A capacidade de um forno de indução varia significativamente em função da sua conceção, aplicação e fonte de energia.Os fornos de indução são amplamente utilizados na indústria para a fusão de metais e a sua capacidade pode variar desde pequenas unidades à escala laboratorial (alguns quilogramas) até grandes fornos industriais capazes de lidar com várias toneladas de metal fundido.A capacidade é influenciada por factores como o tipo de forno de indução (sem núcleo ou de canal), a fonte de alimentação (baseada em IGBT ou outra) e os requisitos específicos da aplicação.Por exemplo, os fornos de indução baseados em IGBT são conhecidos pela sua eficiência e controlo preciso, o que os torna adequados tanto para operações de pequena como de grande escala.Compreender os requisitos de capacidade é crucial para selecionar o forno certo para uma determinada aplicação, garantindo um desempenho ótimo e uma boa relação custo-eficácia.
Pontos-chave explicados:
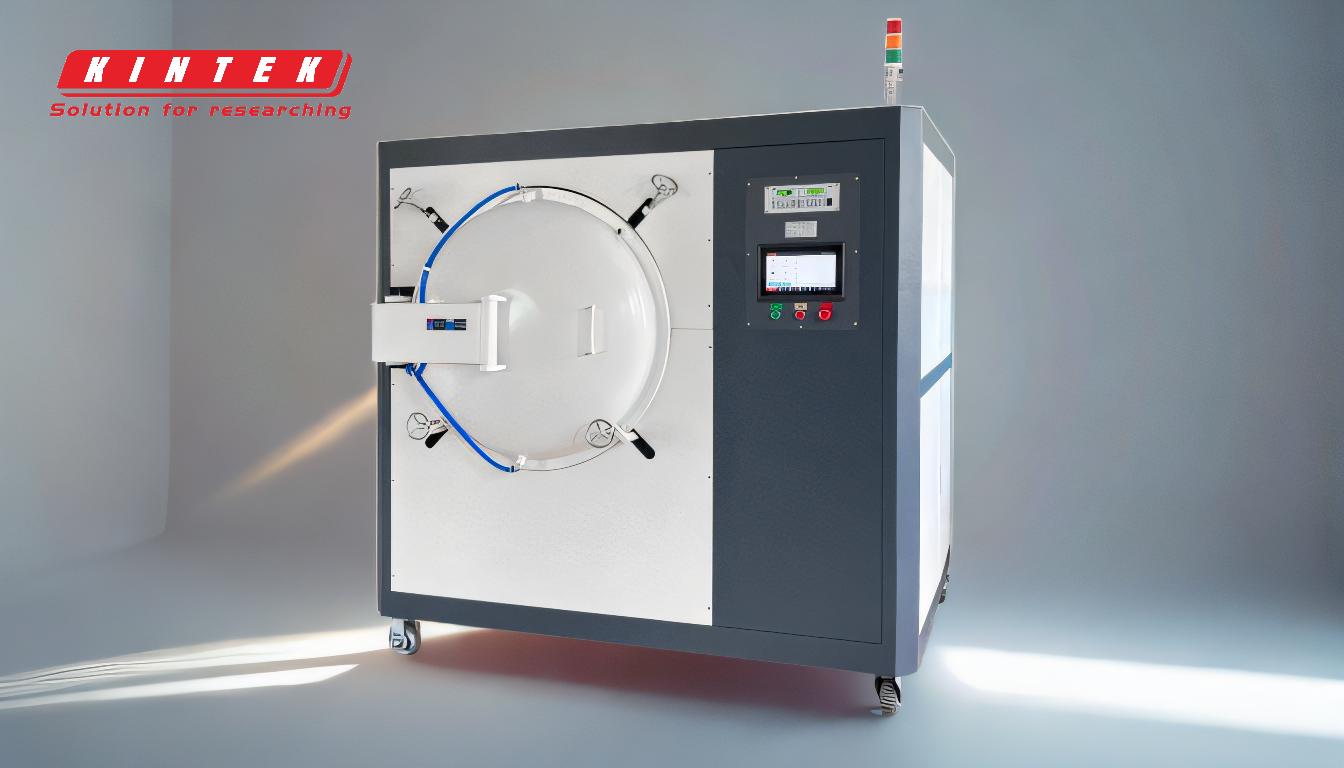
-
Definição e tipos de fornos de indução:
- Os fornos de indução são utilizados para fundir metais utilizando a indução electromagnética.São classificados em dois tipos principais: fornos sem núcleo e fornos de canal.
- Os fornos sem núcleo são mais versáteis e podem lidar com uma vasta gama de capacidades, enquanto os fornos de canal são normalmente utilizados para processos de fusão contínua.
- A escolha entre estes tipos depende da aplicação específica e da capacidade necessária.
