O tratamento térmico dos metais é um processo amplamente utilizado para melhorar as propriedades mecânicas, como a dureza, a resistência e a tenacidade.No entanto, apresenta várias desvantagens que podem afetar o desempenho, o custo e a adequação da aplicação do material.Estas desvantagens incluem potenciais distorções ou deformações, tensões residuais, ductilidade reduzida, maior fragilidade e custos mais elevados associados ao consumo de energia e ao equipamento.Além disso, um tratamento térmico incorreto pode conduzir a resultados inconsistentes, tornando crucial o controlo cuidadoso do processo.Abaixo, exploramos estas desvantagens em pormenor para fornecer uma compreensão abrangente dos desafios associados ao tratamento térmico.
Pontos-chave explicados:
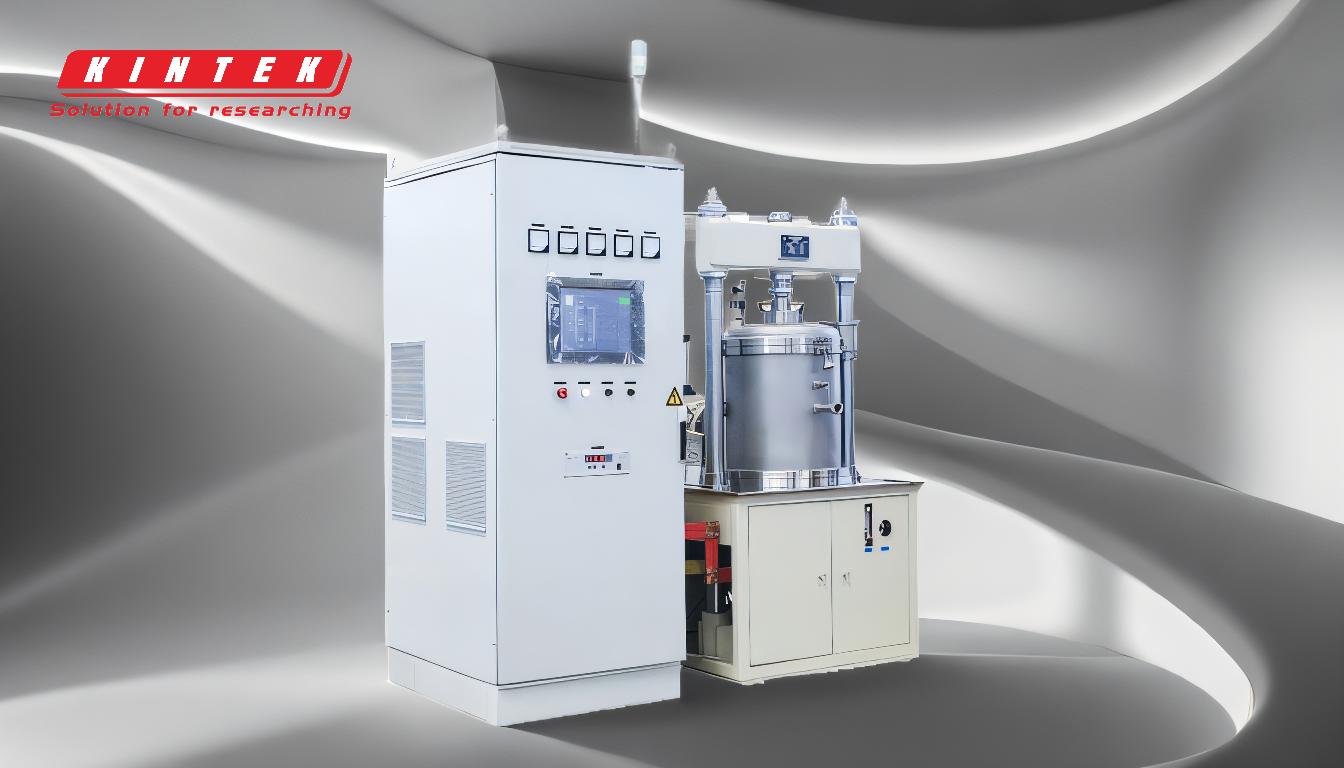
-
Distorção e empenamento
- Durante o tratamento térmico, os metais sofrem alterações significativas de temperatura, o que pode causar expansão e contração irregulares.Isto leva frequentemente à distorção ou deformação do material.
- Os componentes finos ou com formas complexas são particularmente susceptíveis a estes problemas, uma vez que não possuem a integridade estrutural necessária para suportar as tensões térmicas.
- A distorção pode tornar as peças inutilizáveis, exigindo maquinação adicional ou mesmo a sua eliminação, o que aumenta os custos e o desperdício.
-
Tensões residuais
- O arrefecimento rápido, tal como a têmpera, pode introduzir tensões residuais no metal.Estas tensões ocorrem porque as camadas exteriores arrefecem mais rapidamente do que as camadas interiores, criando tensão interna.
- As tensões residuais podem comprometer a integridade estrutural do material, levando a uma falha prematura sob carga ou durante o serviço.
- Podem ser necessários tratamentos de alívio de tensões para mitigar este problema, acrescentando passos e custos adicionais ao processo.
