A soldagem por indução, embora vantajosa em muitas aplicações industriais, tem várias desvantagens notáveis. Estes incluem altos custos iniciais, complexidade na operação, limitações de materiais e desafios relacionados ao refinamento e manutenção da composição do material. Abaixo, exploramos essas desvantagens em detalhes, proporcionando uma compreensão abrangente das limitações associadas à soldagem por indução.
Pontos-chave explicados:
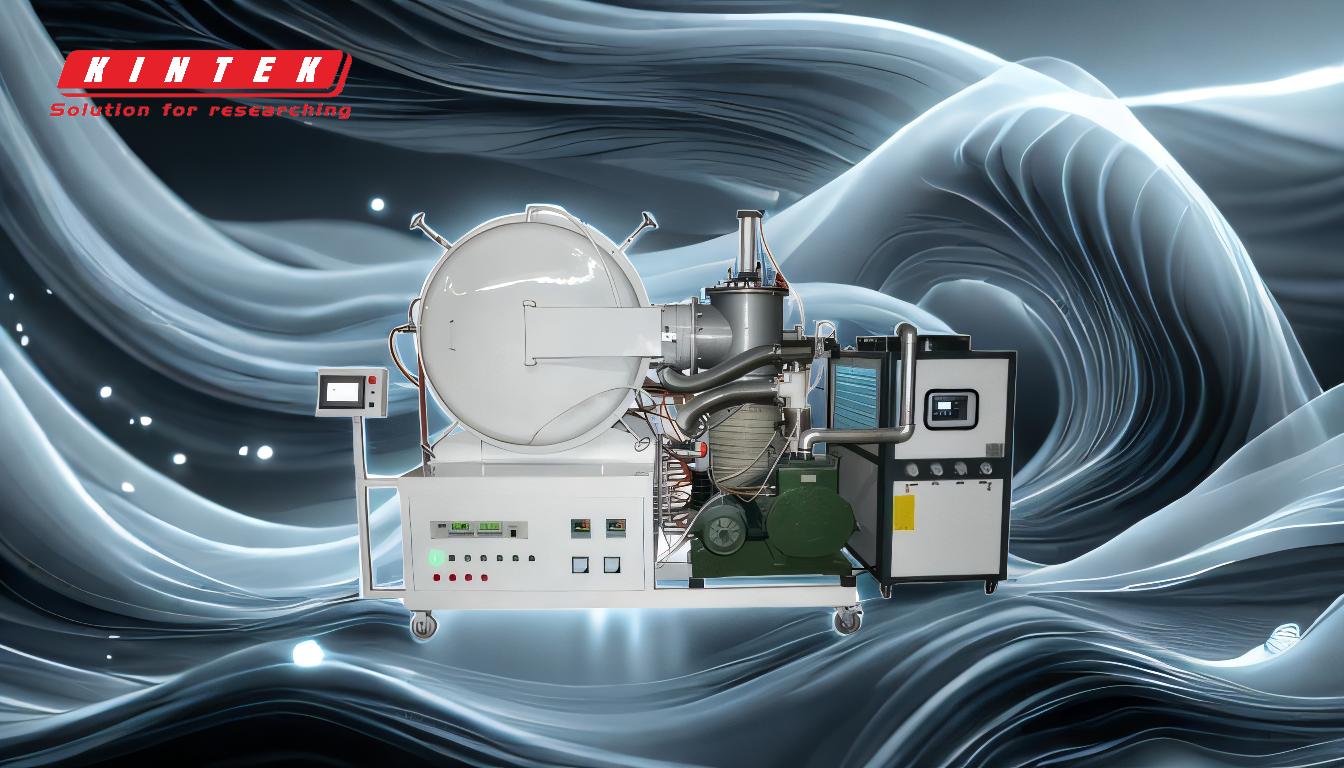
-
Alto custo inicial
- O equipamento de soldagem por indução é significativamente mais caro em comparação com os métodos tradicionais de soldagem.
- O custo inclui não apenas a máquina em si, mas também a infraestrutura associada, como fontes de alimentação e sistemas de refrigeração.
