O processo de sinterização é uma técnica de fabrico fundamental utilizada para transformar materiais em pó em corpos sólidos densos, aplicando calor e pressão abaixo do ponto de fusão do material.Envolve várias fases, incluindo a preparação de uma mistura de pó com um agente de ligação, a moldagem do material numa forma desejada, o aquecimento para remover o agente de ligação e a fusão das partículas primárias para criar uma massa unificada de baixa porosidade.Este processo é amplamente utilizado em indústrias como a metalurgia do pó e a cerâmica para produzir componentes duráveis e de elevada resistência.As etapas principais incluem composição, compressão, aquecimento, fusão de partículas e solidificação, cada uma contribuindo para as propriedades do material final.
Pontos-chave explicados:
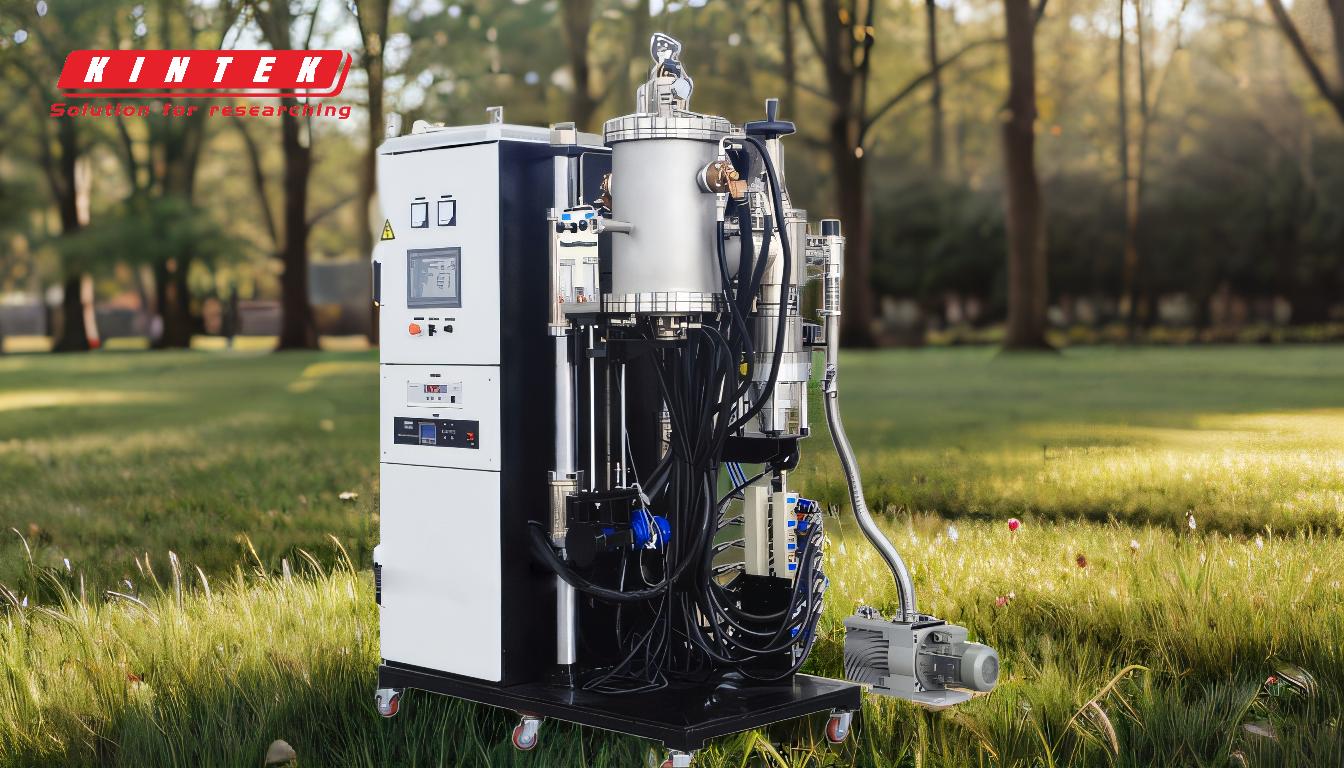
-
Preparação da mistura em pó:
- Composição:O processo começa com a mistura de materiais primários (tais como pós metálicos ou cerâmicos) com um agente de ligação (por exemplo, cera ou polímero).O agente de ligação ajuda as partículas de pó a aderirem umas às outras, formando uma mistura coesa.