-
Redução da ductilidade e aumento da fragilidade
- Embora o tratamento térmico possa melhorar a dureza e a resistência, reduz frequentemente a ductilidade, tornando o material mais frágil.
- Os materiais frágeis são propensos a fissurar ou fraturar sob impacto ou tensão, limitando a sua adequação a aplicações que exijam tenacidade.
- Por exemplo, o endurecimento excessivo de um componente de aço pode torná-lo demasiado frágil para ser utilizado em ambientes de elevada tensão, como aplicações automóveis ou aeroespaciais.
-
Consumo de energia e impacto ambiental
- Os processos de tratamento térmico, como o recozimento, a têmpera e o revenido, requerem um consumo significativo de energia para atingir e manter temperaturas elevadas.
- Este elevado consumo de energia contribui para o aumento dos custos operacionais e para uma maior pegada de carbono, tornando o tratamento térmico menos amigo do ambiente.
- As indústrias estão a procurar cada vez mais métodos alternativos para reduzir a utilização de energia e o impacto ambiental.
-
Custo do equipamento e manutenção
- O tratamento térmico requer equipamento especializado, como fornos, tanques de têmpera e fornos de revenimento, cuja aquisição e manutenção podem ser dispendiosas.
- É necessária uma manutenção regular para garantir resultados consistentes, o que aumenta o custo global do processo.
- Os fabricantes de pequena escala podem ter dificuldade em justificar o investimento neste tipo de equipamento.
-
Resultados inconsistentes devido a um controlo inadequado
- O tratamento térmico é um processo altamente sensível que requer um controlo preciso da temperatura, das taxas de arrefecimento e do tempo.
- Variações nestes parâmetros podem levar a resultados inconsistentes, como dureza desigual ou transformação incompleta da microestrutura.
- Operadores qualificados e sistemas de monitorização avançados são essenciais para obter resultados fiáveis, aumentando ainda mais os custos.
-
Limitações específicas do material
- Nem todos os metais respondem bem ao tratamento térmico.Por exemplo, algumas ligas podem não atingir as propriedades desejadas ou podem exigir condições extremamente específicas.
- Certos materiais, como o alumínio ou o titânio, têm requisitos únicos de tratamento térmico que podem complicar o processo e limitar a sua eficácia.
- Isto restringe a versatilidade do tratamento térmico como uma solução universal para melhorar as propriedades do metal.
-
Potencial de oxidação da superfície e descarbonetação
- A exposição a temperaturas elevadas pode provocar a oxidação da superfície, levando à formação de incrustações ou camadas de óxido no metal.
- A descarbonetação, a perda de carbono da superfície do aço, pode ocorrer durante o tratamento térmico, reduzindo a dureza e a resistência da superfície.
- Estes problemas necessitam frequentemente de processos de acabamento adicionais, como a retificação ou o revestimento, para restaurar as propriedades superficiais desejadas.
-
Processo moroso
- O tratamento térmico não é um processo rápido.Dependendo do tipo de tratamento e do material, pode demorar horas ou mesmo dias a concluir.
- Este tempo de processamento alargado pode atrasar os programas de produção e aumentar os prazos de entrega, afectando a eficiência global.
- Para as indústrias que requerem uma resposta rápida, podem ser mais adequados métodos alternativos.
-
Riscos para a saúde e segurança
- O tratamento térmico envolve o trabalho com altas temperaturas, materiais inflamáveis (por exemplo, óleos de têmpera) e gases potencialmente perigosos.
- Os operadores devem seguir protocolos de segurança rigorosos para evitar acidentes, tais como queimaduras, incêndios ou exposição a fumos tóxicos.
- A garantia de um ambiente de trabalho seguro aumenta a complexidade e o custo do processo.
Ao compreender estas desvantagens, os fabricantes e engenheiros podem tomar decisões informadas sobre se o tratamento térmico é a escolha certa para a sua aplicação específica.Embora ofereça benefícios significativos, os desafios associados ao processo devem ser cuidadosamente ponderados em relação aos resultados desejados.
Quadro recapitulativo:
Desvantagem | Impacto chave |
---|---|
Distorção e deformação | Expansão/contração irregular, especialmente em peças finas ou complexas. |
Tensões residuais | Tensão interna devido ao arrefecimento rápido, levando a uma falha prematura. |
Ductilidade reduzida | Aumento da fragilidade, tornando os materiais propensos a fissuras. |
Consumo de energia | O elevado consumo de energia aumenta os custos e o impacto ambiental. |
Custos de equipamento | Fornos, tanques de têmpera e manutenção dispendiosos. |
Resultados inconsistentes | Um controlo inadequado conduz a uma dureza desigual ou a transformações incompletas. |
Limitações específicas do material | Nem todos os metais respondem bem ao tratamento térmico. |
Oxidação da superfície | A formação de incrustações e a descarbonetação reduzem a dureza da superfície. |
Demora | Os longos tempos de processamento atrasam os calendários de produção. |
Riscos para a saúde e segurança | Altas temperaturas, materiais inflamáveis e gases perigosos representam riscos. |
Precisa de ajuda para decidir se o tratamento térmico é adequado para a sua aplicação? Contacte hoje os nossos especialistas para obter aconselhamento personalizado!