O processo de endurecimento, embora essencial para melhorar as propriedades mecânicas dos materiais, apresenta diversas desvantagens que podem impactar a qualidade, o custo e a usabilidade do produto final. Essas desvantagens incluem a necessidade de operadores qualificados, perda potencial de material e desafios relacionados à qualidade da superfície e ao pós-processamento. Compreender estas desvantagens é crucial para que os compradores de equipamentos e consumíveis tomem decisões informadas e otimizem os seus processos.
Pontos-chave explicados:
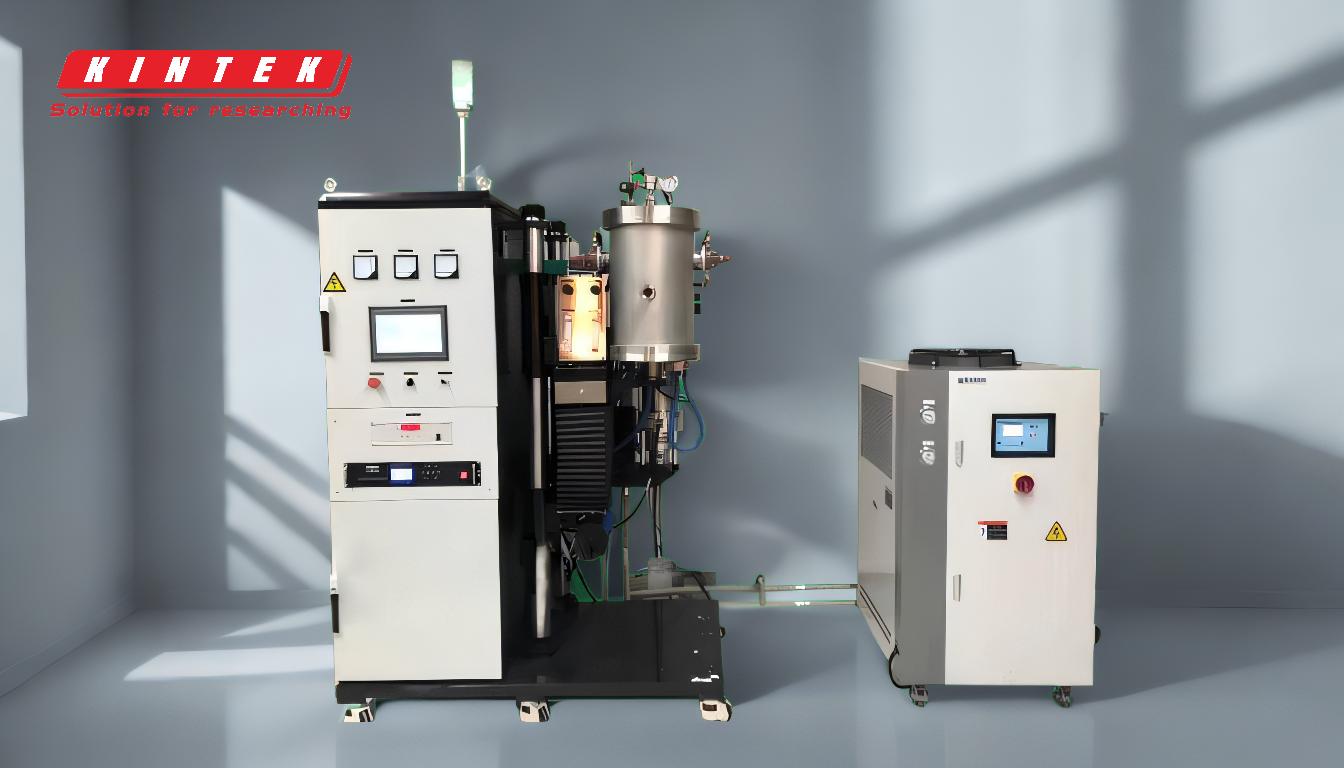
-
Alta exigência de habilidade para operadores:
- O processo de endurecimento, particularmente em métodos como a prensagem a quente, exige um alto nível de habilidade do operador. Isso ocorre porque a combinação das taxas de temperatura, pressão, aquecimento e resfriamento deve ser controlada com precisão para atingir as propriedades desejadas do material.
- São necessários operadores qualificados para monitorar e ajustar esses parâmetros em tempo real, garantindo que o material não superaqueça, esfrie muito rapidamente ou sofra distribuição desigual de pressão. Este nível de controle é fundamental para evitar defeitos como empenamentos, rachaduras ou dureza inconsistente.
- Para os compradores, isso significa investir em programas de treinamento ou contratar pessoal experiente, o que pode aumentar os custos operacionais.
