A brasagem por chama, embora seja um método amplamente utilizado para unir metais, tem várias desvantagens que podem afetar a qualidade, a eficiência e a relação custo-eficácia do processo.Estas desvantagens incluem a necessidade de ajustes precisos da junta para garantir uma ação capilar adequada, o potencial recozimento dos componentes devido a temperaturas elevadas e considerações de design para a colocação do material de brasagem.Compreender estas limitações é crucial para selecionar o método de brasagem adequado para aplicações específicas.
Pontos-chave explicados:
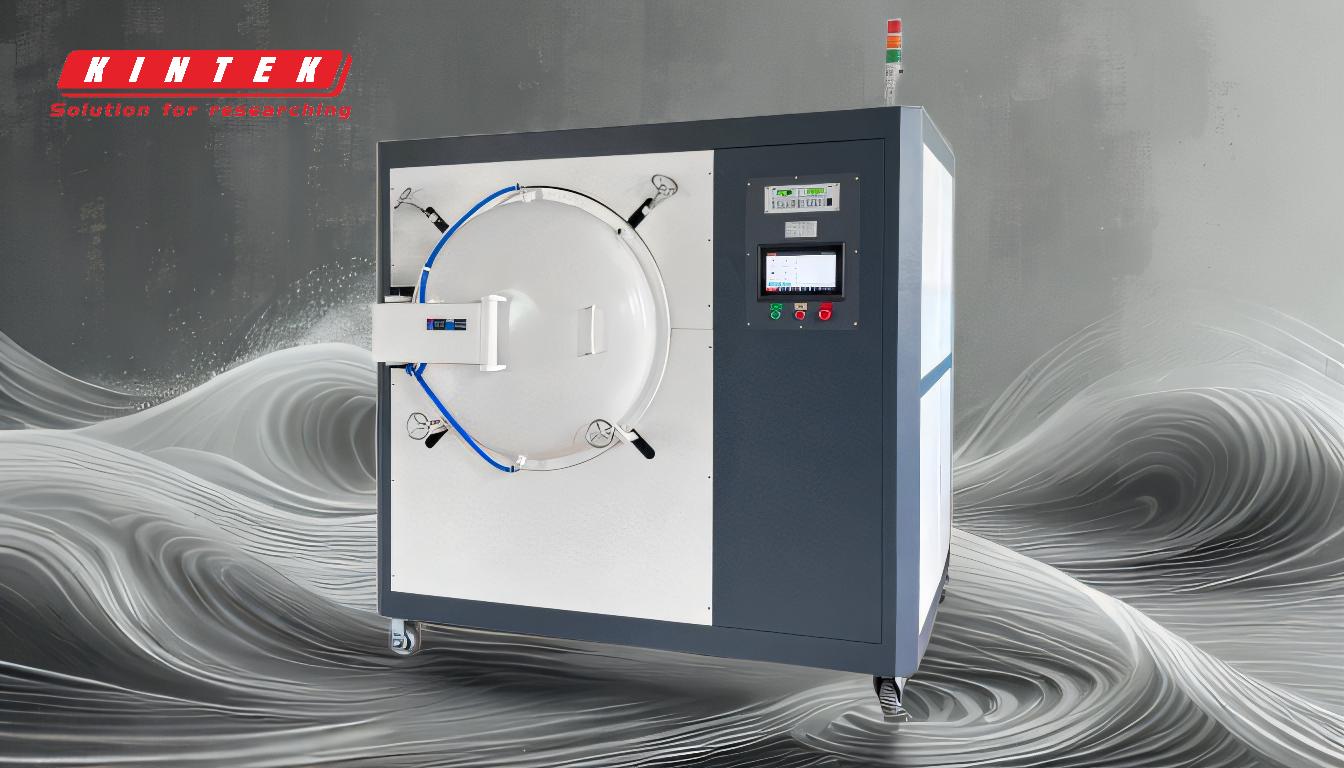
-
Necessidade de ajustes estreitos para facilitar a ação capilar:
- A brasagem por chama baseia-se na ação capilar para atrair o metal de adição fundido para a junta.Isto requer que as superfícies da junta estejam muito próximas umas das outras, normalmente dentro de alguns milésimos de polegada.Alcançar e manter tolerâncias tão apertadas pode ser um desafio, especialmente para montagens complexas ou de grandes dimensões.
- Impacto:A necessidade de ajustes apertados pode aumentar a complexidade do processo de conceção e fabrico, conduzindo potencialmente a custos mais elevados e a tempos de produção mais longos.
