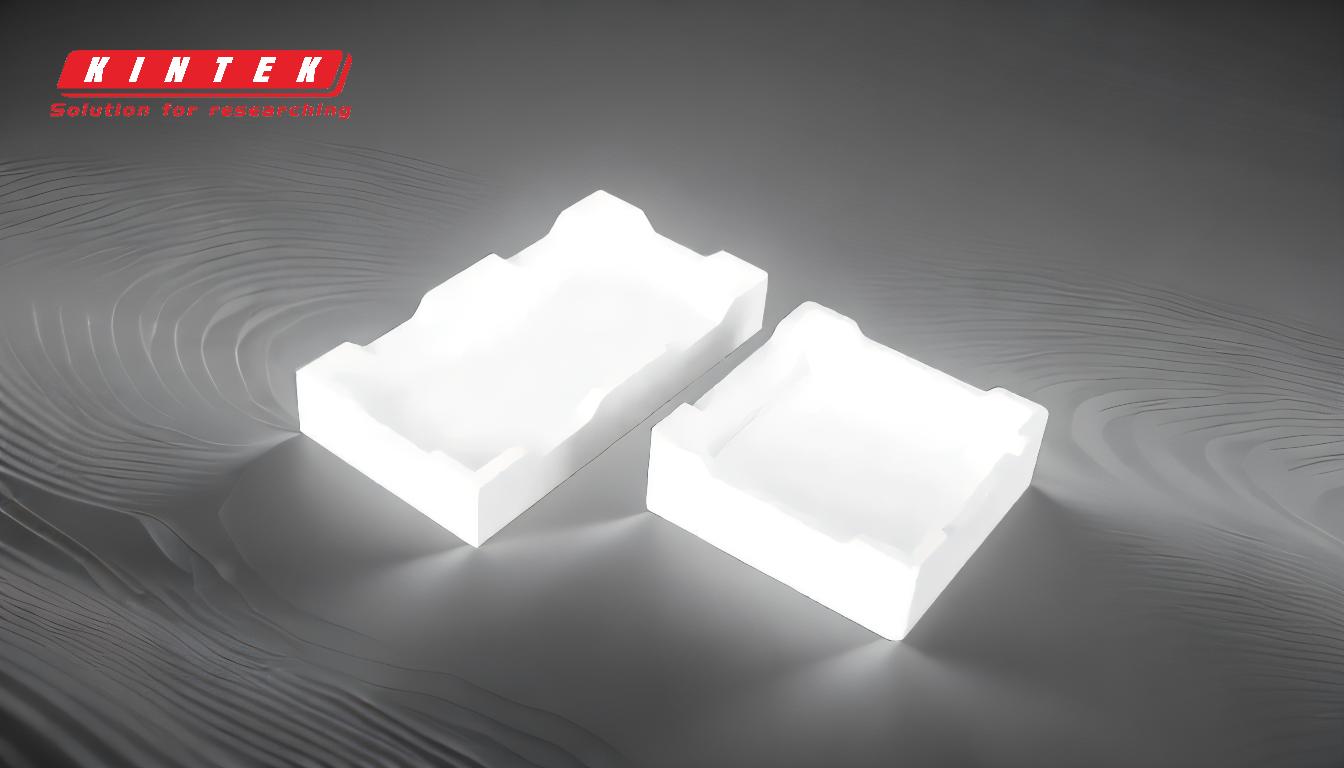
-
Faixa de temperatura:
- O ajuste de temperatura de um mufla depende do uso pretendido. Os modelos de alta temperatura normalmente operam entre 1.000°C e 2.000°C, enquanto os fornos de laboratório são projetados para 1.100°C a 1.200°C. Alguns modelos especializados podem atingir até 1200°C, tornando-os adequados para aplicações como incineração e tratamento térmico.
- A faixa de temperatura escolhida deve estar alinhada com os requisitos específicos do material ou processo que está sendo conduzido. Por exemplo, a incineração de amostras orgânicas pode exigir temperaturas mais baixas, enquanto a sinterização de cerâmicas ou metais pode necessitar de temperaturas mais altas.
-
Considerações materiais:
- O tipo de material que está sendo aquecido influencia significativamente as configurações do forno. Os materiais comuns incluem borossilicato, alumina, carboneto de silício e aço carbono. Cada material possui propriedades térmicas únicas, que determinam a faixa ideal de temperatura e a duração do aquecimento.
- Por exemplo, os elementos de aquecimento de carboneto de silício são ideais para aplicações de alta temperatura devido à sua durabilidade e condutividade térmica, enquanto a alumina é preferida pela sua resistência ao choque térmico.
-
Fonte de Combustível e Eficiência Energética:
- Os fornos mufla podem ser alimentados por eletricidade ou gás (por exemplo, propano ou gás natural). Fornos elétricos são mais comuns em laboratórios devido à sua facilidade de uso e controle preciso de temperatura. As unidades movidas a gás, por outro lado, são frequentemente utilizadas em aplicações industriais onde são necessárias temperaturas mais elevadas.
- A eficiência energética é um benefício importante dos fornos mufla, pois são projetados para minimizar a perda de calor e maximizar a condutividade térmica, reduzindo os custos operacionais.
-
Fatores Ambientais e de Colocação:
- O ambiente circundante, incluindo ventilação e temperatura ambiente, pode afetar o desempenho do forno. O posicionamento adequado garante um fluxo de ar adequado, evitando o superaquecimento e prolongando a vida útil dos elementos de aquecimento.
- Os elementos internos do forno são protegidos do contato direto com vapores e gases, o que aumenta sua durabilidade em comparação aos fornos elétricos tradicionais.
-
Recursos de segurança e controle:
- Os fornos mufla modernos são equipados com recursos de segurança avançados, como sensores de corte automático e controladores de temperatura, para evitar superaquecimento e garantir um desempenho consistente. Esses recursos são essenciais para manter a integridade das amostras e proteger o equipamento.
- A integração do software permite programação e monitoramento precisos da temperatura, facilitando a obtenção de aquecimento uniforme e resultados repetíveis.
-
Tamanho e design da câmara:
- As dimensões da câmara do forno e as opções de abertura da porta são considerações importantes, especialmente ao processar amostras grandes ou de formato irregular. Uma câmara bem projetada garante distribuição uniforme de calor e manuseio eficiente de amostras.
- O elemento de aquecimento e a fonte de alimentação devem ser compatíveis com o uso pretendido, garantindo uma operação confiável e desempenho consistente.
Ao considerar cuidadosamente esses fatores, os usuários podem otimizar as configurações de sua mufla para atender aos requisitos específicos da aplicação, garantindo uma operação eficiente e confiável.
Tabela Resumo:
Fator-chave | Detalhes |
---|---|
Faixa de temperatura | 1000°C–2000°C (alta temperatura), 1100°C–1200°C (modelos de laboratório) |
Considerações materiais | Borossilicato, alumina, carboneto de silício, aço carbono |
Fonte de combustível | Eletricidade (controle preciso) ou gás (temperaturas mais altas) |
Fatores Ambientais | Colocação, ventilação e temperatura ambiente adequadas |
Recursos de segurança | Sensores de corte automático, controladores de temperatura, integração de software |
Projeto de Câmara | Dimensões, opções de portas e compatibilidade de elementos de aquecimento |
Precisa de ajuda para otimizar as configurações do seu forno mufla? Contate nossos especialistas hoje para soluções personalizadas!