Uma atmosfera inerte para recozimento refere-se a um ambiente controlado em que os gases reactivos, como o oxigénio, são substituídos por gases não reactivos (inertes), como o azoto ou o árgon. Este ambiente evita a oxidação, a descarbonetação e a contaminação da superfície do metal durante o processo de recozimento, garantindo resultados de elevada qualidade. As atmosferas inertes são particularmente cruciais para o recozimento de aços inoxidáveis e metais não ferrosos, uma vez que protegem o material de reacções químicas que poderiam comprometer as suas propriedades. A utilização de gases inertes de elevada pureza (por exemplo, 99,99% de pureza) e de sistemas de controlo precisos nos fornos aumenta ainda mais a eficácia do processo de recozimento.
Pontos-chave explicados:
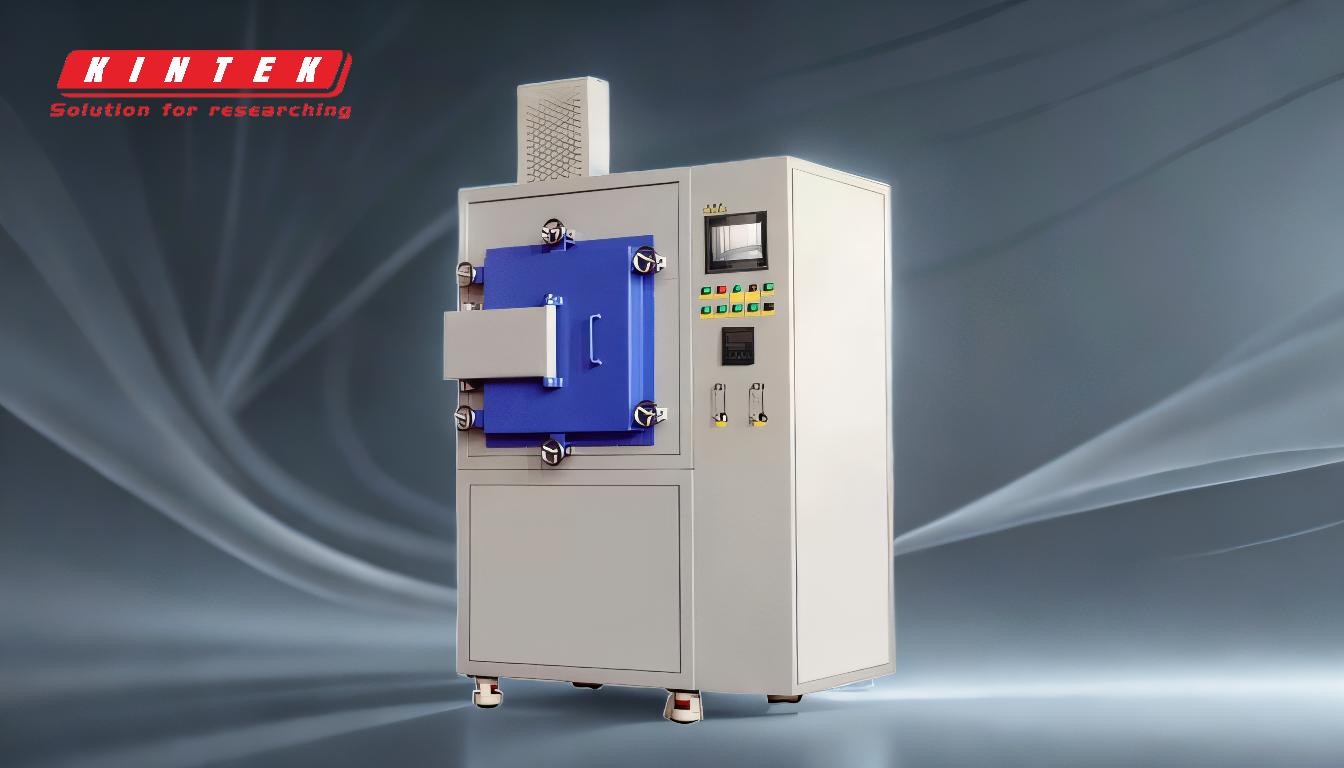
-
Definição de uma Atmosfera Inerte:
- Uma atmosfera inerte é um ambiente controlado em que os gases reactivos (por exemplo, o oxigénio) são substituídos por gases não reactivos, como o azoto ou o árgon.
- Este ambiente foi concebido para evitar reacções químicas indesejadas, como a oxidação ou a descarbonetação, durante os processos de tratamento térmico, como o recozimento.
-
Objetivo da utilização de uma atmosfera inerte no recozimento:
- Prevenção da oxidação: A oxidação ocorre quando os metais reagem com o oxigénio, levando à formação de incrustações na superfície. Uma atmosfera inerte elimina o oxigénio, impedindo esta reação.
