O recozimento é um processo de tratamento térmico utilizado para alterar as propriedades físicas e, por vezes, químicas de um material, normalmente metais, para aumentar a ductilidade, reduzir a dureza e melhorar a maquinabilidade. O processo envolve o aquecimento do material a uma temperatura específica, mantendo-o a essa temperatura durante um determinado período e, em seguida, arrefecendo-o a uma velocidade controlada. Existem vários tipos de processos de recozimento, cada um adaptado para alcançar resultados específicos com base no material e na sua utilização pretendida. Estes tipos incluem o recozimento preto, o recozimento azul, o recozimento em caixa, o recozimento brilhante, o recozimento de ciclo, o recozimento de chama, o recozimento completo, a grafitização, o recozimento intermédio, o recozimento isotérmico, o recozimento de processo, o recozimento de têmpera e a esferoidização. Cada tipo de recozimento tem caraterísticas e aplicações únicas, o que torna essencial a escolha do processo correto para as propriedades desejadas do material.
Pontos-chave explicados:
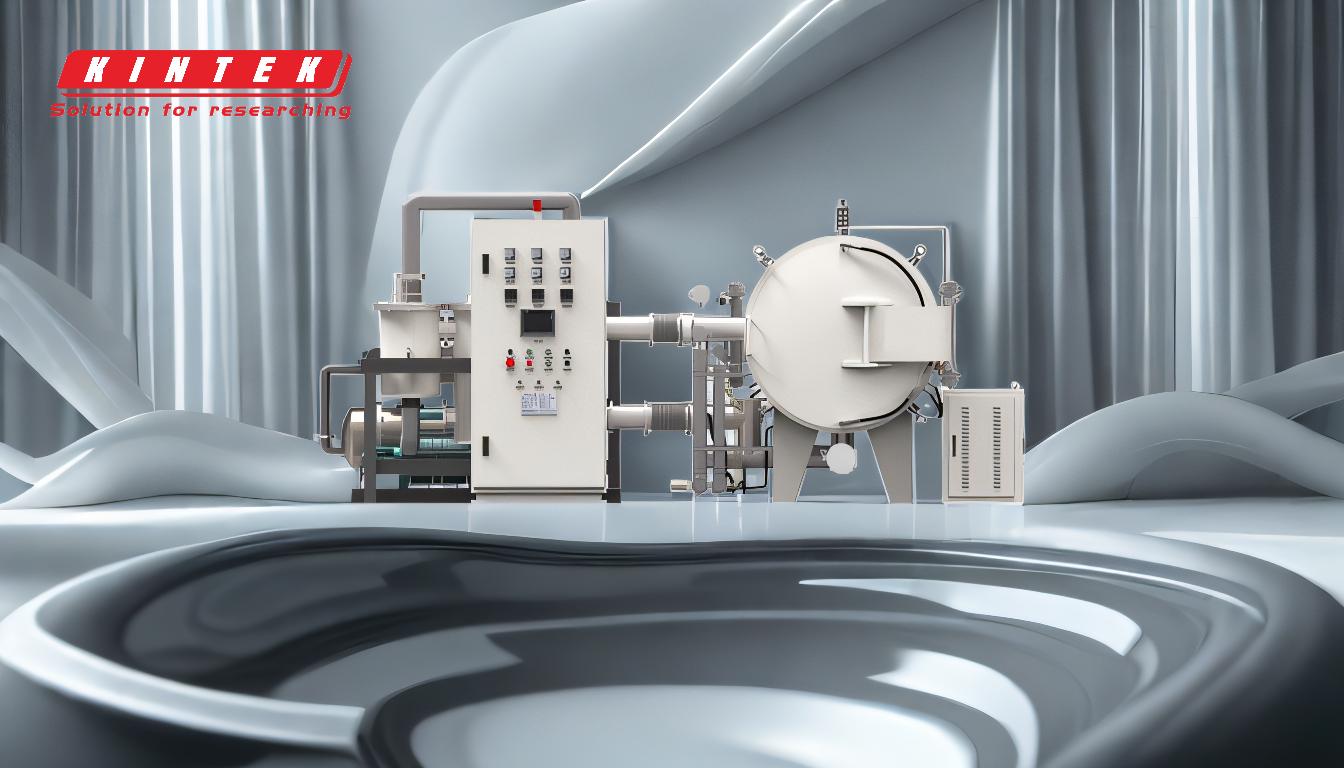
-
Recozimento preto:
- Processo: O material é aquecido num forno com uma atmosfera redutora para evitar a oxidação, resultando numa camada de óxido preto na superfície.
- Aplicação: Normalmente utilizado em chapas e fios de aço para melhorar a ductilidade e reduzir a dureza.
-
Recozimento azul:
- Processo: Semelhante ao recozimento negro, mas efectuado a uma temperatura mais baixa, resultando numa camada de óxido azul.
- Aplicação: Normalmente utilizado em chapas de aço para melhorar a formabilidade e reduzir as tensões internas.
-
Recozimento em caixa:
- Processo: O material é colocado num recipiente selado (caixa) com uma atmosfera controlada e aquecido a uma temperatura específica.
- Aplicação: Utilizado para recozer grandes lotes de chapas, tiras e fios de aço para obter propriedades uniformes.
