Desenvolvimento histórico da tecnologia de revestimento por vácuo
Desafios iniciais e tecnologia CVD
A tecnologia de revestimento a vácuo deu seus primeiros passos significativos na década de 1960 com o advento da Deposição Química de Vapor (CVD). Esta técnica pioneira, embora revolucionária na altura, não estava isenta de desafios. Um dos obstáculos mais significativos era a necessidade de altas temperaturas, o que limitava os tipos de substratos que podiam ser efetivamente revestidos. As elevadas exigências térmicas dos processos de CVD significavam que apenas os materiais com elevada estabilidade térmica podiam suportar as condições de deposição, reduzindo significativamente o campo de potenciais aplicações.
Além disso, a tecnologia CVD inicial estava condicionada pela variedade limitada de revestimentos que podia produzir. A complexidade e a especificidade das reacções químicas envolvidas na CVD significavam que apenas um pequeno número de materiais podia ser depositado de forma fiável, restringindo ainda mais a sua utilidade. Estas limitações colocaram desafios significativos ao desenvolvimento e à adoção generalizada da tecnologia de revestimento por vácuo, exigindo a procura de métodos alternativos que pudessem ultrapassar estas barreiras.
Nas décadas seguintes, estes desafios iniciais abririam caminho para o desenvolvimento de tecnologias de revestimento mais versáteis e eficientes, como a deposição física de vapor (PVD), que surgiu na década de 1970 e oferecia uma solução mais adaptável e amiga do ambiente.
Surgimento da tecnologia PVD
Na década de 1970, o panorama da tecnologia de revestimento a vácuo sofreu uma transformação significativa com o advento da tecnologia de Deposição Física de Vapor (PVD). Este novo método não só abordou algumas das preocupações ambientais associadas ao seu antecessor, a Deposição Química de Vapor (CVD), como também introduziu uma miríade de propriedades de superfície versáteis que eram anteriormente inatingíveis. A mudança da CVD para a PVD foi marcada por uma redução das temperaturas operacionais e uma expansão da gama de revestimentos que podiam ser aplicados, alargando assim as suas aplicações a várias indústrias.
Os benefícios ambientais da PVD foram particularmente notáveis. Ao contrário da CVD, que frequentemente exigia temperaturas elevadas e produtos químicos potencialmente perigosos, a PVD funcionava em condições mais controladas, conduzindo a um menor consumo de energia e a menos emissões. Este respeito pelo ambiente, associado à sua capacidade de produzir revestimentos com dureza superior, resistência ao desgaste e proteção contra a corrosão, rapidamente atraiu a atenção de investigadores e industriais.
O rápido desenvolvimento da tecnologia PVD durante este período pode ser atribuído à sua adaptabilidade e às melhorias significativas que trouxe à qualidade e durabilidade dos revestimentos. As indústrias, desde a automóvel à aeroespacial, começaram a adotar a PVD pela sua capacidade de melhorar o desempenho de ferramentas e componentes, o que conduziu a uma maior eficiência e a uma vida útil mais longa dos produtos. Esta adoção generalizada impulsionou ainda mais os avanços nas técnicas de PVD, fazendo avançar a tecnologia e solidificando o seu lugar no domínio dos processos industriais modernos.
Estado atual e desafios
Desenvolvimento desequilibrado
Apesar da adoção generalizada da tecnologia de revestimento a vácuo para fins decorativos, a aplicação destes revestimentos no fabrico de moldes industriais continua a ser repleta de desafios. O principal obstáculo reside nos rigorosos requisitos de aderência exigidos pelos moldes industriais, que necessitam de uma ligação mais robusta e duradoura entre o revestimento e o substrato. Esta exigência acrescida não é facilmente satisfeita pelas tecnologias de revestimento actuais, que muitas vezes dão prioridade ao apelo estético em detrimento da durabilidade funcional.
Além disso, a falta de tecnologias de processo abrangentes adaptadas especificamente para o revestimento de moldes industriais agrava ainda mais estes desafios. Ao contrário dos revestimentos decorativos, que podem dar-se ao luxo de serem menos rigorosos nos seus métodos de aplicação, os revestimentos de moldes industriais requerem processos precisos e controlados para garantir um desempenho e uma longevidade óptimos. Esta disparidade no desenvolvimento tecnológico levou a um crescimento desequilibrado na indústria de revestimentos a vácuo, em que os avanços nos revestimentos decorativos não foram adequadamente reflectidos nas aplicações industriais.
Para resolver estas questões, existe uma necessidade premente de desenvolvimento de tecnologias e metodologias especializadas que possam satisfazer as exigências únicas do revestimento de moldes industriais. Isto inclui não só a melhoria das propriedades de aderência dos revestimentos, mas também o aperfeiçoamento de toda a cadeia de processos, desde o pré-tratamento até ao controlo de qualidade pós-aplicação. Ao concentrar-se nestas áreas, a indústria pode colmatar o fosso entre os revestimentos decorativos e industriais, promovendo uma trajetória de desenvolvimento mais equilibrada e abrangente.
