O processo de recozimento oferece várias vantagens, especialmente no que respeita ao aumento das propriedades e da capacidade de trabalho dos materiais. Alivia as tensões internas, aumenta a ductilidade, reduz a dureza e melhora a uniformidade e homogeneidade da estrutura interna do material. Isto torna o material mais trabalhável e menos propenso a falhas em serviço. Além disso, o recozimento pode melhorar a maquinabilidade, as propriedades mecânicas e eléctricas e estabilizar os revestimentos de superfície. No caso da cerâmica, ajuda a atingir o equilíbrio térmico, densifica a estrutura interna e melhora a qualidade e a vida útil. Em geral, o recozimento é um processo crítico para otimizar o desempenho e a durabilidade do material.
Pontos-chave explicados:
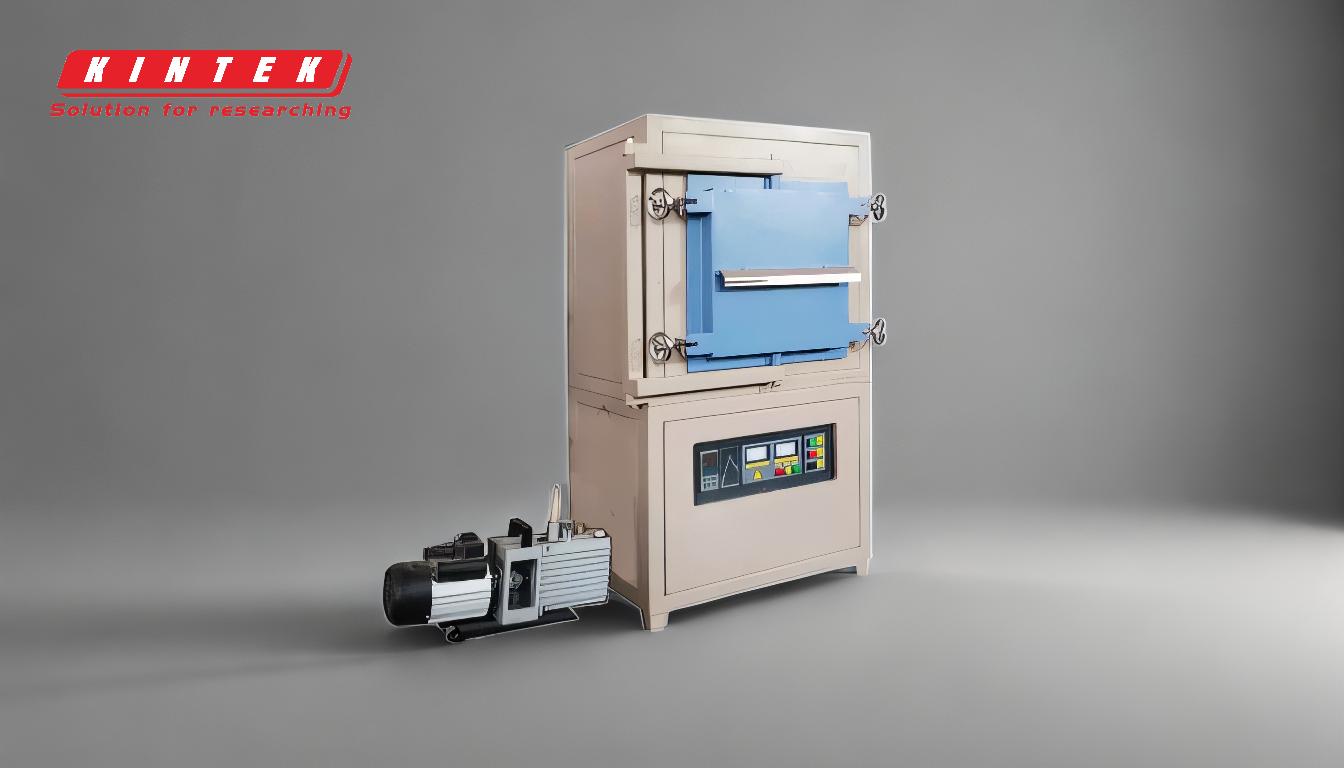
-
Alívio das tensões internas
- O recozimento elimina as tensões internas que se acumulam durante os processos de fabrico, como o trabalho a frio, a maquinagem ou a retificação.
- Estas tensões, se não forem resolvidas, podem levar à falha, distorção ou fissuração do material durante o processamento subsequente ou em serviço.