- Evitar a descarbonetação: A descarbonetação é a perda de carbono da superfície do aço, o que pode enfraquecer o material. Os gases inertes evitam esta situação, criando um ambiente não reativo.
- Reduzir a contaminação: As atmosferas inertes minimizam o risco de contaminação por impurezas, assegurando que o metal mantém as suas propriedades desejadas.
- Melhorar a reprodutibilidade: Ao manter um ambiente consistente, as atmosferas inertes asseguram resultados de recozimento fiáveis e repetíveis.
-
Tipos de gases inertes utilizados:
- Nitrogénio: O gás inerte mais utilizado devido à sua relação custo-eficácia e à sua natureza não reactiva com o aço. Está amplamente disponível e proporciona uma excelente proteção contra a oxidação.
- Árgon: Outra escolha popular, especialmente para aplicações que exigem maior pureza ou quando o azoto pode reagir com determinados materiais. O árgon é mais denso do que o azoto, proporcionando uma melhor proteção em alguns casos.
- Hidrogénio: Ocasionalmente utilizado em combinação com árgon para aplicações específicas, como o recozimento de aços inoxidáveis, para melhorar a limpeza da superfície e reduzir a formação de óxidos.
-
Aplicações de atmosferas inertes no recozimento:
- Aços inoxidáveis: As atmosferas inertes são essenciais para o recozimento dos aços inoxidáveis para evitar a formação de óxido de crómio, que pode degradar a resistência à corrosão.
- Metais não ferrosos: Metais como o cobre, o alumínio e o titânio beneficiam de atmosferas inertes para evitar a oxidação e manter a qualidade da superfície.
- Tratamentos térmicos especializados: As atmosferas inertes são utilizadas em processos como a colagem, a cura e o tratamento térmico para garantir um controlo preciso das propriedades dos materiais.
-
Equipamentos e sistemas de controlo:
- Fornos de atmosfera de gás inerte: Estes fornos são concebidos com controlos de temperatura de precisão baseados em microprocessadores e isolamento energeticamente eficiente para manter condições consistentes.
- Gases de alta pureza: São utilizados gases inertes com um grau de pureza superior a 99,99% para garantir uma contaminação mínima e um desempenho ótimo.
- Controlo da pressão: A pressão do gás inerte é normalmente mantida dentro de um intervalo específico (por exemplo, 0,05 a 0,07 MPa) para obter o ambiente de proteção desejado.
-
Vantagens da utilização de uma atmosfera inerte:
- Melhoria da qualidade da superfície: Evita a formação de incrustações e mantém uma superfície limpa e sem óxidos.
- Propriedades melhoradas do material: Mantém o teor de carbono e outros elementos críticos, garantindo a resistência e a durabilidade do material.
- Segurança: Reduz o risco de incêndio e de explosões, eliminando os gases reactivos.
- Poupança de custos: Os fornos energeticamente eficientes e os sistemas de controlo precisos optimizam a utilização dos recursos, reduzindo os custos operacionais.
-
Desafios e considerações:
- Custo dos Gases Inertes: Os gases de elevada pureza, como o árgon, podem ser dispendiosos, afectando o custo global do processo de recozimento.
- Manutenção de equipamentos: Os fornos de atmosfera de gás inerte requerem uma manutenção regular para garantir um desempenho consistente e evitar fugas.
- Compatibilidade de materiais: Nem todos os materiais requerem atmosferas inertes, pelo que é essencial avaliar as necessidades específicas do material que está a ser recozido.
Ao compreender estes pontos-chave, os compradores de equipamentos e consumíveis podem tomar decisões informadas sobre a implementação de atmosferas inertes nos seus processos de recozimento, garantindo resultados de alta qualidade e operações económicas.
Quadro de resumo:
Aspeto | Detalhes |
---|---|
Definição | Ambiente controlado com gases não reactivos (por exemplo, azoto, árgon). |
Objetivo | Evita a oxidação, a descarbonetação, a contaminação e assegura a reprodutibilidade. |
Gases inertes utilizados | Azoto (rentável), Árgon (alta pureza), Hidrogénio (especializado). |
Aplicações | Aços inoxidáveis, metais não ferrosos, tratamentos térmicos especializados. |
Equipamento | Fornos de gás inerte com controlos de precisão e gases de alta pureza. |
Benefícios | Melhoria da qualidade da superfície, melhoria das propriedades dos materiais, segurança e poupança de custos. |
Desafios | Custo dos gases inertes, manutenção do equipamento, compatibilidade dos materiais. |
Precisa de ajuda para criar uma atmosfera inerte para recozimento? Contacte os nossos especialistas hoje mesmo para soluções à medida!