A austêmpera é um processo de tratamento térmico que oferece várias vantagens, tais como ductilidade melhorada, tenacidade e distorção reduzida em comparação com a têmpera e o revenido tradicionais.No entanto, também tem desvantagens notáveis, incluindo limitações na adequação do material, custos mais elevados e complexidade do processo.O processo não é universalmente aplicável a todos os aços, particularmente aqueles com elevado teor de carbono, e requer um controlo preciso da temperatura e do tempo, o que pode aumentar os custos operacionais.Além disso, a necessidade de equipamento especializado e os tempos de processamento mais longos podem tornar a austêmpera menos eficiente para a produção de grandes volumes.Estes factores devem ser cuidadosamente considerados quando se decide utilizar a austemperagem para uma aplicação específica.
Pontos-chave explicados:
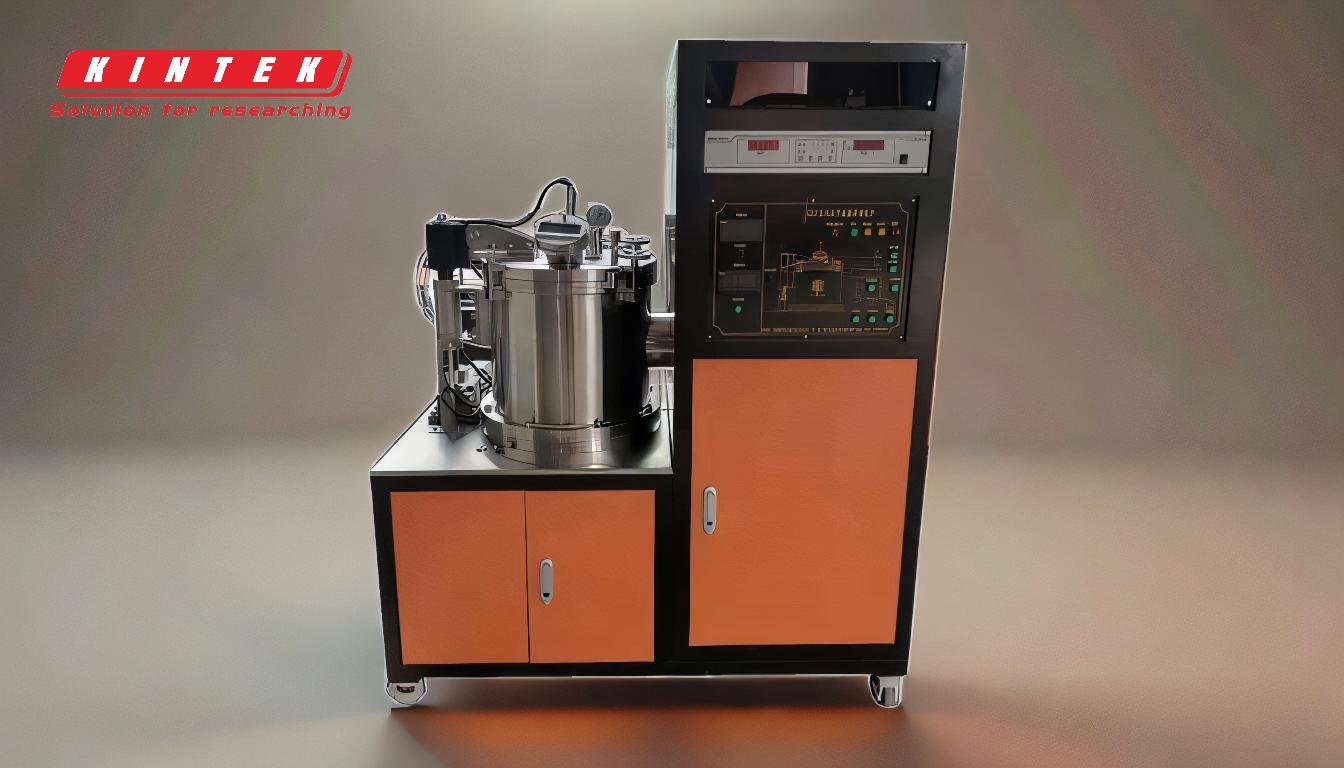
-
Limitações materiais:
- Não adequado para todos os aços:A austêmpera é mais eficaz para os aços de médio teor de carbono e para certas ligas de aço.Os aços com elevado teor de carbono, como os aços para ferramentas, são menos adequados porque podem não atingir a microestrutura desejada (bainite) devido à sua elevada temperabilidade e ao risco de formação de martensite.