-
Gama de capacidades:
-
A capacidade de um forno de indução pode variar entre alguns quilogramas e várias toneladas.Por exemplo:
- Fornos de pequena dimensão: 1 kg a 500 kg, frequentemente utilizados em laboratórios ou pequenas fundições.
- Fornos de média dimensão: 500 kg a 5 toneladas, adequados para operações industriais de média dimensão.
- Fornos de grande dimensão: 5 toneladas a 50 toneladas ou mais, utilizados em grandes fundições e siderurgias.
- A capacidade é determinada pela conceção do forno, pela fonte de alimentação e pelo sistema de arrefecimento.
-
A capacidade de um forno de indução pode variar entre alguns quilogramas e várias toneladas.Por exemplo:
-
Papel da tecnologia IGBT:
- A tecnologia IGBT (Insulated Gate Bipolar Transistor) revolucionou os fornos de indução ao proporcionar um controlo de potência eficiente e preciso.
- Os fornos de indução IGBT são capazes de lidar com uma ampla gama de capacidades, de pequenas a grandes, devido à sua capacidade de fornecer energia de alta frequência com perda mínima de energia.
- Esta tecnologia permite um melhor controlo da temperatura, tempos de fusão mais rápidos e custos operacionais reduzidos, tornando-a ideal tanto para aplicações de pequena como de grande escala.
-
Factores que influenciam a capacidade:
- Fonte de alimentação:A potência do forno afecta diretamente a sua capacidade.Potências mais elevadas permitem capacidades maiores e tempos de fusão mais rápidos.
- Sistema de arrefecimento:Um arrefecimento eficiente é essencial para manter o desempenho do forno, especialmente em capacidades mais elevadas.
- Tipo de material:O tipo de metal que está a ser fundido (por exemplo, aço, alumínio, cobre) também influencia a capacidade do forno, uma vez que os diferentes metais têm pontos de fusão e propriedades térmicas diferentes.
- Projeto do forno:As dimensões físicas e a conceção do forno, incluindo o tamanho do cadinho e a configuração da bobina, desempenham um papel significativo na determinação da sua capacidade.
-
Aplicações e critérios de seleção:
- Os fornos de indução são utilizados em várias indústrias, incluindo a automóvel, a aeroespacial e a da joalharia.
- Ao selecionar um forno de indução, é essencial considerar a capacidade necessária, o tipo de metal a fundir e o ambiente operacional.
- Para aplicações de pequena escala, como laboratórios de investigação ou trabalhos artesanais em metal, um forno com uma capacidade de 1-100 kg pode ser suficiente.Em contrapartida, as operações industriais em grande escala podem exigir fornos com capacidades superiores a 10 toneladas.
-
Vantagens dos fornos de indução de alta capacidade:
- Os fornos de alta capacidade são ideais para a produção em grande escala, oferecendo taxas de fusão mais rápidas e maior rendimento.
- São mais eficientes do ponto de vista energético quando funcionam a plena capacidade, reduzindo os custos de energia por unidade.
- As caraterísticas avançadas, como o controlo automático da temperatura e a monitorização em tempo real, aumentam a eficiência e a segurança operacionais.
-
Desafios e considerações:
- Os fornos de elevada capacidade requerem um investimento inicial e infra-estruturas significativos, incluindo sistemas robustos de fornecimento de energia e de refrigeração.
- Os custos operacionais e de manutenção podem ser mais elevados para os fornos de grandes dimensões, o que exige um planeamento e um orçamento cuidadosos.
- A formação adequada dos operadores é crucial para garantir uma operação segura e eficiente, especialmente em capacidades mais elevadas.
Ao compreender estes pontos-chave, os compradores podem tomar decisões informadas ao selecionar um forno de indução que satisfaça os seus requisitos operacionais e de capacidade específicos.Quer se trate de trabalho de precisão em pequena escala ou de produção industrial em grande escala, o forno correto pode aumentar significativamente a produtividade e a eficiência de custos.
Tabela de resumo:
Gama de capacidades | Aplicações |
---|---|
1 kg - 500 kg | Laboratórios, pequenas fundições |
500 kg - 5 toneladas | Operações industriais de média dimensão |
5 toneladas - 50+ toneladas | Grandes fundições, siderurgias |
Factores-chave | Detalhes |
---|---|
Fonte de alimentação | Maior potência permite maiores capacidades |
Sistema de arrefecimento | Essencial para um desempenho de elevada capacidade |
Tipo de material | Influencia os pontos de fusão e a capacidade |
Conceção do forno | Tamanho do cadinho, configuração da bobina |
Precisa de ajuda para selecionar o forno de indução certo? Contacte hoje mesmo os nossos especialistas para soluções à medida!