Um forno de indução funciona utilizando a indução electromagnética para gerar calor dentro de uma carga metálica, permitindo a sua fusão sem contacto direto entre a fonte de calor e o metal.O forno é constituído por uma bobina de cobre que transporta corrente alternada, criando um campo magnético que muda rapidamente.Este campo induz correntes de Foucault no metal, que geram calor devido à resistência eléctrica (aquecimento de Joule).Nos materiais ferromagnéticos, é produzido calor adicional por histerese magnética.O processo é eficiente, preciso e permite a fusão controlada de metais a altas temperaturas, como o aço a 1370°C (2500°F).O forno funciona a frequências médias (300 Hz a 1000 Hz) para otimizar a transferência de energia e a eficiência do aquecimento.
Pontos-chave explicados:
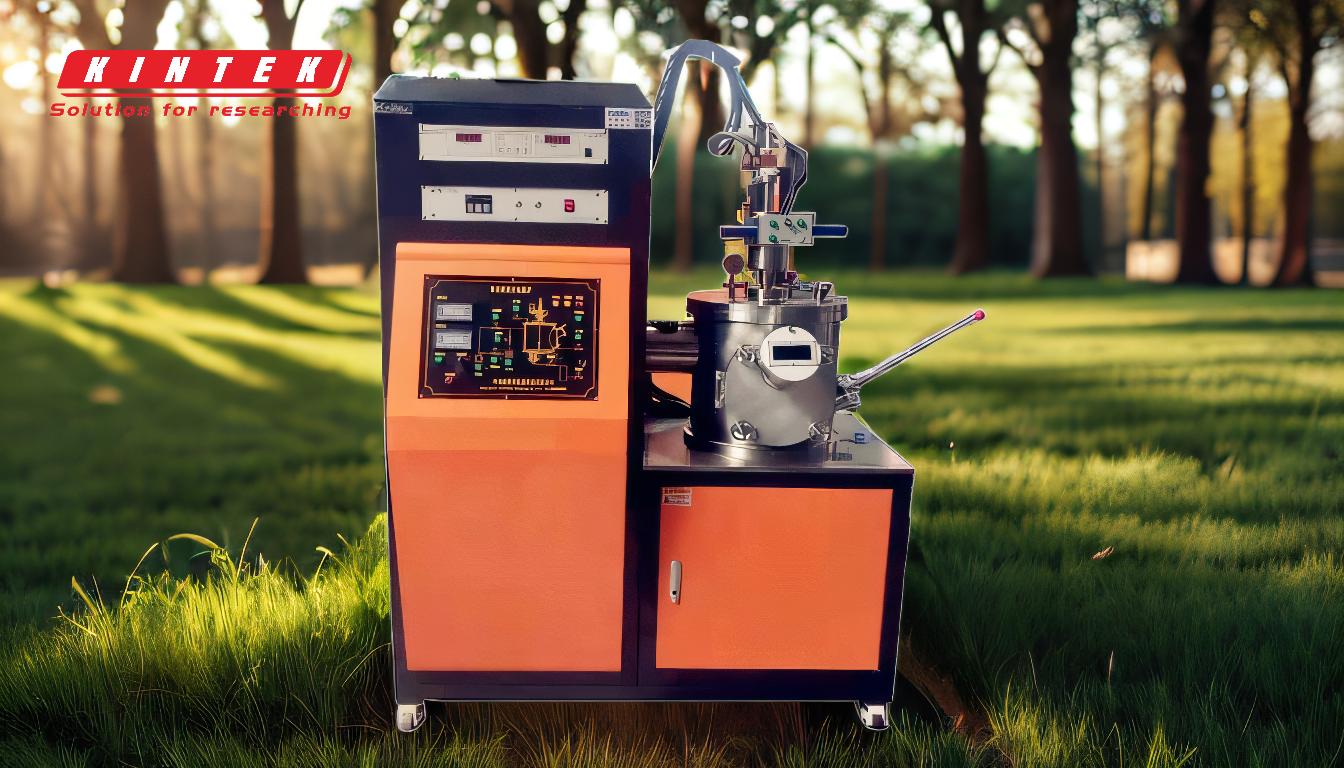
-
Indução electromagnética:
- O princípio fundamental de um forno de indução é a indução electromagnética.Quando uma corrente alternada flui através da bobina de cobre que envolve o cadinho, gera um campo magnético que se inverte rapidamente.
- Este campo magnético penetra na carga metálica no interior do cadinho, induzindo correntes de Foucault no metal.Estas correntes fluem em circuitos fechados e geram calor devido à resistência eléctrica do metal, um fenómeno conhecido como aquecimento Joule.