Disparidades técnicas
No domínio da tecnologia de revestimento a vácuo, particularmente no contexto da PVD (Deposição Física de Vapor), as capacidades técnicas nacionais encontram-se frequentemente atrás das normas internacionais. Esta disparidade não é apenas uma questão de sofisticação do equipamento, mas abrange também uma gama mais vasta de factores, incluindo a otimização do processo, os avanços na ciência dos materiais e as metodologias de controlo de qualidade.
Para colmatar esta lacuna, existe uma necessidade premente de a indústria nacional não só introduzir equipamento avançado, mas também absorver e integrar tecnologias de ponta. Isto implica uma abordagem multifacetada, incluindo:
- Atualização do equipamento: Investir em câmaras de vácuo, fontes de alimentação e sistemas de entrada de gás de última geração, capazes de lidar com processos complexos de PVD com precisão.
- Absorção tecnológica: Envolvimento na investigação e desenvolvimento em colaboração com parceiros internacionais para compreender e implementar as melhores práticas na tecnologia PVD.
- Otimização de processos: Aperfeiçoamento dos processos existentes para garantir a uniformidade da qualidade do revestimento, abordando questões como a adesão e a consistência das camadas.
Aspeto | Estatuto nacional | Normas internacionais |
---|---|---|
Equipamento | Básico ou desatualizado | Avançado e altamente preciso |
Controlo do processo | Manual ou semi-automatizado | Totalmente automatizado com suporte de IA |
Ciência dos materiais | Foco limitado na investigação | Investigação e inovação alargadas |
Controlo de qualidade | Métodos ad-hoc | Controlo de qualidade sistemático e rigoroso |
O caminho para a paridade envolve não só a aquisição de tecnologia, mas também o desenvolvimento de um ecossistema sólido que apoie a inovação e a melhoria contínuas. Esta abordagem holística é essencial para elevar as capacidades nacionais e garantir a sua competitividade à escala global.
Conceitos básicos e caraterísticas do revestimento PVD
Métodos e técnicas
A Deposição Física de Vapor (PVD) engloba vários métodos avançados, cada um com caraterísticas e aplicações únicas. Duas técnicas proeminentes no âmbito da PVD são a galvanização por arco múltiplo e a pulverização catódica por magnetrão.
A galvanização multiarco envolve a evaporação do material alvo utilizando um arco elétrico, que ioniza o material e o impulsiona em direção ao substrato. Este método é conhecido pelas suas elevadas taxas de deposição e capacidade de revestir geometrias complexas. No entanto, pode sofrer de problemas como a contaminação por partículas e a espessura não uniforme do revestimento.
Por outro lado, a pulverização catódica por magnetrão utiliza um campo magnético para aumentar a ionização dos átomos alvo, que são depois acelerados em direção ao substrato. Esta técnica oferece um melhor controlo das propriedades do revestimento, incluindo a densidade e a uniformidade, tornando-a ideal para aplicações que requerem revestimentos precisos. Apesar destas vantagens, a pulverização catódica por magnetrão pode ser mais lenta e consumir mais energia do que a galvanização por arco múltiplo.
Método | Vantagens | Desvantagens |
---|---|---|
Revestimento por arco múltiplo | Taxas de deposição elevadas, adequadas para geometrias complexas | Contaminação por partículas, espessura de revestimento não uniforme |
Sputterização por magnetrão | Excelente controlo das propriedades do revestimento, elevada densidade e uniformidade | Processo mais lento, maior consumo de energia |
Compreender estes métodos e os seus respectivos prós e contras é crucial para selecionar a técnica de PVD mais adequada para aplicações industriais específicas.
Combinação de tecnologias
A integração das tecnologias de arco múltiplo e magnetrão representa um avanço significativo no domínio do revestimento por vácuo. Esta combinação não é apenas a soma das partes, mas uma abordagem sinérgica que maximiza os benefícios de ambas as tecnologias, garantindo a produção de revestimentos estáveis e de alta qualidade.
A galvanização por arco múltiplo, conhecida pelas suas elevadas taxas de deposição e capacidade de produzir revestimentos densos, complementa a pulverização catódica por magnetrão, que se destaca na produção de revestimentos uniformes e conformes com um aquecimento mínimo do substrato. Combinando estes métodos, os fabricantes podem alcançar um equilíbrio entre a velocidade de deposição e a uniformidade do revestimento, essencial para aplicações que requerem eficiência e precisão.
