O tratamento térmico de recozimento, embora benéfico para melhorar a maquinabilidade, as propriedades mecânicas e a trabalhabilidade dos materiais, tem várias desvantagens.Estas incluem o potencial amolecimento do material, que pode reduzir a dureza e a resistência, tornando-o inadequado para aplicações que exijam elevada resistência ao desgaste.O processo também pode levar ao crescimento do grão, afectando negativamente as propriedades mecânicas.Além disso, o recozimento requer um controlo preciso da temperatura e das taxas de arrefecimento, o que o torna moroso e consome muita energia.Pode também alterar a microestrutura do material de forma indesejável e, nalguns casos, pode introduzir oxidação ou descarbonetação da superfície, comprometendo a integridade da superfície do material.
Pontos-chave explicados:
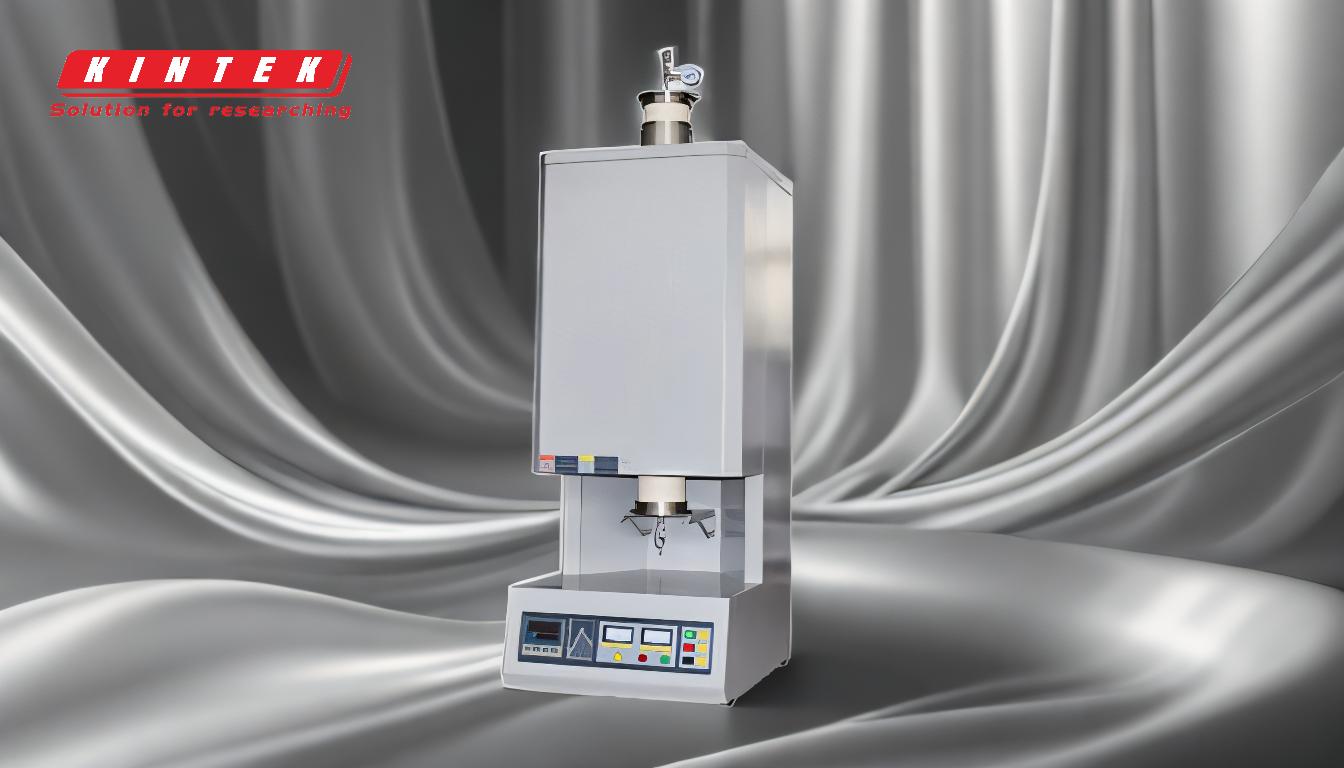
-
Amolecimento de materiais:
- O recozimento reduz a dureza e a resistência do material, amolecendo-o. Este facto pode ser uma desvantagem em aplicações em que é necessária uma elevada resistência ao desgaste ou uma elevada resistência.Isto pode ser uma desvantagem em aplicações onde é necessária uma elevada resistência ao desgaste ou força.Por exemplo, as ferramentas ou os componentes sujeitos a grandes tensões podem não ter um bom desempenho após o recozimento.
-
Crescimento dos grãos:
- Durante o recozimento, os grãos no interior do material podem aumentar de tamanho.Este crescimento do grão pode afetar negativamente as propriedades mecânicas, como a tenacidade e a resistência à fadiga.Os grãos maiores podem levar a uma redução do desempenho geral do material sob carga.
-
Consumo de tempo e energia:
- O processo de recozimento exige um controlo preciso da temperatura e das taxas de arrefecimento, o que o torna um processo moroso e que consome muita energia.Isto pode aumentar os custos de produção e os prazos de entrega, especialmente no fabrico em grande escala.
-
Alterações microestruturais:
- O recozimento pode alterar a microestrutura do material de formas que podem não ser desejáveis para aplicações específicas.Por exemplo, certas fases ou estruturas que contribuem para a resistência do material ou outras propriedades podem ser perdidas ou transformadas durante o processo de recozimento.
-
Oxidação da superfície e descarbonetação:
- As altas temperaturas envolvidas no recozimento podem levar à oxidação ou descarbonetação da superfície, especialmente em metais como o aço.Isto pode comprometer a integridade da superfície e as propriedades mecânicas do material, exigindo tratamentos de superfície adicionais ou maquinagem para restaurar as propriedades desejadas.
-
Aplicabilidade limitada:
- Nem todos os materiais ou aplicações beneficiam do recozimento.Por exemplo, os materiais que requerem elevada dureza ou microestruturas específicas podem não ser adequados para recozimento, uma vez que o processo pode contrariar estes requisitos.
-
Potencial de distorção:
- Durante as fases de aquecimento e arrefecimento do recozimento, existe o risco de distorção ou deformação do material, especialmente em componentes complexos ou de paredes finas.Isto pode levar a imprecisões dimensionais e à necessidade de maquinação adicional ou de medidas corretivas.
Ao compreender estas desvantagens, os compradores de equipamento e consumíveis podem tomar decisões informadas sobre se o recozimento é o tratamento térmico adequado para as suas necessidades e aplicações específicas.
Tabela de resumo:
Desvantagem | Impacto |
---|---|
Amolecimento do material | Reduz a dureza e a resistência, não sendo adequado para uma elevada resistência ao desgaste. |
Crescimento do grão | Afecta negativamente a tenacidade e a resistência à fadiga. |
Consumo de tempo e energia | Aumenta os custos de produção e os prazos de entrega. |
Alterações microestruturais | Podem alterar fases ou estruturas desejáveis no material. |
Oxidação/Descarburação da superfície | Compromete a integridade da superfície, exigindo tratamentos adicionais. |
Aplicabilidade limitada | Não é adequado para materiais que exijam elevada dureza ou microestruturas específicas. |
Potencial de distorção | Risco de deformação, especialmente em componentes complexos ou de paredes finas. |
Precisa de ajuda para decidir se o recozimento é adequado para a sua aplicação? Contacte os nossos especialistas hoje para um aconselhamento personalizado!