-
Aquecimento sem contacto:
- Ao contrário dos fornos tradicionais, os fornos de indução não requerem o contacto direto entre a fonte de calor (a bobina) e a carga metálica.O calor é gerado internamente no próprio metal, garantindo um aquecimento uniforme e reduzindo os riscos de contaminação.
- Este método sem contacto também minimiza o desgaste dos componentes do forno, aumentando a longevidade e reduzindo os custos de manutenção.
-
Conversão de frequência:
- Os fornos de indução funcionam a frequências médias (300 Hz a 1000 Hz), que são mais elevadas do que a frequência de alimentação normal de 50 Hz.Isto é conseguido através de um dispositivo de alimentação que converte a corrente alternada trifásica em corrente contínua e depois em corrente alternada de média frequência ajustável.
- Frequências mais elevadas aumentam a eficiência da transferência de energia e permitem um aquecimento mais rápido e controlado, tornando o processo adequado para fundir uma vasta gama de metais.
-
Papel da bobina de indução:
- A bobina de indução, normalmente feita de cobre, é um componente crítico do forno.Transporta a corrente alternada e gera o campo magnético necessário para o aquecimento por indução.
- A bobina é arrefecida por circulação de água para evitar o sobreaquecimento e garantir um desempenho consistente durante o funcionamento.
-
Mecanismos de geração de calor:
- Correntes de Foucault:A principal fonte de calor num forno de indução são as correntes de Foucault induzidas no metal.Estas correntes fluem em resposta à alteração do campo magnético e geram calor devido à resistência do metal.
- Histerese magnética:Nos materiais ferromagnéticos, como o ferro, é produzido calor adicional por histerese magnética.Isto ocorre porque os domínios magnéticos no interior do material se realinham continuamente com o campo magnético alternado, dissipando energia sob a forma de calor.
-
Cadinho e carga metálica:
- A carga metálica é colocada dentro de um cadinho não condutor, normalmente feito de materiais como grafite ou cerâmica, que pode suportar altas temperaturas sem interferir com o processo de indução.
- O cadinho mantém o metal seguro e assegura que o calor gerado é concentrado dentro da carga, promovendo uma fusão eficiente.
-
Controlo e precisão da temperatura:
- Os fornos de indução oferecem um controlo preciso da temperatura, permitindo aos operadores atingir o ponto de fusão exato necessário para metais específicos.Esta precisão é crucial para aplicações em indústrias como a aeroespacial, automóvel e eletrónica, onde as propriedades dos materiais têm de cumprir normas rigorosas.
- A capacidade de ajustar rapidamente a frequência e a potência de entrada permite ciclos rápidos de aquecimento e arrefecimento, melhorando a produtividade e a eficiência energética.
-
Aplicações e vantagens:
- Os fornos de indução são amplamente utilizados na fundição de metais, produção de ligas e reciclagem devido à sua eficiência, limpeza e capacidade de lidar com uma variedade de metais.
- As vantagens incluem o consumo reduzido de energia, a oxidação mínima do metal e a capacidade de operar em atmosferas controladas para evitar a contaminação.
-
Segurança e manutenção:
- A conceção dos fornos de indução dá prioridade à segurança, com caraterísticas como bobinas arrefecidas a água e controlos automáticos para evitar o sobreaquecimento e os riscos eléctricos.
- Os requisitos de manutenção são relativamente baixos, uma vez que o método de aquecimento sem contacto reduz o desgaste dos componentes.No entanto, as inspecções regulares da bobina, do cadinho e dos sistemas de arrefecimento são essenciais para garantir um desempenho ótimo.
Ao compreender estes pontos-chave, um comprador pode avaliar a adequação de um forno de indução às suas necessidades específicas, considerando factores como o tipo de material, o volume de produção e a eficiência energética.
Tabela de resumo:
Caraterística-chave | Descrição |
---|---|
Indução electromagnética | Gera calor através de correntes de Foucault e histerese magnética na carga metálica. |
Aquecimento sem contacto | Sem contacto direto entre a fonte de calor e o metal, reduzindo os riscos de contaminação. |
Frequências médias | Funciona a 300 Hz a 1000 Hz para uma transferência de energia optimizada e um aquecimento mais rápido. |
Controlo da temperatura | Controlo preciso para fundir metais como o aço até 1370°C (2500°F). |
Aplicações | Utilizado na fundição de metais, produção de ligas e reciclagem. |
Vantagens | Eficiência energética, oxidação mínima e baixa manutenção. |
Pronto para melhorar o seu processo de fusão de metais? Contacte os nossos especialistas hoje para encontrar o forno de indução perfeito para as suas necessidades!