Além disso, a hibridação destas tecnologias permite a otimização das propriedades do revestimento. Por exemplo, a incorporação de iões multi-arco no processo de pulverização catódica magnetrónica pode melhorar a aderência e a dureza dos revestimentos, respondendo a desafios comuns no revestimento de moldes industriais, onde uma maior aderência e durabilidade são fundamentais.
Esta integração também abre novos caminhos para a seleção de materiais e controlo de processos. Aproveitando os pontos fortes de ambas as tecnologias, é possível depositar uma gama mais vasta de materiais com propriedades personalizadas, desde revestimentos duros e resistentes ao desgaste até estruturas multicamadas mais complexas. O resultado é uma solução de revestimento mais versátil e robusta que satisfaz as diversas exigências de várias aplicações industriais.
Em suma, a combinação das tecnologias de arco múltiplo e magnetrão não só melhora a qualidade e a estabilidade dos revestimentos, como também alarga o âmbito das propriedades dos materiais e da eficiência dos processos. Este avanço é fundamental para alargar os limites do que a tecnologia de revestimento por vácuo pode alcançar, tornando-a uma pedra angular na evolução dos revestimentos industriais.
Equipamentos e processos de revestimento modernos
Componentes e sistemas
O equipamento de revestimento moderno é um conjunto sofisticado de componentes essenciais, cada um desempenhando um papel crucial no processo de deposição em vácuo. No centro deste sistema está acâmara de vácuoum ambiente selado que isola o substrato das condições atmosféricas, assegurando uma superfície imaculada para o revestimento. A câmara de vácuo é normalmente construída a partir de materiais como o aço inoxidável, conhecido pela sua durabilidade e resistência à corrosão.
Para atingir os níveis de vácuo necessários,peças de obtenção de vácuo são utilizadas. Estas incluem bombas de vácuo, tais como bombas de palhetas rotativas e bombas turbo-moleculares, que funcionam em conjunto para reduzir a pressão da câmara para os níveis ultra-baixos necessários para os processos PVD. A eficiência destas bombas é crítica, uma vez que tem um impacto direto na qualidade e uniformidade do revestimento.
As fontes de alimentação são outro componente crítico, fornecendo a energia eléctrica necessária para vaporizar o material de revestimento. Os sistemas modernos utilizam frequentementefontes de alimentação de frequência intermédia outecnologia de impulsosque oferecem um controlo preciso do processo de deposição, resultando em revestimentos de maior qualidade. Estas fontes de alimentação avançadas ajudam a atenuar problemas como a formação de arcos e a deposição não uniforme, desafios comuns nas configurações tradicionais de PVD.
Finalmente, ossistemas de entrada de gás de processo são parte integrante do funcionamento. Estes sistemas introduzem gases reactivos na câmara de vácuo, permitindo a formação de revestimentos complexos com propriedades personalizadas. O controlo preciso dos caudais e da composição dos gases permite a criação de revestimentos com caraterísticas mecânicas, químicas e ópticas específicas, aumentando a versatilidade e a aplicabilidade da tecnologia.
Em resumo, o equipamento de revestimento moderno é uma interação complexa de câmaras de vácuo, peças de obtenção de vácuo, fontes de alimentação e sistemas de entrada de gás de processo, cada um contribuindo para a precisão e qualidade do processo PVD.
Técnicas avançadas
No domínio da tecnologia de revestimento por vácuo, surgiram várias técnicas avançadas que melhoraram significativamente a qualidade e a aplicabilidade dos revestimentos. Uma dessas técnicas é a utilização decampos magnéticos de não-equilíbrio. Estes campos permitem um controlo mais preciso do processo de deposição, possibilitando a criação de revestimentos com uniformidade e aderência superiores. Isto é particularmente benéfico em aplicações industriais onde a durabilidade e o desempenho do revestimento são críticos.
Outro avanço fundamental é a introdução defontes de alimentação de frequência intermédia. Ao contrário das fontes de alimentação tradicionais, estes sistemas de frequência intermédia oferecem maior estabilidade e eficiência. Facilitam a deposição de revestimentos mais espessos e mais robustos sem comprometer a integridade do material subjacente. Esta inovação é particularmente útil em indústrias que requerem revestimentos de alto desempenho para moldes e ferramentas.
Além disso,tecnologia de impulsos revolucionou o processo de revestimento. Ao fornecer energia em rajadas curtas e controladas, a tecnologia de impulsos minimiza o stress térmico no substrato, evitando a deformação e a degradação. Este método é especialmente vantajoso para materiais delicados ou para aqueles que requerem tratamentos de superfície complexos. O fornecimento preciso de energia também garante que o revestimento adere mais eficazmente, conduzindo a resultados mais duradouros e fiáveis.