- Para operações de pequena escala ou empresas com orçamentos limitados, este elevado investimento inicial pode ser uma grande barreira à adoção.
-
Processo e Operação Complexos
- A soldagem por indução requer conhecimento e treinamento especializado para operar de forma eficaz.
- O processo envolve controle preciso de parâmetros como frequência, potência e tempo de aquecimento, o que pode ser um desafio para operadores inexperientes.
- A manutenção dos equipamentos também exige conhecimento técnico, aumentando a complexidade operacional.
-
Limitações materiais
- A soldagem por indução não é adequada para todos os materiais. Funciona melhor com metais condutores como cobre, latão e aço.
- Materiais não condutores ou com baixa condutividade térmica podem não aquecer de maneira uniforme ou eficiente, levando a resultados inconsistentes.
- Certos materiais também podem degradar-se ou oxidar sob as altas temperaturas geradas pelo aquecimento por indução.
-
Falta de capacidade de refino
- A soldagem por indução não tem a capacidade de refinar ou purificar materiais durante o processo.
- Os materiais utilizados devem estar previamente isentos de óxidos e contaminantes, pois estes podem impactar negativamente a qualidade da junta de solda.
- Esta limitação requer etapas adicionais de pré-processamento, aumentando o tempo e o custo.
-
Oxidação e perda de elementos de liga
- Altas temperaturas durante a soldagem por indução podem causar oxidação de certos materiais, particularmente aqueles com elementos de liga reativos.
- A oxidação pode levar à perda de elementos de liga críticos, que podem precisar ser adicionados novamente para manter as propriedades desejadas do material.
- Esse problema pode comprometer a integridade e o desempenho do produto final.
-
Consumo e Eficiência Energética
- Os sistemas de soldagem por indução podem consumir muita energia, especialmente quando operam em altas frequências ou níveis de potência.
- Embora o aquecimento por indução seja geralmente eficiente, o consumo geral de energia ainda pode ser maior em comparação com outros métodos de soldagem, dependendo da aplicação.
-
Flexibilidade limitada para peças pequenas ou complexas
- A soldagem por indução é menos eficaz para peças pequenas, complexas ou de formato irregular devido às dificuldades em obter aquecimento uniforme.
- Projetos de bobinas personalizadas podem ser necessários para aplicações específicas, aumentando a complexidade e o custo.
-
Preocupações de segurança
- As altas temperaturas e os campos eletromagnéticos gerados durante a soldagem por indução representam riscos de segurança para os operadores.
- Medidas de segurança adequadas, tais como blindagem e equipamento de proteção, são necessárias para mitigar estes riscos.
Em resumo, embora a soldagem por indução ofereça vantagens como velocidade, precisão e aquecimento localizado, suas desvantagens – incluindo altos custos, limitações de material e complexidade operacional – devem ser cuidadosamente consideradas. Esses fatores o tornam menos adequado para determinadas aplicações ou negócios com recursos limitados. Compreender essas limitações é crucial para tomar decisões informadas sobre se a soldagem por indução é a escolha certa para um caso de uso específico.
Tabela Resumo:
Desvantagem | Detalhes |
---|---|
Alto custo inicial | Equipamentos e infraestrutura caros; barreira para operações de pequena escala. |
Processo e Operação Complexos | Requer treinamento especializado e controle preciso de parâmetros. |
Limitações materiais | Melhor para metais condutores; desafios com materiais não condutores. |
Falta de capacidade de refino | Nenhuma purificação de material durante o processo; pré-processamento necessário. |
Oxidação e perda de liga | Altas temperaturas causam oxidação e perda de elementos de liga críticos. |
Consumo de energia | Pode consumir muita energia, especialmente em altas frequências. |
Flexibilidade Limitada | Menos eficaz para peças pequenas ou complexas; bobinas personalizadas podem ser necessárias. |
Preocupações de segurança | Altas temperaturas e campos eletromagnéticos representam riscos para os operadores. |
Precisa de ajuda para decidir se a soldagem por indução é adequada para sua aplicação? Contate nossos especialistas hoje para aconselhamento personalizado!