-
Perda de material e problemas de superfície:
- Uma desvantagem significativa do processo de endurecimento é a perda potencial de material, como o cobalto, que pode ser extrudado da superfície do produto durante a prensagem a quente. Isto não só leva ao desperdício de material, mas também afeta a qualidade da superfície do produto final.
- O material extrudado pode tornar a superfície áspera, dificultando a limpeza e o processamento posterior. Esta rugosidade pode exigir etapas adicionais de acabamento, como lixamento ou polimento, para atingir a lisura superficial desejada.
- Para os compradores, isso se traduz em custos de material mais elevados e etapas de processamento adicionais, o que pode aumentar o tempo e as despesas de produção.
-
Desafios no pós-processamento:
- O processo de endurecimento pode tornar o material mais difícil de usinar ou moldar após o tratamento. Por exemplo, os materiais endurecidos são muitas vezes mais duros e frágeis, tornando-os propensos a rachar ou lascar durante a usinagem.
- Esta fragilidade também pode limitar os tipos de técnicas de pós-processamento que podem ser aplicadas, já que alguns métodos podem não ser adequados para materiais endurecidos. Por exemplo, certos processos de soldagem ou dobra podem não ser viáveis sem risco de danos ao material.
- Os compradores precisam considerar essas limitações ao planejar seus processos de produção, pois podem precisar investir em equipamentos ou técnicas especializadas para manusear materiais endurecidos de maneira eficaz.
-
Custos de Energia e Equipamentos:
- O processo de endurecimento normalmente requer um consumo significativo de energia, especialmente em métodos como prensagem a quente ou tratamento térmico. Altas temperaturas e ciclos de aquecimento prolongados podem levar ao aumento do consumo de energia, o que pode ser dispendioso.
- Além disso, o equipamento utilizado para o endurecimento, como fornos ou prensas, pode ser caro para adquirir e manter. Essas máquinas geralmente exigem manutenção regular para garantir um desempenho consistente e evitar tempos de inatividade.
- Para os compradores, isto significa despesas de capital mais elevadas e custos operacionais contínuos, que precisam de ser tidos em conta no orçamento global.
-
Potencial para tensões residuais:
- Durante o processo de endurecimento, tensões residuais podem se desenvolver no material devido ao resfriamento irregular ou às rápidas mudanças de temperatura. Essas tensões podem levar à instabilidade dimensional, empenamento ou até mesmo rachaduras ao longo do tempo.
- As tensões residuais também podem afetar as propriedades mecânicas do material, como sua resistência à fadiga ou capacidade de carga. Isto pode ser particularmente problemático em aplicações onde o material está sujeito a cargas cíclicas ou altas tensões.
- Os compradores devem considerar o impacto potencial das tensões residuais no desempenho e na longevidade dos seus produtos e podem necessitar de implementar tratamentos de alívio de tensões ou outras medidas corretivas.
-
Compatibilidade limitada de materiais:
- Nem todos os materiais são adequados para o processo de endurecimento. Alguns materiais podem não responder bem ao tratamento térmico ou podem exigir condições específicas que são difíceis de alcançar de forma consistente.
- Por exemplo, certas ligas ou materiais compósitos podem ter capacidades de endurecimento limitadas, o que pode restringir a sua utilização em aplicações que requerem elevada resistência ou durabilidade.
- Os compradores precisam avaliar cuidadosamente a compatibilidade dos materiais escolhidos com o processo de endurecimento e considerar tratamentos ou materiais alternativos, se necessário.
Em resumo, embora o processo de endurecimento ofereça benefícios significativos em termos de resistência e durabilidade do material, também apresenta vários desafios que precisam de ser cuidadosamente geridos. Estes incluem a necessidade de operadores qualificados, perda potencial de material, problemas de qualidade de superfície, dificuldades de pós-processamento, altos custos de energia e equipamentos, tensões residuais e compatibilidade limitada de materiais. Ao compreender estas desvantagens, os compradores de equipamentos e consumíveis podem tomar decisões mais informadas e otimizar os seus processos para alcançar os melhores resultados possíveis.
Tabela Resumo:
Desvantagem | Impacto |
---|---|
Alta exigência de habilidade | Aumento dos custos operacionais devido à necessidade de operadores qualificados. |
Perda de material e problemas de superfície | Custos de material mais elevados e etapas de processamento adicionais. |
Desafios pós-processamento | Dificuldade em usinar ou moldar materiais endurecidos. |
Custos de Energia e Equipamentos | Alto consumo de energia e manutenção cara de equipamentos. |
Tensões residuais | Risco de instabilidade dimensional, empenamento ou fissuração. |
Compatibilidade limitada de materiais | Restringe o uso de certos materiais ou requer tratamentos alternativos. |
Precisa de ajuda para otimizar seu processo de endurecimento? Contate nossos especialistas hoje para soluções personalizadas!