A temperatura de calcinação influencia significativamente as propriedades das nanopartículas, incluindo o seu tamanho, morfologia, cristalinidade e caraterísticas de superfície.As temperaturas de calcinação mais elevadas conduzem geralmente a um aumento da cristalinidade e a uma redução da área de superfície devido à aglomeração e sinterização das partículas.No entanto, temperaturas excessivas podem causar transformações de fase indesejáveis ou degradação.As temperaturas óptimas de calcinação são cruciais para obter as propriedades desejadas, tais como uma maior atividade catalítica ou uma melhor resistência mecânica, dependendo da aplicação.Compreender a relação entre a temperatura de calcinação e as propriedades das nanopartículas é essencial para adaptar os materiais a utilizações específicas.
Pontos-chave explicados:
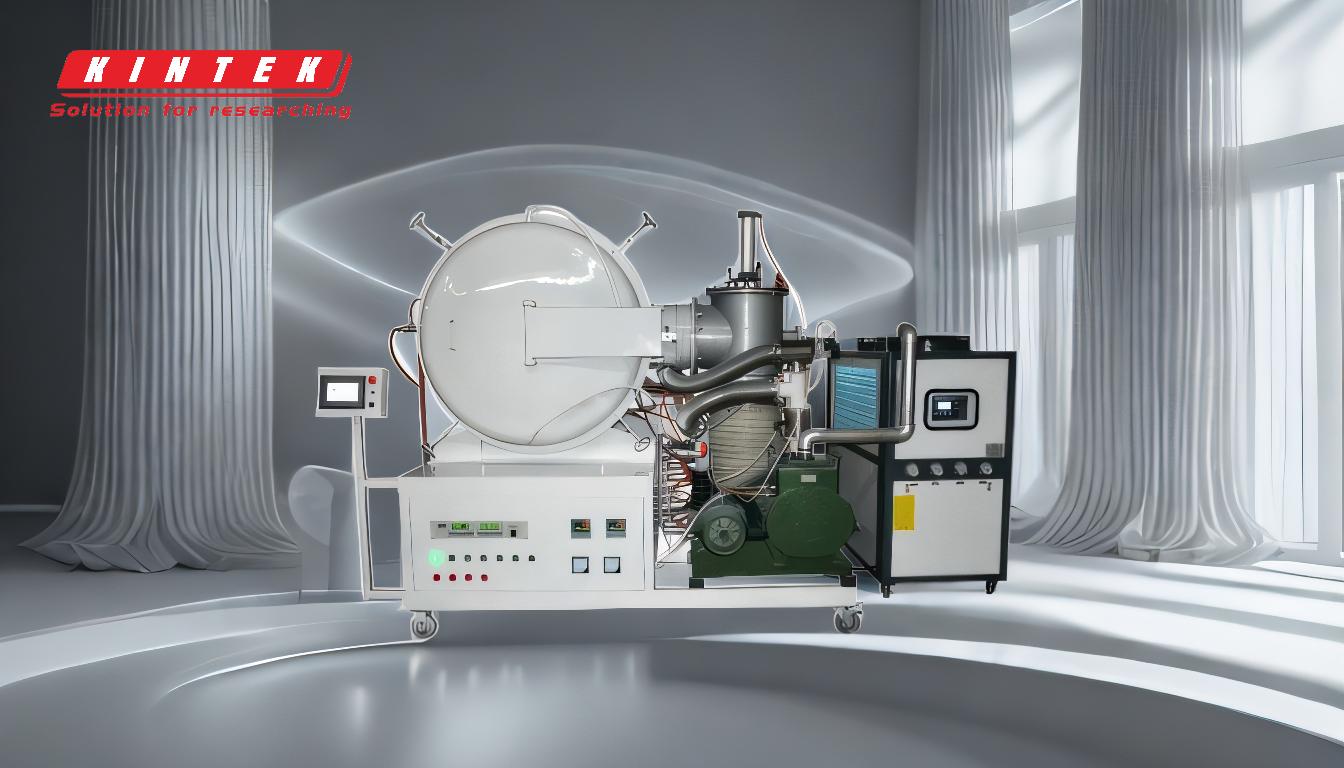
-
Efeito no tamanho das partículas e na aglomeração:
- Temperaturas de calcinação mais elevadas resultam frequentemente em tamanhos de partículas maiores devido a uma maior aglomeração e sinterização.
- Com o aumento da temperatura, as nanopartículas tendem a fundir-se, reduzindo a área de superfície e aumentando o tamanho das partículas.