-
Recozimento de peças de componentes:
- As altas temperaturas utilizadas na brasagem por chama podem provocar o recozimento dos metais de base, que é um processo que amolece o metal alterando a sua microestrutura.Isto pode ser particularmente problemático para metais que requerem elevada resistência ou dureza.
- Impacto:O recozimento pode reduzir as propriedades mecânicas dos componentes, como a resistência à tração e a dureza, o que pode exigir processos de tratamento térmico adicionais para restaurar as propriedades desejadas.Isto aumenta o custo global e a complexidade do processo de fabrico.
-
Considerações sobre o projeto de colocação de material de brasagem:
- A brasagem por chama requer um planeamento cuidadoso para garantir que o material de brasagem é colocado corretamente na junta.Isto envolve frequentemente a conceção dos componentes para incluir caraterísticas como ranhuras ou reservatórios para segurar o metal de enchimento.
- Impacto:A necessidade de tais modificações no projeto pode complicar o processo de engenharia e pode limitar a flexibilidade no projeto do componente.Também requer um controlo preciso durante o processo de brasagem para garantir que o metal de adição flui corretamente e forma uma ligação forte.
-
Potencial de oxidação e contaminação:
- A chama aberta utilizada na brasagem por chama pode expor as superfícies metálicas ao oxigénio, conduzindo à oxidação.Isto pode enfraquecer a junta e reduzir a qualidade geral do conjunto soldado.
- Impacto:Para atenuar a oxidação, é frequentemente utilizado fluxo, mas este acrescenta mais um passo ao processo e pode introduzir contaminação se não for corretamente aplicado ou removido.Para além disso, a utilização de fluxo pode exigir a limpeza pós-brasagem, aumentando ainda mais a complexidade e o custo.
-
Controlo limitado da distribuição de calor:
- A brasagem por chama pode resultar numa distribuição desigual do calor, o que pode levar a uma qualidade inconsistente da junta.As áreas demasiado quentes podem sofrer fusão ou distorção excessivas, enquanto as áreas mais frias podem não conseguir uma ligação adequada.
- Impacto:Uma distribuição inconsistente do calor pode comprometer a integridade da junta soldada, conduzindo a potenciais falhas em serviço.Também requer operadores qualificados para gerir cuidadosamente a chama e a aplicação de calor, o que pode aumentar os custos de mão de obra.
-
Preocupações com a segurança e o ambiente:
- A utilização de uma chama aberta apresenta riscos de segurança, incluindo a possibilidade de queimaduras, incêndios e explosões.Além disso, o processo pode produzir fumos nocivos, especialmente se forem utilizados fluxos ou outros produtos químicos.
- Impacto:As medidas de segurança e a ventilação adequada são essenciais, o que pode aumentar os custos operacionais.Poderá também haver regulamentos ambientais a considerar, particularmente no que respeita à eliminação do fluxo usado e de outros subprodutos.
Em resumo, embora a brasagem por chama seja um método de união versátil e amplamente utilizado, apresenta várias desvantagens que podem afetar a qualidade, o custo e a complexidade do processo de fabrico.Estas incluem a necessidade de ajustes precisos das juntas, o potencial recozimento dos componentes, considerações de design para a colocação do material de brasagem, riscos de oxidação e contaminação, controlo limitado sobre a distribuição do calor e preocupações ambientais e de segurança.Compreender estas limitações é essencial para tomar decisões informadas sobre a utilização da brasagem por chama em aplicações específicas.
Tabela de resumo:
Desvantagem | Impacto |
---|---|
Necessidade de ajustes precisos das juntas | Aumenta a complexidade do projeto, os custos e o tempo de produção |
Potencial recozimento de componentes | Reduz as propriedades mecânicas, exigindo tratamento térmico adicional |
Considerações de projeto para a colocação de material | Complica a engenharia e limita a flexibilidade do projeto |
Riscos de oxidação e contaminação | Enfraquece as juntas, requer fluxo e aumenta a limpeza pós-brasagem |
Controlo limitado da distribuição do calor | Conduz a uma qualidade inconsistente das juntas e a custos de mão de obra mais elevados |
Preocupações ambientais e de segurança | Requer medidas de segurança, ventilação e conformidade com os regulamentos |
Precisa de ajuda para escolher o método de brasagem correto para a sua aplicação? Contacte os nossos especialistas hoje mesmo!