Estas técnicas avançadas contribuem coletivamente para a evolução da tecnologia de revestimento por vácuo, tornando-a mais versátil e eficaz em várias aplicações industriais. A integração de campos magnéticos sem equilíbrio, fontes de alimentação de frequência intermédia e tecnologia de impulsos não só melhora a qualidade dos revestimentos, como também alarga a sua aplicabilidade, satisfazendo as exigências cada vez mais rigorosas das indústrias modernas.
Aplicação e controlo de qualidade em PVD para moldes
Processos de pré-tratamento e revestimento
Os métodos de pré-tratamento são passos cruciais na preparação de superfícies para o revestimento por Deposição Física de Vapor (PVD). Estes métodos incluem a limpeza a vapor a alta temperatura, que remove eficazmente os contaminantes e garante um substrato limpo. O jato de areia é outra técnica vital, proporcionando uma superfície rugosa que melhora a aderência do revestimento. O próprio processo de revestimento por PVD depende fortemente de um controlo preciso da temperatura e de um aquecimento uniforme para obter resultados óptimos.
O aquecimento uniforme é essencial porque assegura que o substrato é aquecido uniformemente, o que, por sua vez, permite uma deposição uniforme do material de revestimento. O controlo da temperatura é igualmente importante, uma vez que os desvios podem levar a inconsistências na espessura e qualidade do revestimento. Técnicas avançadas, como fontes de alimentação de frequência intermédia e tecnologia de impulsos, são frequentemente utilizadas para manter condições de aquecimento estáveis e consistentes, melhorando assim a qualidade global do revestimento PVD.
Estes processos de pré-tratamento e revestimento são essenciais para o sucesso das aplicações de PVD em moldes industriais. Não só melhoram a durabilidade e o desempenho dos moldes, como também prolongam a sua vida útil, tornando-os indispensáveis em ambientes de fabrico de alta precisão.
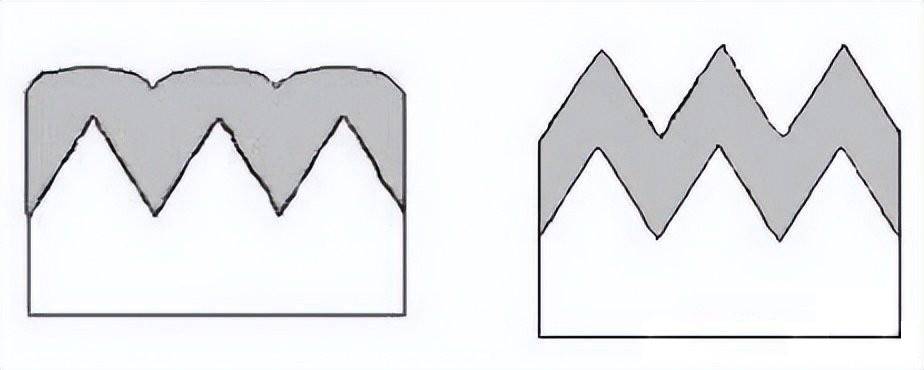
Medidas de controlo de qualidade
O Controlo de Qualidade Funcional (FQC) é um aspeto crítico para garantir a fiabilidade e o desempenho dos moldes revestidos. Este processo engloba várias inspecções meticulosas para garantir que os revestimentos cumprem as normas exigidas.
Um dos principais métodos do FQC é ainspeção do aspeto. Isto envolve um exame visual minucioso para detetar quaisquer imperfeições na superfície, tais como riscos, buracos ou descoloração. Estes defeitos podem afetar significativamente a funcionalidade e o tempo de vida do molde, tornando este passo indispensável.
Outro método fundamental é ainspeção da profundidade da camada. Esta técnica mede a espessura das camadas de revestimento para garantir que cumprem os parâmetros especificados. São utilizados vários instrumentos, tais como profilómetros e microscópios electrónicos de varrimento, para determinar com precisão a profundidade e a uniformidade do revestimento.
Ainspeção da aderência também é crucial. Este processo avalia a força de ligação entre o revestimento e o substrato do molde. Os métodos comuns incluem testes de arranhões, testes de tração e testes de corte transversal. Estes testes ajudam a identificar quaisquer potenciais problemas de delaminação ou descamação, garantindo a durabilidade e eficácia do revestimento.
Ao integrar estes métodos de FQC, os fabricantes podem garantir que os seus moldes revestidos não só cumprem como excedem as normas da indústria, fornecendo ferramentas fiáveis e de elevado desempenho para várias aplicações industriais.
CONTACTE-NOS PARA UMA CONSULTA GRATUITA
Os produtos e serviços da KINTEK LAB SOLUTION foram reconhecidos por clientes de todo o mundo. A nossa equipa terá todo o prazer em ajudar com qualquer questão que possa ter. Contacte-nos para uma consulta gratuita e fale com um especialista de produto para encontrar a solução mais adequada para as suas necessidades de aplicação!