- Ao aquecer o material a uma temperatura específica e arrefecê-lo lentamente, o recozimento redistribui as tensões internas, resultando numa estrutura mais estável e uniforme.
-
Aumento da ductilidade e redução da dureza
- O recozimento amolece o material, tornando-o mais dúctil e menos quebradiço.
- Esta maior ductilidade permite que o material seja processado posteriormente, por exemplo, através de dobragem, moldagem ou maquinagem, sem fissuras ou rupturas.
- A dureza reduzida também melhora a trabalhabilidade, tornando o material mais fácil de manusear e processar.
-
Melhoria da uniformidade e homogeneidade
- O processo cria uma estrutura interna mais uniforme e homogénea, permitindo que os átomos se reorganizem e formem uma microestrutura estável.
- Esta uniformidade melhora as propriedades mecânicas do material, como a resistência e a tenacidade, e garante um desempenho consistente em toda a peça de trabalho.
-
Maquinabilidade melhorada
- O recozimento melhora a maquinabilidade dos materiais, reduzindo a dureza e aumentando a ductilidade.
- Isto facilita o corte, a perfuração ou a modelação do material sem causar desgaste excessivo da ferramenta ou danos na peça de trabalho.
-
Propriedades mecânicas e eléctricas melhoradas
- O processo pode melhorar as propriedades mecânicas como a força, a tenacidade e a resistência à fadiga.
- Em alguns casos, o recozimento também melhora a condutividade eléctrica ou outras propriedades eléctricas, tornando-o benéfico para materiais utilizados em aplicações eléctricas.
-
Estabilização de revestimentos de superfície
- O recozimento ajuda a estabilizar os revestimentos de superfície, assegurando uma estrutura interna uniforme e reduzindo as tensões residuais.
- Isto evita a delaminação ou fissuração do revestimento, melhorando a durabilidade e o desempenho dos materiais revestidos.
-
Densificação e melhoria da qualidade em cerâmica
- Para materiais cerâmicos, o recozimento promove o equilíbrio térmico e densifica a estrutura interna.
- Isto resulta numa melhor qualidade, resistência e vida útil da cerâmica.
- Também melhora as suas propriedades físicas e químicas, tornando-as mais fortes e mais leves.
-
Compatibilidade com o processamento subsequente
- O recozimento prepara os materiais para outros tratamentos ou processamento a alta temperatura, eliminando as tensões que poderiam causar distorção ou falha.
- Isto garante que o material se mantém estável e trabalhável durante todo o seu ciclo de vida.
-
Custo-eficácia na produção
- Ao melhorar a trabalhabilidade e reduzir o risco de falha, o recozimento reduz o desperdício de material e os custos de produção.
- Também prolonga a vida útil das ferramentas e do equipamento, tornando os materiais mais fáceis de processar.
-
Versatilidade em todos os materiais
- O recozimento é aplicável a uma vasta gama de materiais, incluindo metais, cerâmicas e certos polímeros.
- A sua adaptabilidade torna-o um processo valioso em várias indústrias, desde o fabrico à eletrónica e à construção.
Em resumo, o processo de recozimento é uma técnica versátil e essencial para otimizar as propriedades dos materiais, melhorar a trabalhabilidade e garantir um desempenho a longo prazo. A sua capacidade para aliviar tensões, melhorar a uniformidade e melhorar as propriedades mecânicas e eléctricas torna-o indispensável no fabrico moderno e na ciência dos materiais.
Quadro de resumo:
Vantagem | Descrição |
---|---|
Alívio das tensões internas | Elimina as tensões do fabrico, evitando falhas e distorções. |
Aumento da ductilidade | Torna os materiais mais macios e mais fáceis de trabalhar, reduzindo a fragilidade. |
Melhoria da uniformidade | Cria uma estrutura interna estável e homogénea para um desempenho consistente. |
Maquinabilidade melhorada | Reduz a dureza, tornando os materiais mais fáceis de cortar, perfurar ou moldar. |
Propriedades mecânicas melhoradas | Aumenta a força, a dureza e a resistência à fadiga. |
Estabilização de revestimentos de superfície | Evita a delaminação ou fissuração do revestimento, melhorando a sua durabilidade. |
Densificação em cerâmica | Melhora a qualidade, a resistência e a vida útil dos materiais cerâmicos. |
Custo-eficácia | Reduz o desperdício de material e os custos de produção, melhorando a trabalhabilidade. |
Versatilidade | Aplicável a metais, cerâmicas e polímeros em vários sectores. |
Optimize o desempenho do seu material com recozimento- contacte os nossos especialistas hoje mesmo !