-
Recozimento brilhante:
- Processo: Conduzido numa atmosfera protetora (por exemplo, hidrogénio ou gás inerte) para evitar a oxidação, resultando numa superfície limpa e brilhante.
- Aplicação: Ideal para aço inoxidável e outros materiais que exijam uma superfície limpa e sem óxido.
-
Ciclo de recozimento:
- Processo: Envolve ciclos repetidos de aquecimento e arrefecimento para obter propriedades específicas do material.
- Aplicação: Utilizado para materiais que requerem um controlo preciso da microestrutura e das propriedades mecânicas.
-
Recozimento por chama:
- Processo: Utiliza uma chama direta para aquecer o material localmente, seguida de um arrefecimento controlado.
- Aplicação: Adequado para o recozimento localizado de componentes de grandes dimensões ou de áreas específicas que exijam uma ductilidade melhorada.
-
Recozimento total:
- Processo: O material é aquecido acima da sua temperatura crítica, mantido durante um período de tempo suficiente e depois arrefecido lentamente no forno.
- Aplicação: Utilizado para obter a máxima suavidade e ductilidade dos aços, facilitando a sua maquinagem ou conformação.
-
Grafitização:
- Processo: Processo especializado de recozimento de ferro fundido para promover a formação de grafite, melhorando a maquinabilidade e reduzindo a fragilidade.
- Aplicação: Utilizado principalmente para componentes de ferro fundido.
-
Recozimento intermédio:
- Processo: Efectuado entre operações de trabalho a frio para restaurar a ductilidade e reduzir a dureza.
- Aplicação: Comum nos processos de fabrico em várias etapas em que os materiais são submetidos a deformações repetidas.
-
Recozimento isotérmico:
- Processo: O material é aquecido a uma temperatura específica, mantido até se formar a microestrutura desejada e depois arrefecido a uma velocidade controlada.
- Aplicação: Utilizado para obter uma microestrutura e propriedades uniformes em aços de alta liga.
-
Processo de recozimento:
- Processo: Processo de recozimento a baixa temperatura utilizado para aliviar tensões internas sem alterar significativamente a microestrutura do material.
- Aplicação: Frequentemente utilizado no fabrico de produtos de aço trabalhados a frio.
-
Recozimento de têmpera:
- Processo: Envolve o arrefecimento rápido (arrefecimento) após o aquecimento para obter propriedades específicas do material.
- Aplicação: Utilizado para materiais que requerem uma combinação de dureza e tenacidade.
-
Esferoidização:
- Processo: Processo de recozimento prolongado que resulta na formação de carbonetos esferoidais, melhorando a maquinabilidade e reduzindo a dureza.
- Aplicação: Normalmente utilizado para aços com elevado teor de carbono e aços para ferramentas.
Cada tipo de processo de recozimento é concebido para obter propriedades específicas do material, sendo crucial selecionar o método adequado com base no material e na sua aplicação pretendida. A compreensão destes processos ajuda a otimizar o tratamento térmico para obter as propriedades mecânicas e físicas desejadas nos metais.
Quadro de resumo:
Tipo de recozimento | Processo | Aplicação |
---|---|---|
Recozimento preto | Aquecimento numa atmosfera redutora para evitar a oxidação, formando uma camada negra | Chapas e fios de aço para melhorar a ductilidade e reduzir a dureza |
Recozimento azul | Semelhante ao recozimento preto, mas a temperaturas mais baixas, formando uma camada azul | Chapas de aço para uma melhor conformabilidade e tensões internas reduzidas |
Recozimento em caixa | Aquecimento num recipiente fechado com uma atmosfera controlada | Grandes lotes de chapas, tiras e fios de aço para obter propriedades uniformes |
Recozimento brilhante | Aquecimento numa atmosfera protetora para evitar a oxidação | Aço inoxidável e materiais que requerem uma superfície limpa e sem óxido |
Ciclo de recozimento | Ciclos repetidos de aquecimento e arrefecimento | Materiais que exigem um controlo preciso da microestrutura e das propriedades mecânicas |
Recozimento por chama | Aquecimento localizado com chama direta, seguido de arrefecimento controlado | Componentes de grandes dimensões ou áreas específicas que necessitem de uma ductilidade melhorada |
Recozimento total | Aquecimento acima da temperatura crítica e arrefecimento lento | Obtenção da máxima suavidade e ductilidade nos aços |
Grafitização | Promove a formação de grafite no ferro fundido | Componentes em ferro fundido para melhor maquinabilidade e menor fragilidade |
**Recozimento intermédio | Efectuado entre operações de trabalho a frio | Processos de fabrico em várias etapas para restaurar a ductilidade |
Recozimento isotérmico | Aquecimento a uma temperatura específica e arrefecimento controlado | Aços de alta liga para uma microestrutura e propriedades uniformes |
Processo de recozimento | Recozimento a baixa temperatura para aliviar as tensões internas | Produtos de aço trabalhados a frio |
Recozimento de têmpera | Arrefecimento rápido após aquecimento | Materiais que requerem uma combinação de dureza e tenacidade |
Esferoidização | Recozimento prolongado para formar carbonetos esferoidais | Aços com elevado teor de carbono e aços para ferramentas para uma melhor maquinabilidade |
Precisa de ajuda para selecionar o processo de recozimento adequado para os seus materiais? Contacte os nossos especialistas hoje mesmo para soluções à medida!