O recozimento em semicondutores é um processo térmico crítico usado para modificar as propriedades do material, como reduzir defeitos, melhorar as características elétricas e aumentar a integridade estrutural. Ao contrário do recozimento de metal, que se concentra principalmente no alívio de tensões e na ductilidade, o recozimento de semicondutores é adaptado para atender aos requisitos exclusivos de materiais semicondutores, como wafers de silício. O processo envolve aquecer o material a uma temperatura específica e depois resfriá-lo sob condições controladas. Este tratamento térmico pode ser categorizado em vários tipos, cada um servindo a finalidades distintas na fabricação de semicondutores.
Pontos-chave explicados:
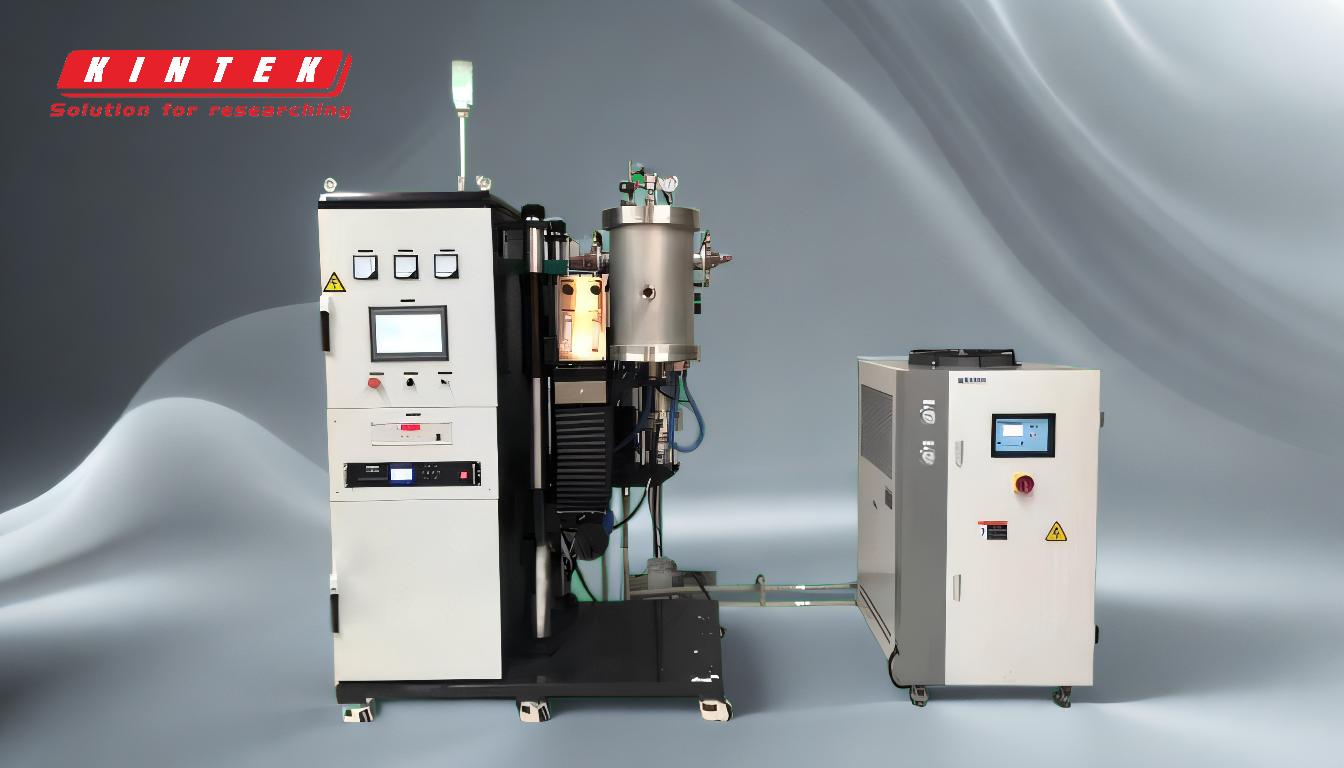
-
Objetivo do recozimento em semicondutores:
- Redução de defeitos: O recozimento ajuda a reduzir defeitos na rede cristalina, como vagas e deslocamentos, que podem impactar negativamente o desempenho de dispositivos semicondutores.
- Ativação de Dopante: Na fabricação de semicondutores, dopantes são introduzidos para modificar as propriedades elétricas. O recozimento ativa esses dopantes, incorporando-os na rede cristalina.
- Alívio do estresse: Semelhante ao recozimento de metal, o recozimento de semicondutores pode aliviar tensões internas que surgem durante processos de fabricação, como deposição ou gravação.
- Recristalização: O recozimento pode promover a recristalização, o que melhora a integridade estrutural e as propriedades elétricas do material.
-
Tipos de recozimento em semicondutores:
-
Recozimento de forno:
- Processo: O wafer semicondutor é aquecido em um forno a temperaturas que normalmente variam de 600°C a 1200°C por vários minutos a horas.
- Aplicativos: Usado para processamento em massa, como ativação de dopantes e recozimento de defeitos. É adequado para produção em larga escala devido à sua capacidade de lidar com vários wafers simultaneamente.
- Vantagens: O aquecimento uniforme e os longos tempos de processamento permitem a redução completa de defeitos e a ativação de dopantes.
- Limitações: Tempos de processamento mais longos podem levar à difusão indesejada de dopantes, afetando o desempenho do dispositivo.