- Restrição a aplicações específicas:O processo não é universalmente aplicável e é frequentemente limitado a peças que requerem elevada dureza e resistência ao desgaste, tais como engrenagens, molas e equipamento agrícola.
-
Custos mais elevados:
- Equipamento especializado:A austemperação requer um controlo preciso da temperatura e banhos de têmpera especializados (por exemplo, banhos de sal ou banhos de metal fundido), cuja instalação e manutenção podem ser dispendiosas.
- Tempos de processamento mais longos:O processo envolve manter o material a uma temperatura intermédia durante um período prolongado para formar bainite, o que aumenta o consumo de energia e os custos de mão de obra em comparação com a têmpera e revenido tradicionais.
-
Complexidade do processo:
- Controlo preciso da temperatura e do tempo:A obtenção da microestrutura bainítica desejada requer um controlo rigoroso da temperatura do meio de têmpera e da duração da manutenção isotérmica.Qualquer desvio pode resultar em microestruturas indesejáveis, como a martensite ou a perlite.
- Compatibilidade com espessuras limitadas:As secções mais espessas podem não arrefecer uniformemente, conduzindo a uma microestrutura e propriedades inconsistentes.Isto restringe a austemperação a peças com secções transversais relativamente uniformes.
-
Eficiência reduzida para produção de grandes volumes:
- Tempos de ciclo mais lentos:Os tempos de espera prolongados necessários para a formação de bainite tornam a austêmpera menos adequada para a produção de grandes volumes em que o processamento rápido é essencial.
- Limitações do processamento em lote:O processo é frequentemente efectuado em lotes, o que pode limitar o rendimento em comparação com os métodos de tratamento térmico contínuo.
-
Potencial para resultados inconsistentes:
- Sensibilidade à taxa de arrefecimento:A taxa de arrefecimento deve ser cuidadosamente controlada para evitar a formação de martensite, que pode comprometer as propriedades mecânicas desejadas.
- Dependência do meio de arrefecimento:A eficácia da austêmpera depende da capacidade do meio de têmpera de manter uma temperatura consistente, o que pode ser um desafio em operações de grande escala.
-
Preocupações ambientais e de segurança:
- Utilização de banhos de sal:Os banhos de sal, normalmente utilizados na austêmpera, podem representar riscos ambientais e de segurança devido ao potencial de derrames de sal, fumos e à necessidade de uma eliminação adequada.
- Manuseamento de metais fundidos:Se forem utilizados banhos de metal fundido, são necessárias precauções de segurança adicionais para proteger os trabalhadores contra queimaduras e exposição a materiais perigosos.
Em conclusão, embora a austêmpera ofereça benefícios significativos em termos de propriedades mecânicas e distorção reduzida, as suas desvantagens - tais como limitações de materiais, custos mais elevados, complexidade do processo e eficiência reduzida para a produção de grandes volumes - devem ser cuidadosamente ponderadas.Estes factores tornam-no menos adequado para determinadas aplicações e exigem uma análise cuidadosa dos requisitos específicos da peça a ser tratada.
Tabela de resumo:
Desvantagem | Detalhes |
---|---|
Limitações materiais | Não é adequado para aços com elevado teor de carbono; limitado a aplicações específicas. |
Custos mais elevados | Requer equipamento especializado e tempos de processamento mais longos. |
Complexidade do processo | É necessário um controlo preciso da temperatura e do tempo; compatibilidade limitada da espessura. |
Eficiência reduzida | Tempos de ciclo mais lentos; o processamento em lote limita o rendimento. |
Resultados inconsistentes | Sensibilidade à taxa de arrefecimento; dependência do meio de arrefecimento. |
Riscos ambientais e de segurança | A utilização de banhos de sal e de metais fundidos apresenta riscos. |
Está a considerar a austemperação para a sua aplicação? Contacte os nossos especialistas hoje para discutir as suas necessidades!