- Moldagem:A mistura de pó é depois moldada na forma desejada utilizando técnicas como a prensagem a frio, a impressão 3D ou outros métodos de moldagem.Isto cria uma \"peça verde,\" que é uma estrutura preliminar que mantém a sua forma mas ainda não é totalmente densa.
-
Compressão e conformação:
- Compressão:A parte verde é comprimida para atingir a forma e a densidade pretendidas.Este passo assegura que as partículas estão bem compactadas, reduzindo a porosidade e preparando o material para a fase de aquecimento.
- Atmosfera controlada:Em alguns casos, a compressão ocorre numa atmosfera controlada para evitar a oxidação ou contaminação, que poderia afetar as propriedades do material.
-
Aquecimento e remoção do agente de ligação:
- Aquecimento inicial:A peça verde é aquecida a uma temperatura em que o agente de ligação se evapora ou queima.Este passo é crucial para eliminar quaisquer materiais orgânicos que possam interferir com o processo de sinterização.
- Controlo da temperatura:A temperatura é cuidadosamente controlada para assegurar que o agente de ligação é totalmente removido sem danificar o material primário.
-
Fusão e fusão de partículas:
-
Temperatura de sinterização:A temperatura é então aumentada para um valor ligeiramente inferior ao ponto de fusão do material.Nesta fase, ocorre um de dois processos:
- Sinterização em estado sólido:As partículas primárias começam a fundir-se nas suas superfícies devido à difusão atómica, criando uma estrutura mais densa.
- Sinterização em fase líquida (LPS):Um agente de ligação intermédio, como o bronze, funde-se e flui entre as partículas, ligando-as entre si enquanto o material primário permanece sólido.
- Densificação:As partículas densificam-se e fundem-se, reduzindo a porosidade e aumentando a resistência e a durabilidade do material.
-
Temperatura de sinterização:A temperatura é então aumentada para um valor ligeiramente inferior ao ponto de fusão do material.Nesta fase, ocorre um de dois processos:
-
Solidificação e arrefecimento:
- Fase de arrefecimento:Após a conclusão do processo de sinterização, o material é deixado arrefecer e solidificar numa massa unificada.Este passo assegura que o material mantém a sua forma e propriedades.
- Propriedades finais:O produto final é um material denso e de baixa porosidade com propriedades mecânicas melhoradas, tais como dureza, resistência e durabilidade.
-
Aplicações e benefícios:
- Utilização industrial:A sinterização é amplamente utilizada na metalurgia do pó para produzir componentes metálicos e no fabrico de cerâmica para criar produtos cerâmicos duradouros.
- Materiais com elevado ponto de fusão:Este processo é particularmente útil para materiais com pontos de fusão extremamente elevados, como o tungsténio e o molibdénio, que são difíceis de processar utilizando técnicas de fusão tradicionais.
- Personalização:A sinterização permite a produção de formas complexas e de componentes personalizados, o que a torna um método de fabrico versátil.
Seguindo estes passos, o processo de sinterização transforma os pós soltos em materiais fortes e densos, adequados a uma vasta gama de aplicações industriais.O controlo cuidadoso da temperatura, pressão e atmosfera garante que o produto final cumpre as especificações e requisitos de desempenho desejados.
Tabela de resumo:
Fase | Principais pormenores |
---|---|
Preparação | Misturar materiais primários com um agente de ligação e dar forma a uma "peça verde". |
Compressão | Comprimir a parte verde para reduzir a porosidade e atingir a densidade desejada. |
Aquecimento | Aquecer para remover o agente de ligação e preparar a fusão de partículas. |
Fusão de partículas | Aumentar a temperatura para fundir as partículas através da sinterização em estado sólido ou em fase líquida. |
Solidificação | Arrefecer e solidificar num material denso e de baixa porosidade com propriedades melhoradas. |
Aplicações | Utilizado em metalurgia do pó e cerâmica para componentes duráveis e de alta resistência. |
Descubra como a sinterização pode melhorar o seu processo de fabrico. contacte-nos hoje para obter orientação especializada!