-
Recozimento Térmico Rápido (RTA):
- Processo: O wafer é aquecido a altas temperaturas (até 1200°C) por um período muito curto, normalmente alguns segundos, usando fontes de luz intensa como lâmpadas halógenas.
- Aplicativos: Ideal para processos que exigem controle preciso de temperatura e tempo, como formação de junções rasas em dispositivos semicondutores avançados.
- Vantagens: Minimiza a difusão de dopantes, tornando-o adequado para dispositivos modernos com recursos menores.
- Limitações: Requer equipamentos sofisticados e controle preciso para evitar estresse térmico e danos ao wafer.
-
Recozimento a Laser:
- Processo: Um feixe de laser de alta energia é usado para aquecer a superfície do wafer a temperaturas extremamente altas por um período muito curto (nanossegundos a milissegundos).
- Aplicativos: Utilizado para recozimento localizado, como reparo de defeitos em áreas específicas ou ativação de dopantes em pequenas regiões.
- Vantagens: Aquecimento altamente preciso e localizado, minimizando o impacto térmico nas áreas circundantes.
- Limitações: Limitado a tratamentos de superfície e requer sistemas avançados de laser.
-
Recozimento de lâmpada flash:
- Processo: A luz intensa de uma lâmpada flash é usada para aquecer rapidamente a superfície do wafer, semelhante ao RTA, mas com durações ainda mais curtas (milissegundos).
- Aplicativos: Adequado para formação de junções ultra-rasas e reparo de defeitos superficiais.
- Vantagens: Processamento extremamente rápido, reduzindo o risco de difusão de dopantes.
- Limitações: Limitado a tratamentos de superfície e requer equipamento especializado.
-
-
Comparação de técnicas de recozimento:
- Temperatura e Tempo: O recozimento do forno opera em temperaturas mais baixas por períodos mais longos, enquanto o RTA, o recozimento a laser e o recozimento com lâmpada flash envolvem temperaturas mais altas por períodos mais curtos.
- Precisão e localização: O recozimento a laser e a lâmpada flash oferecem maior precisão e localização em comparação ao recozimento em forno e RTA.
- Complexidade do equipamento: O recozimento do forno é relativamente simples, enquanto o RTA, o recozimento a laser e o recozimento da lâmpada flash requerem equipamentos mais avançados e caros.
-
Aplicações na fabricação de semicondutores:
- Ativação de Dopante: Todas as técnicas de recozimento são usadas para ativar dopantes, mas a escolha depende dos requisitos do dispositivo e do tamanho do recurso.
- Reparo de Defeitos: O recozimento a laser e a lâmpada flash são particularmente úteis para reparar defeitos em áreas específicas sem afetar todo o wafer.
- Alívio do estresse: O recozimento em forno é comumente usado para alívio de tensões no processamento em massa, enquanto o RTA é preferido para alívio de tensões em dispositivos avançados.
-
Tendências Futuras em Recozimento de Semicondutores:
- Materiais Avançados: À medida que os materiais semicondutores evoluem, as técnicas de recozimento precisarão se adaptar para lidar com novos materiais como nitreto de gálio (GaN) e carboneto de silício (SiC).
- Dispositivos 3D: Com o surgimento dos dispositivos semicondutores 3D, as técnicas de recozimento precisarão enfrentar desafios relacionados à distribuição de calor e ao gerenciamento de tensões em estruturas complexas.
- Eficiência Energética: Os futuros processos de recozimento podem se concentrar na redução do consumo de energia, mantendo ou melhorando o desempenho.
Em resumo, o recozimento em semicondutores é um processo versátil e essencial que desempenha um papel crucial no desempenho e na confiabilidade do dispositivo. A escolha da técnica de recozimento depende dos requisitos específicos do dispositivo semicondutor, como tamanho do recurso, propriedades do material e características elétricas desejadas. À medida que a tecnologia de semicondutores continua a avançar, os processos de recozimento evoluirão para atender às demandas dos dispositivos da próxima geração.
Tabela Resumo:
Tipo | Processo | Aplicativos | Vantagens | Limitações |
---|---|---|---|---|
Recozimento de forno | Aquecido a 600°C–1200°C durante minutos a horas | Processamento em massa, ativação de dopantes, recozimento de defeitos | Aquecimento uniforme, redução completa de defeitos | Tempos de processamento mais longos podem causar difusão de dopantes |
Térmica Rápida (RTA) | Aquecido a 1200°C por segundos usando lâmpadas halógenas | Formação de junções rasas, dispositivos avançados | Minimiza a difusão de dopantes, controle preciso | Requer equipamentos sofisticados, risco de estresse térmico |
Recozimento a Laser | Laser de alta energia aquece superfície por nanossegundos a milissegundos | Reparo localizado de defeitos, ativação de dopantes | Impacto térmico mínimo e altamente preciso nas áreas circundantes | Limitado a tratamentos de superfície, requer sistemas avançados de laser |
Recozimento de lâmpada flash | A luz intensa aquece a superfície rapidamente (milissegundos) | Formação de junção ultra-rasa, reparo de defeitos superficiais | Processamento extremamente rápido, reduz a difusão de dopantes | Limitado a tratamentos de superfície, requer equipamento especializado |
Descubra a melhor técnica de recozimento para suas necessidades de semicondutores— entre em contato com nossos especialistas hoje !