- Este facto pode ser prejudicial para aplicações que exijam uma área de superfície elevada, como a catálise ou a adsorção.
-
Impacto na cristalinidade:
- A calcinação promove a cristalização ao fornecer a energia necessária para que os átomos se reorganizem em estruturas ordenadas.
- As temperaturas mais elevadas aumentam a cristalinidade, conduzindo a estruturas cristalinas mais definidas e a propriedades mecânicas melhoradas.
- No entanto, temperaturas excessivas podem causar transformações de fase ou degradação, alterando as propriedades pretendidas do material.
-
Área de superfície e porosidade:
- A área de superfície normalmente diminui com o aumento da temperatura de calcinação devido à densificação das partículas e ao colapso dos poros.
- Áreas de superfície mais baixas podem reduzir a reatividade em aplicações catalíticas, mas podem melhorar a estabilidade em ambientes de alta temperatura.
- A otimização da temperatura de calcinação é essencial para equilibrar a área de superfície e a integridade estrutural.
-
Estabilidade e transformação de fases:
- A temperatura de calcinação pode induzir transformações de fase, como a conversão de materiais amorfos em fases cristalinas ou a alteração das estruturas cristalinas.
- Por exemplo, em óxidos metálicos, temperaturas mais altas podem levar à formação de fases estáveis como rutilo a partir de anatase em TiO₂.
- A compreensão dessas transformações é fundamental para aplicações que exigem propriedades de fase específicas.
-
Propriedades térmicas e mecânicas:
- As temperaturas de calcinação mais elevadas melhoram geralmente a estabilidade térmica e a resistência mecânica devido ao aumento da cristalinidade e à redução dos defeitos.
- No entanto, temperaturas excessivas podem levar à fragilidade ou fissuração, comprometendo o desempenho mecânico.
- A adaptação das condições de calcinação é vital para alcançar o equilíbrio desejado entre resistência e flexibilidade.
-
Considerações específicas da aplicação:
- Catálise:As temperaturas de calcinação mais baixas são frequentemente preferidas para manter uma elevada área de superfície e reatividade.
- Materiais estruturais:Poderão ser necessárias temperaturas mais elevadas para obter resistência mecânica e estabilidade térmica suficientes.
- Aplicações ópticas e electrónicas:É necessário um controlo preciso da temperatura de calcinação para otimizar propriedades como o bandgap e a condutividade.
-
Otimização experimental:
- Os investigadores utilizam frequentemente técnicas como a análise termogravimétrica (TGA) e a difração de raios X (XRD) para determinar a temperatura de calcinação ideal para um material específico.
- São efectuados estudos sistemáticos para avaliar os efeitos da temperatura em propriedades como a cristalinidade, a área de superfície e a composição das fases.
Em resumo, a temperatura de calcinação é um parâmetro crítico na síntese de nanopartículas, influenciando o tamanho, a cristalinidade, a área de superfície e a estabilidade da fase.Ao controlar cuidadosamente esta variável, os investigadores podem adaptar as nanopartículas a aplicações específicas, equilibrando propriedades como a reatividade, a resistência e a estabilidade térmica.
Tabela de resumo:
Propriedade | Efeito de uma temperatura de calcinação mais elevada | Implicações para a aplicação |
---|---|---|
Tamanho das partículas | Aumenta devido à aglomeração e sinterização. | Prejudicial para necessidades de elevada área superficial, como a catálise. |
Cristalinidade | Aumenta a cristalinidade, melhorando as propriedades mecânicas. | É benéfico para materiais estruturais, mas pode causar degradação de fase se for excessivo. |
Área de superfície e porosidade | Diminui devido à densificação e ao colapso dos poros. | Reduz a reatividade mas melhora a estabilidade em ambientes de alta temperatura. |
Estabilidade de fase | Induz transformações de fase (por exemplo, de amorfo para cristalino). | Crítico para aplicações que requerem propriedades de fase específicas. |
Térmicas e mecânicas | Melhora a estabilidade térmica e a resistência, mas pode causar fragilidade a temperaturas excessivas. | Adaptar as condições para equilibrar a resistência e a flexibilidade. |
Aplicação específica | Varia: temperaturas mais baixas para catálise, mais altas para materiais estruturais, controlo preciso para ótica/eletrónica. | Optimize a reatividade, a resistência ou a condutividade com base nas necessidades da aplicação. |
Precisa de ajuda para otimizar as temperaturas de calcinação para a sua síntese de nanopartículas? Contacte os nossos especialistas hoje mesmo !